Injection molding is a manufacturing process that has revolutionized the production of plastic and other materials. It has become an integral part of various industries, from automotive to electronics, owing to its precision, efficiency, and versatility. In this article, we will delve into the world of injection molded parts, exploring the process, its advantages, and its wide-ranging applications.
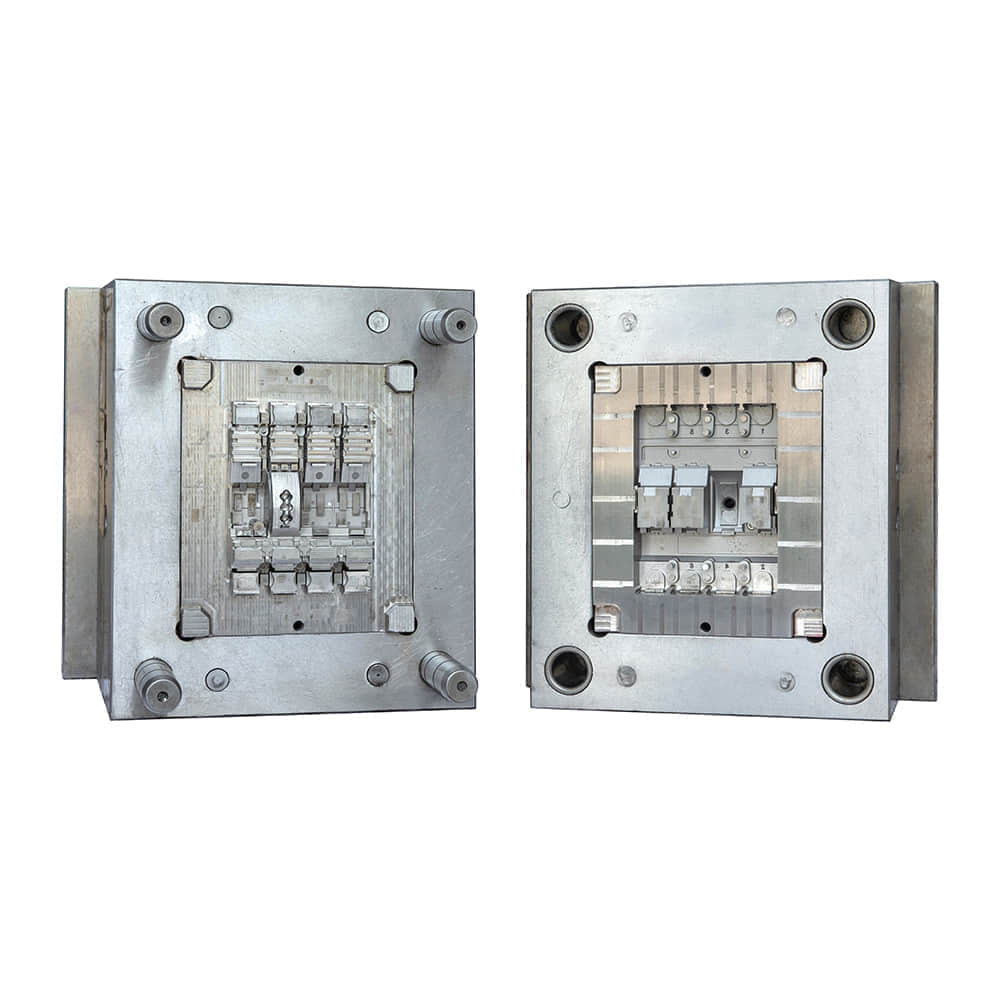
The Injection Molding Process
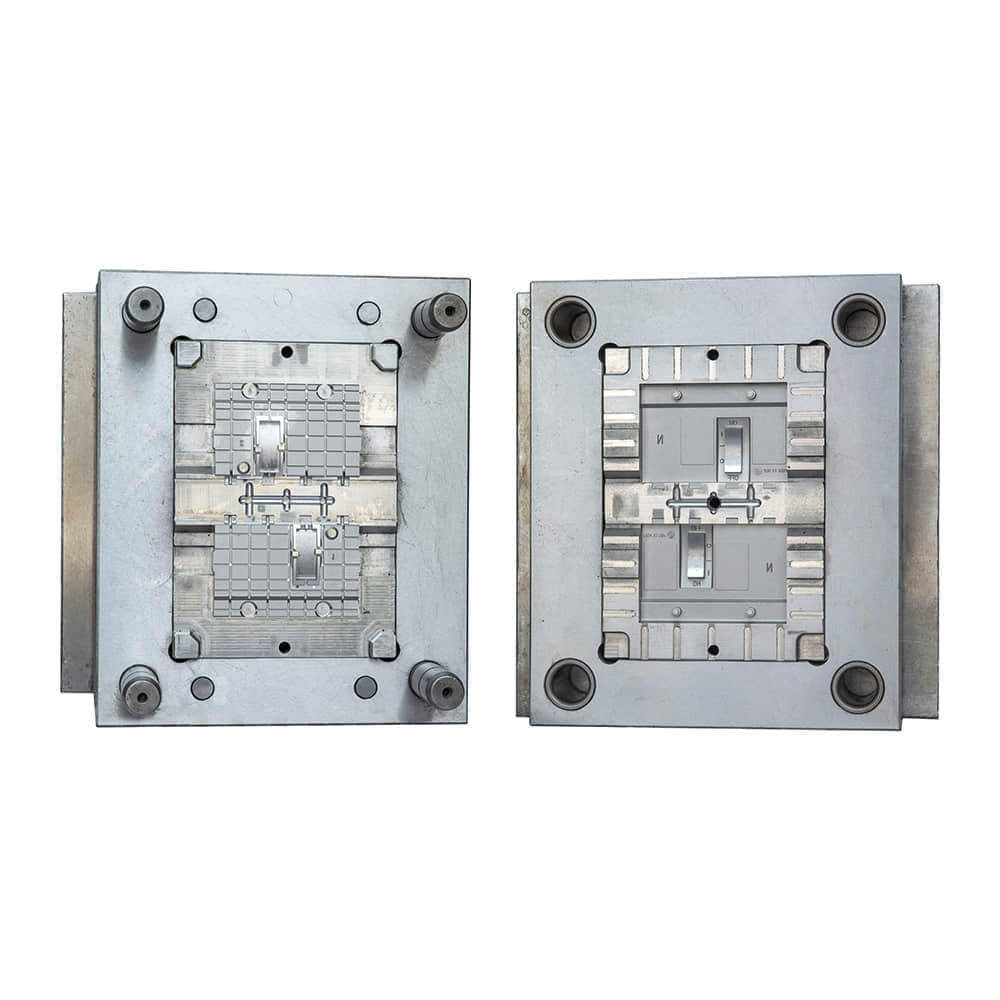
Injection molding is a highly efficient manufacturing process for producing parts and products. It involves injecting molten material into a mold cavity, allowing it to cool and solidify, and then ejecting the finished part. Here’s a breakdown of the key steps: Material Selection: The process begins with the selection of a suitable material, typically thermoplastics like polyethylene, polypropylene, or polycarbonate. The choice of material depends on the desired characteristics of the final product. Melting: The selected material is fed into a heated barrel, where it is melted. Additives, such as colorants or stabilizers, can be mixed in at this stage to achieve specific properties. Injection: Once molten, the material is injected into a mold cavity under high pressure. The mold is typically made of two halves that come together to form the desired shape. Cooling: The material rapidly cools and solidifies within the mold. Cooling is a critical step that affects the part’s quality and dimensional accuracy. Ejection: After cooling, the mold opens, and the finished part is ejected. It’s then ready for any necessary post-processing steps, such as trimming or assembly. Advantages of Injection Molding Injection molding offers several advantages that make it a preferred choice for many manufacturers: Precision: Injection molding allows for the production of highly precise and complex parts with tight tolerances. This precision ensures that parts fit together perfectly, reducing the need for additional machining. Efficiency: The process is highly efficient, with short cycle times and the ability to produce large quantities of identical