In today’s rapidly advancing world of electrical engineering, the demand for innovative and reliable circuit protection solutions has never been greater. One company that stands at the forefront of this industry is the Manufacturer of DC Molded Case Circuit Breakers. With a commitment to quality, safety, and technological advancement, this manufacturer has earned a stellar reputation among engineers, electricians, and businesses worldwide.
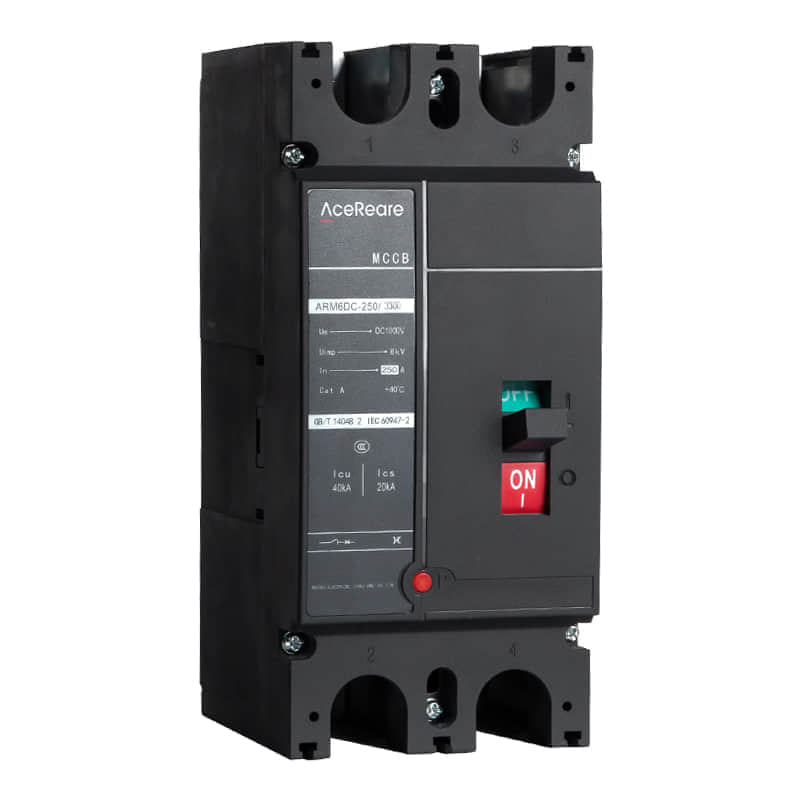
A History of Excellence
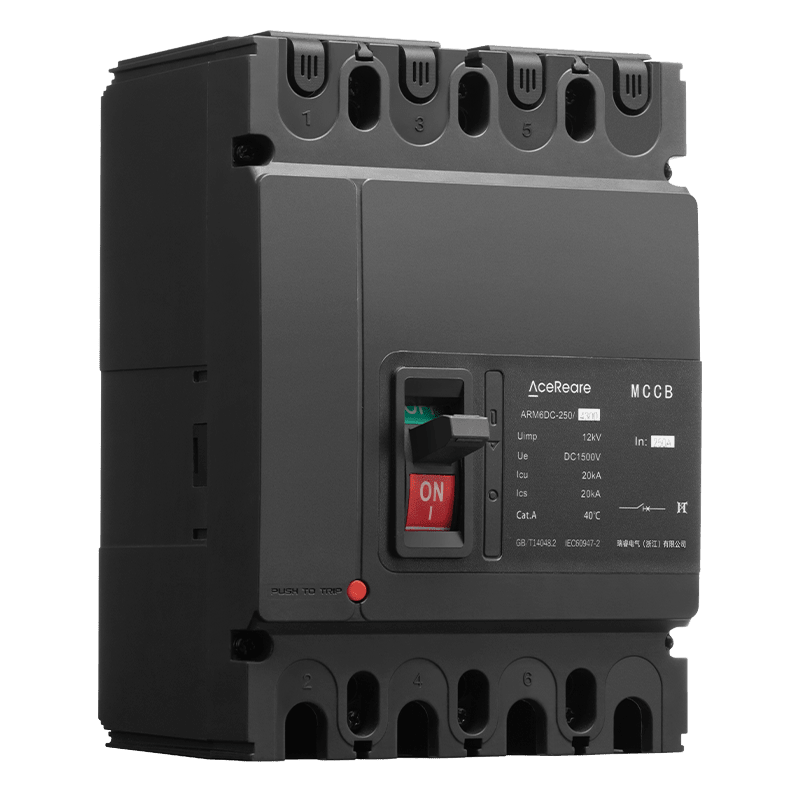
Established over three decades ago, the Manufacturer of DC Molded Case Circuit Breakers has consistently been a pioneer in the field. From its humble beginnings, the company has grown to become a global leader in circuit protection technology, serving diverse industries ranging from renewable energy to telecommunications. Unparalleled Product Range The hallmark of this manufacturer’s success is its extensive range of DC molded case circuit breakers. These breakers are specifically designed to provide reliable and efficient protection in DC electrical systems, making them a vital component in an array of applications. From low-voltage DC circuits to high-power DC installations, this manufacturer offers a comprehensive selection of circuit breakers to meet the unique needs of each customer. Whether safeguarding photovoltaic solar arrays, data center power distribution, or electric vehicle charging stations, their products are engineered for top-notch performance. Quality and Safety Assurance The Manufacturer of DC Molded Case Circuit Breakers places the utmost importance on product quality and safety. Rigorous testing and adherence to international standards ensure that every circuit breaker leaving their facility is of the highest quality, offering superior protection against faults, overloads, and short circuits. Stringent quality control measures are integrated into every step of the manufacturing process. From component selection to assembly and final inspection, a team of highly skilled engineers and technicians ensures that each breaker meets or exceeds industry standards. Innovation at its Core One of the driving forces behind this manufacturer’s success is