In the world of manufacturing, precision and innovation are paramount. One industry that exemplifies these qualities is metal stamping, and at its core lies the Metal Stamping Die OEM Manufacturer. In this article, we will delve into the world of metal stamping die OEM manufacturing, exploring its significance, processes, and the key players who make it all possible.
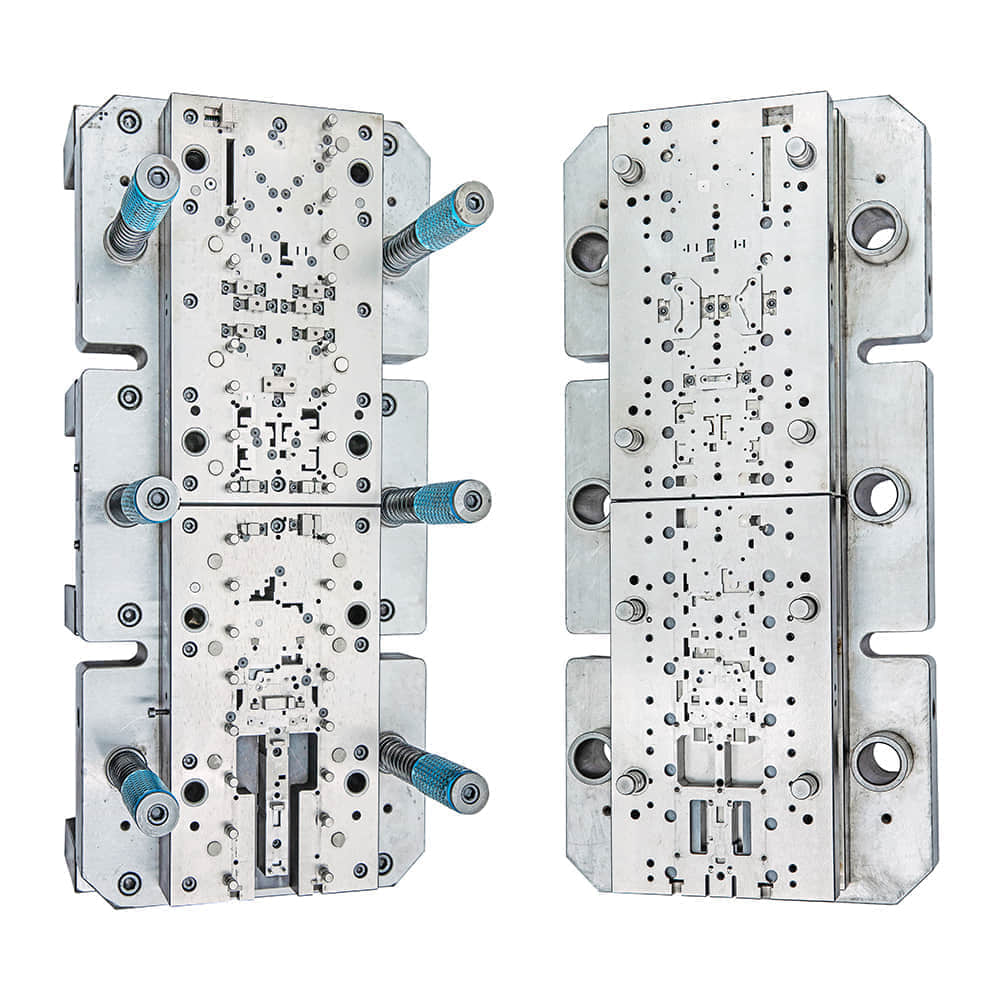
The Significance of Metal Stamping Die OEM Manufacturers
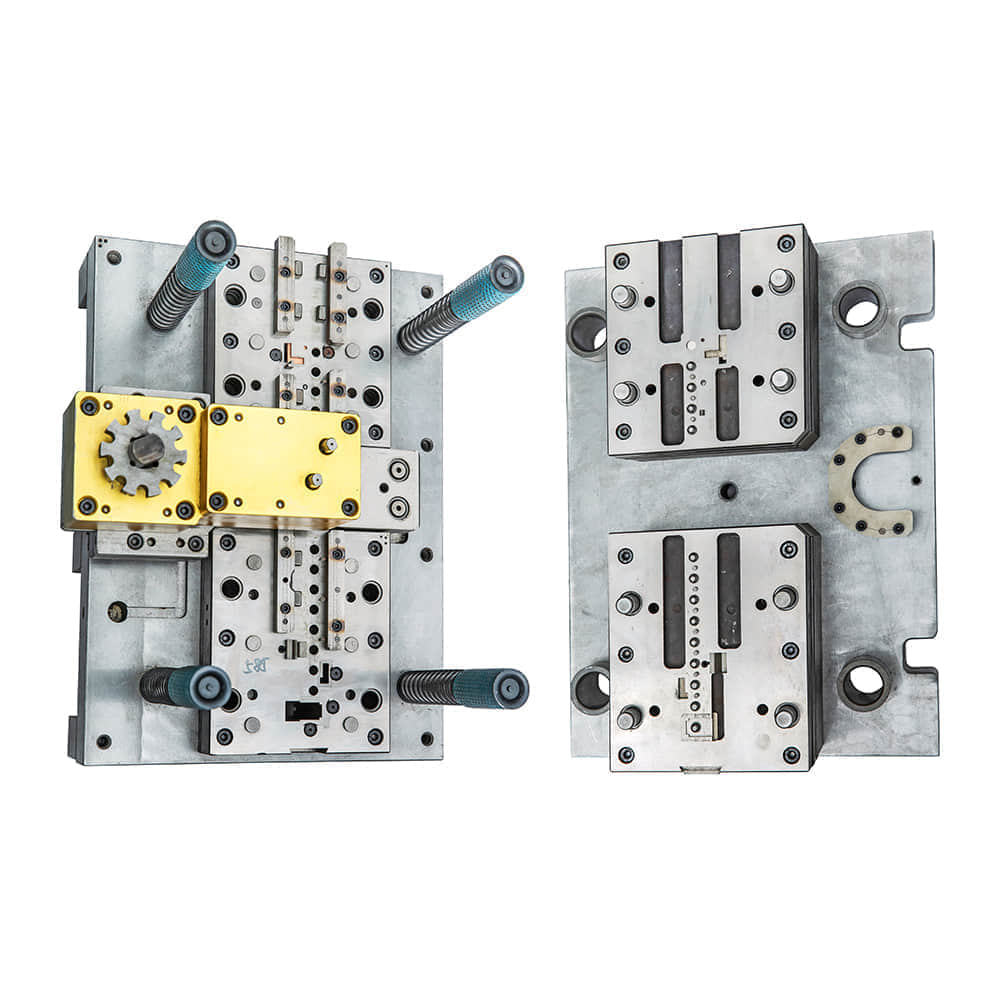
Metal stamping is a versatile process that involves shaping and cutting metal sheets into various forms and sizes. From automotive components and aerospace parts to everyday appliances and consumer electronics, metal stamping is an indispensable part of modern manufacturing. This is where Metal Stamping Die OEM Manufacturers come into play. OEM, or Original Equipment Manufacturer, refers to companies that design and produce specialized equipment or components for other companies to incorporate into their products. Metal Stamping Die OEM Manufacturers are the craftsmen behind the dies that drive the metal stamping process. Their role is pivotal in ensuring the quality, accuracy, and efficiency of metal stamping operations across diverse industries. The Art and Science of Metal Stamping Dies Creating a metal stamping die is a combination of artistry and precision engineering. These dies are essentially custom-made tools, often crafted from high-grade steel or other durable materials. They come in various forms, including blanking dies, progressive dies, and compound dies, each designed to suit specific production needs. The process begins with meticulous design and engineering, where every detail is considered. Factors such as material thickness, tolerances, and production volume all play a crucial role in the die’s design. Once the design is finalized, the physical die is fabricated using state-of-the-art machinery and techniques. Precision is the name of the game in metal stamping die manufacturing. Even a minor flaw in the die can lead to defective parts, production delays, and increased