Innovating the Future: Frame Circuit Breaker Fixed Switch ODM Manufacturing
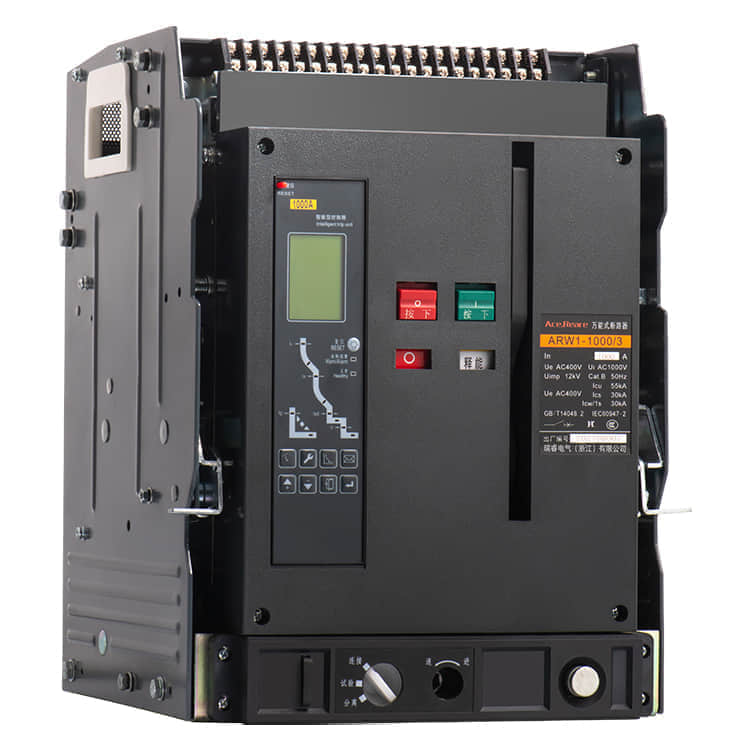
The modern world is powered by electricity, and at the heart of electrical systems are circuit breakers. Among the many components that contribute to the efficiency and safety of circuit breakers, the frame circuit breaker fixed switch stands out as a crucial element. In the realm of Original Design Manufacturing (ODM), companies specializing in producing these essential components play a pivotal role in shaping the landscape of electrical distribution. This article delves into the significance of frame circuit breaker fixed switch ODM manufacturers and their contributions to innovation.
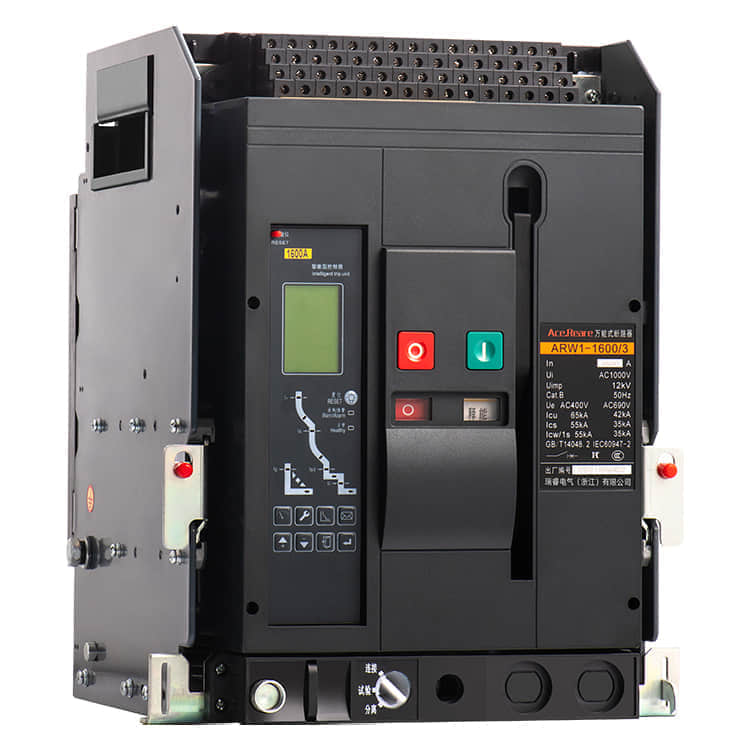
Understanding Frame Circuit Breaker Fixed Switches Frame circuit breaker fixed switches are fundamental components within electrical distribution systems. They serve as a crucial link between the incoming power supply and the distribution network. The primary purpose of these switches is to provide a means to manually disconnect power when maintenance or repairs are needed. Their design and functionality are critical to the safety of personnel working with electrical systems and the longevity of the equipment itself. The Role of ODM Manufacturers ODM manufacturers play a unique and vital role in the production of frame circuit breaker fixed switches. Unlike Original Equipment Manufacturers (OEMs), who create products based on their own designs, ODM manufacturers specialize in designing and producing components as per the specifications provided by other companies. This flexibility allows for a collaborative approach, where the expertise of the ODM manufacturer combines with the requirements of the client to create tailored solutions. Driving Innovation In the realm of electrical components, innovation is the cornerstone of progress. ODM manufacturers of frame circuit breaker fixed switches contribute to innovation in several ways: Customization: Every electrical system is unique, and ODM manufacturers recognize this diversity. They work closely with clients to customize frame circuit breaker fixed switches