In the realm of manufacturing, precision is paramount. One of the key players in achieving this precision is the metal stamping die manufacturer. These skilled artisans create the molds and dies that enable the mass production of intricate metal components used in various industries. In this article, we will delve into the world of metal stamping die manufacturers, exploring their vital role and the craftsmanship behind their work.
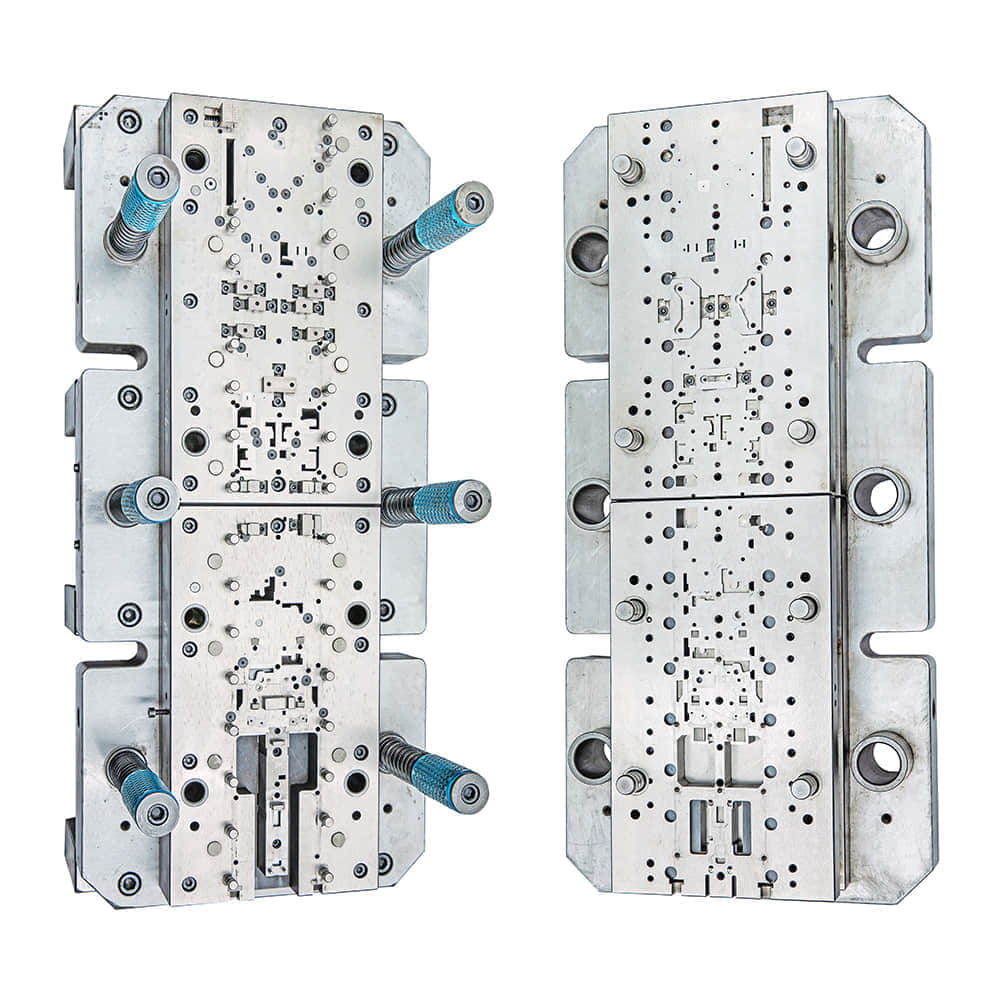
The Art of Metal Stamping Die Manufacturing
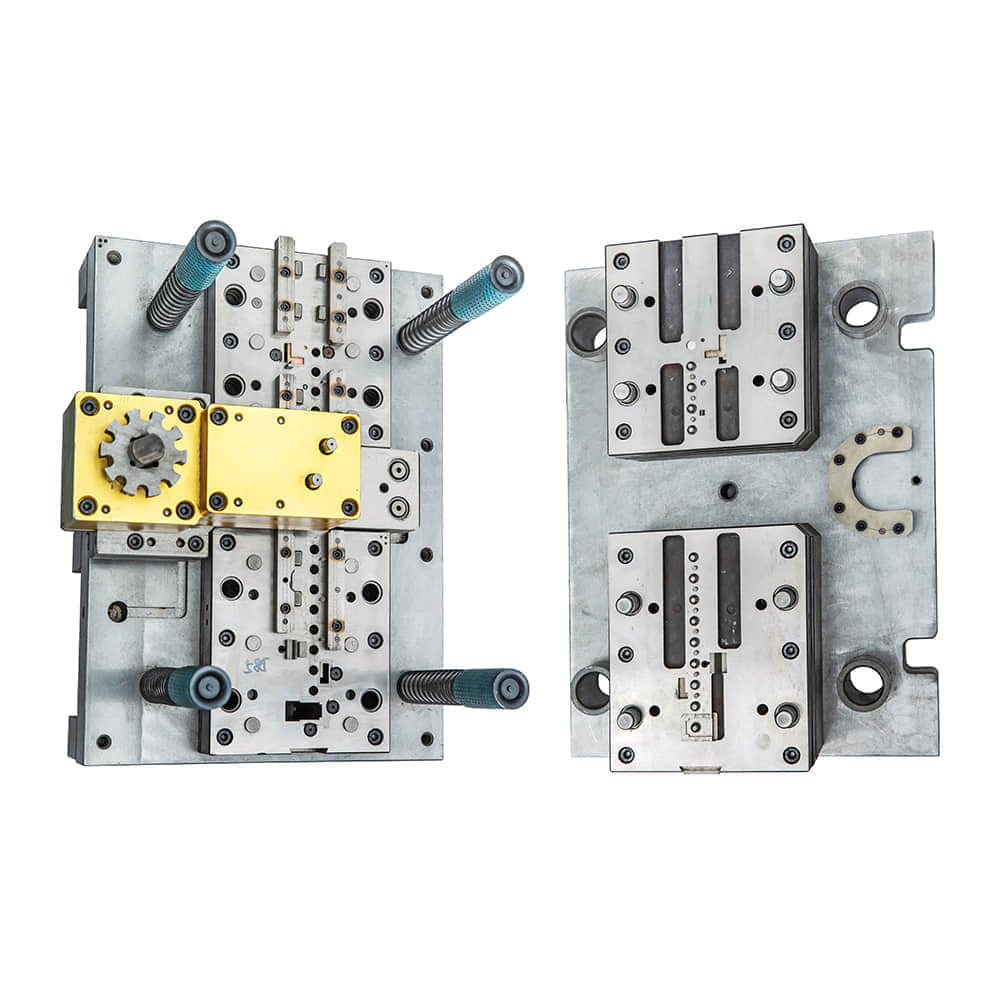
Metal stamping die manufacturers are the unsung heroes of modern industry. Their craftsmanship lies in designing, fabricating, and maintaining the dies used to shape raw metal sheets into specific forms. These forms can range from simple brackets and clips to complex automotive parts and intricate electronics components. Precision is Paramount One of the defining characteristics of metal stamping die manufacturers is their unwavering commitment to precision. Every cut, every impression, and every detail must be meticulously crafted to ensure that each stamped metal piece meets exacting standards. This precision is critical in industries such as aerospace, automotive, and electronics, where the smallest deviation can lead to costly defects or failures. Advanced Technology Meets Traditional Craftsmanship Modern metal stamping die manufacturers have embraced advanced technologies to enhance their precision and efficiency. Computer-aided design (CAD) software enables them to create intricate die designs with remarkable accuracy. Computer numerical control (CNC) machining further ensures that these designs are translated into physical dies with minimal errors. However, technology alone cannot replace the expertise that comes with years of experience. Skilled artisans play a crucial role in the final assembly and fine-tuning of the dies. They possess an intimate knowledge of metal properties, heat