In the realm of modern electrical engineering, the significance of quality and precision in every component cannot be overstated. One such crucial element is the Molded Case Circuit Breaker (MCCB) base cover parts. These unassuming components play a pivotal role in ensuring the safety and reliability of electrical systems. Among the numerous manufacturers of MCCB base cover parts, there emerges a standout – a manufacturer that not only produces these parts but sets new industry standards: MCCB TechPro.
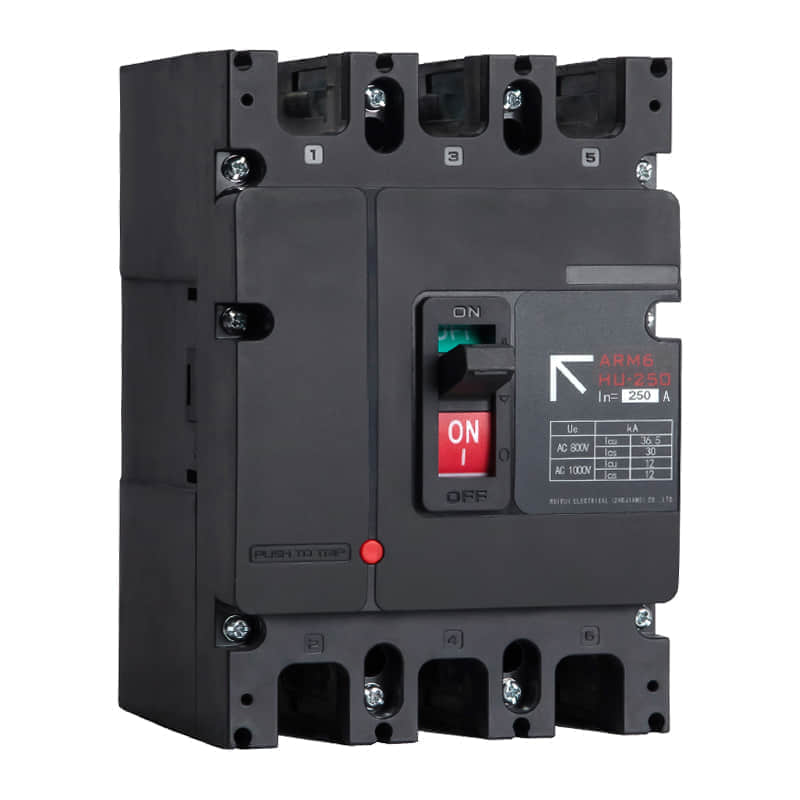
Setting Unmatched Quality Benchmarks
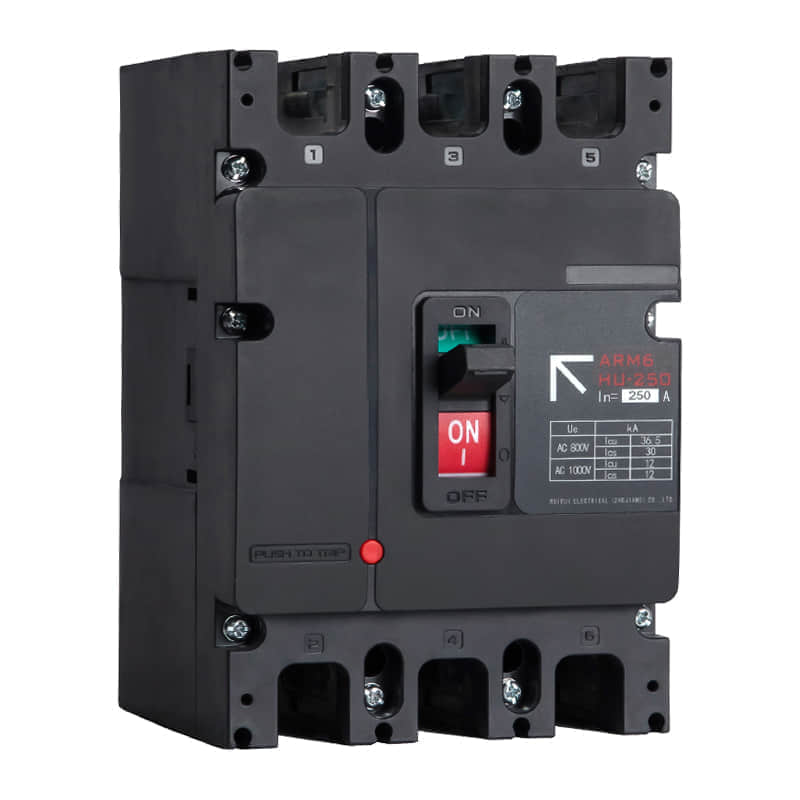
MCCB TechPro has emerged as a trailblazer in the field of MCCB base cover parts manufacturing. The company’s commitment to excellence and unyielding dedication to producing parts of unparalleled quality has solidified its reputation in the industry. The base cover parts manufactured by MCCB TechPro undergo rigorous testing procedures, ensuring that they conform to international standards and regulations. This level of quality control guarantees that these parts can withstand the demanding conditions of various electrical applications. State-of-the-Art Manufacturing Process What sets MCCB TechPro apart is its utilization of state-of-the-art manufacturing processes. The company employs cutting-edge technology, including precision molding and advanced material selection, to craft base cover parts that are not only durable but also resistant to environmental factors such as heat, moisture, and corrosive agents. This emphasis on innovative manufacturing techniques positions MCCB TechPro as an industry leader, consistently delivering products that exceed expectations. Customization for Specific Needs Recognizing the diverse needs of its clientele, MCCB TechPro goes a step further by offering customization options for MCCB base cover parts. The company collaborates closely with clients to understand their unique requirements, allowing them to tailor the parts to specific applications. This flexibility in manufacturing not only showcases MCCB TechPro’s versatility