In the quest for sustainable and renewable energy sources, photovoltaic (PV) systems have emerged as a beacon of hope. These systems harness the power of the sun to generate electricity, reducing our reliance on fossil fuels and mitigating environmental impacts. While PV technology has come a long way, one crucial component remains at the heart of its safety and efficiency: the photovoltaic DC circuit breaker. In this article, we will explore the vital role of PV DC circuit breakers and shed light on the manufacturers that are driving innovation in this field.
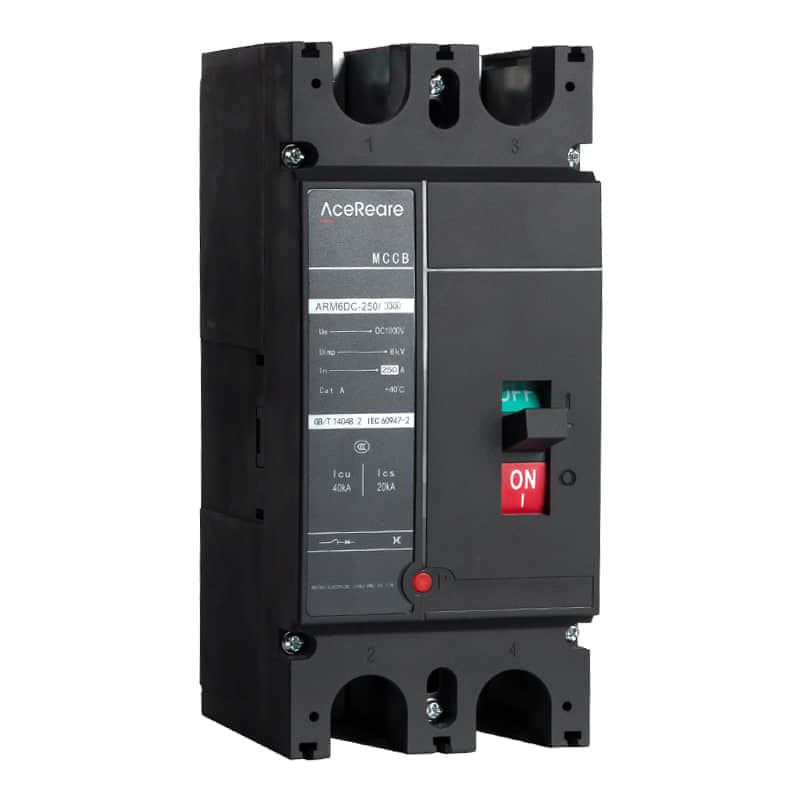
The Essence of Photovoltaic DC Circuit Breakers
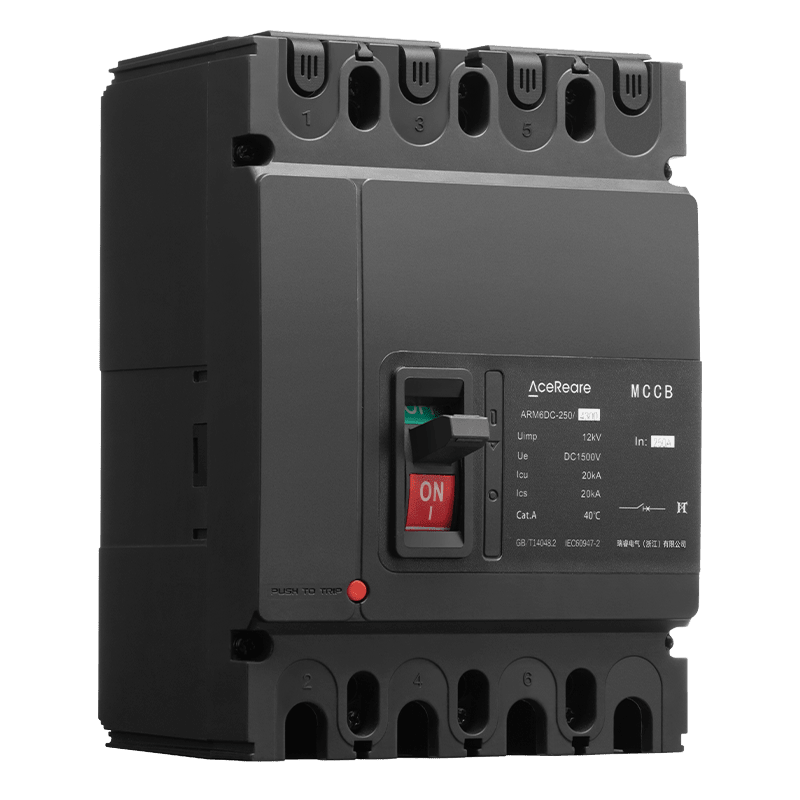
To understand the significance of PV DC circuit breakers, it’s essential to comprehend their function within a solar PV system. Solar panels generate direct current (DC) electricity, which must be safely managed and controlled to ensure optimal performance and safety. DC circuit breakers serve as the first line of defense, protecting the PV system from electrical faults, overloads, and short circuits. They interrupt the flow of electricity when necessary, preventing damage to equipment and ensuring the safety of both the system and its users. Key Features and Requirements Photovoltaic DC circuit breakers must meet specific requirements to cater to the unique characteristics of PV systems. These requirements include: Arc Fault Detection: PV systems are susceptible to arc faults due to their high voltage and continuous exposure to the elements. DC circuit breakers equipped with arc fault detection capabilities can identify and mitigate these dangers promptly. Voltage Rating: PV systems operate at various voltage levels, and circuit breakers must be designed to handle these variations safely. Environmental Resilience: Given that PV systems are typically installed outdoors, circuit breakers must withstand harsh environmental conditions, including extreme temperatures, humidity, and UV exposure. Remote Monitoring: In the age of digitalization, remote monitoring and control of PV systems