that precisely fit the requirements of the particular system. This level of personalization ensures optimal performance and safety. Technological Integration: As technology advances, so do the capabilities of electrical systems. ODM manufacturers stay at the forefront of these advancements, integrating new technologies into the design and functionality of frame circuit breaker fixed switches. This can include features like smart monitoring, remote operation, and compatibility with renewable energy sources. Efficiency Enhancement: ODM manufacturers are continually seeking ways to improve the efficiency of frame circuit breaker fixed switches. This involves not only the electrical efficiency of the component but also the ease of installation and maintenance. Streamlining these processes contributes to overall system efficiency. Safety Innovations: Safety is paramount in the design of electrical systems. ODM manufacturers innovate by incorporating enhanced safety features into frame circuit breaker fixed switches. These features can include arc-flash mitigation, improved insulation, and fail-safe mechanisms. The Collaborative Process The collaboration between ODM manufacturers and their clients is a symbiotic relationship that drives progress. Clients provide insights into the specific needs and challenges of their systems, while ODM manufacturers contribute their engineering expertise and innovative thinking. This partnership results in the creation of frame circuit breaker fixed switches that not only meet industry standards but exceed them. Conclusion In the grand tapestry of modern electricity distribution, frame circuit breaker fixed switches stand as essential threads, weaving together safety, efficiency, and innovation. The ODM manufacturers behind these components are the unsung heroes of the electrical world, driving advancements that power our lives. Through customization, technological integration, efficiency enhancement, and safety innovations, these manufacturers continue to shape the landscape of electrical distribution, illuminating the path towards a brighter and more electrifying future.
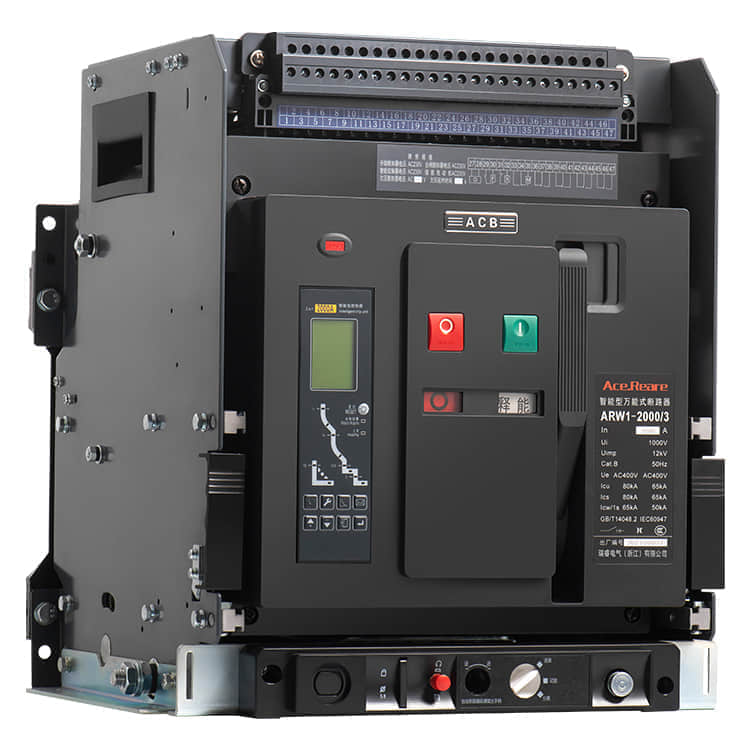