In the realm of modern manufacturing, injection molding stands as a cornerstone technology, driving the creation of intricate and versatile plastic components that shape our world. At the heart of this technology lies the crucial figure of the injection mold manufacturer. With precision craftsmanship and innovative techniques, these manufacturers play a pivotal role in transforming raw materials into products that serve industries ranging from automotive to electronics.
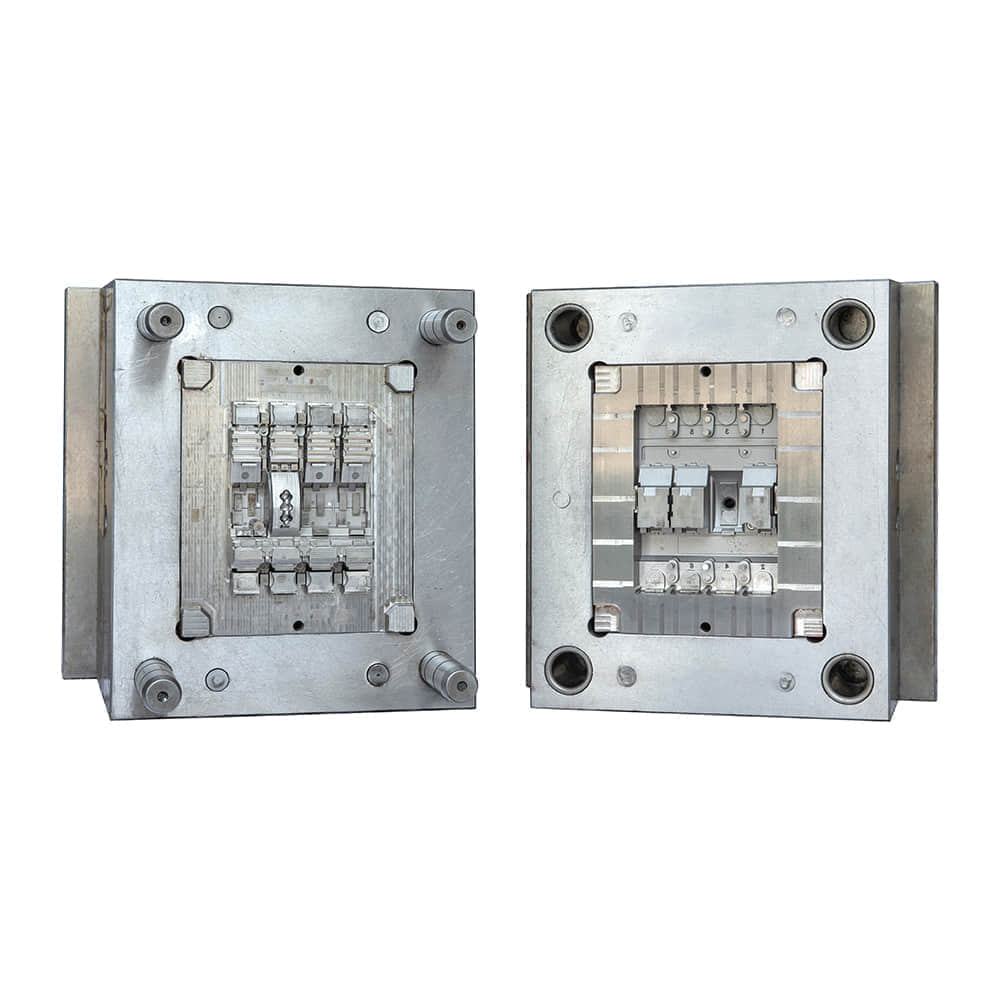
An injection mold manufacturer is akin to an artist, sculpting with metal and engineering. Their process begins long before the first injection cycle. Meticulous planning and design are the initial keystones, where every detail of the mold is envisioned. Computer-aided design (CAD) software becomes their canvas, allowing them to draft the mold’s geometry down to the micron. Each contour matters, as it dictates the final form of the plastic product it will shape.
