In the world of electrical distribution and circuit protection, electronic molded case circuit breakers (MCCBs) play a pivotal role in ensuring the safety and reliability of electrical systems. These devices are designed to interrupt electrical currents in the event of overloads or short circuits, preventing potential damage to equipment and, most importantly, ensuring the safety of people working with or around electricity. Behind the scenes of this critical technology, a manufacturer stands at the forefront of innovation, setting the standards for excellence in MCCB production.
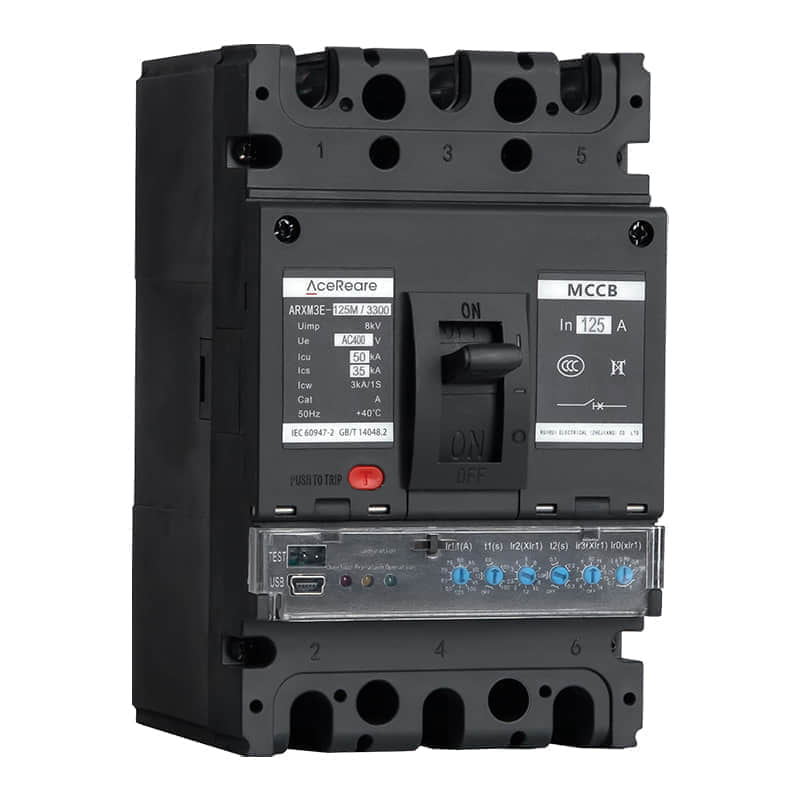
Pioneering Excellence
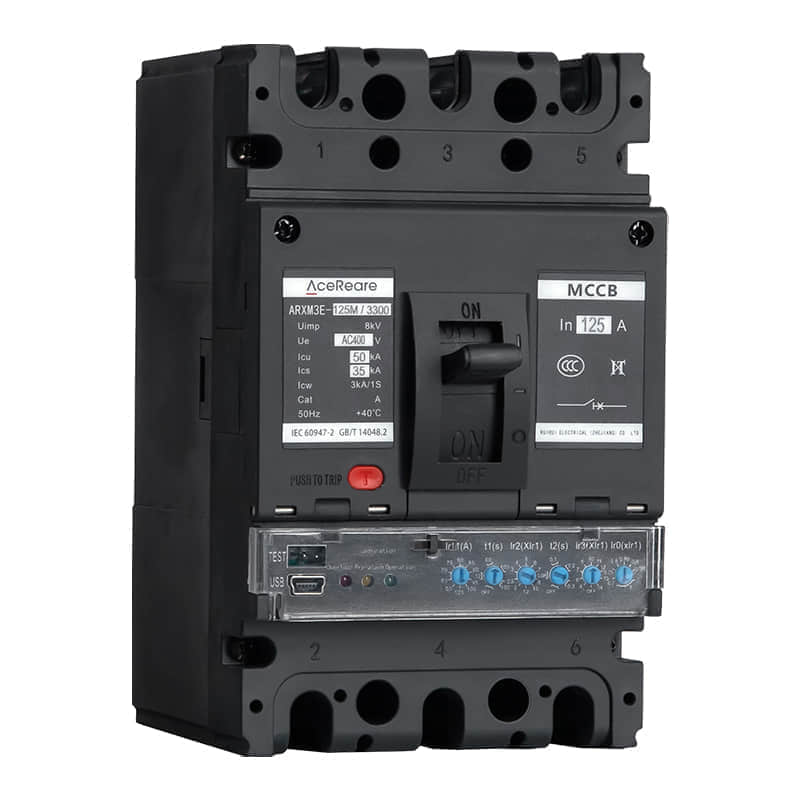
The manufacturer of electronic molded case circuit breakers has a rich history of pioneering excellence in the field of electrical protection. With a legacy dating back decades, the company has consistently pushed the boundaries of what MCCBs can achieve. From their humble beginnings to their current global presence, their commitment to quality and innovation has remained unwavering. Cutting-Edge Technology At the heart of their success lies an unrelenting dedication to cutting-edge technology. The manufacturer invests heavily in research and development, ensuring that their MCCBs are at the forefront of industry advancements. This commitment to innovation has resulted in MCCBs that are not only more efficient but also more intelligent. Their MCCBs are equipped with advanced digital technologies, including microprocessors and sensors, allowing for precise monitoring of electrical currents. This level of sophistication enables real-time analysis of electrical loads and rapid response to abnormal conditions, thus minimizing downtime and reducing the risk of electrical fires or other hazards. Global Reach The manufacturer’s influence extends far beyond their home base. With a global network of distribution and service centers, they are able to meet the needs of customers worldwide. This widespread presence ensures that their MCCBs are readily available to industries and businesses regardless of their location. It also allows them to provide timely support and maintenance