In recent years, the global shift towards renewable energy sources has gained tremendous momentum. Among these, solar power has emerged as a leading contender in the race to reduce carbon emissions and combat climate change. As solar panels continue to adorn rooftops and open spaces, ensuring the safety and efficiency of photovoltaic (PV) systems has become paramount. One critical component contributing to this safety is the Photovoltaic Molded Case Circuit Breaker (MCCB). This article explores the vital role of MCCB manufacturers in the solar energy sector and their innovations in enhancing the safety and reliability of PV systems.
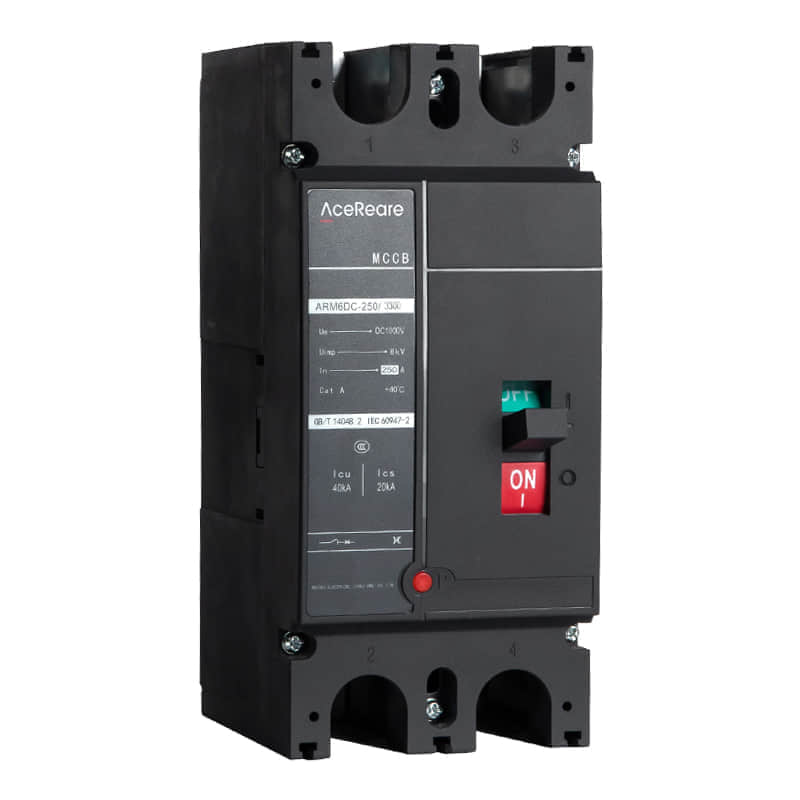
MCCBs: Safeguarding Solar Installations
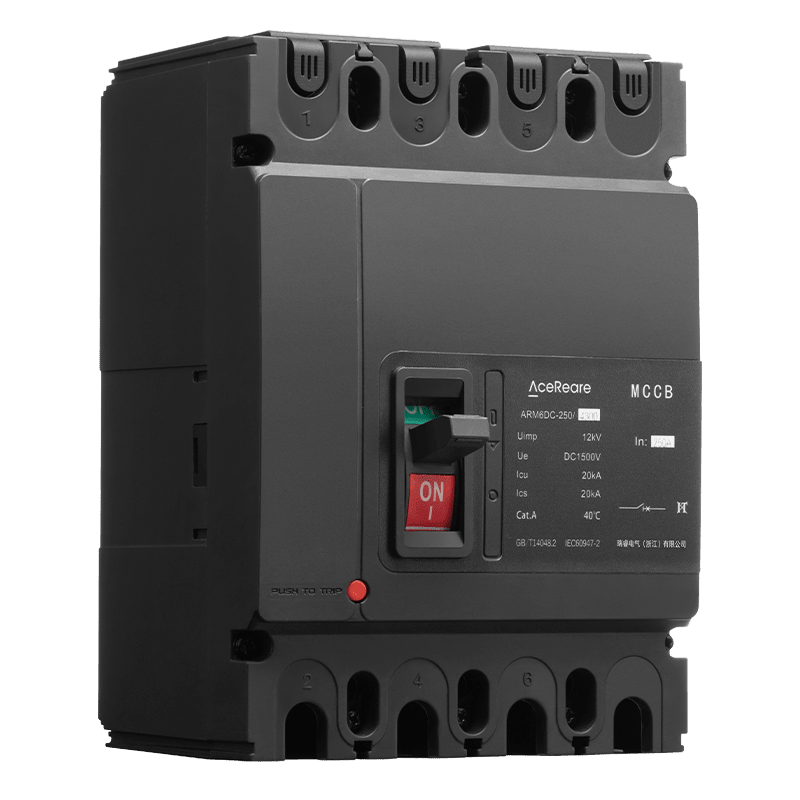
Photovoltaic MCCBs are electrical protection devices that play a crucial role in safeguarding solar installations. They serve as a critical link between the solar panels, inverters, and the electrical grid. MCCBs are designed to interrupt the flow of electricity in the event of faults or overloads, preventing electrical fires and protecting valuable PV system components. The Significance of MCCB Manufacturers MCCB manufacturers are at the forefront of solar safety, continuously researching and developing innovative solutions to ensure the reliable operation of PV systems. These manufacturers are responsible for producing MCCBs that are specifically tailored to meet the unique requirements of solar applications. Here are some key aspects of their contribution: 1. Specialized Designs:MCCB manufacturers understand the distinct characteristics of PV systems, including high-voltage direct current (HVDC) operation. They design MCCBs capable of handling these unique conditions, ensuring they can reliably interrupt DC currents and protect solar installations. 2. Durability:Solar installations are often exposed to harsh environmental conditions, from extreme temperatures to moisture and UV radiation. MCCB manufacturers engineer their products to withstand these challenges, providing long-lasting protection for PV systems. 3. Remote Monitoring:Many MCCB manufacturers incorporate advanced monitoring and communication capabilities into their devices. This enables real-time monitoring and remote control, allowing solar system operators to quickly respond to faults and optimize system performance. 