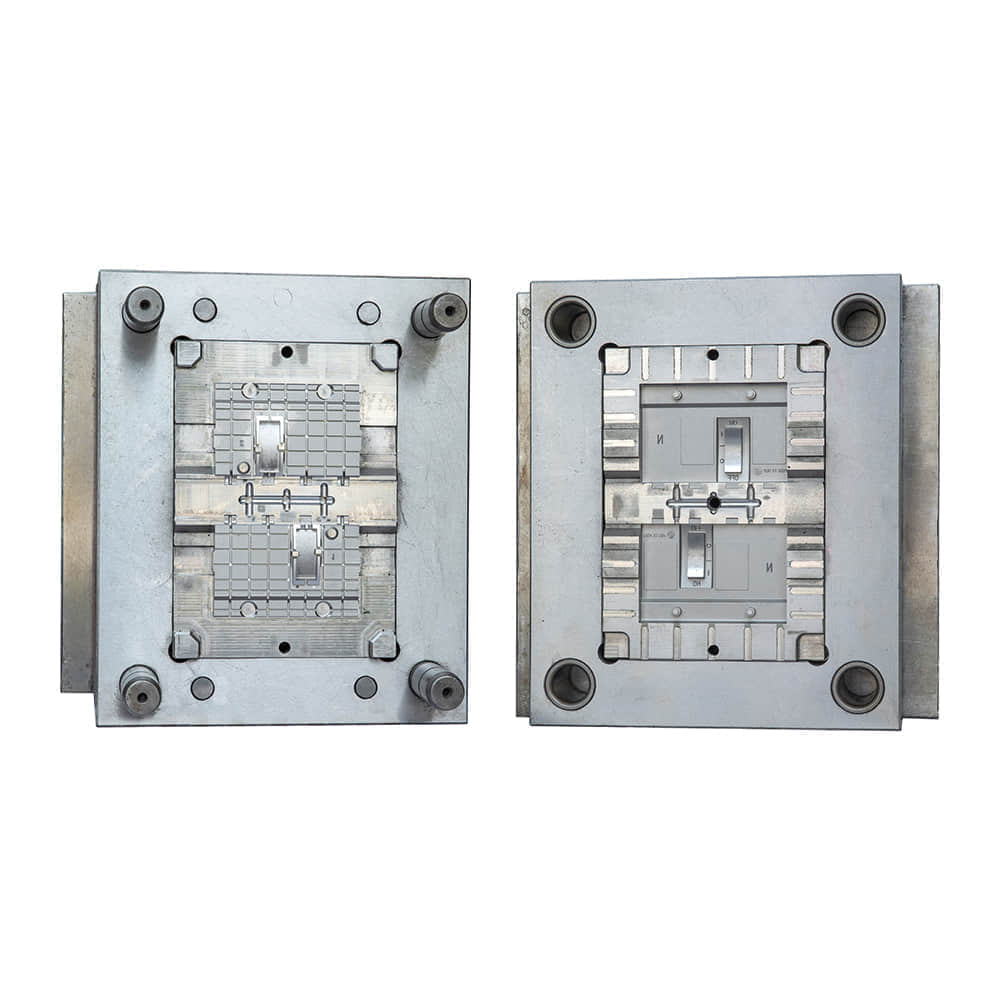
The next phase is a testament to the manufacturer’s skill: mold creation. High-quality metals, often tool steels, are meticulously cut, shaped, and assembled into the mold’s core and cavity. This demands a fusion of experience and technological finesse. Computer numerical control (CNC) machines carve out the most intricate sections, while craftsmanship refines the finer details. The manufacturer’s hands and the CNC machine work in harmony to achieve perfection. In injection molding, precision is paramount. The manufacturer must calculate not only the volumetric shrinkage of the plastic material as it cools and solidifies within the mold, but also the potential warping or defects that could mar the final product. These considerations require not only scientific knowledge but a deep understanding that comes from years of hands-on experience. Beyond the artistic aspect, injection mold manufacturers are also pioneers of innovation. They continuously seek novel solutions to enhance efficiency, reduce waste, and optimize the molding process. This includes the integration of technologies like real-time monitoring and data analytics to ensure each injection cycle yields consistent, high-quality products. Moreover, eco-friendly materials and sustainable practices have become focal points, reflecting the industry’s commitment to environmental responsibility. Collaboration forms another cornerstone of an injection mold manufacturer’s journey. They collaborate closely with clients, forging a relationship built on effective communication and mutual understanding. This connection extends beyond the initial project, as manufacturers provide maintenance, adjustments, and new iterations of molds as product designs evolve. In an era driven by automation and digitalization, injection mold manufacturing preserves the essence of craftsmanship. It combines the artistry of design, the dexterity of engineering, and the analytical prowess of science. As industries evolve and consumer demands shift, injection mold manufacturers stand as adaptable architects of plastic transformation. In conclusion, the world owes much of its plastic innovation to injection mold manufacturers. Their meticulous craftsmanship, rooted in design precision and propelled by innovation, forges the molds that shape the products we encounter daily. Beyond the technical complexities, these manufacturers are artists, engineers, and collaborators, all woven into the fabric of modern manufacturing. The next time you hold a perfectly molded plastic product, take a moment to appreciate the expertise woven into its creation by these unsung heroes of industry.