treatment techniques, and the subtle nuances that can affect the quality of the stamped parts. Tailored Solutions for Diverse Industries Metal stamping die manufacturers do not produce one-size-fits-all solutions. Instead, they collaborate closely with clients to understand their specific needs. Whether it’s a requirement for high-volume production or the creation of prototypes for a new product, these manufacturers tailor their processes to meet the unique demands of each project. Quality Assurance at Every Stage Quality control is embedded in every aspect of metal stamping die manufacturing. From the initial design phase to the final inspection, manufacturers employ rigorous testing and measurement techniques to ensure that the dies meet the highest standards. This dedication to quality extends to the materials used, as well as the precision machinery employed in the production process. Environmental Responsibility In addition to precision and quality, many metal stamping die manufacturers are committed to environmental responsibility. They seek sustainable solutions in die production, waste reduction, and energy efficiency. This eco-conscious approach aligns with the broader shift towards environmentally friendly manufacturing practices. The Future of Metal Stamping Die Manufacturing As industries continue to evolve and demand for precision metal components grows, metal stamping die manufacturers will remain at the forefront of innovation. Advancements in materials, technologies, and processes will drive further improvements in efficiency and precision. In conclusion, metal stamping die manufacturers are the unsung heroes behind many of the metal components that shape our modern world. Their craft combines advanced technology with time-honored skills to create precision tools that drive industries forward. As we look to the future, their role will only become more critical in meeting the demands of a rapidly changing manufacturing landscape.
