China has emerged as a global leader in manufacturing frame circuit breakers, revolutionizing the electrical industry with innovative technology and high-quality products. This article delves into the growth of China’s frame circuit breaker manufacturing industry and the key players driving this transformation.
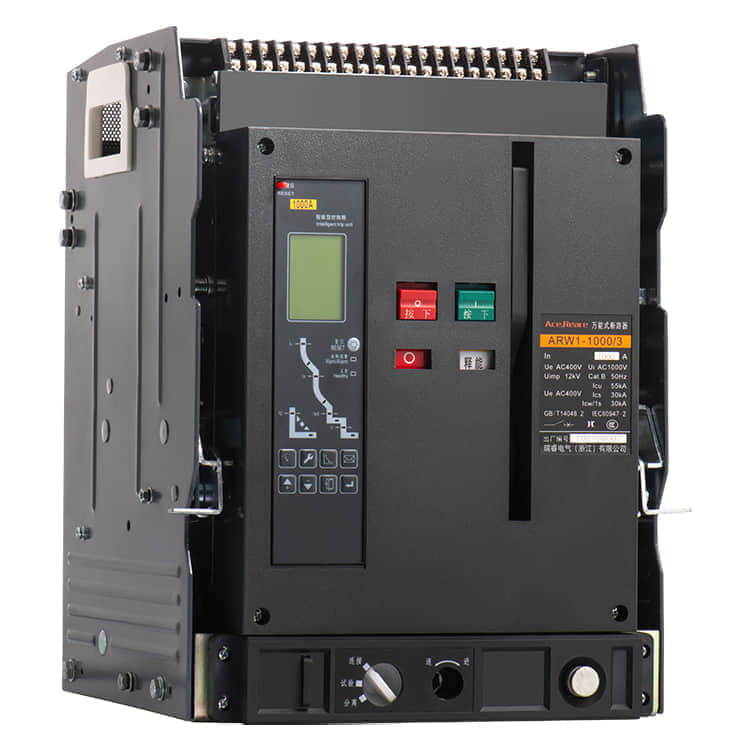
Introduction
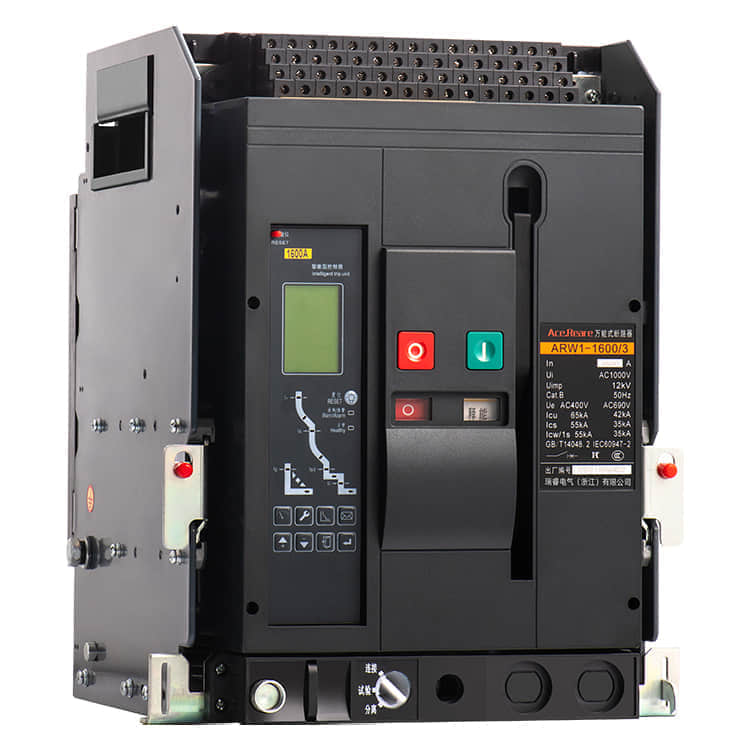
Frame circuit breakers play a crucial role in ensuring electrical safety by interrupting current flow when necessary. Over the years, China has made significant strides in manufacturing these essential electrical components, positioning itself as a dominant player in the global market. The Rise of Chinese Manufacturers Chinese manufacturers have consistently demonstrated their commitment to quality, innovation, and affordability. This dedication has led to the rapid expansion of China’s frame circuit breaker manufacturing sector. Several factors have contributed to this ascent: Advanced Technology: Chinese manufacturers have invested heavily in research and development, resulting in the integration of cutting-edge technology into their products. This has led to the production of more efficient, durable, and safer circuit breakers. Cost Efficiency: China’s manufacturing capabilities allow for cost-effective production, making their frame circuit breakers highly competitive in the global market. Robust Supply Chain: The country’s well-established supply chain infrastructure ensures a steady stream of quality raw materials, contributing to the production of reliable circuit breakers. Global Export Strategy: Chinese manufacturers have adopted an aggressive export strategy, reaching customers worldwide and expanding their market share. Key Players in China’s Frame Circuit Breaker Industry Several Chinese companies have gained international recognition for their excellence in frame circuit breaker manufacturing: Chint Group Corporation: Chint is one of China’s largest electrical equipment manufacturers, renowned for its wide range of high-quality circuit breakers. They prioritize innovation and have a strong global presence. Sensata Technologies: Sensata, with its headquarters in China, is a