In today’s fast-paced world, electricity plays an indispensable role in powering our homes, industries, and technology. However, with the convenience of electricity comes the responsibility of ensuring electrical safety. Electrical accidents can lead to serious injuries or even fatalities. To mitigate these risks, technological advancements have given birth to a remarkable innovation: the Molded Case Circuit Breaker with Residual Leakage Protection (MCCB-RLP). This article explores the significance of MCCB-RLP, its features, and its applications in enhancing electrical safety.
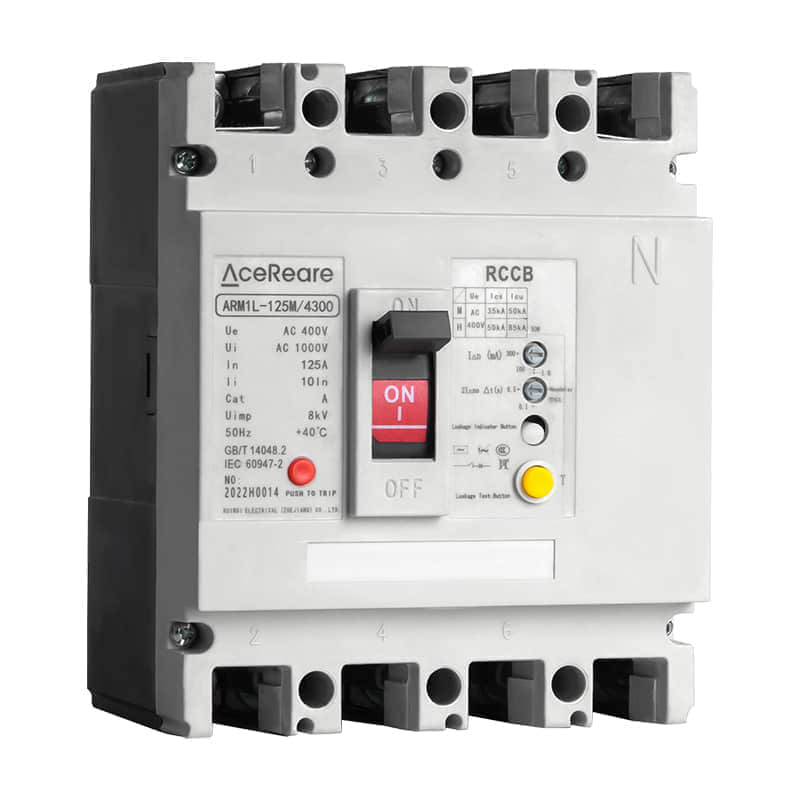
1. Understanding MCCB-RLP
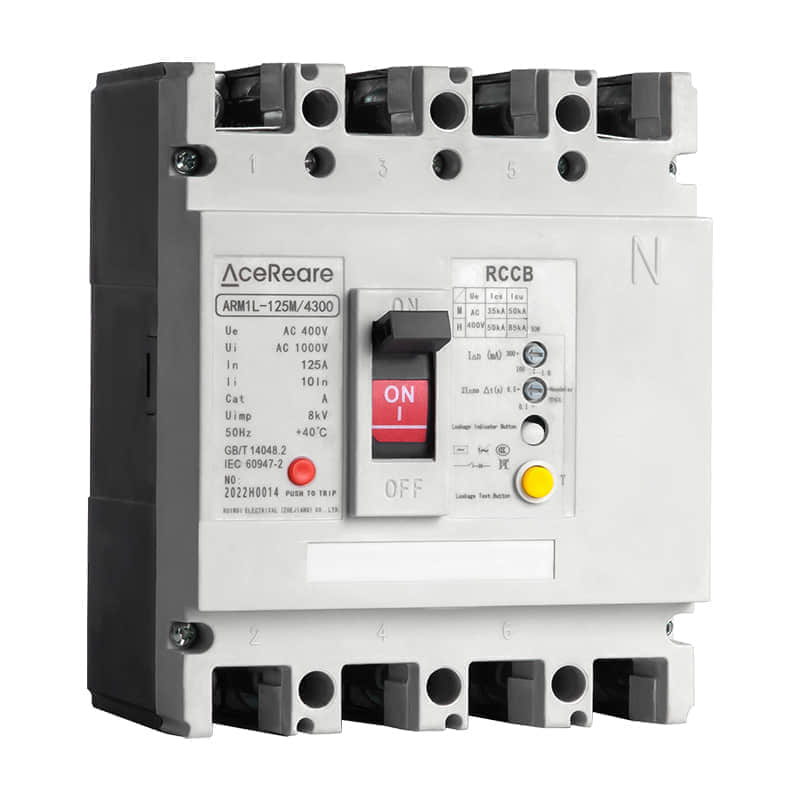
A Molded Case Circuit Breaker (MCCB) is a protective device used in electrical circuits to interrupt or disconnect the flow of electricity in the event of overcurrent or short circuit faults. While traditional MCCBs are effective in preventing electrical fires and protecting equipment, they may not detect certain hidden dangers, such as ground faults or residual currents. MCCB-RLP, on the other hand, takes electrical safety to the next level by incorporating residual leakage protection. This added feature enables MCCB-RLP to identify and respond to ground faults, where electricity is unintentionally diverted to an unintended path, such as a human body, posing a grave risk. 2. Key Features of MCCB-RLP Residual Current Sensing: MCCB-RLP utilizes advanced sensors to constantly monitor the current flowing through the circuit. Any deviation from the expected current pattern is flagged as a potential ground fault. Instantaneous Tripping: In the event of a ground fault, MCCB-RLP reacts swiftly, interrupting the current flow within milliseconds. This rapid response reduces the risk of electrical shock and prevents equipment damage. Adjustable Sensitivity: MCCB-RLP allows users to adjust its sensitivity to cater to specific applications. This flexibility ensures that the device can distinguish between harmless transient currents and potentially dangerous ground faults. Self-Testing Mechanism: To guarantee reliable operation, MCCB-RLP includes a self-testing mechanism that regularly checks the device’s functionality. Any detected issues are promptly indicated for maintenance. 