Progressive Die: Streamlining Manufacturing Processes
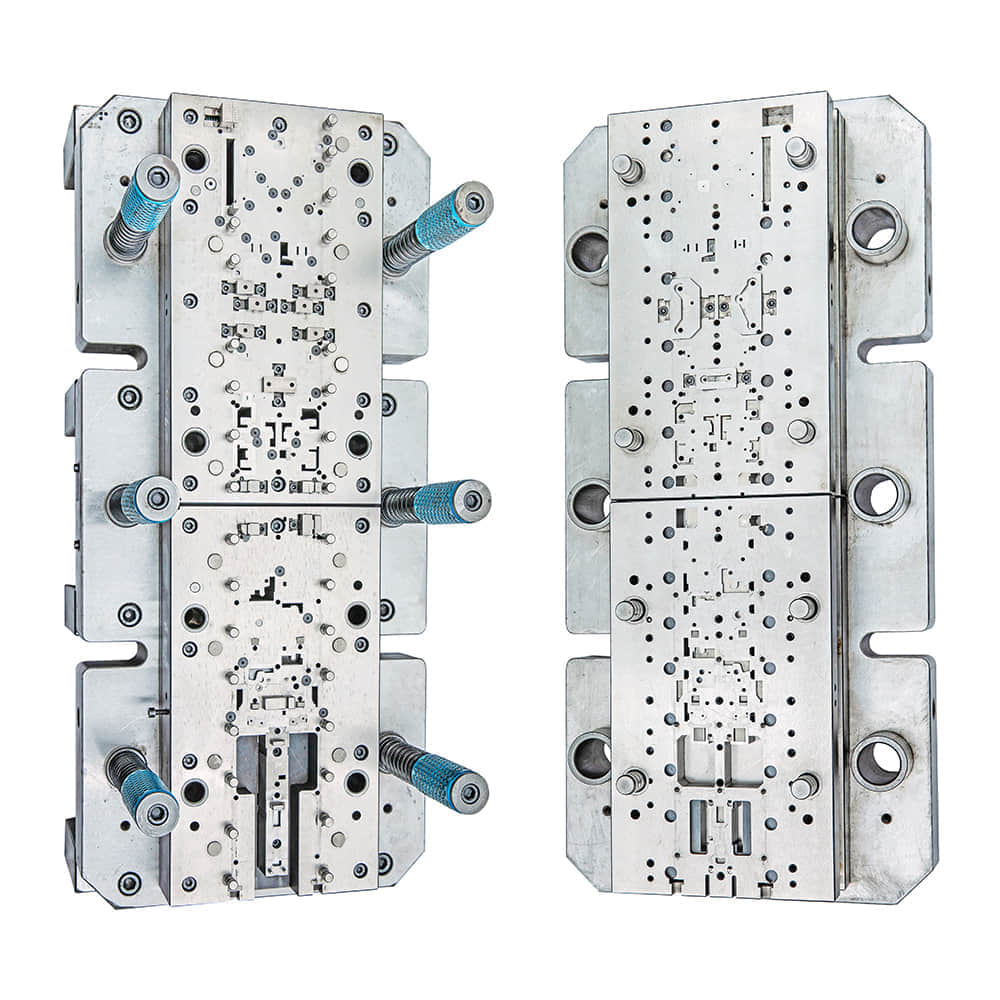
In the ever-evolving landscape of manufacturing, efficiency is the name of the game. One of the key players in achieving this efficiency is the progressive die. Progressive dies are innovative tools that have transformed metalworking industries, enabling manufacturers to produce intricate parts with precision and speed. In this article, we will delve into the world of progressive dies, exploring their functionality, advantages, and applications.
