In today’s rapidly advancing world, a stable and uninterrupted power supply is essential for businesses, industries, and households. Moulded Case Circuit Breakers (MCCBs) play a crucial role in safeguarding electrical systems from overloads and short circuits. In China, MCCB suppliers have been at the forefront of providing high-quality electrical protection solutions, ensuring a reliable power supply for various applications.
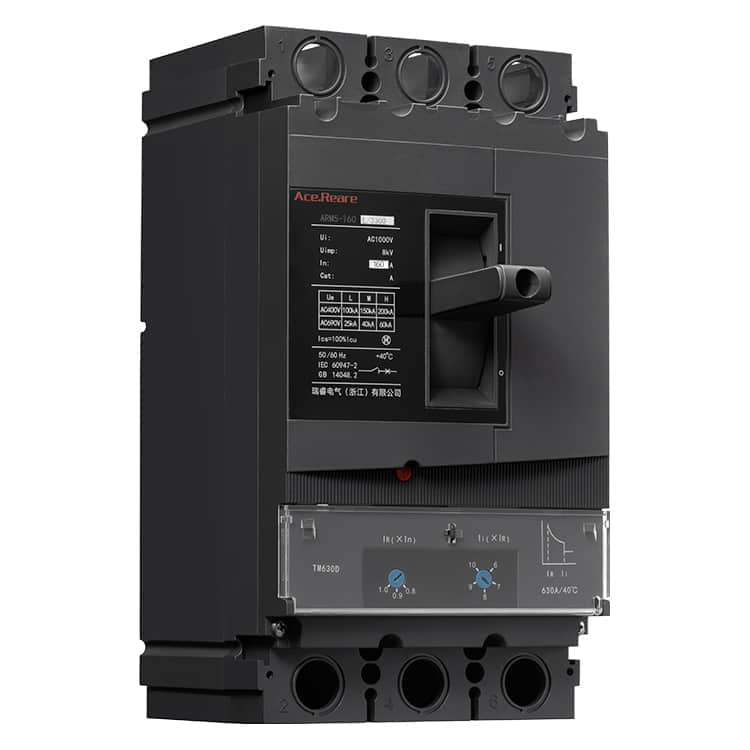
Introduction to Moulded Case Circuit Breakers (MCCBs)
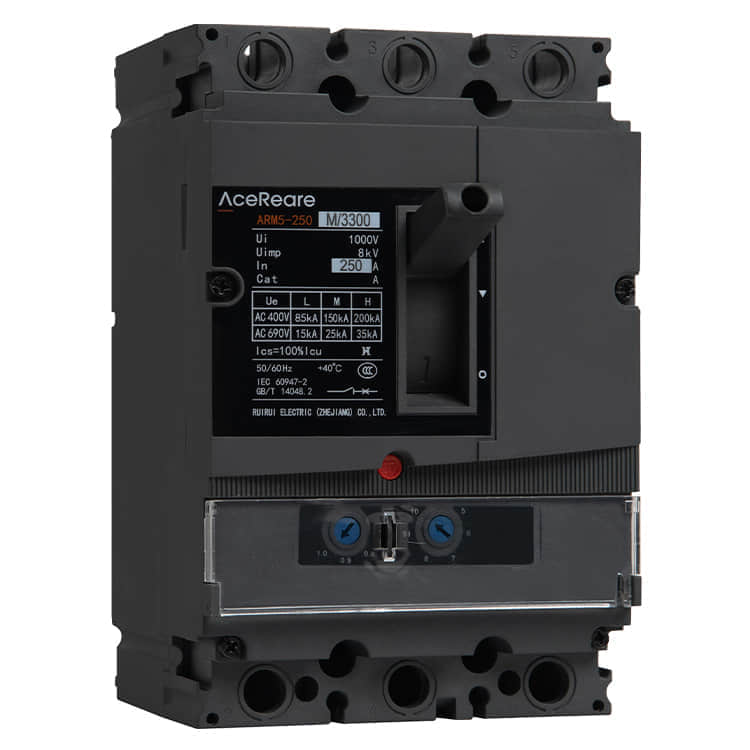
Moulded Case Circuit Breakers are a vital component of electrical distribution systems. They are designed to protect circuits and equipment from the damaging effects of excessive current. MCCBs are widely used in industrial and commercial settings due to their ability to disconnect the circuit when abnormal conditions occur, thus preventing potential fires, electrical damage, and downtime. The Importance of Quality MCCB Suppliers China has emerged as a significant hub for MCCB production and supply. Chinese MCCB suppliers have gained recognition globally for their commitment to delivering reliable and high-performance MCCBs. These suppliers understand the critical role played by MCCBs in electrical safety and have invested in research and development to meet international standards and certifications. Key Advantages of Choosing a Moulded Case Circuit Breaker China Supplier Diverse Product Range: Chinese MCCB suppliers offer a wide range of MCCBs, catering to various voltage levels, current ratings, and breaking capacities. This diversity ensures that customers can find the perfect MCCB for their specific needs. Quality Assurance: Many Chinese MCCB suppliers adhere to strict quality control standards, ensuring that their products meet or exceed industry requirements. This commitment to quality translates into enhanced safety and reliability for end-users. Competitive Pricing: The competitive nature of the MCCB market in China often results in cost-effective solutions for customers without compromising quality. This affordability makes it easier for businesses of all sizes to invest in MCCBs. Technical Expertise: Chinese MCCB suppliers employ skilled engineers and technicians who provide technical support, guidance, and customized solutions to address unique electrical protection challenges. Global Reach: Several Chinese MCCB suppliers have expanded their reach beyond domestic borders, exporting their products to international markets. This global presence demonstrates their commitment to meeting the diverse needs of customers worldwide. Examples of Prominent MCCB Suppliers in China CHINT Group Corporation: CHINT is one of China’s leading MCCB suppliers, known for its wide product range, innovation, and commitment to quality. ABB: While ABB is a multinational corporation, it has a significant presence in China, manufacturing and supplying MCCBs that meet global standards. Legrand: Legrand, with a strong presence in China, offers MCCBs known for their performance and reliability. Conclusion In a world where electricity is the lifeblood of modern society, Moulded Case Circuit Breakers are a critical line of defense against electrical hazards. Chinese MCCB suppliers have risen to the occasion, providing a wide array of reliable and high-quality MCCBs to meet the growing demand for electrical protection solutions. Their commitment to quality, competitive pricing, and technical expertise make them invaluable partners in ensuring a stable and secure power supply for a variety of applications. When it comes to power protection, choosing a Moulded Case Circuit Breaker China Supplier is a smart and responsible choice.
