Progressive Die: The Advancements in Metal Stamping
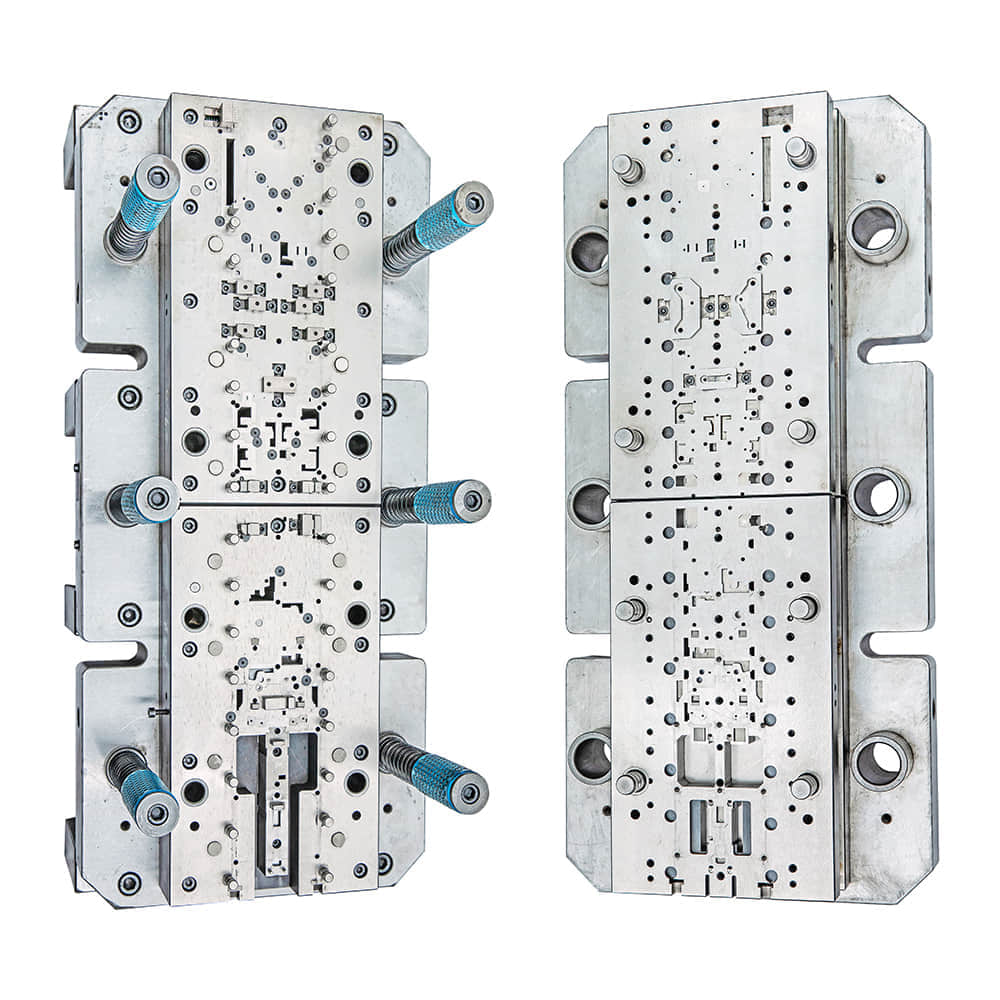
Metal stamping is a manufacturing process that has been vital to various industries for decades. It involves shaping and cutting metal sheets into desired forms and sizes. Among the many methods used in metal stamping, progressive die stamping stands out as an efficient and cost-effective approach. In this article, we will delve into the world of progressive die stamping, exploring its history, benefits, and the recent advancements that have transformed the industry.