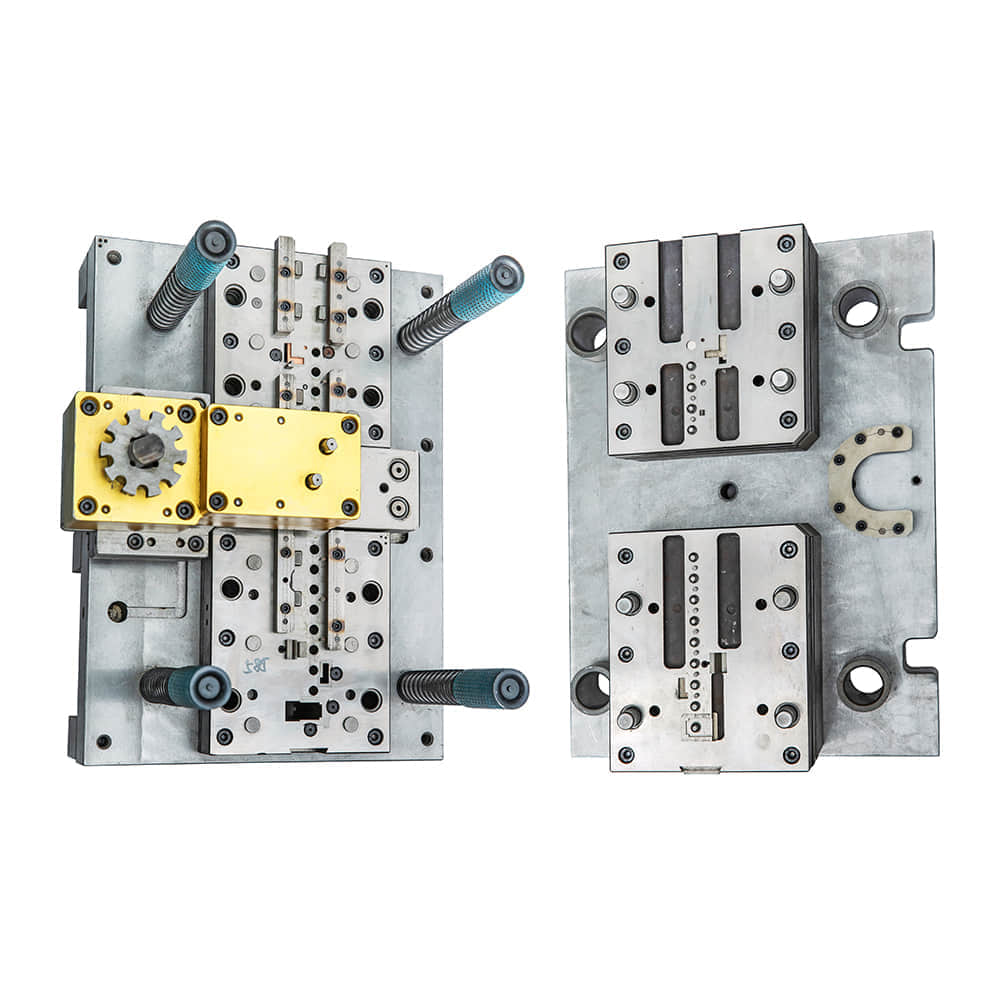
Understanding Progressive Dies At its core, a progressive die is a specialized tool used in metal stamping and forming processes. Its primary function is to transform raw metal sheets into finished components, typically used in industries such as automotive, electronics, and aerospace. Unlike traditional stamping dies, progressive dies are incredibly versatile and efficient. A progressive die operates on the principle of continuous feeding. It consists of a series of stations, each performing a specific operation on the metal sheet as it advances through the die. These stations include cutting, bending, punching, and coining. The metal sheet moves from one station to the next, with each station adding another layer of detail or precision to the part. This sequential process eliminates the need for multiple setups and handling, reducing the risk of errors and minimizing material wastage. Advantages of Progressive Dies High Efficiency: Progressive dies are designed for high-speed production. They can produce parts at rates of hundreds or even thousands per minute, making them ideal for mass production. Precision: The sequential nature of progressive die operations ensures consistent accuracy. This precision is crucial in industries where tight tolerances are required. Reduced Labor Costs: As a highly automated process, progressive die stamping reduces the need for manual labor, saving both time and money. Material Savings: Progressive dies minimize material wastage by optimizing the layout of parts on the metal sheet. This reduces scrap and contributes to cost savings. Complex Part Production: Progressive dies excel in producing complex parts with multiple features. They can perform multiple operations in a single pass, reducing production time. Applications of Progressive Dies Progressive dies find applications in various industries, including: Automotive: Progressive dies are extensively used to manufacture automotive components like brackets, clips, and connectors. Their speed and precision are essential in meeting the demands of the automotive sector. Electronics: In the electronics industry, progressive dies create intricate parts such as connectors, contacts, and heat sinks. The high degree of precision ensures these parts meet the stringent requirements of modern electronics. Aerospace: Aerospace manufacturers rely on progressive dies for the production of components used in aircraft and spacecraft. These dies ensure the highest level of quality and consistency in critical aerospace parts. Consumer Goods: Items like metal enclosures for household appliances and tools are often produced using progressive dies. The efficiency of these dies allows for cost-effective production of consumer goods. Medical Devices: Progressive dies play a crucial role in the production of medical device components. Their precision is vital in ensuring the safety and reliability of medical equipment. Conclusion Progressive dies have revolutionized the manufacturing industry by combining speed, precision, and efficiency. They are the go-to choice for industries that require high volumes of complex parts with minimal material wastage. As technology continues to advance, progressive dies are likely to become even more sophisticated, further enhancing their capabilities. In an era where time and resources are precious commodities, progressive dies have established themselves as indispensable tools for manufacturers worldwide, driving progress in the world of manufacturing.
