Thermoplastic injection molds have revolutionized modern manufacturing processes, offering precision, versatility, and efficiency that were once unimaginable. This innovative technology has become the backbone of industries ranging from automotive and aerospace to electronics and consumer goods. In this article, we will explore the intricacies of thermoplastic injection molds, their key components, advantages, and their pivotal role in shaping our world.
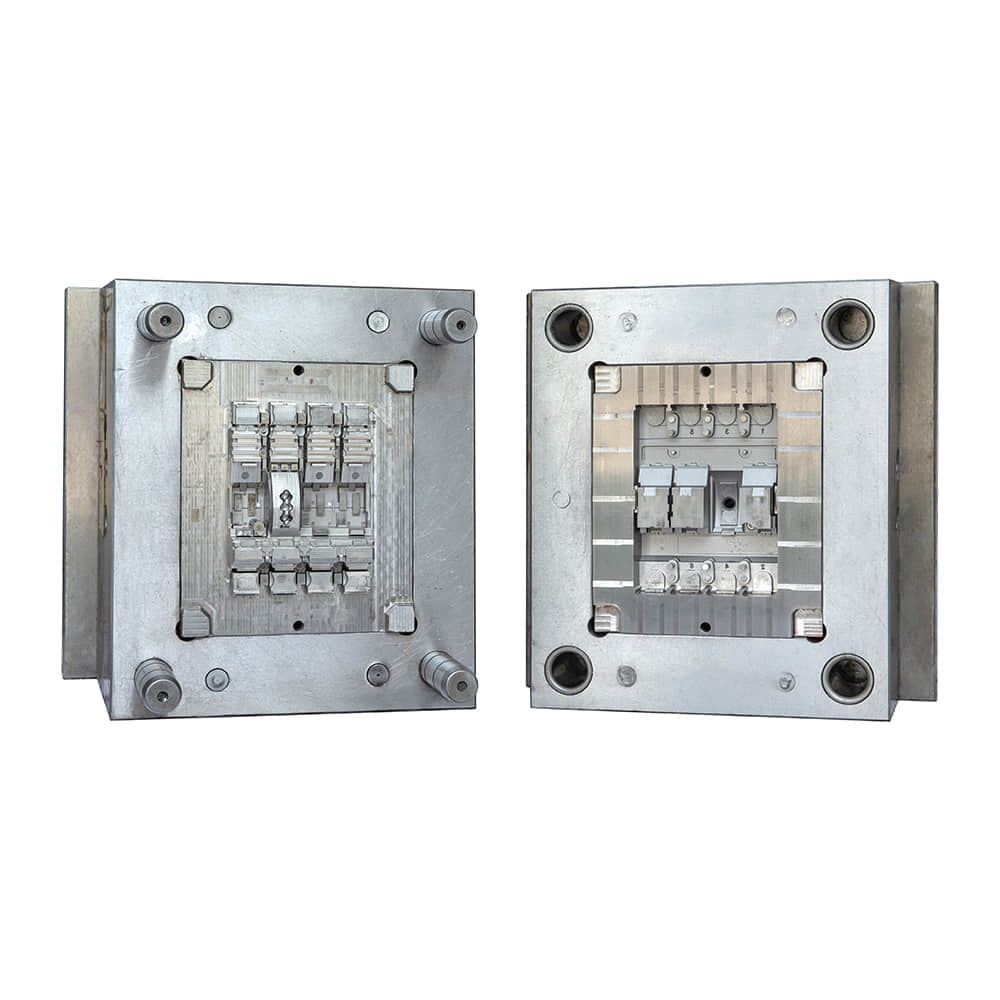
Understanding Thermoplastic Injection Molds
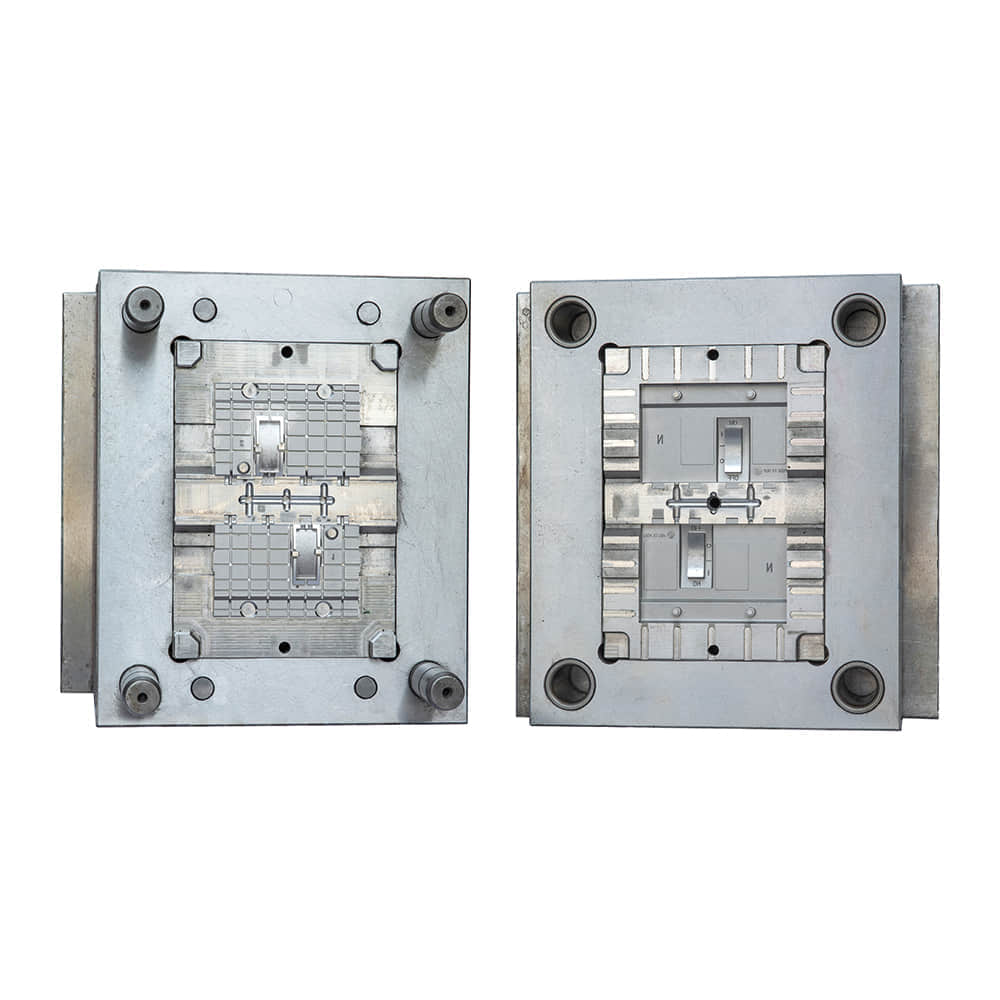
Thermoplastic injection molds are specialized tools designed to shape and create intricate plastic parts with high precision. They are primarily used for mass production and are central to industries where plastic components are integral. These molds are typically made from high-quality steel or aluminum, which ensures durability and longevity. Key Components of Thermoplastic Injection Molds Cavity: The cavity is the core component responsible for shaping the plastic part. It is usually designed to mirror the final product’s shape. Core: The core complements the cavity, creating the space for the plastic material to flow and take shape. Runner System: This network of channels and gates facilitates the flow of molten plastic from the injection unit into the mold cavity. Ejector System: Once the plastic has cooled and solidified, the ejector system helps remove the finished part from the mold. The Injection Molding Process The thermoplastic injection molding process begins with the heating of plastic resin pellets. Once the material reaches a molten state, it is injected into the mold under high pressure. The plastic fills the cavity and takes the shape of the mold. After cooling and solidification, the mold opens, and the part is ejected. This process can be repeated rapidly, making it ideal for mass production. Advantages of Thermoplastic Injection Molds Precision: Injection molds offer unparalleled precision and consistency, ensuring that