4. Compliance with Standards:To ensure the safety and reliability of PV systems, MCCB manufacturers adhere to stringent international standards and certifications. This commitment to quality ensures that their products meet the highest industry standards. 5. Customization:MCCB manufacturers offer a range of products with varying current ratings, breaking capacities, and features to cater to the specific needs of different solar installations. This customization allows solar system designers to select the MCCB that best fits their requirements. Innovations in MCCB Technology As the solar industry continues to evolve, so does MCCB technology. Manufacturers are continually pushing the boundaries to enhance the safety and efficiency of PV systems. Some notable innovations include: 1. Arc Fault Detection:Advanced MCCBs are equipped with arc fault detection capabilities, which can identify and mitigate dangerous arc faults, reducing the risk of fires. 2. Rapid Shutdown Solutions:In response to safety regulations, MCCB manufacturers have developed rapid shutdown devices that can quickly disconnect the PV system from the grid during emergencies or maintenance. 3. Smart MCCBs:Integration of smart technologies such as IoT connectivity and predictive maintenance algorithms allows for proactive monitoring and management of PV systems. 4. Enhanced Coordination:MCCBs are designed to work in coordination with other protective devices, ensuring a comprehensive and layered approach to electrical safety within PV installations. Conclusion Photovoltaic Molded Case Circuit Breaker (MCCB) manufacturers are indispensable partners in the solar power revolution. Their dedication to innovation and safety is pivotal in the growth and sustainability of the solar energy sector. As the world continues to transition to cleaner, renewable energy sources, the role of MCCB manufacturers will only become more critical in ensuring the safe and efficient operation of photovoltaic systems. By investing in cutting-edge technology and maintaining a commitment to quality, these manufacturers contribute significantly to a greener and more sustainable future.
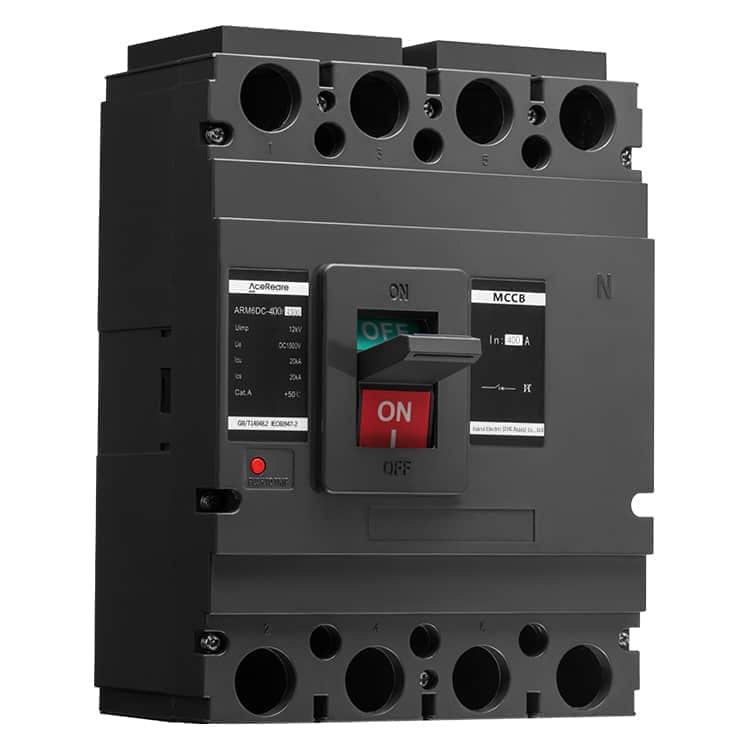