Thermosetting compression moulding is a widely used manufacturing process that plays a crucial role in producing a vast range of products across various industries. This article explores the fundamentals of thermosetting compression moulding, its applications, advantages, and some key considerations for successful implementation.
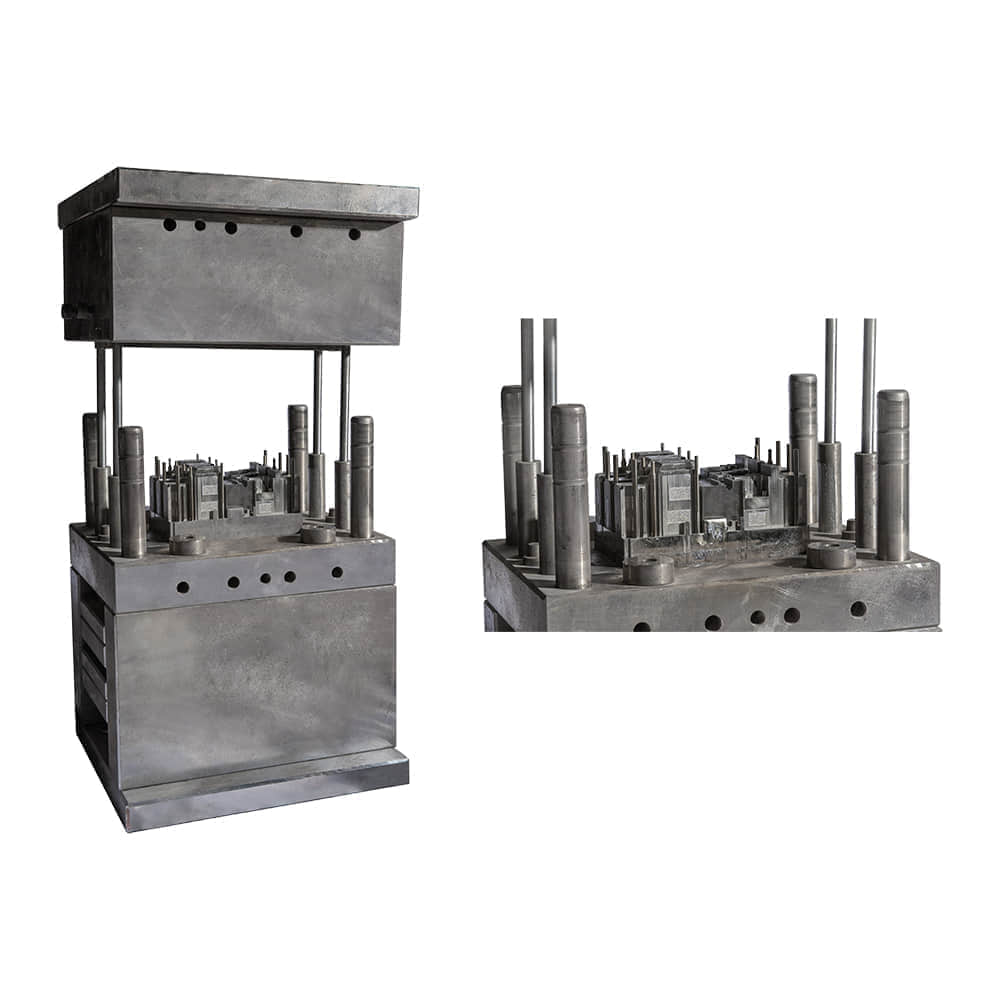
Understanding Thermosetting Compression Moulding
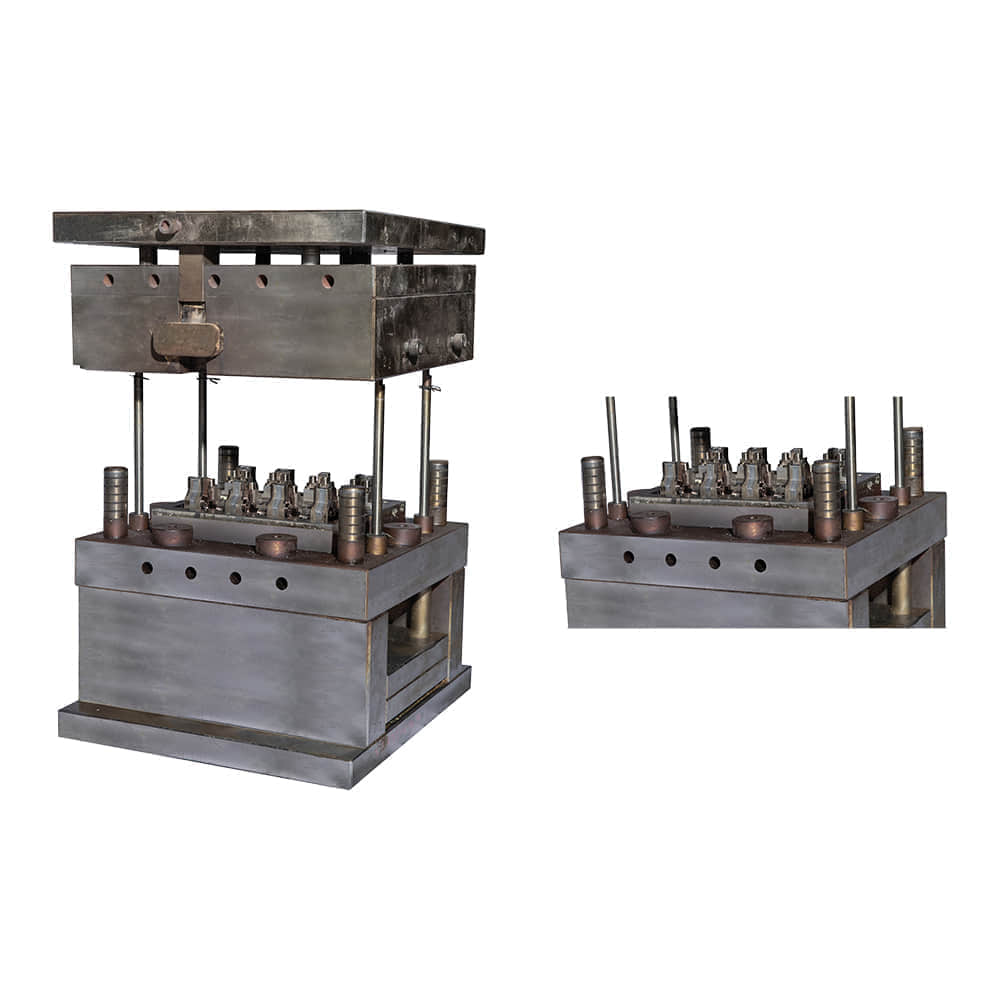
Thermosetting compression moulding is a manufacturing technique used to shape thermosetting materials into desired forms by subjecting them to heat and pressure. Thermosetting materials, in contrast to thermoplastics, undergo a chemical reaction during the moulding process that irreversibly sets their shape. This transformation makes them highly resilient and capable of withstanding elevated temperatures. Applications This manufacturing process finds applications in numerous industries, including automotive, aerospace, electrical, and consumer goods. Some common products produced through thermosetting compression moulding include: Composite Components:Thermosetting materials are often used to create high-strength composite components in the aerospace and automotive industries, where lightweight and durable materials are essential. Electrical Insulators:The excellent electrical insulation properties of thermosetting materials make them ideal for producing electrical components such as circuit breakers, transformers, and insulators. Kitchenware:Many heat-resistant kitchen utensils and cookware items are made using this method due to their ability to withstand high temperatures without deformation. Automotive Parts:Brake pads, engine components, and interior trim pieces in the automotive sector are frequently manufactured using thermosetting compression moulding. Advantages of Thermosetting Compression Moulding Strength and Durability:Thermosetting materials offer superior strength and durability, making them suitable for applications that require robust and long-lasting products. Heat Resistance:These materials can withstand high temperatures without