In the world of manufacturing, precision and reliability are paramount. Industries ranging from automotive to electronics rely on the expertise of Metal Stamping Parts ODM (Original Design Manufacturer) companies to produce high-quality components. This article delves into the world of Metal Stamping Parts ODM manufacturers, highlighting their critical role in modern manufacturing and the qualities that set them apart.
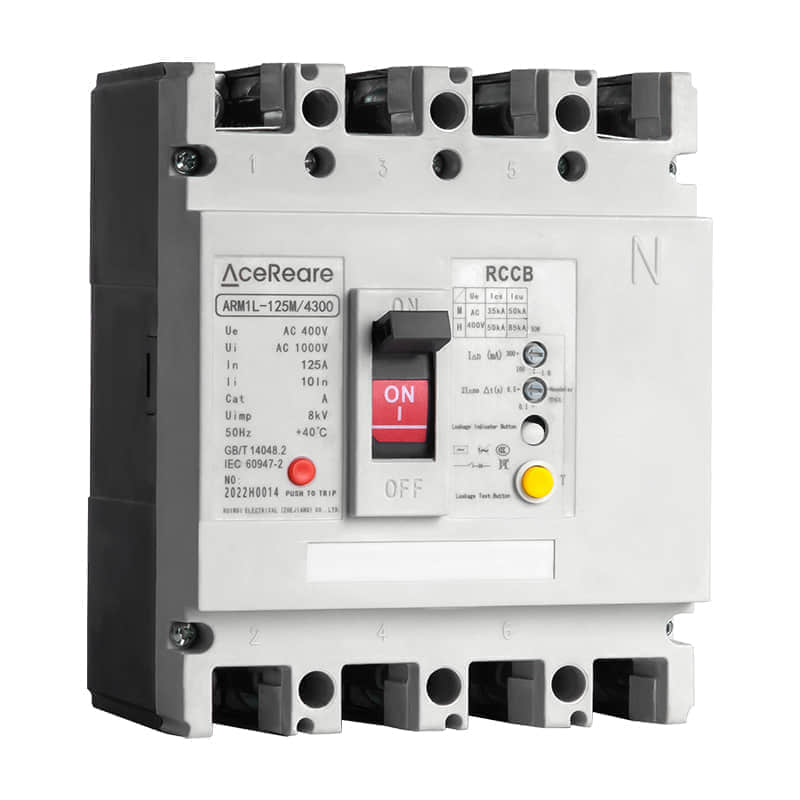
The Art of Metal Stamping
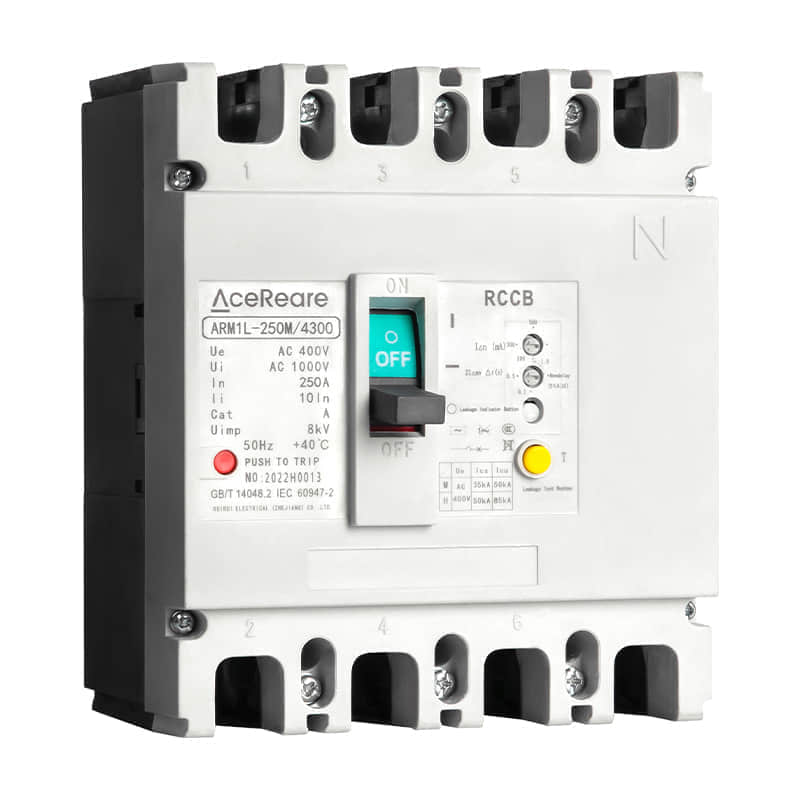
Metal stamping is a versatile and cost-effective method for shaping metals into intricate forms. This process involves a die and a press to create parts from sheet metal. From brackets and connectors to intricate electrical components, metal stamping is the backbone of many industries. ODM manufacturers specialize in designing and producing these stamped parts to meet the specific needs of their clients. The Role of ODM Manufacturers ODM manufacturers play a pivotal role in the supply chain. They are not only responsible for producing parts but also for the design and development of these components. Unlike OEM (Original Equipment Manufacturer) manufacturers, who produce parts based on pre-existing designs, ODMs provide a holistic solution. They work closely with their clients to understand their unique requirements, offering a customized approach that ensures every part is tailored to exact specifications. Precision Engineering One of the hallmarks of a top-notch Metal Stamping Parts ODM manufacturer is precision engineering. They employ cutting-edge technology, including Computer-Aided Design (CAD) and Computer Numerical Control (CNC) machining, to create dies and molds that produce parts with incredible accuracy. This precision is crucial, especially in industries where safety and performance are paramount. Materials Mastery Another critical aspect of ODM manufacturing is material expertise. Different industries require different materials, whether it’s stainless steel for medical devices, aluminum for aerospace components, or various