Molded case parts are a vital component in various industries, offering durability, versatility, and cost-efficiency. These parts are extensively used in manufacturing, construction, and engineering applications, contributing to the overall efficiency and safety of machinery and equipment. In this article, we will delve into the world of molded case parts, exploring their functions, the manufacturing process, and their wide range of applications.
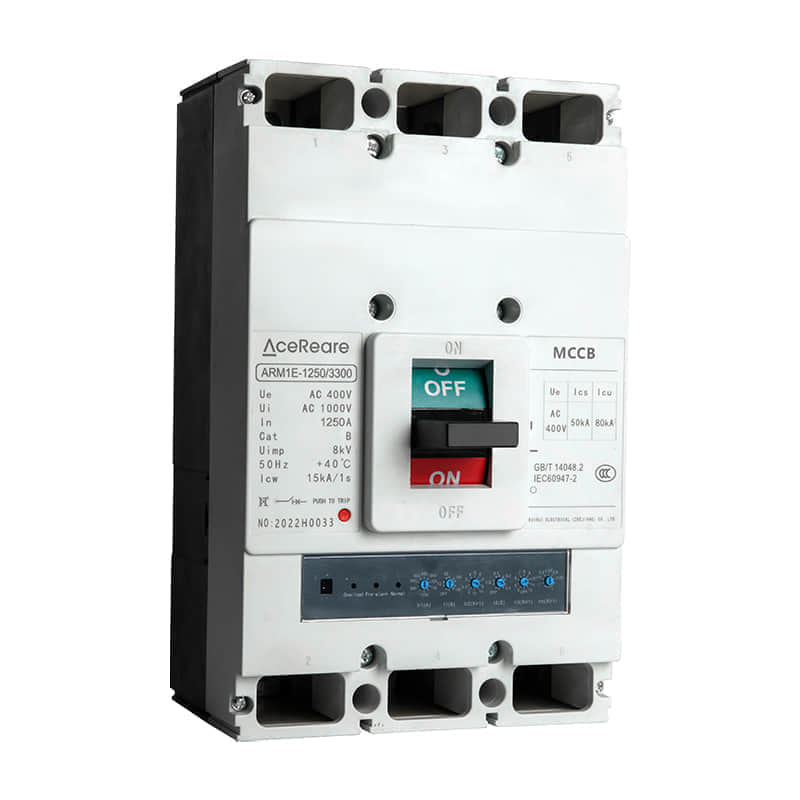
Functions of Molded Case Parts
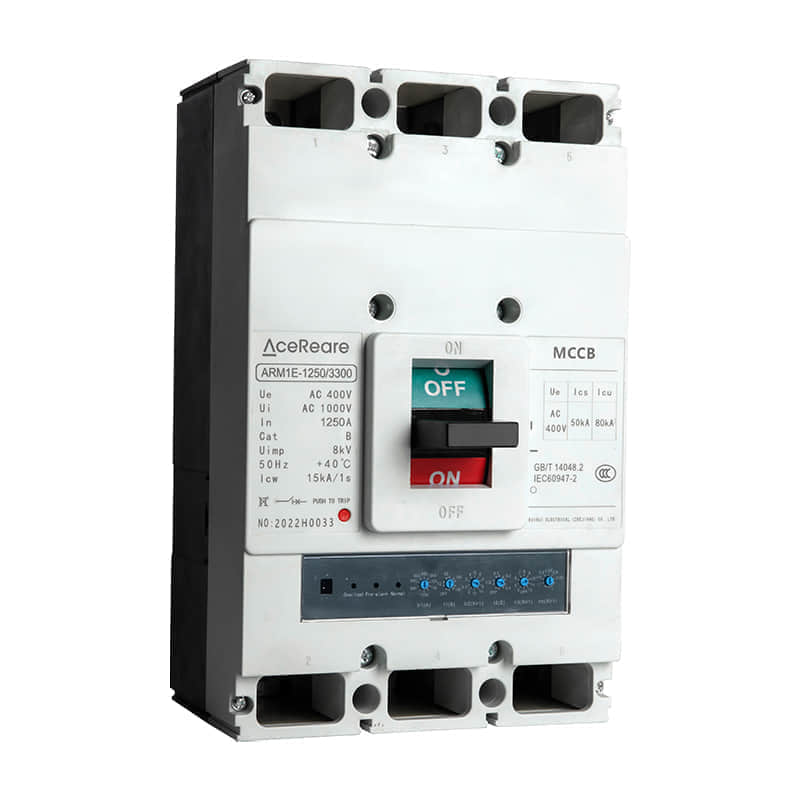
Molded case parts are primarily designed to protect and encapsulate sensitive components within machinery and electrical equipment. They serve multiple functions: Electrical Insulation:One of the key functions of molded case parts is to provide electrical insulation. These parts are often used in circuit breakers and other electrical devices to prevent electrical shocks and short circuits. Mechanical Protection:Molded case parts offer mechanical protection to critical components, safeguarding them from physical damage due to external factors like impact, vibration, or environmental conditions. Heat Dissipation:Many molded case parts are designed with heat dissipation features, helping to manage and dissipate heat generated by the equipment. This ensures optimal operating conditions and prevents overheating. Contaminant Resistance:Molded case parts can seal sensitive components from contaminants such as dust, moisture, and chemicals, ensuring the equipment’s longevity and reliability. Manufacturing Process The manufacturing process of molded case parts involves several steps: Material Selection:The choice of material is crucial, as it determines the part’s electrical and mechanical properties. Common materials include thermoplastics, thermosetting plastics, and composite materials. Molding:The selected material is heated to a molten state and injected into a mold cavity. The mold is typically custom-designed to match the specific dimensions and features of the desired part. Cooling and Solidification:After