softening or losing their structural integrity, making them suitable for applications in high-temperature environments. Chemical Resistance:Thermosetting materials are often resistant to chemicals, which makes them suitable for applications where exposure to corrosive substances is a concern. Complex Shapes:Compression moulding allows for the production of complex shapes with precise dimensions, ensuring the final product meets the required specifications. Cost-Effective Mass Production:The efficiency and speed of the compression moulding process make it a cost-effective choice for mass production. Key Considerations Successful thermosetting compression moulding requires careful consideration of several factors: Material Selection:Choosing the right thermosetting material is crucial, as different materials offer varying properties and performance characteristics. Mould Design:The design of the mould must be precise and well-engineered to ensure the final product meets dimensional and quality requirements. Temperature and Pressure Control:Proper control of temperature and pressure during the moulding process is essential to achieve the desired material properties and product quality. Curing Time:The curing time, or the time the material spends under pressure and heat, should be optimized to achieve the desired material properties. Post-Moulding Processing:Some products may require post-moulding processes such as trimming, painting, or assembly, which should be factored into the production process. In conclusion, thermosetting compression moulding is a versatile and widely used manufacturing process that offers a range of benefits, including strength, durability, and heat resistance. Its applications span various industries, making it a valuable technique in modern manufacturing. To successfully implement this process, careful consideration of material selection, mould design, temperature and pressure control, curing time, and post-moulding processing is essential. With the right approach, thermosetting compression moulding can contribute to the production of high-quality, durable products across many sectors.