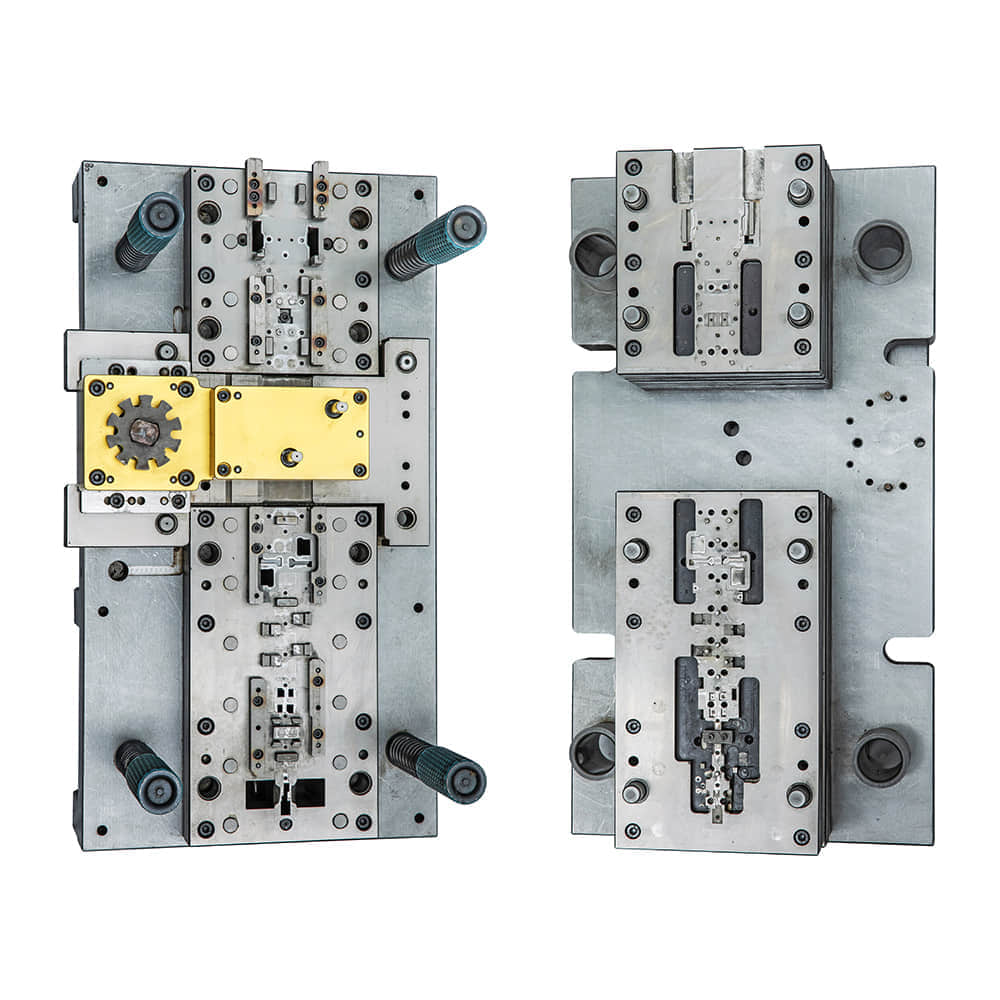