In the realm of manufacturing, precision and innovation are paramount. One crucial aspect of this world is thermosetting molds, integral tools that shape various products we encounter daily. Thermosetting mold manufacturers play a pivotal role in creating these molds, contributing significantly to industries like automotive, electronics, aerospace, and more.
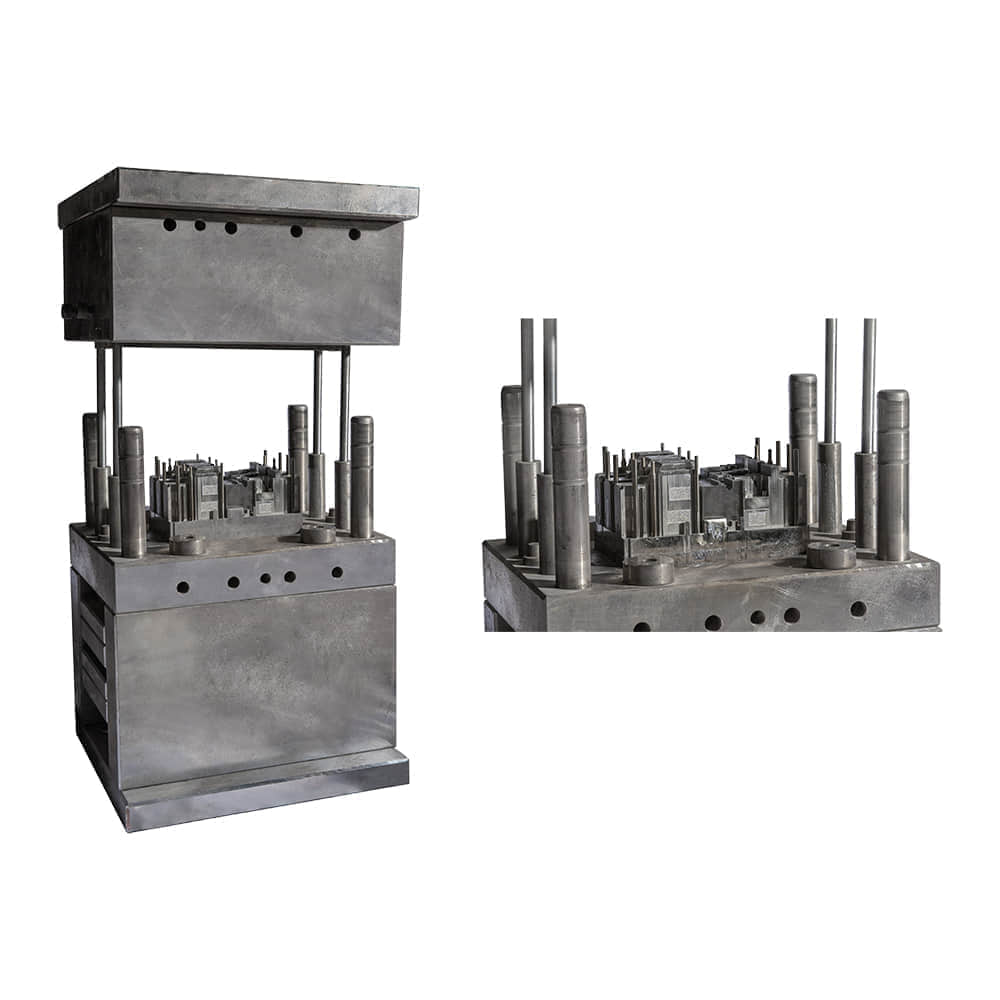
The Essence of Thermosetting Molds
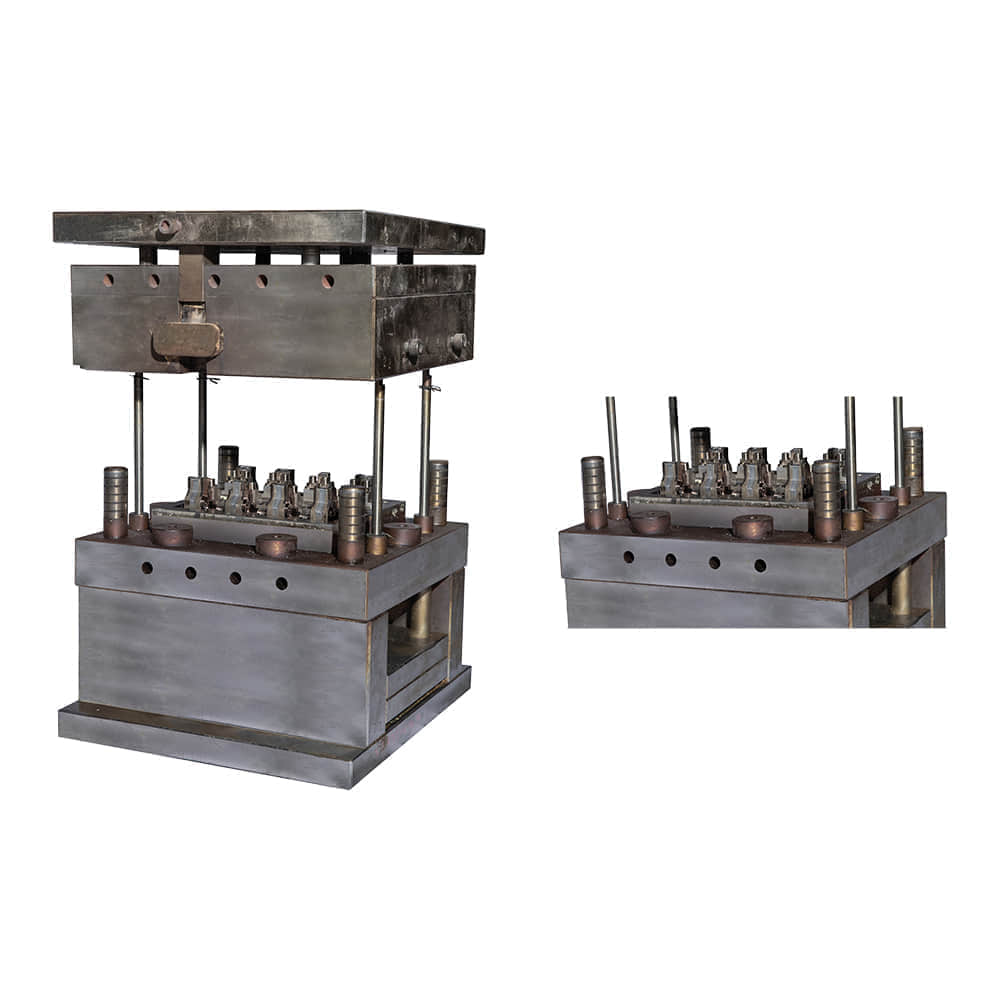
Thermosetting molds are a type of industrial tooling that facilitates the production of items with complex shapes and structures. Unlike thermoplastic materials that can be melted and reshaped, thermosetting materials undergo a chemical transformation when heated, irreversibly hardening into a specific form. The molds used for shaping thermosetting materials are designed with precision and care, demanding the expertise of skilled manufacturers. Crafting Perfection: The Role of Thermosetting Mold Manufacturers Thermosetting mold manufacturers are artisans of industry, blending technical knowledge with creative ingenuity. Their journey begins with an intricate design process, where they translate a product’s specifications into a mold design. This design phase requires a deep understanding of the properties of thermosetting materials, as well as the intended functionality of the final product. The next phase involves material selection. Manufacturers must choose the appropriate materials that can withstand the high temperatures and pressures involved in the molding process. This choice greatly influences the mold’s durability, the quality of the molded products, and the overall efficiency of the manufacturing process. Precision Engineering and Innovation Creating thermosetting molds demands precision engineering. Manufacturers utilize advanced software and machinery to bring their designs to life. Computer-aided design (CAD) software enables them to visualize intricate details and simulate the molding process