Blanking dies play a crucial role in the world of manufacturing, enabling the precise cutting and shaping of various materials. From sheet metal in the automotive industry to intricate parts in electronics, blanking dies are essential tools that transform raw materials into finished products. In this article, we will delve into the world of blanking dies, exploring their functions, types, and significance in modern manufacturing.
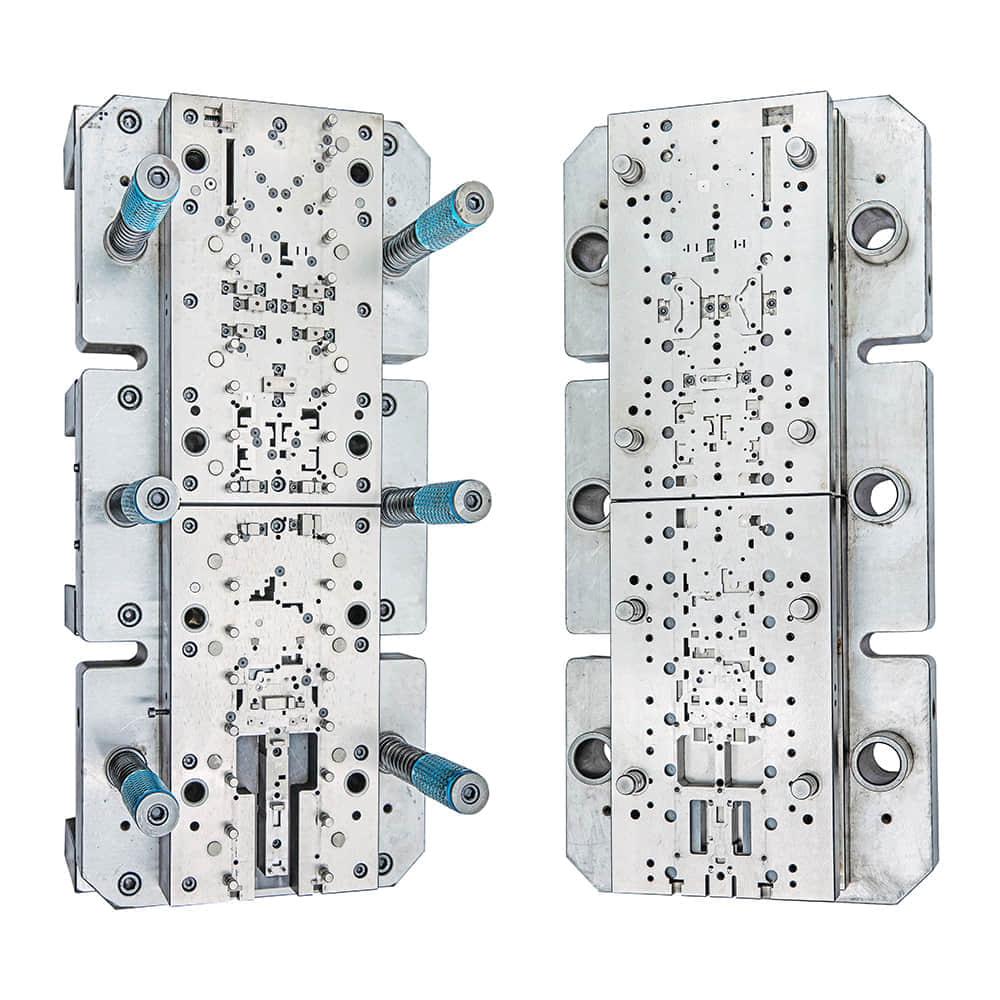
1. What Are Blanking Dies?
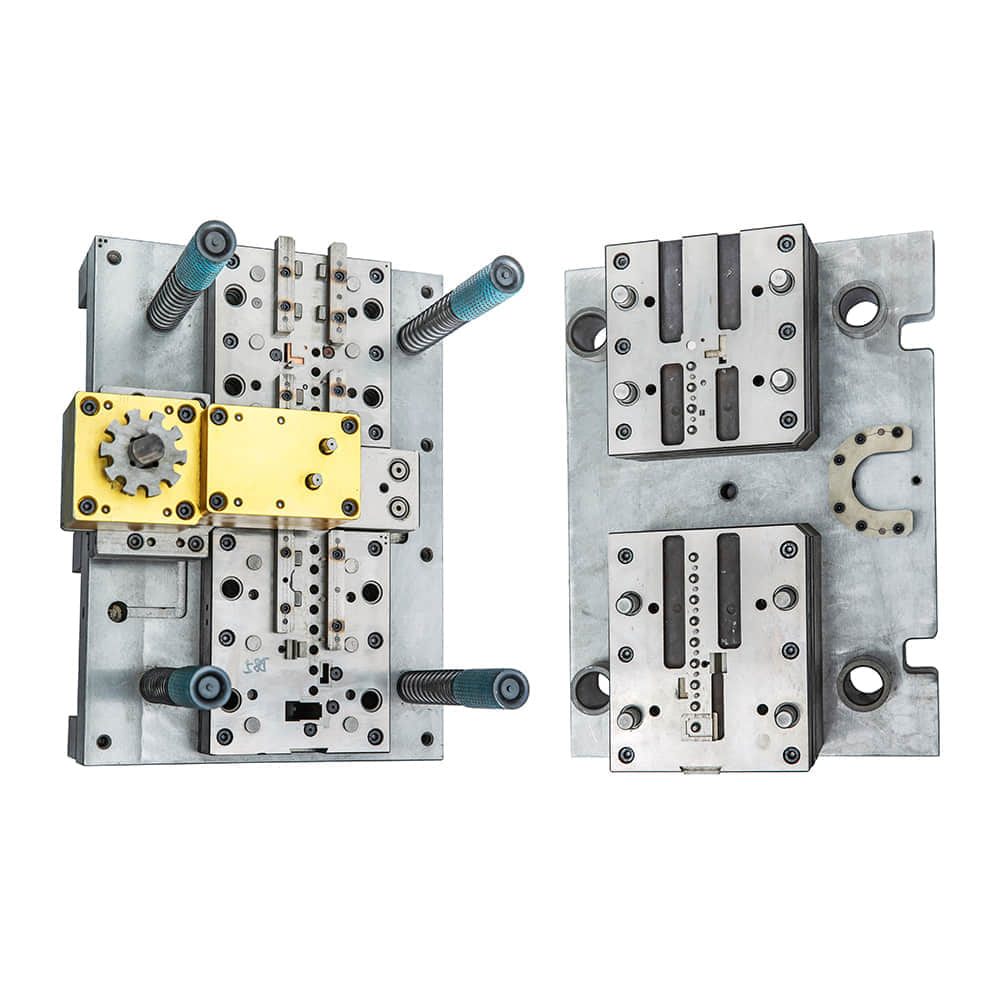
Blanking dies are specialized cutting tools designed to cut out specific shapes or blanks from a sheet or strip of material, leaving the desired part while removing the excess material. These dies are used in various industries, including automotive, aerospace, and electronics, to create components with high precision and efficiency. 2. The Function of Blanking Dies The primary function of blanking dies is to cut materials into precise shapes with tight tolerances. This process involves the following steps: a. Material Feeding:The raw material, typically a sheet or strip, is fed into the blanking die. b. Cutting:The blanking die, equipped with a sharp punch and die, cuts out the desired shape from the material. c. Ejection:The cut piece, known as the blank, is ejected from the die, leaving the waste material behind. d. Collection:The collected blanks can then undergo further processing or assembly into finished products. 3. Types of Blanking Dies There are several types of blanking dies, each designed for specific applications: a. Simple Blanking Die:This type of die is used to create simple shapes, such as circles or rectangles, and is often employed in the production of basic components. b. Compound Blanking Die:Compound dies are capable of cutting multiple shapes simultaneously, increasing production efficiency and reducing material waste. c. Progressive Blanking Die:Progressive dies are complex tools that perform a series of cutting operations in a single pass. They are commonly used for high-volume production of intricate parts. 