In the vast world of manufacturing, certain industries stand out as pioneers of precision and innovation. Molded case parts manufacturing is one such domain that plays a pivotal role in various sectors, including electrical, automotive, and industrial machinery. This article delves into the fascinating realm of molded case parts manufacturers, exploring their crucial role, technological advancements, and commitment to quality.
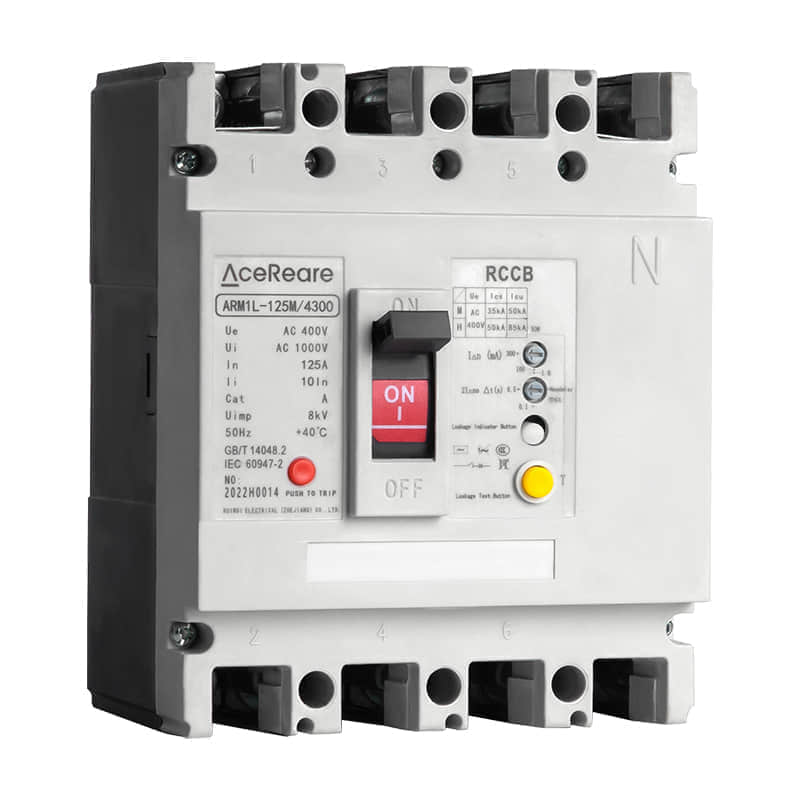
The Heartbeat of Modern Engineering
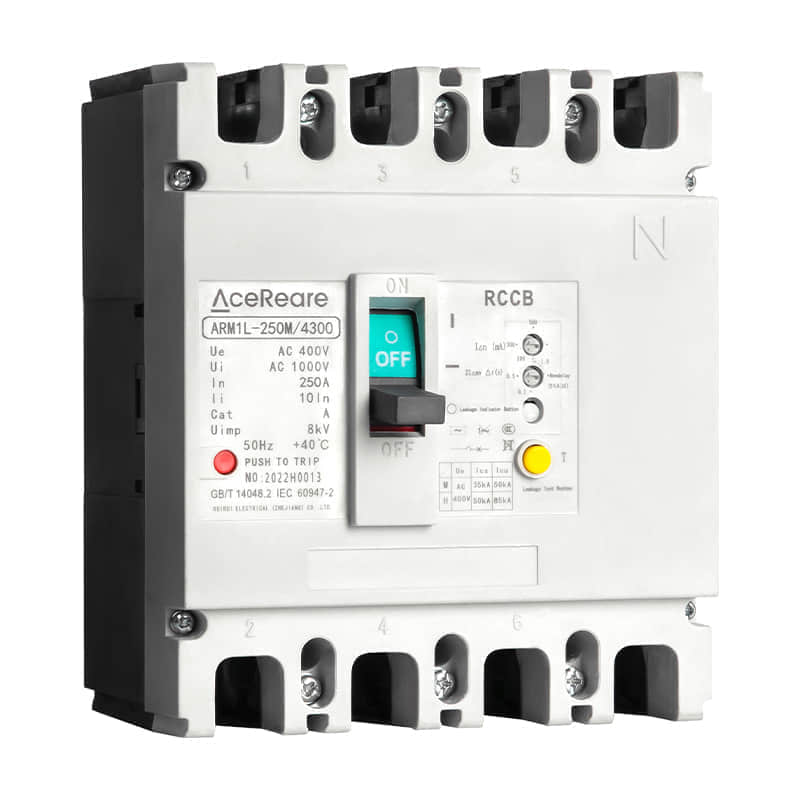
Molded case parts manufacturers serve as the backbone of modern engineering. These companies specialize in crafting essential components that are utilized in diverse applications. Whether it’s producing electrical circuit breaker cases, automotive engine parts, or intricate industrial machinery components, molded case parts manufacturers are integral to the functioning of numerous industries. Technological Advancements: Pioneering Excellence In the ever-evolving landscape of manufacturing, technology is the driving force behind innovation and excellence. Molded case parts manufacturers have embraced cutting-edge technologies to enhance their production processes. Computer-aided design (CAD) and computer numerical control (CNC) machining have revolutionized the precision and efficiency of molding processes. Furthermore, advancements in materials science have allowed manufacturers to experiment with a wider range of materials, including high-strength plastics, composite materials, and advanced alloys. This diversity in materials has opened doors to designing and producing parts with enhanced durability, heat resistance, and weight reduction. Quality Assurance: A Non-Negotiable Priority In the world of molded case parts manufacturing, quality is paramount. Manufacturers understand that the components they produce must adhere to stringent standards and specifications to ensure the safety and reliability of the end products they are incorporated into. Quality control measures are deeply ingrained in their production processes. To achieve these high-quality standards, manufacturers employ state-of-the-art inspection techniques, such as laser scanning, coordinate measuring machines (CMM), and X-ray inspection. These methods enable them to identify even the slightest deviations from the required specifications, ensuring that only flawless parts make their way to the assembly line. Environmental Responsibility In recent years, environmental sustainability has become a significant concern for industries worldwide. Molded case parts manufacturers are no exception. Many of these companies are actively seeking ways to reduce their environmental footprint. This includes adopting eco-friendly materials, recycling processes, and energy-efficient manufacturing technologies. Additionally, manufacturers are exploring innovative techniques, such as 3D printing, which can minimize material wastage and energy consumption while allowing for greater design flexibility. Meeting Customization Demands One of the remarkable aspects of molded case parts manufacturers is their ability to meet the unique requirements of various industries. They understand that a one-size-fits-all approach does not work in engineering. As a result, these manufacturers offer customizable solutions that cater to specific design and performance needs. Engineers and product designers from different sectors collaborate closely with molded case parts manufacturers to develop components tailored to their projects. This collaboration fosters innovation and ensures that the final products excel in performance and durability. Global Reach and Impact The impact of molded case parts manufacturers extends beyond their immediate surroundings. These companies often operate on a global scale, supplying components to manufacturers and industries worldwide. Their role in enabling the growth and development of industries cannot be overstated. In conclusion, molded case parts manufacturers are the unsung heroes of modern engineering. Their commitment to excellence, technological advancements, quality assurance, environmental responsibility, and customization capabilities make them indispensable partners in various industries. As technology continues to advance, we can only expect these manufacturers to push the boundaries of what is possible, contributing to the continued evolution of engineering and manufacturing.
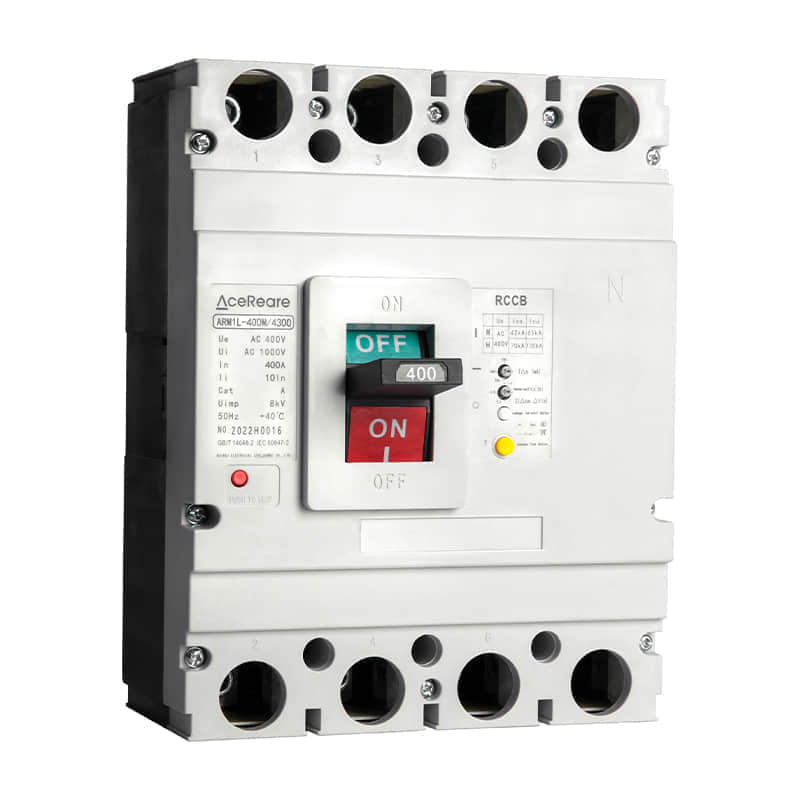