global leader in electrical protection solutions. Their frame circuit breakers are widely used in various industries, thanks to their reliability and safety features. Schneider Electric: While Schneider Electric is a French company, it has a significant manufacturing presence in China. They produce top-notch circuit breakers known for their innovation and energy efficiency. ABB: ABB, a Swiss-Swedish multinational corporation, has a substantial manufacturing footprint in China. They offer a diverse range of circuit breakers designed for various applications. Global Impact China’s dominance in frame circuit breaker manufacturing has had a significant global impact: Lower Costs for Consumers: The competition created by Chinese manufacturers has led to more affordable frame circuit breakers for consumers worldwide. Technological Advancements: China’s emphasis on innovation has driven the industry to develop safer and more efficient circuit breakers. Increased Accessibility: Chinese manufacturers have made frame circuit breakers more accessible, especially to developing regions where electrical safety is crucial. Challenges and Future Prospects While China’s frame circuit breaker manufacturing industry continues to grow, it faces some challenges: Quality Control: Maintaining high-quality standards is essential to uphold China’s reputation as a reliable manufacturer. Environmental Concerns: The industry must focus on sustainable production methods to minimize its environmental impact. Intellectual Property Rights: Chinese manufacturers need to address concerns regarding intellectual property rights to foster trust among international partners. In conclusion, China has firmly established itself as a global leader in frame circuit breaker manufacturing through its dedication to innovation, cost-efficiency, and quality. Key players in the industry have contributed to China’s rise on the international stage, positively impacting consumers and industries worldwide. As the industry continues to evolve, addressing challenges and embracing sustainability will be essential for China to maintain its position as a manufacturing powerhouse in the electrical sector.
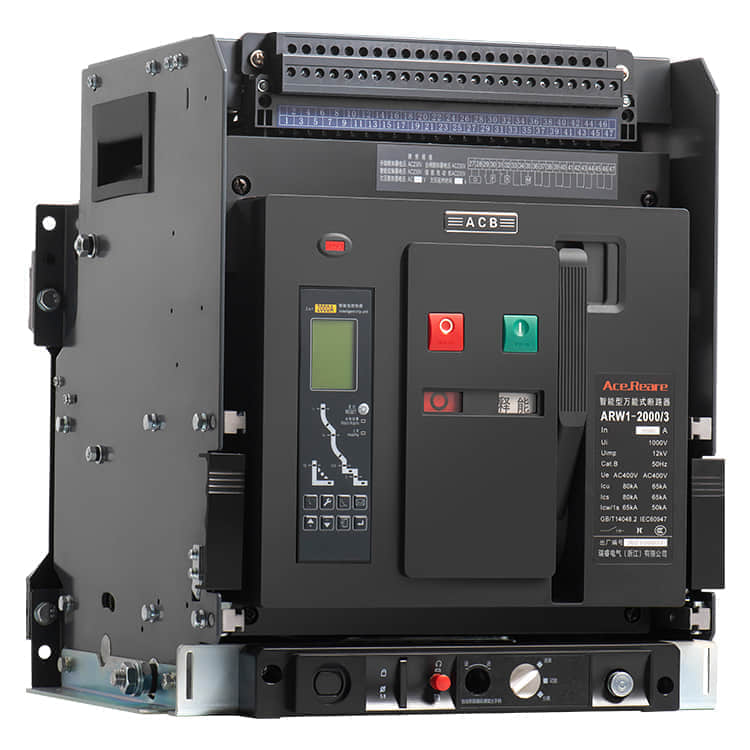