Metal stamping is a vital manufacturing process used across various industries to create intricate and precise components for everything from automobiles to consumer electronics. At the heart of this process lies the metal stamping die, a critical tool that shapes raw metal into the desired form. When it comes to metal stamping dies, ODM (Original Design Manufacturer) companies play a pivotal role in ensuring the quality, precision, and innovation required for modern manufacturing.
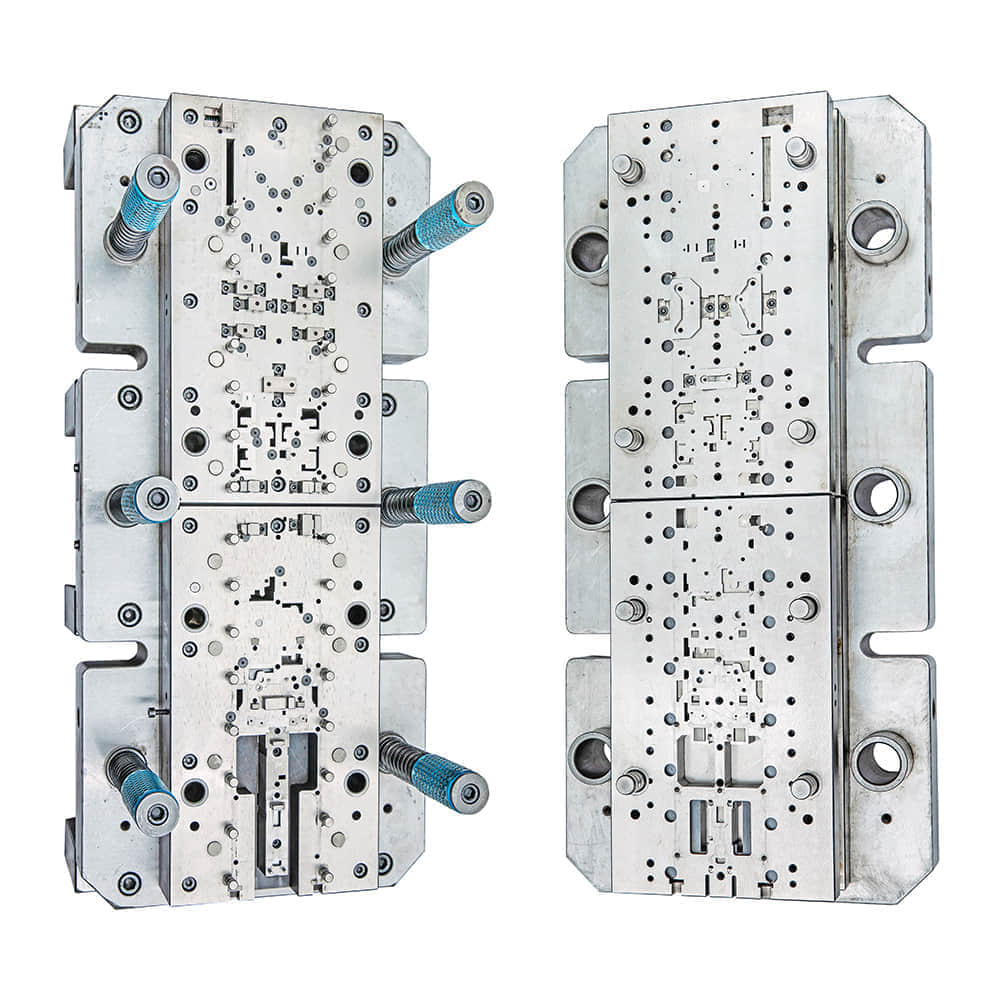
The Essence of Metal Stamping Dies
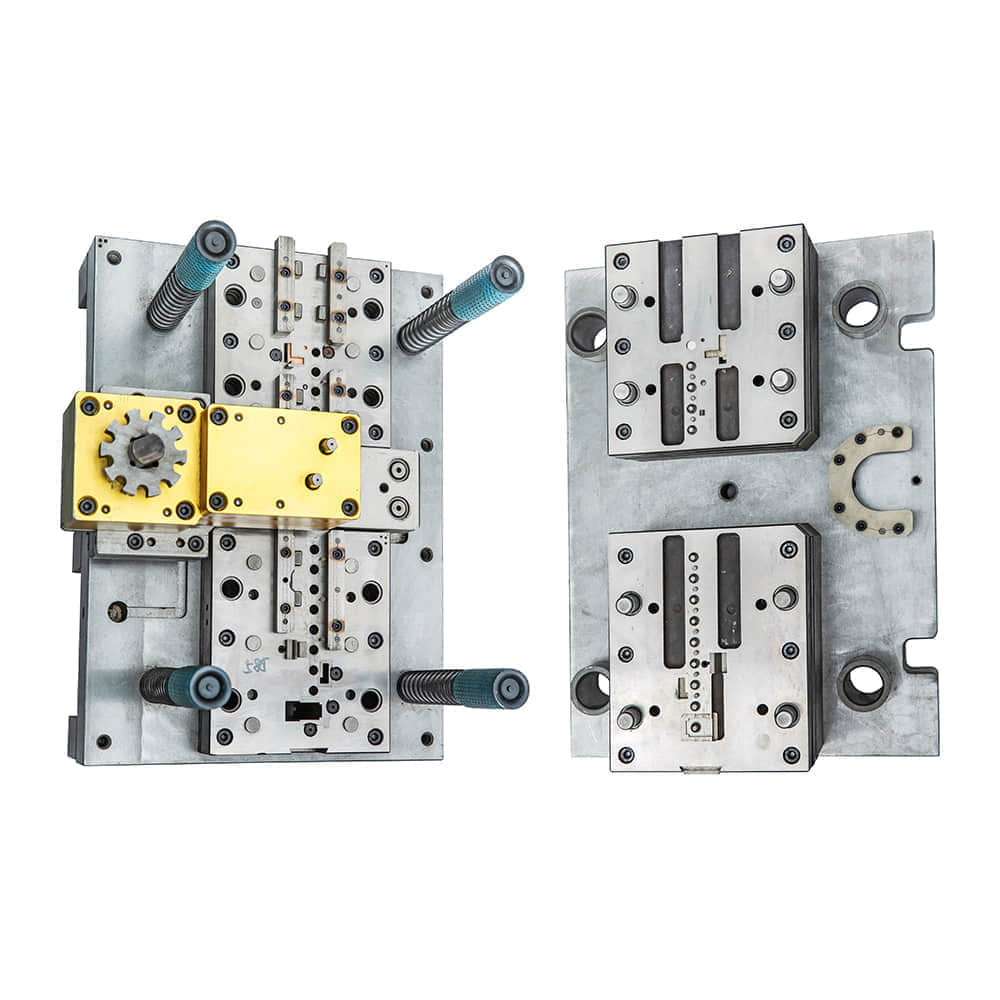
Metal stamping dies, often simply referred to as “stamping dies,” are specialized tools that are used to cut, shape, and form metal sheets into specific parts or components. These dies come in various forms, including blanking dies, piercing dies, and forming dies, depending on the intended outcome. The precision and intricacy of these dies determine the quality and accuracy of the final stamped metal components, making them an indispensable part of the manufacturing process. The Role of an ODM Manufacturer An ODM manufacturer specializing in metal stamping dies is a key player in the manufacturing ecosystem. Unlike OEMs (Original Equipment Manufacturers) who produce finished products, ODMs focus on the design and production of specialized components, such as metal stamping dies, that are essential to OEMs. ODM manufacturers bring expertise, innovation, and a customer-centric approach to the table. Precision Engineering One of the primary responsibilities of a metal stamping die ODM manufacturer is to design and engineer dies with extreme precision. Every component they produce must meet exacting standards to ensure consistent quality in the final stamped products. This precision starts with the initial design, where the ODM manufacturer considers factors such as material selection, die geometry, and manufacturing