PTC Fan Heaters: A Modern Marvel of Heating Technology
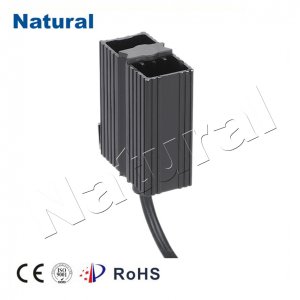
Introduction As the seasons change and the weather turns colder, the need for effective heating solutions becomes paramount. Among the numerous options available in the market, PTC (Positive Temperature Coefficient) fan heaters have emerged as a modern marvel of heating technology. These compact and versatile devices have gained popularity for their efficiency, safety, and convenience. In this article, we will explore the features and benefits of PTC fan heaters and understand why they have become a go-to choice for many households and businesses. Efficient Heating One of the standout features of PTC fan heaters is their remarkable efficiency in generating heat. Unlike traditional heating elements that rely on resistance to generate warmth, PTC heaters use a unique ceramic heating element with a positive temperature coefficient. This means that as the temperature rises, their resistance increases, reducing the risk of overheating and ensuring consistent heat output. PTC fan heaters excel at quickly heating up a room, making them ideal for those chilly winter mornings when you need rapid warmth. Compact Design PTC fan heaters are designed with compactness in mind. Their small, portable size makes them a versatile heating solution for various settings. Whether you need to warm up a bedroom, office, or even a garage, PTC fan heaters are easy to move around and position exactly where you need them. This portability factor allows users to optimize their heating efficiency and save energy by only heating the spaces they occupy. Safety First Safety is a paramount concern when it comes to heating appliances, and PTC fan heaters excel in this regard. Thanks to their self-regulating heating element, PTC heaters are less likely to overheat or pose a fire hazard compared to traditional heaters. Additionally, they often come equipped with features such as tip-over protection and overheat protection, which automatically shut off the device if it senses any irregularities. These safety measures offer peace of mind to users, especially those with children or pets. Energy Efficiency PTC fan heaters are not only efficient at generating heat but are also energy-efficient. Their self-regulating feature ensures that they consume only the necessary amount of energy to maintain a consistent temperature. This not only reduces electricity bills but also contributes to a more sustainable environment by minimizing energy wastage. Adjustable Settings To cater to individual heating preferences, PTC fan heaters often come with adjustable settings. Users can choose from different temperature levels and fan speeds to create the perfect indoor climate. This flexibility allows PTC fan heaters to adapt to changing weather conditions and user comfort, making them a versatile heating solution. Quiet Operation Nobody wants a noisy heater disrupting their peace and quiet. PTC fan heaters are known for their quiet operation, making them an excellent choice for bedrooms, offices, and other quiet spaces. You can enjoy the warmth without the distracting noise often associated with some heating appliances. Conclusion In summary, PTC fan heaters have revolutionized the way we approach heating solutions. Their efficient, compact, and safe design, coupled with energy-saving features, makes them a top choice for individuals and businesses alike. As we continue to seek ways to stay warm and comfortable during the colder months, PTC fan heaters stand out as a modern marvel of heating technology, providing reliable and effective warmth while prioritizing safety and energy efficiency. So, whether you’re looking to beat the winter chill or enhance the coziness of your workspace, consider the power and versatility of PTC fan heaters.