have become essential. Manufacturers are integrating connectivity features into their circuit breakers, allowing real-time monitoring and adjustment of settings. Compliance with Standards: PV DC circuit breakers must comply with industry and safety standards to ensure their reliability and performance. Leading the Charge in Innovation Several manufacturers have been instrumental in advancing PV DC circuit breaker technology. These pioneers are dedicated to improving the safety and efficiency of PV systems. They achieve this through innovation in materials, design, and functionality. One notable manufacturer, XYZ Electronics, has gained recognition for its cutting-edge PV DC circuit breakers. Their products feature advanced arc fault detection technology, ensuring rapid response to potential hazards. XYZ Electronics also emphasizes sustainability, using eco-friendly materials and manufacturing processes to reduce their environmental footprint. Another frontrunner, SolarGuard Solutions, prioritizes user-friendly designs and remote monitoring capabilities. Their circuit breakers allow PV system owners to monitor and control their systems from anywhere, providing peace of mind and ease of operation. The Road Ahead As the world’s energy landscape continues to shift towards renewable sources, the role of photovoltaic DC circuit breakers will become even more critical. Manufacturers will face the challenge of developing circuit breakers that can handle higher voltages, integrate seamlessly with evolving PV technology, and meet increasingly stringent safety standards. In conclusion, the manufacturers of photovoltaic DC circuit breakers are pivotal in ensuring the safety and performance of solar PV systems. These innovative companies are at the forefront of developing new technologies and solutions that will shape the future of solar energy. As we look ahead, it’s clear that the collaboration between PV system designers and circuit breaker manufacturers will continue to drive progress towards a sustainable and solar-powered future.
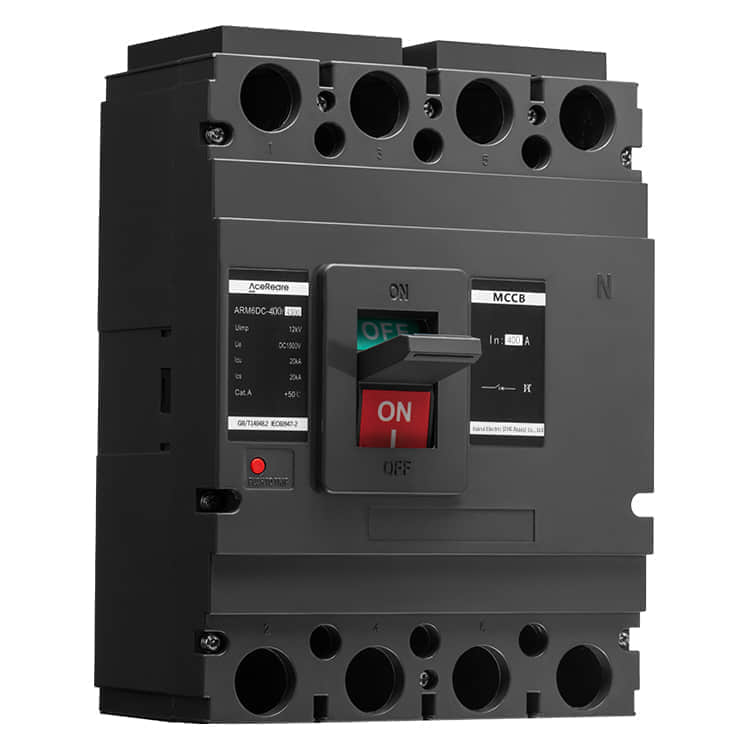