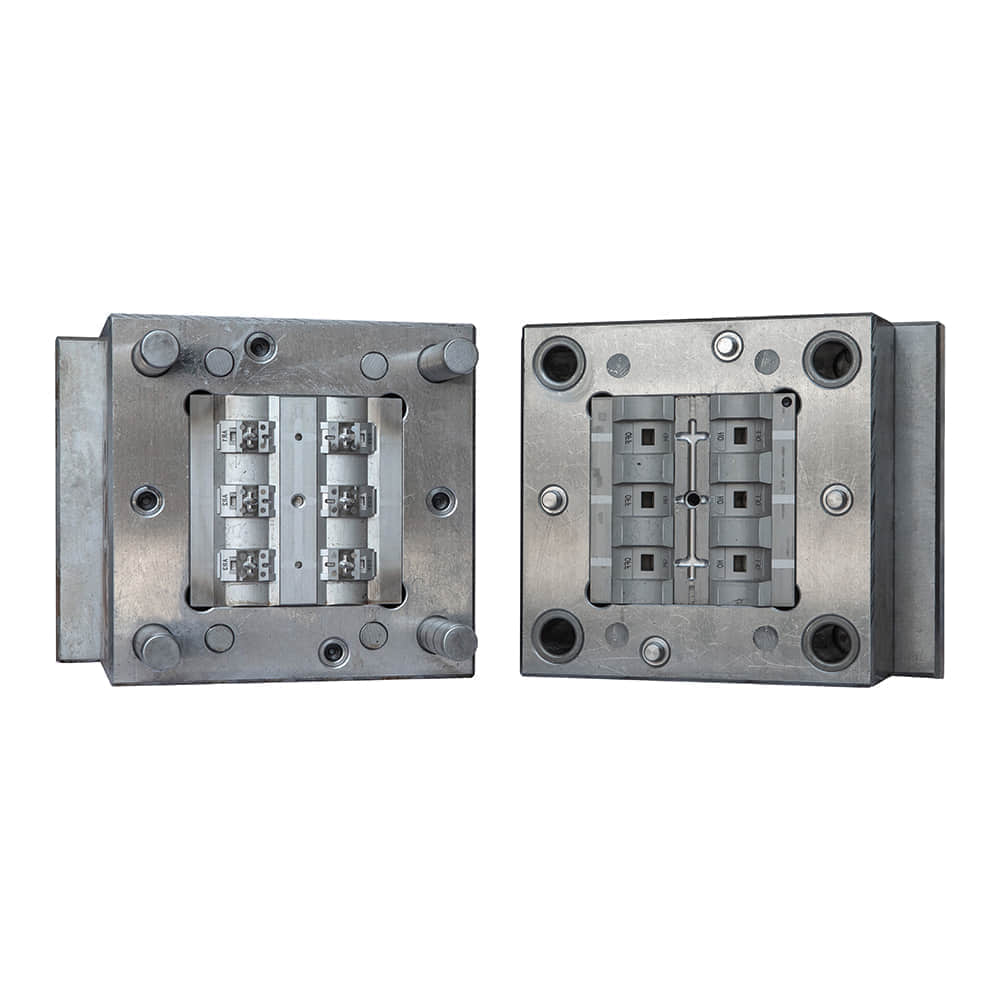