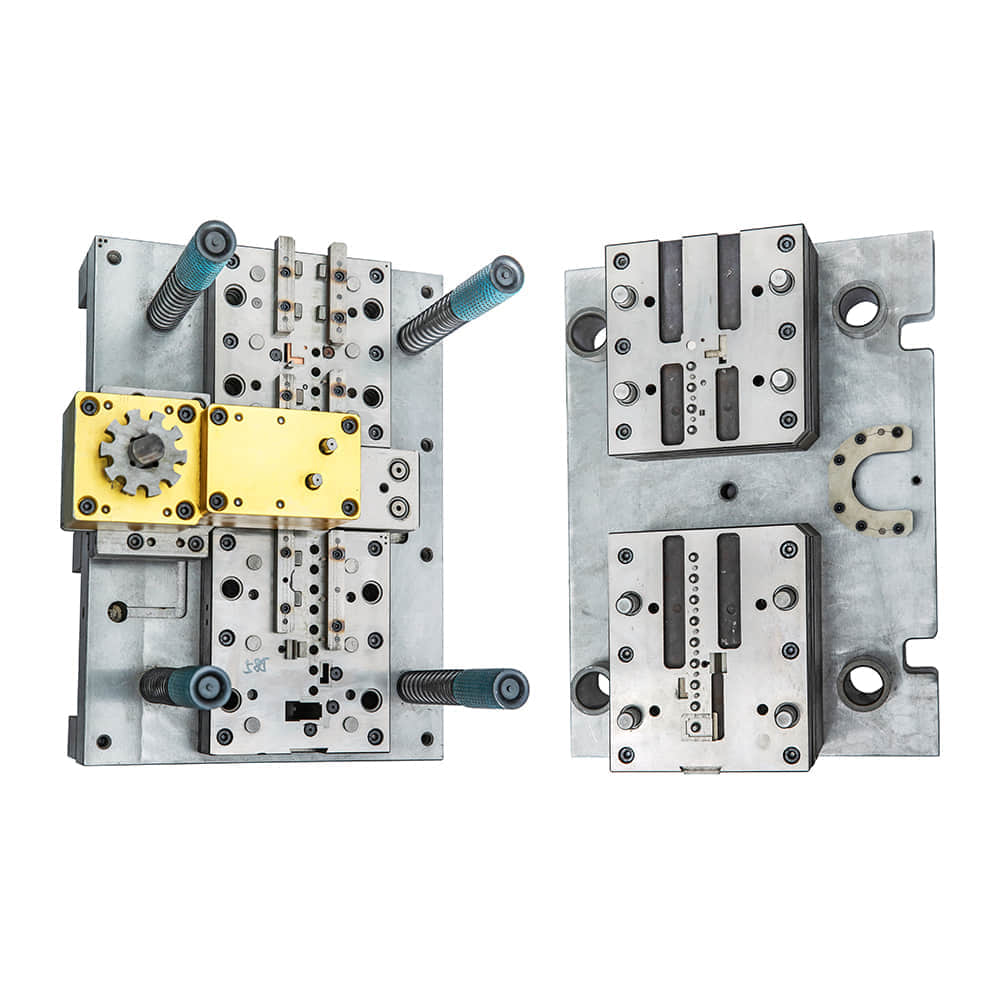
A Glimpse into Progressive Die Stamping’s Origins Progressive die stamping has roots dating back to the late 19th century. During this period, industrialization was rapidly taking hold, leading to increased demand for metal components in various sectors such as automotive, aerospace, and electronics. Traditional manufacturing methods were too slow and costly to meet this demand. Progressive die stamping emerged as a solution. The fundamental principle of progressive die stamping involves a continuous feed of a metal coil through a set of dies and stations. With each station, a specific operation is performed, such as cutting, bending, or forming. As the metal strip advances through the dies, it gradually transforms into a finished part. This progressive approach greatly improved production efficiency, making it possible to create high volumes of intricate parts with precision. Benefits of Progressive Die Stamping Cost Efficiency: One of the most significant advantages of progressive die stamping is its cost efficiency. The process minimizes material waste, as multiple operations are performed on a single strip of metal. This reduces material costs and leads to higher profitability for manufacturers. High Precision: Progressive die stamping offers exceptional precision and repeatability. The dies are designed to exact specifications, ensuring that each part produced meets quality standards consistently. Shorter Lead Times: The continuous nature of progressive die stamping means that parts are produced quickly. This shortens lead times and allows manufacturers to respond swiftly to market demands. Complex Geometries: Progressive dies can handle complex part geometries and intricate designs, making it suitable for a wide range of applications. Scalability: Progressive die stamping can be easily scaled to accommodate both small and large production runs, making it a versatile choice for manufacturers. Recent Advancements in Progressive Die Stamping In recent years, progressive die stamping has seen several technological advancements that have further enhanced its capabilities: Advanced Materials: The ability to work with advanced materials, such as high-strength alloys and exotic metals, has expanded the application range of progressive die stamping. This is crucial in industries like aerospace and defense. Simulation Software: The development of sophisticated simulation software allows manufacturers to optimize the design of progressive dies for better performance and reduced lead times. Automation and Robotics: Automation has become more prevalent in progressive die stamping. Robots are now used for tasks like material handling and quality inspection, improving efficiency and reducing labor costs. Data Analytics: The integration of data analytics and Industry 4.0 principles has enabled manufacturers to monitor and optimize their progressive die stamping processes in real-time, leading to higher yields and reduced downtime. Sustainability Initiatives: Progressive die stamping has also embraced sustainability. Manufacturers are exploring ways to reduce energy consumption, minimize waste, and implement eco-friendly coatings and materials. Conclusion Progressive die stamping has come a long way since its inception in the late 19th century. Its cost efficiency, precision, and adaptability make it a cornerstone of modern manufacturing. With ongoing technological advancements, progressive die stamping is poised to continue playing a crucial role in shaping the future of metal component production across various industries. As materials and processes evolve, so too will the capabilities of progressive die stamping, ensuring its relevance in the ever-changing landscape of manufacturing.