injection, the material is cooled and allowed to solidify within the mold. This process ensures that the part takes on its final shape and structure. Finishing:Once the part is removed from the mold, it may undergo additional finishing processes, such as trimming, drilling, or surface treatments, to meet the exact specifications required. Applications Molded case parts find applications across various industries: Electrical Industry:They are extensively used in electrical components such as circuit breakers, switches, and electrical connectors, where electrical insulation and protection are paramount. Automotive Industry:Molded case parts are utilized in vehicles for protecting and insulating sensitive electronics, ensuring the safe and reliable operation of onboard systems. Construction Sector:These parts are employed in construction equipment to safeguard control systems, wiring, and sensors from harsh environmental conditions, extending the equipment’s lifespan. Industrial Machinery:Molded case parts are integral in industrial machinery to protect control panels, motor drives, and other critical components from dust, moisture, and mechanical stress. Medical Devices:In the medical field, molded case parts play a vital role in ensuring the safety and reliability of medical equipment by protecting sensitive electronic components. Aerospace Industry:Aerospace applications demand lightweight, durable components with superior electrical insulation properties, making molded case parts invaluable. In conclusion, molded case parts are indispensable in modern industries, offering multifunctional benefits that encompass electrical insulation, mechanical protection, heat dissipation, and contaminant resistance. Their precise manufacturing process ensures consistency and reliability, making them an ideal choice for a wide range of applications. As industries continue to evolve and demand more advanced equipment, the importance of molded case parts in enhancing safety and efficiency is likely to grow even further.
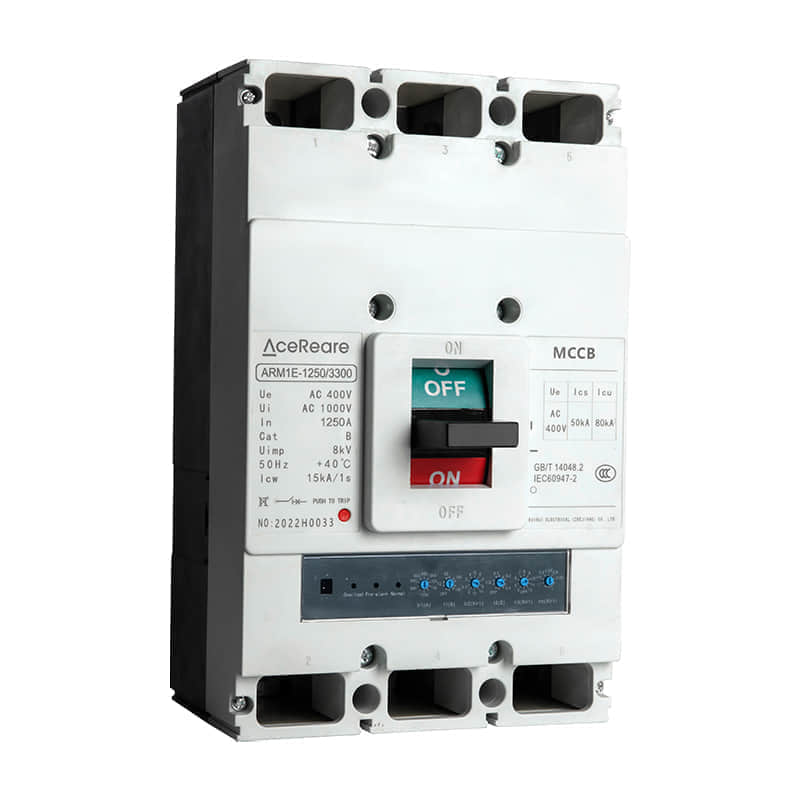