parts quickly. This efficiency translates to cost savings. Versatility: Injection molding is not limited to plastics; it can be used with a variety of materials, including metals and ceramics. This versatility makes it suitable for a wide range of applications. Reduced Waste: The process generates minimal waste as any excess material can be reground and reused. This is environmentally friendly and cost-effective. Consistency: With automated machinery and precise controls, injection molding ensures consistent part quality from the first piece to the last. Applications of Injection Molded Parts Injection molded parts find application across numerous industries: Automotive: From interior components to under-the-hood parts, injection molding is used extensively in the automotive industry to produce durable and lightweight components. Electronics: The production of small, intricate components like connectors, switches, and housings is made possible by injection molding. Medical: Many medical devices and equipment, such as syringes, are made using injection molding due to its ability to maintain a sterile environment during production. Consumer Goods: Everyday items like bottle caps, toys, and packaging are often manufactured through injection molding. Aerospace: Injection molding contributes to the production of lightweight, high-performance parts for aircraft and spacecraft. Appliances: Components for household appliances, such as washing machine parts and refrigerator components, are often injection molded. Conclusion Injection molded parts have become ubiquitous in modern manufacturing due to their precision, efficiency, and versatility. As technology continues to advance, the process becomes even more accessible and cost-effective, expanding its reach into new industries and applications. Understanding the injection molding process and its advantages is essential for manufacturers looking to stay competitive in today’s fast-paced market. Whether you’re designing the next generation of automotive components or creating innovative medical devices, injection molding offers the precision and efficiency needed to turn ideas into reality.