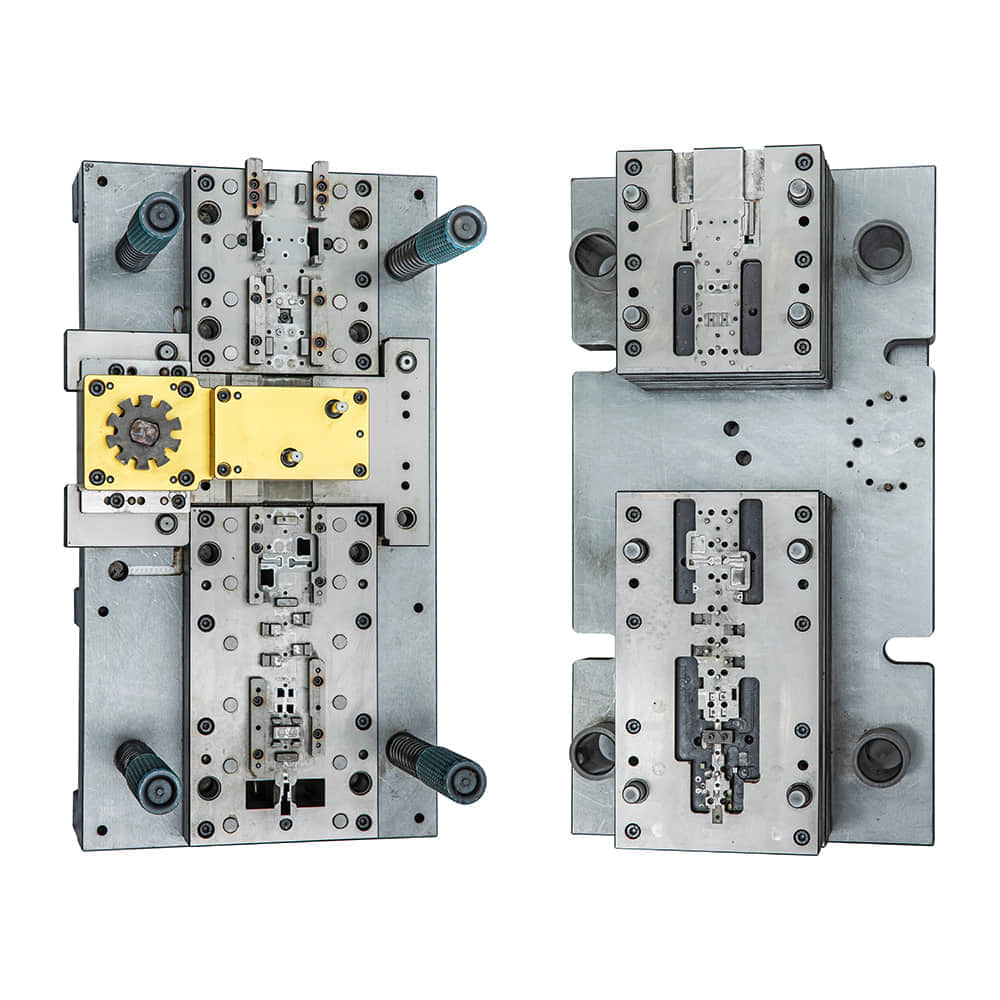