In today’s fast-paced manufacturing industry, injection molding has become an indispensable process for producing a wide range of products, from automotive components to consumer goods. Choosing the right injection mold manufacturer is critical to ensuring product quality, production efficiency, and cost-effectiveness. In this article, we will explore the key factors to consider when selecting an injection mold manufacturer and highlight the importance of making an informed decision.
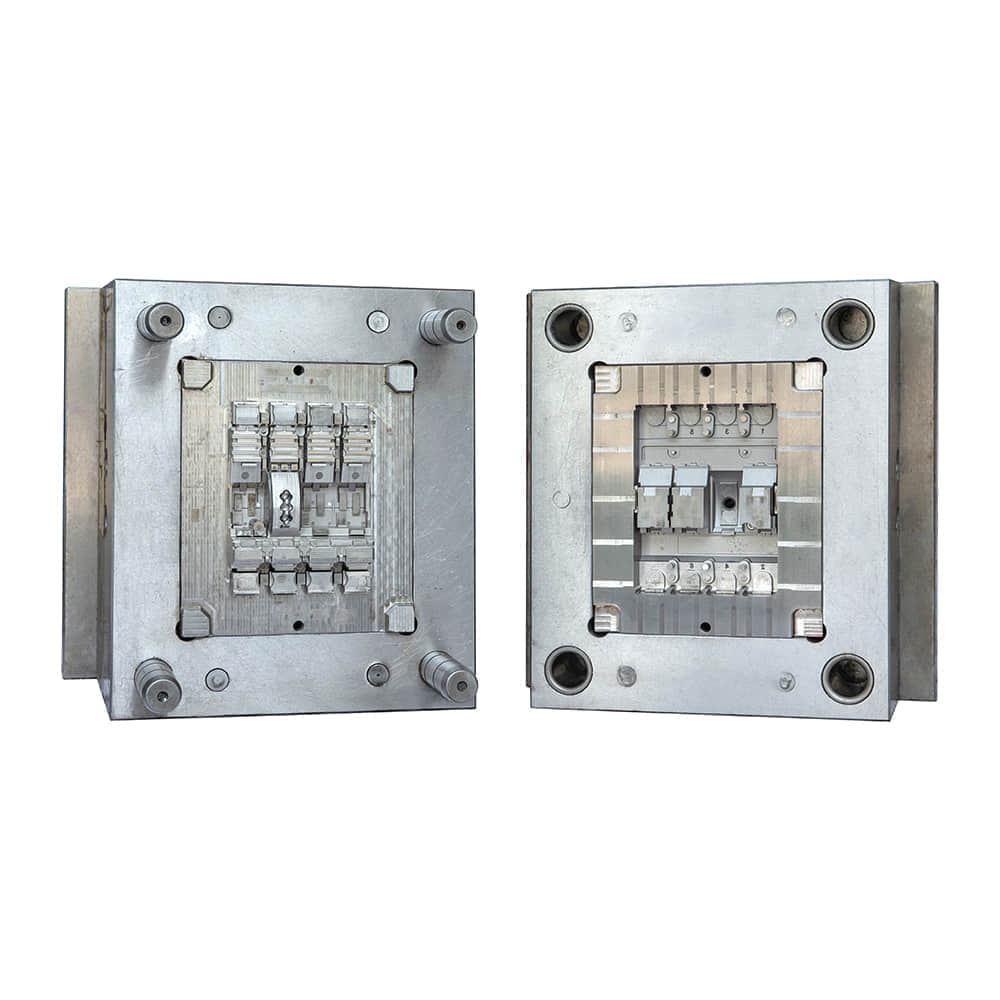
1. Expertise and Experience
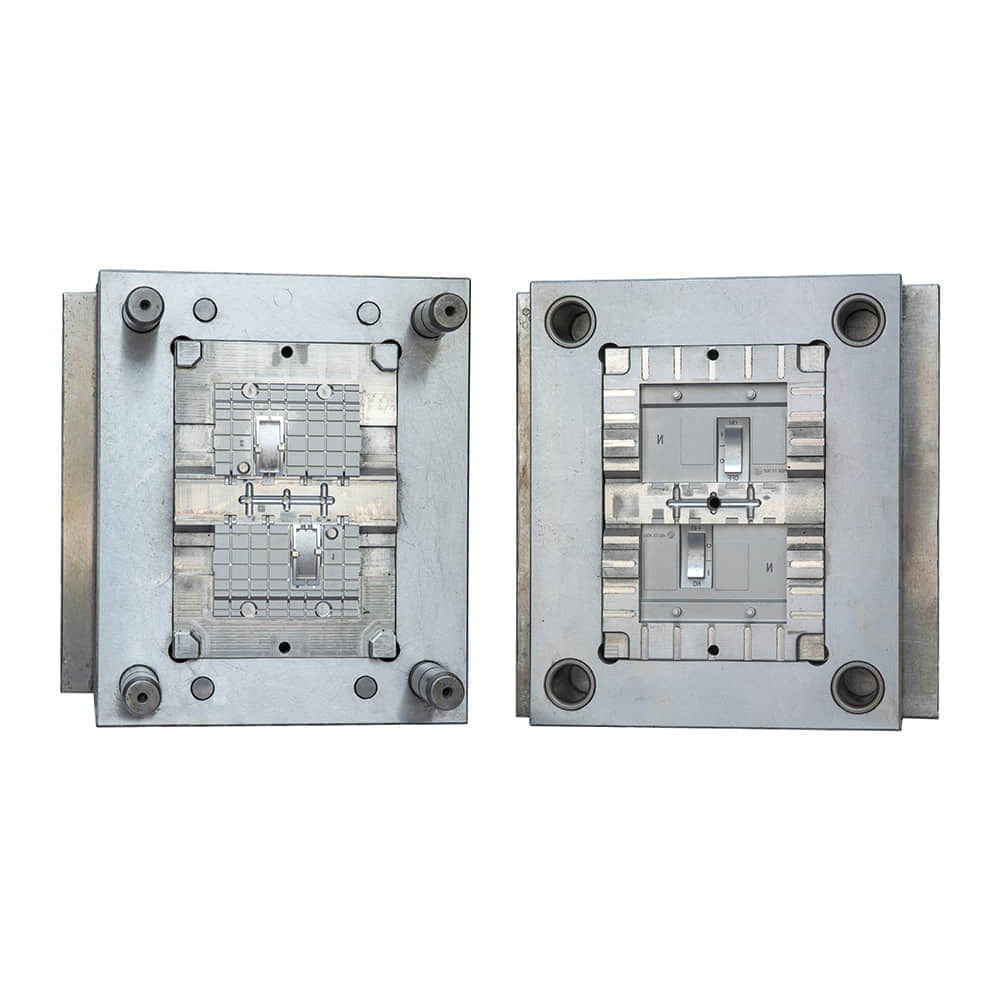
One of the primary factors to evaluate when choosing an injection mold manufacturer is their expertise and experience in the field. A reputable manufacturer should have a track record of producing high-quality molds for various industries. They should also be knowledgeable about the latest technologies and materials, ensuring that your product will meet the highest standards. 2. Quality Control Quality control is paramount in injection molding. Ask the manufacturer about their quality control processes and certifications. ISO 9001 certification, for example, is a good indicator of a commitment to quality. Ensure that they have a comprehensive quality control system in place to catch defects and maintain consistency in production. 3. Material Selection The choice of material for your injection molding project is crucial. A reliable manufacturer should offer a wide range of materials to suit your specific requirements. They should also have the expertise to recommend the most suitable material for your application, considering factors like strength, durability, and cost. 4. Customization Options Every product is unique, and your injection mold manufacturer should be able to tailor their services to meet your specific needs. Inquire about their ability to handle custom mold designs, modifications, and special requests. The flexibility to adapt to your project’s requirements is a significant advantage. 