each produced part meets exact specifications. Cost-Effective: While initial mold production can be expensive, the per-unit cost for mass production is significantly lower, making it cost-effective over time. Versatility: Injection molds can be designed for a wide range of complex shapes and sizes, making them suitable for various industries. Efficiency: The rapid cycle times of injection molding machines allow for high-volume production, reducing lead times. Material Variety: Thermoplastic injection molds can be used with a vast array of plastic materials, each with its unique properties. Applications Across Industries Automotive: Injection molds are used to manufacture components such as dashboard panels, bumpers, and interior trim. Electronics: The production of intricate and precise components like connectors and casings relies heavily on injection molds. Medical Devices: Many medical devices, such as syringes and IV components, are produced using thermoplastic injection molds due to their sterile and precise nature. Consumer Goods: Everyday items like bottles, toys, and packaging owe their existence to the efficiency of injection molding. Challenges and Innovations While thermoplastic injection molds offer numerous advantages, they are not without challenges. Tool wear, temperature control, and the need for constant maintenance are issues that manufacturers continually address through innovative materials and technologies. For instance, the use of advanced coatings and cooling techniques has significantly improved mold longevity. Conclusion Thermoplastic injection molds have transformed modern manufacturing by providing precision, efficiency, and versatility. They are the driving force behind the production of countless products that have become integral to our daily lives. As technology continues to advance, we can expect even greater innovations in the world of injection molding, further expanding its reach and capabilities. This remarkable technology exemplifies the power of engineering in shaping our world.