services to keep electrical systems running smoothly. Commitment to Sustainability In today’s world, sustainability is a top priority. The manufacturer recognizes this and is committed to reducing its environmental footprint. They have implemented eco-friendly manufacturing practices, using materials and processes that minimize waste and energy consumption. Additionally, their MCCBs are designed for longevity, reducing the need for frequent replacements and further contributing to sustainability efforts. Custom Solutions One of the manufacturer’s key strengths is their ability to provide custom solutions to meet the unique needs of their customers. They understand that every industry and application has specific requirements when it comes to circuit protection. Whether it’s a specialized MCCB for a renewable energy project or a high-capacity solution for an industrial application, they have the expertise and flexibility to deliver tailor-made solutions. Unparalleled Support Beyond their products, the manufacturer is known for their unparalleled customer support. They have a team of highly trained engineers and technicians who are readily available to assist customers with technical inquiries, installation, and maintenance. This commitment to customer satisfaction has earned them a reputation for reliability and trustworthiness. Future Innovations Looking ahead, the manufacturer shows no signs of slowing down. They continue to invest in research and development, exploring new avenues for enhancing MCCB technology. As the world becomes more reliant on electricity, the role of MCCBs in ensuring safety and reliability will only become more critical. The manufacturer is poised to lead the way in shaping the future of electronic molded case circuit breakers. In conclusion, the manufacturer of electronic molded case circuit breakers is not just a producer of electrical devices; they are pioneers of innovation, champions of sustainability, and a trusted partner for industries worldwide. Their unwavering commitment to excellence ensures that our electrical systems remain safe and reliable, both now and in the future.
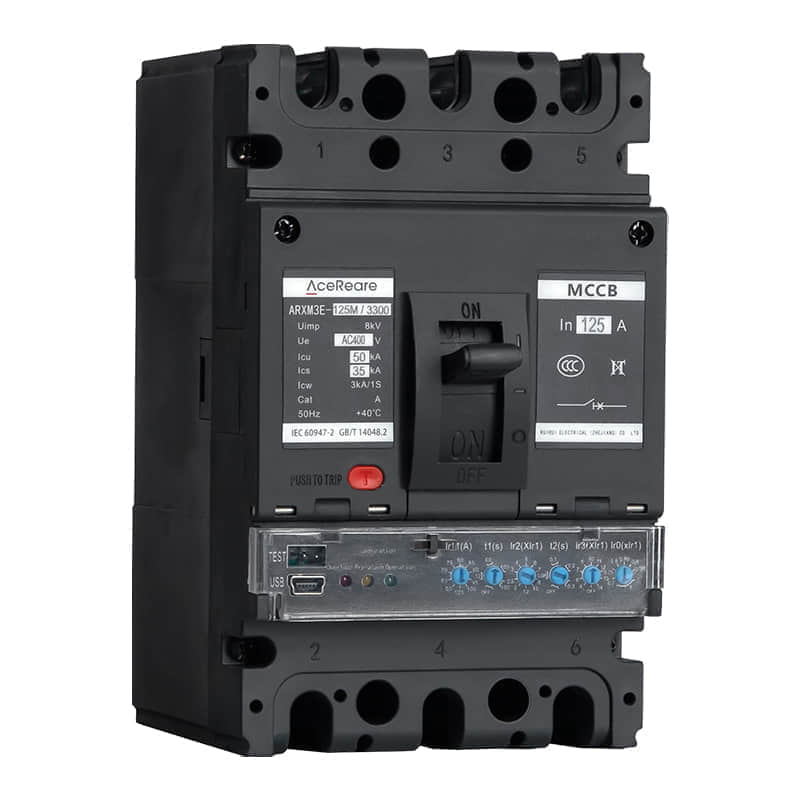