In the world of electrical engineering and power distribution, precision and reliability are paramount. To meet these stringent demands, the choice of components plays a critical role. Among these components, the frame circuit breaker drawer switch stands out as a vital element in ensuring the safe and efficient operation of electrical systems. In this article, we will delve into the world of frame circuit breaker drawer switches and explore the significance of partnering with a trusted OEM manufacturer in delivering top-notch solutions.

Understanding the Frame Circuit Breaker Drawer Switch
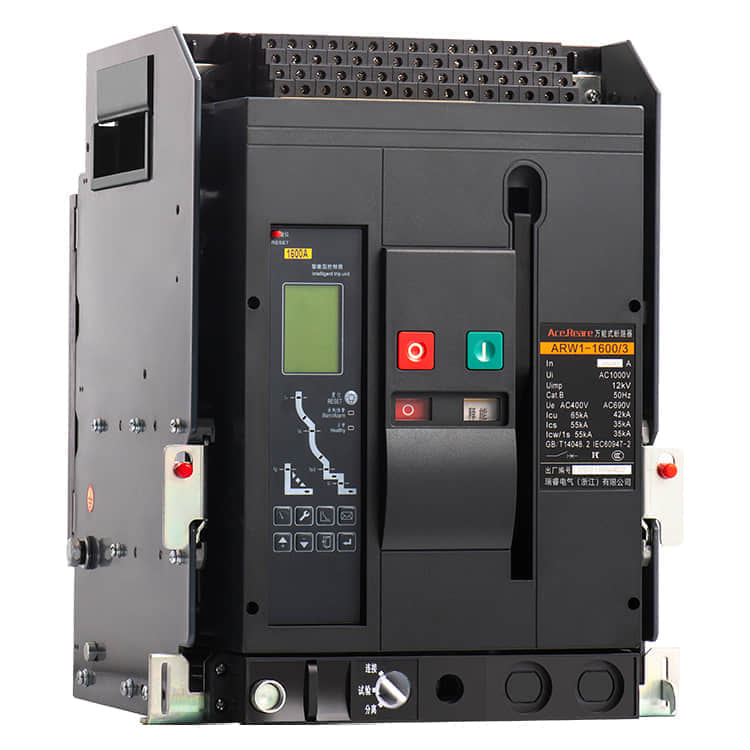
A frame circuit breaker drawer switch, often referred to simply as a drawer switch, is an integral part of electrical cabinets and control panels. Its primary function is to control and disconnect electrical circuits when necessary. The device is designed to fit within the frame of a circuit breaker, allowing for easy installation and operation. This compact but crucial component serves as a gateway to safety and efficient power distribution. The OEM Advantage In today’s dynamic market, where precision and quality are non-negotiable, partnering with an original equipment manufacturer (OEM) for frame circuit breaker drawer switches is a strategic choice. OEM manufacturers specialize in producing components that meet the highest industry standards. Here’s why working with an OEM stands out as a smart decision: 1. Expertise and Specialization OEM manufacturers focus exclusively on producing specific components, such as frame circuit breaker drawer switches. Their dedication to specialization ensures in-depth knowledge of the product, leading to superior design, engineering, and production processes. 2. Quality Assurance Quality is a non-negotiable factor in electrical components, where safety is paramount. OEMs prioritize rigorous quality control measures to deliver products that consistently meet or exceed industry standards. Their reputation relies on the reliability of their components. 3. Customization Options OEM manufacturers understand that one size does not fit all. They offer customization options, allowing clients to tailor frame circuit breaker drawer switches to their unique specifications. This flexibility is invaluable when designing complex electrical systems. 4. Regulatory Compliance Electrical components must adhere to strict safety and regulatory standards. OEMs stay up-to-date with these regulations and ensure that their products are compliant, reducing potential risks and liabilities for their customers. Choosing the Right OEM Manufacturer Selecting the right OEM manufacturer for frame circuit breaker drawer switches is a crucial step in ensuring the success of your electrical projects. Here are some factors to consider: 1. Reputation and Track Record Research the manufacturer’s reputation and track record. Customer reviews, industry certifications, and past projects can provide valuable insights into their capabilities and reliability. 2. Technical Expertise Evaluate the manufacturer’s technical expertise. Do they have a skilled engineering team? Are they up-to-date with the latest industry advancements and trends? A knowledgeable team can make a significant difference in the quality of the final product. 3. Quality Control Inquire about the manufacturer’s quality control processes. Are they ISO certified? What steps do they take to ensure product quality and consistency? Reliable quality control procedures are a must. 4. Customization Options Consider whether the manufacturer offers customization options to meet your specific requirements. A manufacturer that can adapt their products to your needs can be a valuable partner. Conclusion In the intricate world of electrical engineering and power distribution, the frame circuit breaker drawer switch plays a pivotal role. Choosing an OEM manufacturer for these critical components is a strategic move that ensures precision, quality, and compliance with industry standards. The right OEM partner can contribute significantly to the success and safety of your electrical projects, making it a decision well worth considering in your engineering endeavors.
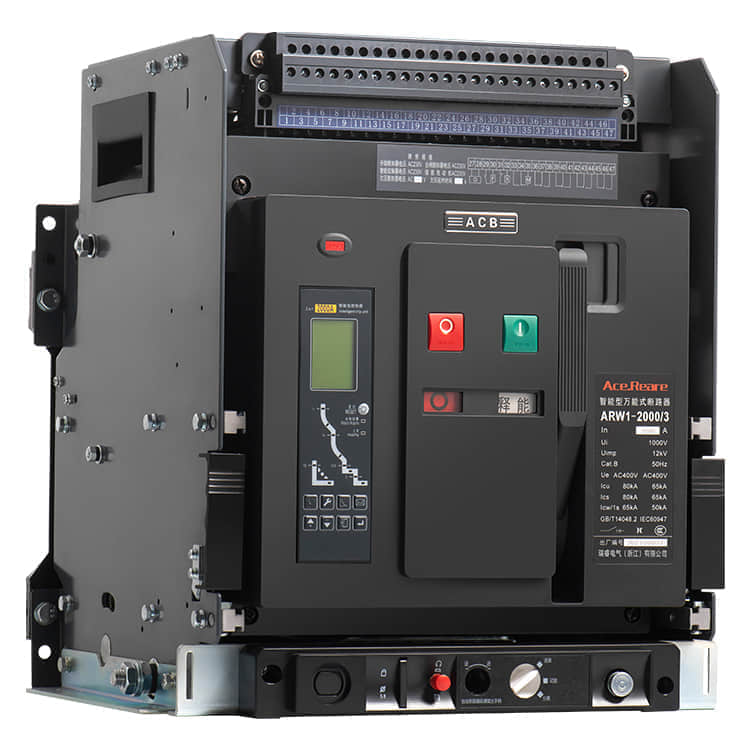