but also demonstrates its commitment to providing solutions that precisely align with customer needs. Sustainability and Environmental Responsibility In an era where environmental consciousness is paramount, MCCB TechPro takes its responsibility seriously. The company integrates sustainable practices into its manufacturing processes, using eco-friendly materials and minimizing waste generation. This dedication to environmental stewardship sets an example for the industry, highlighting that quality manufacturing can be achieved while minimizing the ecological footprint. Global Reach, Local Approach Despite its global reach, MCCB TechPro maintains a local approach to customer service. The company’s responsive and attentive customer support team ensures that clients’ queries are addressed promptly, fostering a strong and enduring client-manufacturer relationship. This personalized touch combined with world-class products solidifies MCCB TechPro’s status as a trusted partner in the MCCB base cover parts arena. Driving Innovation Forward MCCB TechPro’s journey is not one of complacency; rather, it is a trajectory of continuous innovation. The company invests significantly in research and development, aiming to pioneer new advancements in MCCB base cover part design and manufacturing. By pushing the boundaries of what is possible, MCCB TechPro contributes to the evolution of electrical systems, enhancing their efficiency, safety, and overall performance. Conclusion In the realm of MCCB base cover parts manufacturing, MCCB TechPro shines as a beacon of quality, innovation, and customer-centricity. Its commitment to producing top-tier components that meet the demands of modern electrical systems underscores its position as an industry leader. As technology advances and electrical systems become more intricate, having a reliable partner like MCCB TechPro becomes indispensable. With a legacy built on excellence, adaptability, and forward-thinking, MCCB TechPro continues to illuminate the path towards a safer and more efficient electrical future.
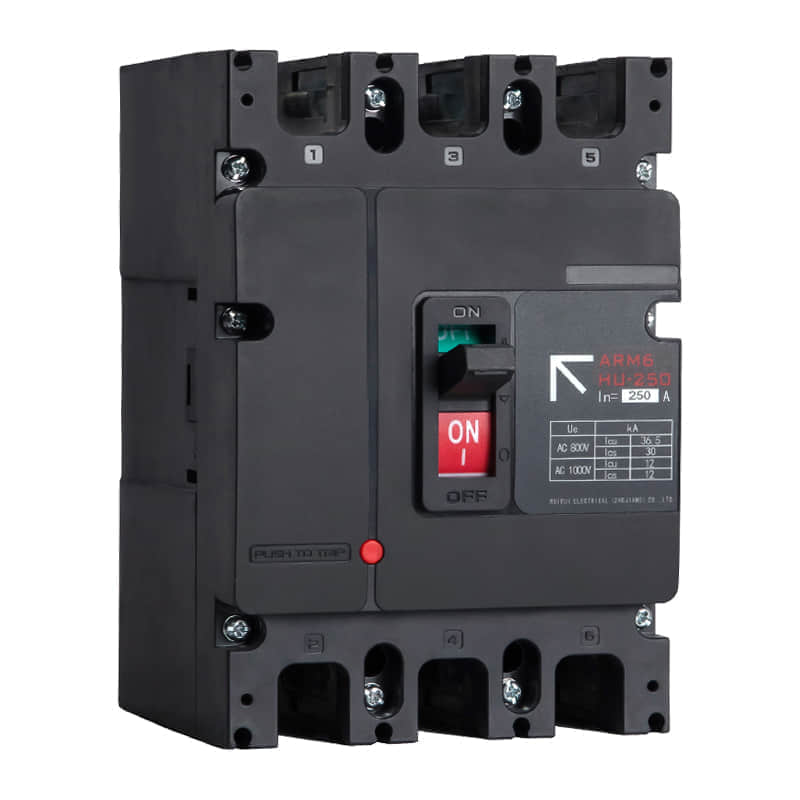