4. Advantages of Blanking Dies Blanking dies offer several advantages in manufacturing: a. Precision:Blanking dies ensure high levels of accuracy, crucial in industries where tight tolerances are required. b. Efficiency:These dies can process materials quickly, leading to increased production rates. c. Material Savings:By minimizing waste material, blanking dies contribute to cost savings and sustainability efforts. d. Versatility:Blanking dies can be customized for various materials and shapes, making them suitable for a wide range of applications. 5. Challenges and Considerations While blanking dies are indispensable, they come with their set of challenges and considerations: a. Tool Wear:Continuous use can lead to wear and tear of the die, affecting the quality of the blanks. Regular maintenance is essential to prolong the die’s lifespan. b. Material Selection:The choice of material plays a vital role in the performance of blanking dies. Harder materials may require specialized dies and cutting techniques. c. Die Design:The design of the blanking die must be carefully considered to ensure it can handle the specific requirements of the production process. 6. Conclusion Blanking dies are essential tools in modern manufacturing, enabling the efficient and precise creation of components used in various industries. Their versatility, precision, and efficiency make them indispensable for producing high-quality products while minimizing material waste. As technology advances, blanking dies continue to evolve, further enhancing their role in shaping the world around us. Understanding the significance of blanking dies is essential for those involved in manufacturing and engineering, as these tools remain at the forefront of innovation and efficiency in material processing.