5. Production Capacity Assess the production capacity of the manufacturer to ensure they can meet your production demands. Whether you require a small batch or high-volume production, choose a manufacturer with the necessary equipment and resources to handle your order efficiently and within your timeline. 6. Lead Times Time-to-market is critical in today’s competitive landscape. Inquire about the manufacturer’s lead times for mold production and delivery. A reliable manufacturer should provide a clear timeline and stick to it to avoid production delays. 7. Cost Considerations While cost is an essential factor, it should not be the sole determining factor. Be cautious of manufacturers offering significantly lower prices, as this can sometimes indicate compromised quality. Instead, focus on value for your investment, considering quality, reliability, and service alongside price. 8. Customer Support Excellent customer support is invaluable when working with an injection mold manufacturer. Ensure that they have a responsive and knowledgeable support team that can address your concerns and provide assistance throughout the project. 9. References and Reviews Don’t hesitate to ask for references and read customer reviews. Feedback from previous clients can provide valuable insights into the manufacturer’s performance and reliability. 10. Sustainability Practices In today’s environmentally conscious world, consider a manufacturer’s sustainability practices. Look for a company that follows eco-friendly manufacturing processes, recycles materials, and minimizes waste. In conclusion, choosing the right injection mold manufacturer is a critical decision that can impact your product’s quality, cost-effectiveness, and time-to-market. By carefully evaluating factors such as expertise, quality control, customization options, production capacity, lead times, cost, customer support, references, and sustainability practices, you can make an informed choice that aligns with your project’s requirements and goals. Investing time in this selection process is a prudent step towards successful injection molding projects and a thriving partnership with your manufacturer.