3. Applications and Benefits MCCB-RLP finds applications across various sectors, including residential, commercial, and industrial settings: Residential Safety: In homes, MCCB-RLP can safeguard occupants from electrical shocks caused by faulty appliances or wiring. It provides peace of mind to homeowners, especially those with young children. Commercial and Industrial Protection: MCCB-RLP is crucial in commercial and industrial environments where electrical equipment is abundant. It not only prevents accidents but also minimizes downtime due to electrical faults. Enhancing Fire Safety: Ground faults are a significant contributor to electrical fires. MCCB-RLP can reduce the risk of such fires by detecting and isolating faults before they escalate. Code Compliance: Many electrical codes and standards now require the use of MCCB-RLP in certain applications to ensure compliance with safety regulations. 4. Future Developments As technology continues to advance, MCCB-RLP is likely to undergo further enhancements. These may include: Integration with Smart Systems: MCCB-RLP can be integrated into smart electrical systems, allowing remote monitoring and control, as well as predictive maintenance. Increased Sensitivity: Ongoing research aims to improve the sensitivity of MCCB-RLP, making it even more adept at detecting minor ground faults. Cost Reduction: As the technology matures and becomes more widespread, the cost of MCCB-RLP may decrease, making it more accessible to a broader range of users. In conclusion, the Molded Case Circuit Breaker with Residual Leakage Protection represents a significant step forward in electrical safety. Its ability to detect and respond to ground faults makes it an invaluable tool in preventing electrical accidents and fires. As technology evolves, MCCB-RLP is set to become an integral part of modern electrical systems, ensuring a safer and more secure electrical environment for all.
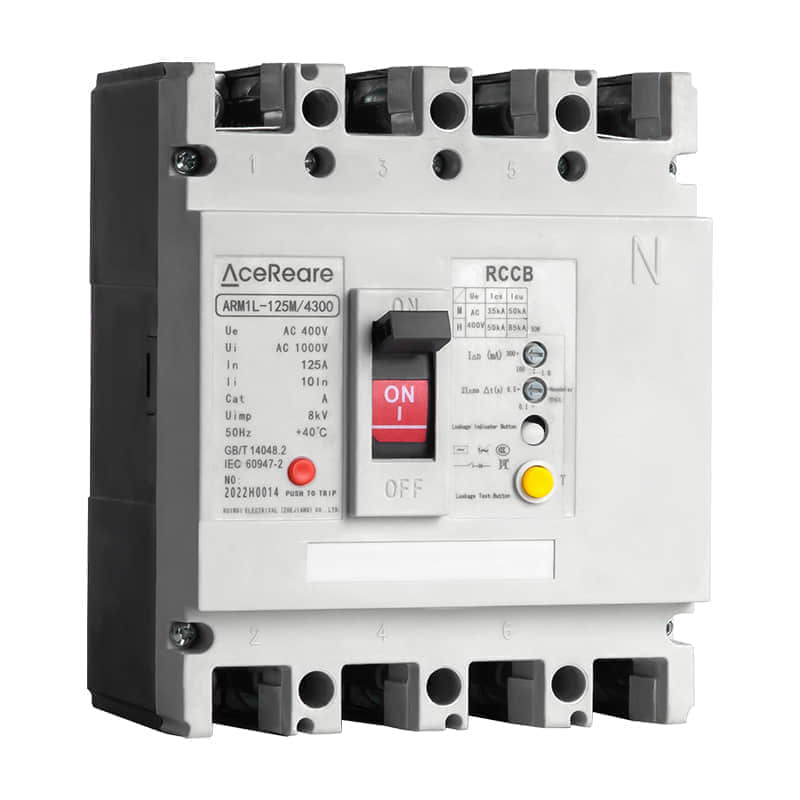