its unwavering commitment to innovation. They continually invest in research and development to stay ahead of the curve in technology and design. Their engineers are at the forefront of creating solutions that address the evolving needs of modern electrical systems. From the integration of smart monitoring and control features to the use of advanced materials for enhanced durability, the Manufacturer of DC Molded Case Circuit Breakers consistently pushes the boundaries of what is possible in circuit protection. Global Reach and Local Support With a presence in over 50 countries, this manufacturer ensures that its products are readily available to customers worldwide. Whether you are operating in North America, Europe, Asia, or beyond, you can count on their network of distributors and service centers to provide timely support and assistance. Their commitment to customer satisfaction extends beyond sales; they provide comprehensive training, technical support, and maintenance services to ensure that customers have the knowledge and resources needed to maximize the performance and lifespan of their circuit breakers. A Sustainable Future As the world embraces sustainability and renewable energy sources, the Manufacturer of DC Molded Case Circuit Breakers is well-positioned to support these initiatives. Their products play a crucial role in enabling the integration of renewable energy systems, helping to reduce carbon emissions and combat climate change. By providing reliable circuit protection solutions for renewable energy projects, electric vehicles, and energy-efficient buildings, this manufacturer contributes to a more sustainable and eco-friendly future. In conclusion, the Manufacturer of DC Molded Case Circuit Breakers is a trailblazer in the electrical industry, known for its commitment to excellence, innovation, and safety. With a diverse product range, global reach, and a dedication to sustainability, they are poised to continue leading the way in circuit protection technology for years to come. Their legacy of quality and reliability ensures that customers can trust their electrical systems to function flawlessly, even in the most demanding applications.
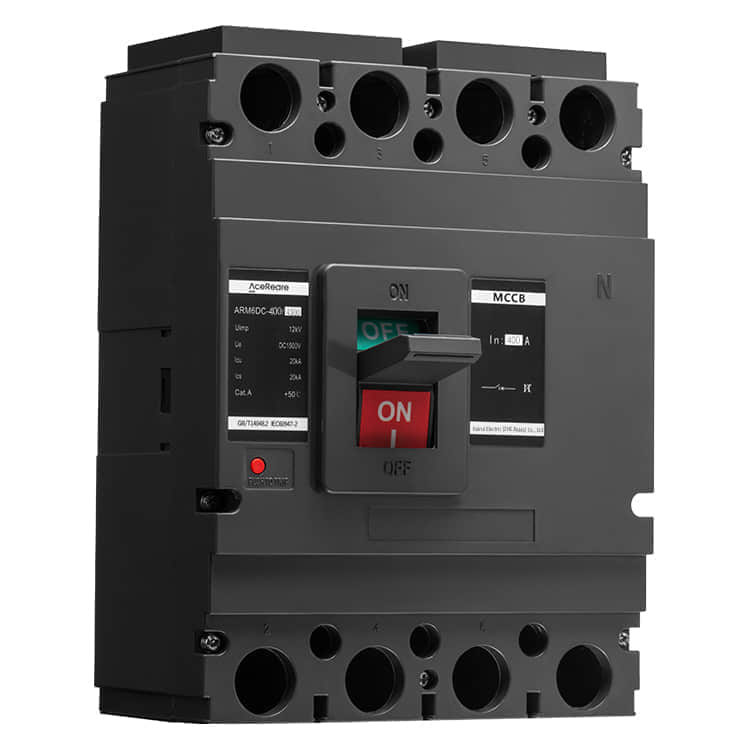