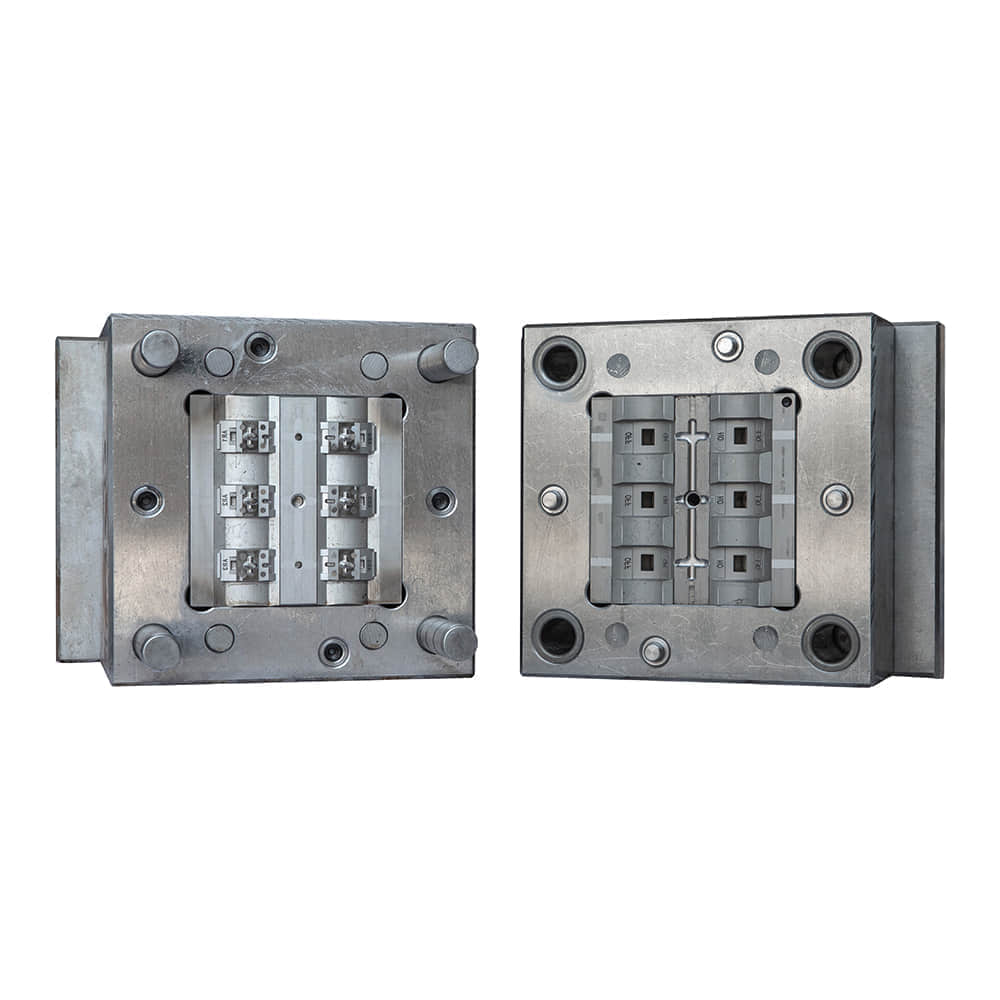