Industrial thermostats play a crucial role in maintaining temperature stability in various manufacturing processes. These devices have come a long way since their inception, evolving to meet the increasingly complex demands of modern industries. In this article, we will explore the journey of industrial thermostats, from their humble beginnings to the advanced systems of today.
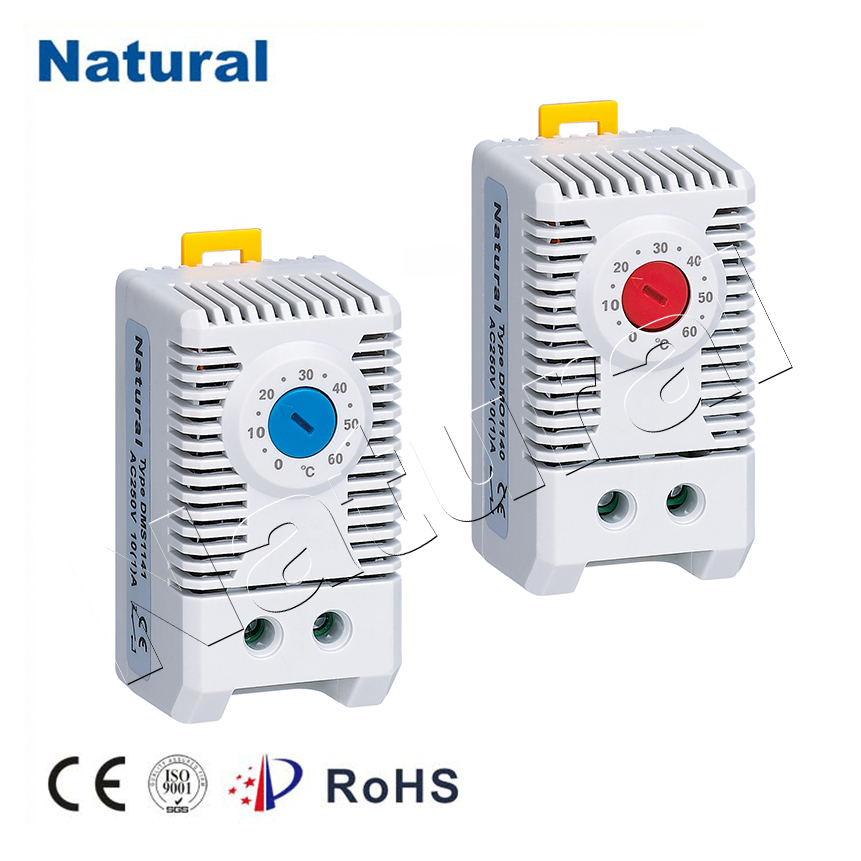
Early Days: Simple Temperature Regulation The concept of temperature control has been around for centuries, but it wasn’t until the 19th century that the first rudimentary industrial thermostats emerged. These early devices relied on simple mechanical mechanisms, such as bimetallic strips that expanded or contracted with temperature changes. When these strips moved, they would trigger switches to turn heating or cooling systems on or off. While basic, these thermostats represented a significant advancement in temperature regulation for various industries, including food processing and textile manufacturing. The Rise of Electronic Thermostats The mid-20th century brought a major breakthrough in thermostat technology with the introduction of electronic components. The transition from mechanical to electronic thermostats allowed for greater precision in temperature control. These thermostats used thermistors and other sensors to detect temperature changes and electronic circuits to manage heating or cooling systems. This enhanced accuracy was vital for industries like pharmaceuticals, where even a slight deviation from the desired temperature could ruin products. The Digital Revolution: Programmable Thermostats As digital technology continued to advance, programmable thermostats entered the scene. These devices allowed for the automation of temperature control, making it possible to create temperature profiles that suited specific processes. Manufacturers could now program thermostats to follow complex temperature curves, enabling more efficient and consistent production. Industries like electronics manufacturing benefited greatly from these advancements, as they required tight temperature tolerances to produce delicate components. Smart Industrial Thermostats In recent years, the industrial thermostat has entered the era of smart technology. These thermostats are equipped with sensors that can detect not only temperature but also humidity, pressure, and other environmental factors. The data collected by these sensors is transmitted to sophisticated control systems that can make real-time adjustments to maintain precise conditions. This level of control is invaluable in industries such as aerospace, where the slightest variation in temperature or humidity can impact the quality of materials and components. Integration with Industry 4.0 In the context of Industry 4.0, industrial thermostats have become integral components of interconnected manufacturing systems. These thermostats can communicate with other equipment and software platforms, allowing for seamless integration into the broader production process. They can also provide valuable data for predictive maintenance, helping to prevent costly equipment failures and downtime. Conclusion: A Future of Precision Industrial thermostats have evolved from simple mechanical devices to sophisticated, smart systems that play a vital role in modern manufacturing. Their ability to provide precise temperature control has revolutionized industries ranging from pharmaceuticals to electronics, enabling higher quality and more efficient production. As technology continues to advance, we can expect industrial thermostats to become even more integral to the manufacturing processes of the future, helping industries achieve new levels of precision and reliability.