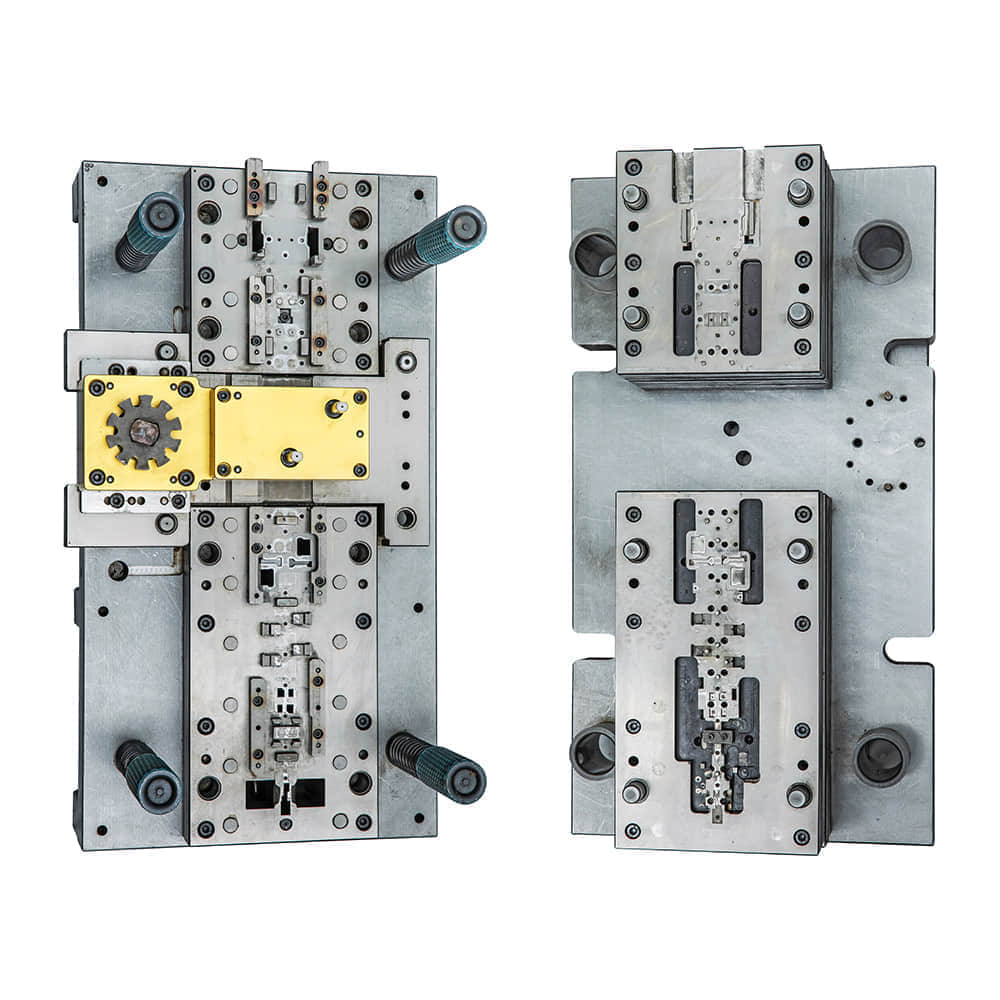