techniques. Customization and Innovation In today’s rapidly evolving manufacturing landscape, customization and innovation are paramount. ODM manufacturers must be capable of tailoring their metal stamping dies to meet the unique requirements of each client. This customization can involve optimizing die designs for maximum efficiency, reducing material waste, or enhancing the overall performance of the stamped parts. Moreover, ODM manufacturers are at the forefront of introducing innovative solutions and technologies to improve the metal stamping process. Collaboration and Quality Assurance Collaboration between ODM manufacturers and their clients is crucial. Effective communication and feedback loops ensure that the final product aligns with the client’s vision and requirements. Quality assurance processes, including rigorous testing and inspections, guarantee that the metal stamping dies produced by ODM manufacturers are reliable, durable, and capable of consistently delivering high-quality results. Industries Served Metal stamping dies find applications in a wide range of industries. Whether it’s automotive, aerospace, electronics, or consumer goods, ODM manufacturers must adapt to the specific demands of each sector. The ability to cater to diverse industries underscores the versatility and expertise of a reputable ODM manufacturer. Conclusion In the world of manufacturing, precision and innovation are the cornerstones of success. Metal stamping dies ODM manufacturers embody these principles, serving as the backbone of industries that rely on stamped metal components. Their commitment to precision engineering, customization, innovation, collaboration, and quality assurance ensures that the products they deliver meet and exceed the expectations of their clients. As manufacturing technology continues to advance, the role of ODM manufacturers in shaping the future of metal stamping cannot be underestimated.