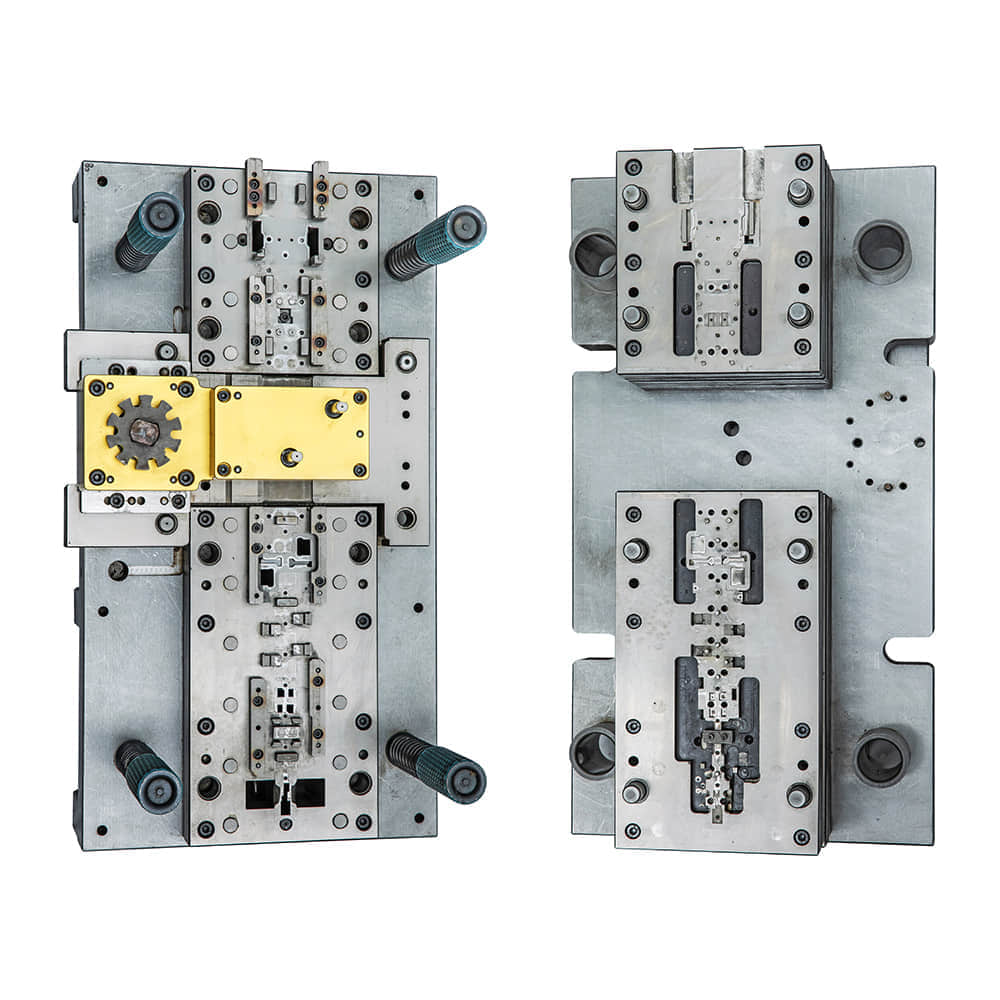