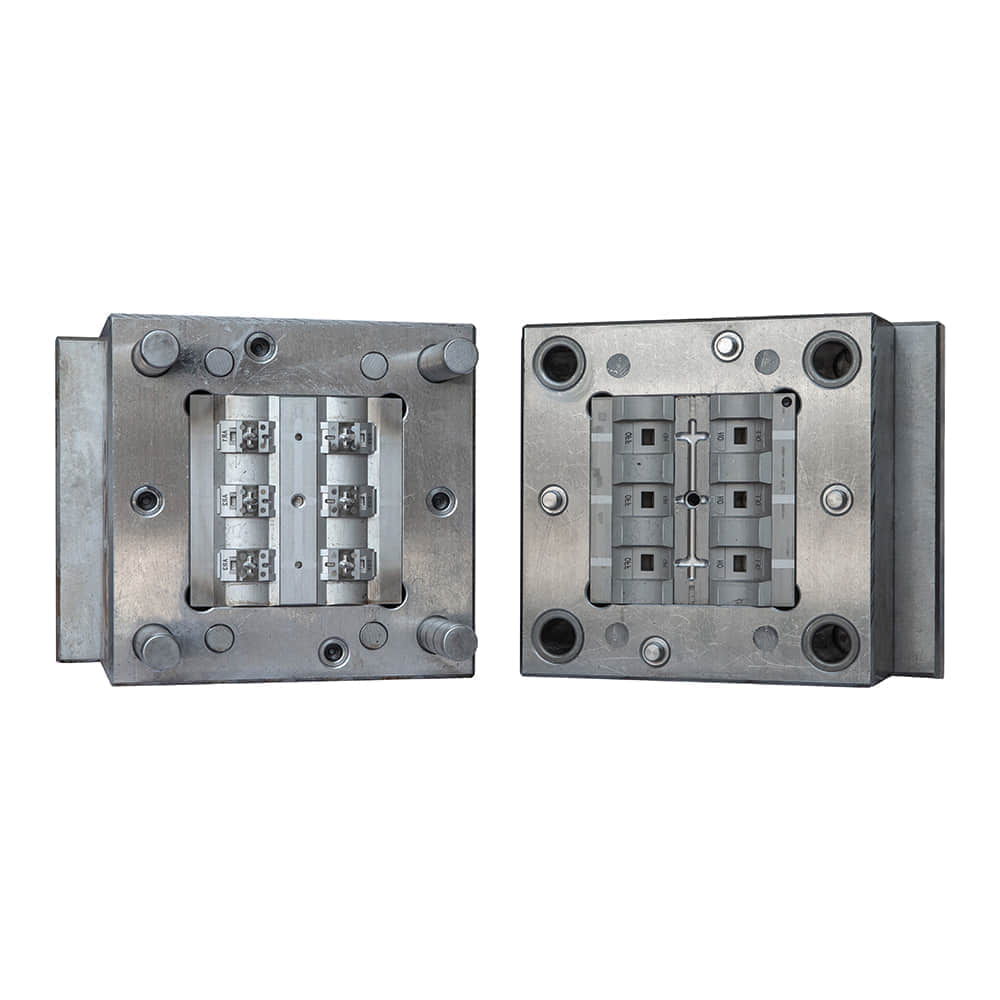