In the electrical industry, molded case switches play a crucial role in controlling and managing various electrical equipment and systems. These switches, often referred to as combination switches or transfer switches, offer a compact, convenient, and reliable solution for a wide range of applications. Behind the scenes, molded case switch manufacturers play a pivotal role in supplying these essential components.
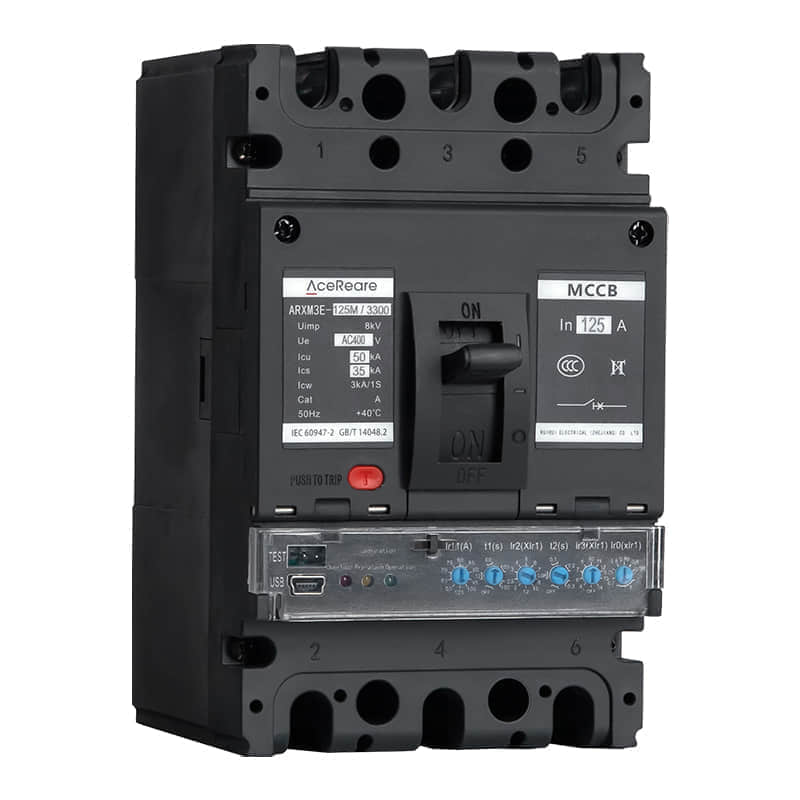
Molded case switches are designed to provide a secure and efficient means of controlling electrical circuits. They are composed of one or more switching units, each capable of controlling a single or multiple circuits. These switches are typically enclosed in a molded case, which protects the internal components from dust, moisture, and other environmental factors that could affect their performance.

The manufacturing process of molded case switches requires precision and expertise. Molded case switch manufacturers employ advanced manufacturing techniques and equipment to ensure consistent product quality. From the selection of materials to the assembly of components, every step is carefully monitored to guarantee durability, reliability, and safety. Moreover, molded case switch manufacturers are constantly innovating to meet the evolving needs of the market. They offer a diverse range of switch types, sizes, and ratings to cater to different applications. Whether it’s for industrial machinery, building automation, or residential use, these manufacturers strive to provide the perfect fit for every requirement.
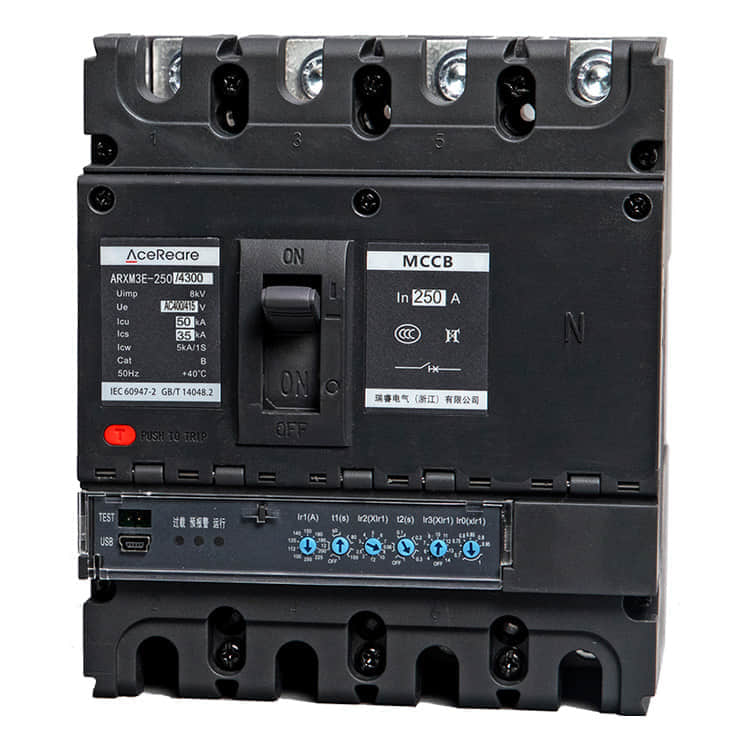