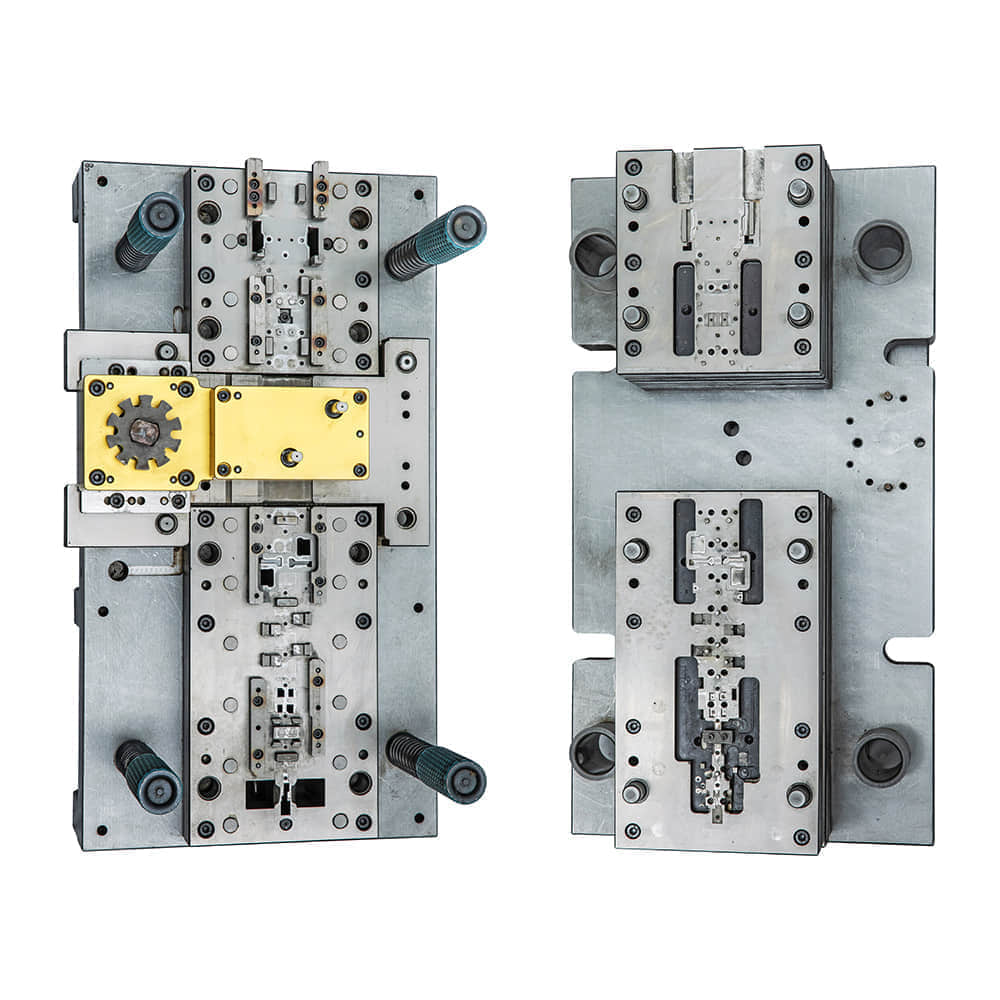