Introduction
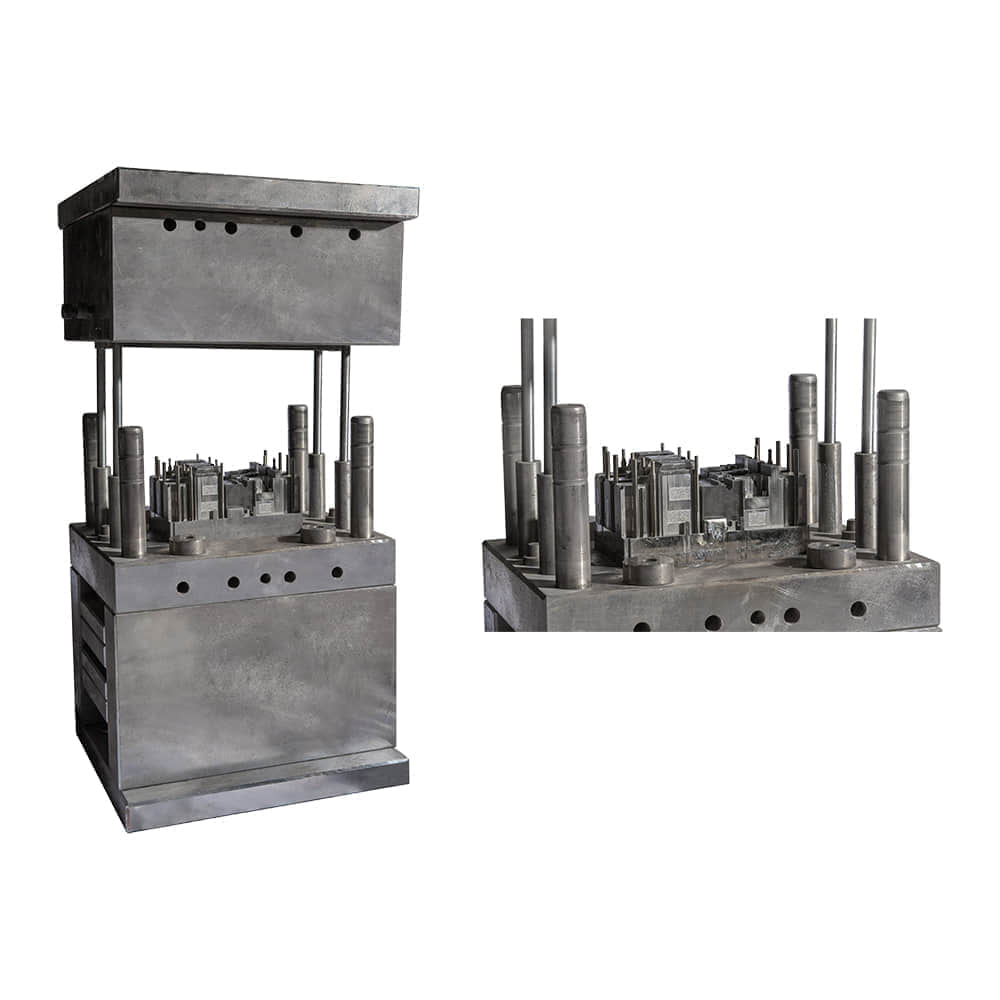
In the world of plastics manufacturing, DMC (Dough Molding Compounds) molding manufacturers occupy a pivotal position. These manufacturers specialize in the production of high-quality, fiber-reinforced thermoplastic parts using the DMC molding process. This process, which involves the placement of DMC material into a mold and then subjecting it to heat and pressure to achieve the desired shape, has revolutionized the manufacturing industry.
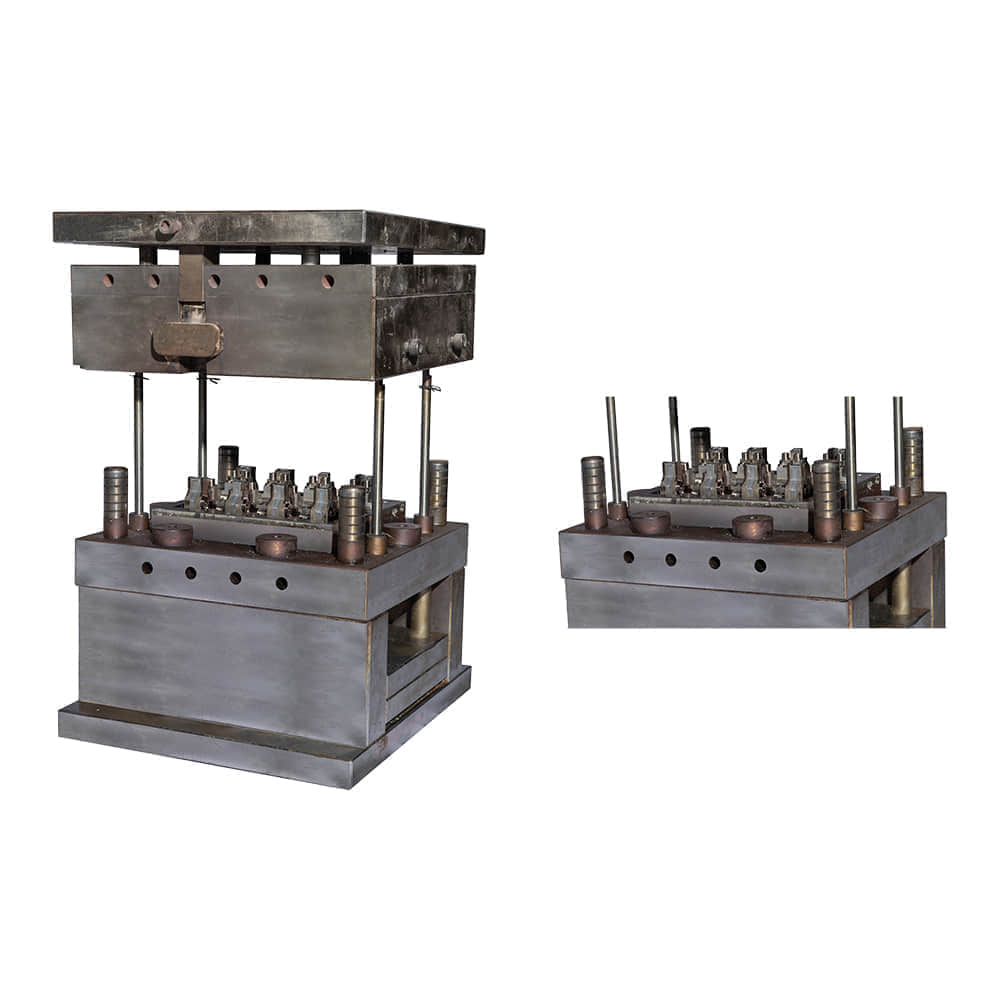
What is DMC Molding? DMC molding is a thermosetting plastic molding process that involves the use of a pre-mixed, semi-solid material called DMC. This material, which consists of short fibers embedded in a thermosetting resin matrix, offers excellent mechanical properties, dimensional stability, and surface finish. The DMC material is placed into a mold, which is then closed and heated to initiate the curing process. The result is a strong, durable part with consistent dimensions and a smooth finish. The Role of DMC Molding Manufacturers DMC molding manufacturers play a crucial role in the supply chain of various industries. They not only produce high-quality parts but also collaborate with customers to design and develop molds that meet specific application requirements. These manufacturers have the expertise and equipment necessary to handle complex mold designs, ensuring that each part produced meets the highest standards of quality and precision.