alloys for automotive parts. ODM manufacturers understand the unique properties of these materials, ensuring that the stamped parts meet stringent quality standards. Quality Assurance Quality is non-negotiable in the world of Metal Stamping Parts ODM manufacturing. These companies implement rigorous quality control processes at every stage of production. From material selection and die design to stamping and finishing, each step is carefully monitored to ensure that the final product is free from defects and meets or exceeds industry standards. Innovation and Adaptability The manufacturing landscape is constantly evolving. ODM manufacturers must stay at the forefront of technological advancements to remain competitive. This includes adopting new materials, improving production processes, and integrating automation for increased efficiency. The ability to innovate and adapt to changing market demands is a hallmark of successful ODM manufacturers. Environmental Responsibility In today’s environmentally conscious world, responsible manufacturing is not just a choice; it’s an imperative. Leading Metal Stamping Parts ODM manufacturers are committed to sustainability. They implement eco-friendly practices such as recycling, waste reduction, and energy efficiency measures to minimize their environmental footprint. Global Reach In a globalized marketplace, Metal Stamping Parts ODM manufacturers often serve clients worldwide. Their ability to navigate international regulations, logistics, and cultural differences is a testament to their adaptability and commitment to customer satisfaction. Conclusion Metal Stamping Parts ODM manufacturers are the unsung heroes of modern manufacturing. Their expertise in precision engineering, materials science, and quality assurance ensures that industries ranging from automotive to electronics can rely on top-notch components. With innovation, adaptability, and a commitment to environmental responsibility, these manufacturers are shaping the future of manufacturing, one stamped part at a time.
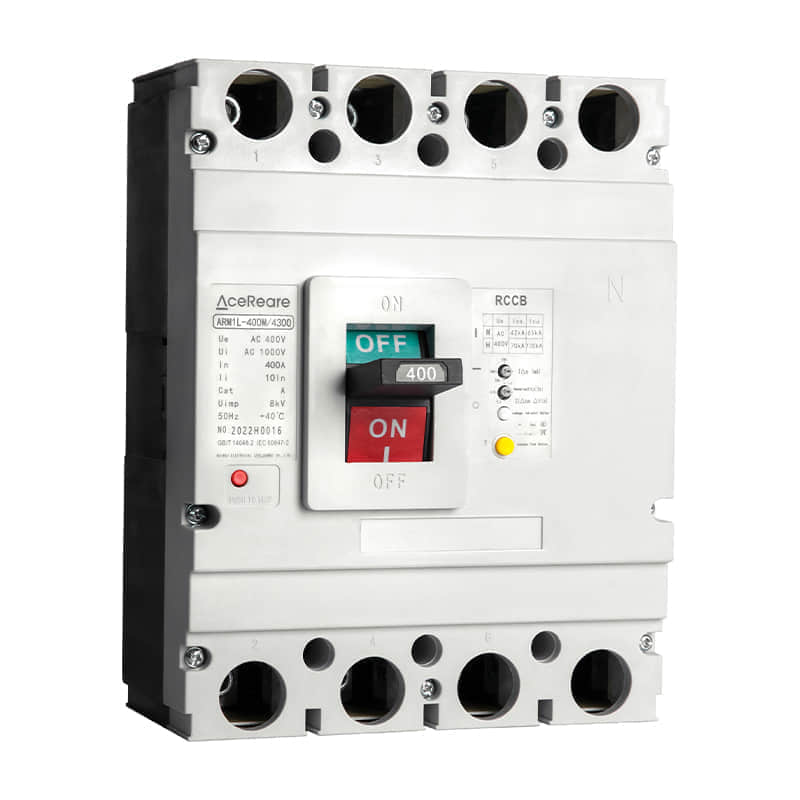