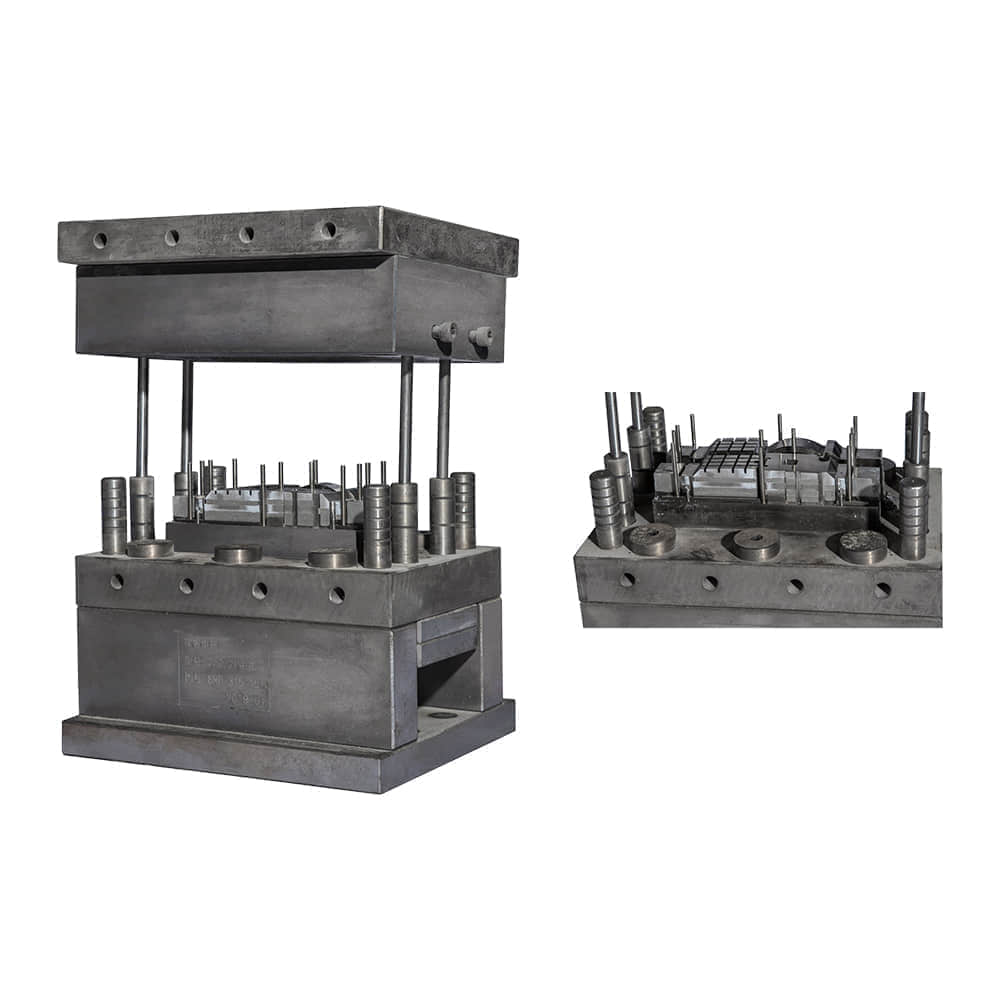