before physical production begins. This step minimizes errors, reduces wastage of materials, and accelerates the manufacturing timeline. Innovation is a driving force in the industry. Manufacturers constantly push boundaries to enhance mold efficiency, product accuracy, and overall production speed. New techniques, such as additive manufacturing (3D printing), are being integrated into the mold-making process, allowing for greater complexity and customization while maintaining structural integrity. Quality Control: Ensuring Excellence Thermosetting mold manufacturers understand that quality control is non-negotiable. Molds undergo rigorous testing to ensure they can withstand the extreme conditions of the molding process. Factors such as temperature resistance, pressure endurance, and dimensional accuracy are meticulously evaluated. Moreover, manufacturers collaborate closely with their clients to fine-tune molds according to specific requirements. This partnership ensures that the final product not only meets the desired specifications but also aligns with the client’s production processes. Towards a Sustainable Future As industries worldwide shift focus towards sustainability, thermosetting mold manufacturers are also embracing eco-friendly practices. They explore the use of recyclable and biodegradable materials for mold production, contributing to reduced environmental impact. Additionally, innovative cooling techniques and energy-efficient processes are being developed to minimize resource consumption during manufacturing. Conclusion Thermosetting mold manufacturers are the unsung heroes behind the scenes, shaping our modern world in ways we often take for granted. Their dedication to precision, innovation, and quality control drives the industries that rely on thermosetting materials. As technology advances and sustainability becomes paramount, these manufacturers will continue to evolve, creating molds that not only shape products but also a more sustainable future.