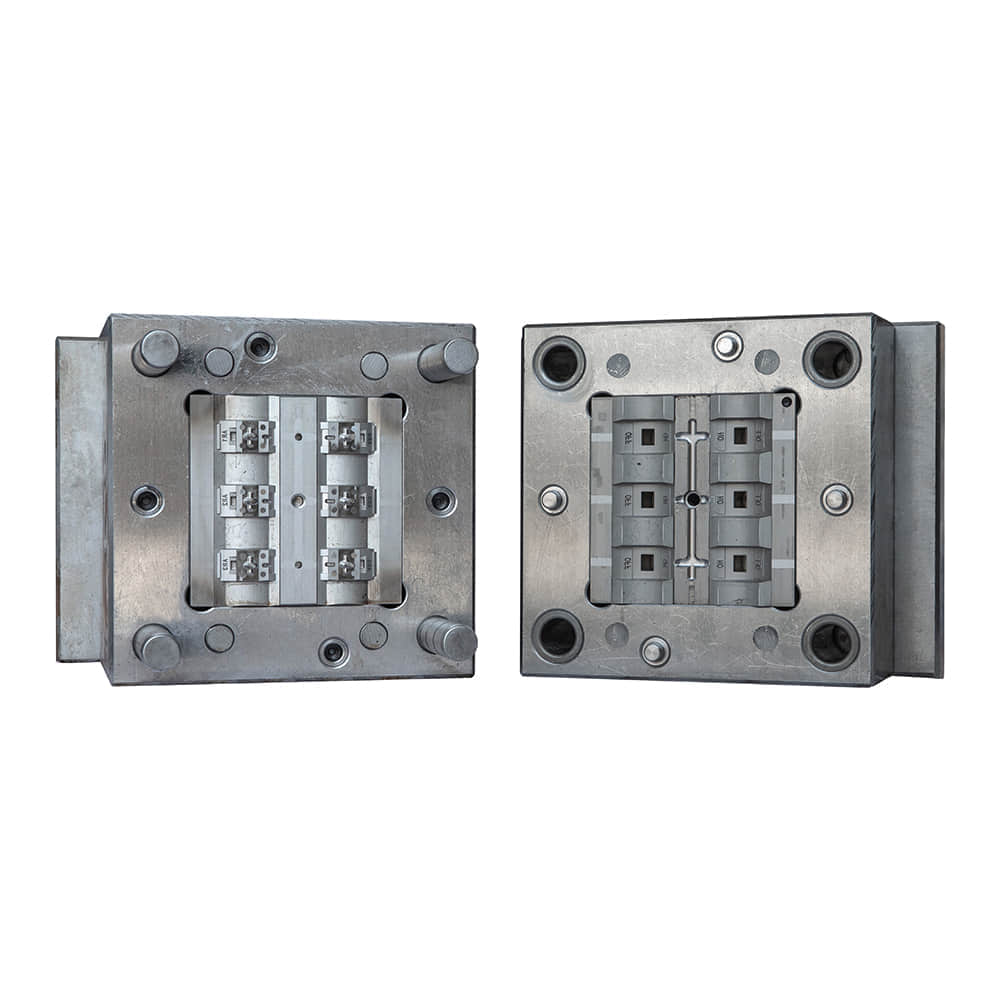