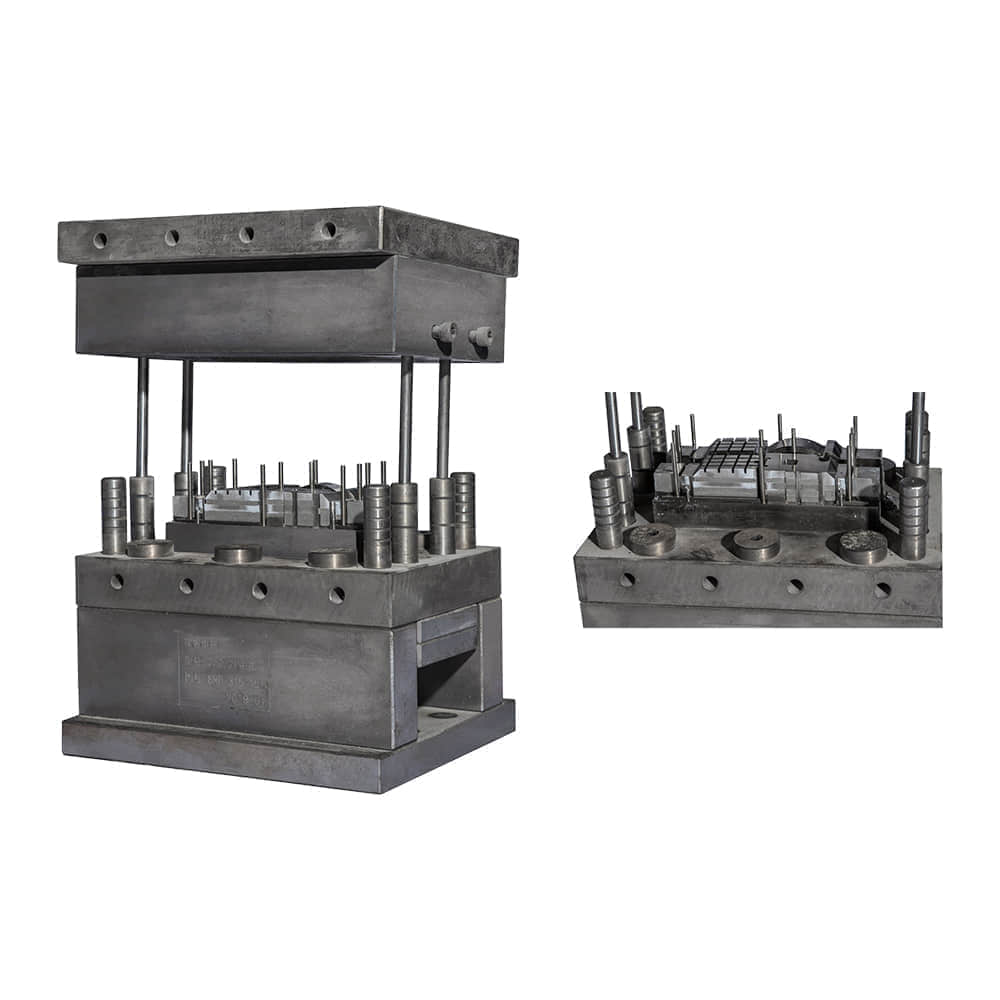