costs. Therefore, manufacturers employ advanced technologies like computer-aided design (CAD) and computer-aided manufacturing (CAM) to ensure accuracy and consistency throughout the production process. Innovation in Metal Stamping Die Manufacturing The metal stamping industry is constantly evolving, driven by the demand for lighter, stronger, and more intricate components. OEM manufacturers must stay at the forefront of innovation to meet these demands. Some key areas of innovation in metal stamping die manufacturing include: Material Advancements: Using advanced materials such as high-strength alloys and composites to create dies that can withstand higher loads and produce finer details. Digitalization: Integrating digital tools and automation into the design and production processes to reduce lead times and improve precision. Simulation and Testing: Employing virtual simulations and testing to identify potential issues before physical dies are created, reducing waste and costs. Sustainability: Embracing sustainable practices by optimizing material usage and minimizing waste in die manufacturing. Key Players in Metal Stamping Die OEM Manufacturing Behind the scenes of the metal stamping industry are numerous Metal Stamping Die OEM Manufacturers, each contributing their unique expertise and capabilities. These manufacturers often partner with companies across various sectors, tailoring their solutions to meet specific needs. From established giants with decades of experience to nimble startups pushing the boundaries of innovation, Metal Stamping Die OEM Manufacturers are the unsung heroes of manufacturing, enabling industries to create products that shape our world. In conclusion, Metal Stamping Die OEM Manufacturers play a pivotal role in modern manufacturing by crafting precision tools that drive the metal stamping process. Their commitment to innovation ensures that the industry continues to meet the evolving demands of diverse sectors. As we look to the future of manufacturing, it’s clear that these OEM manufacturers will remain at the forefront, driving progress and excellence in metal stamping.
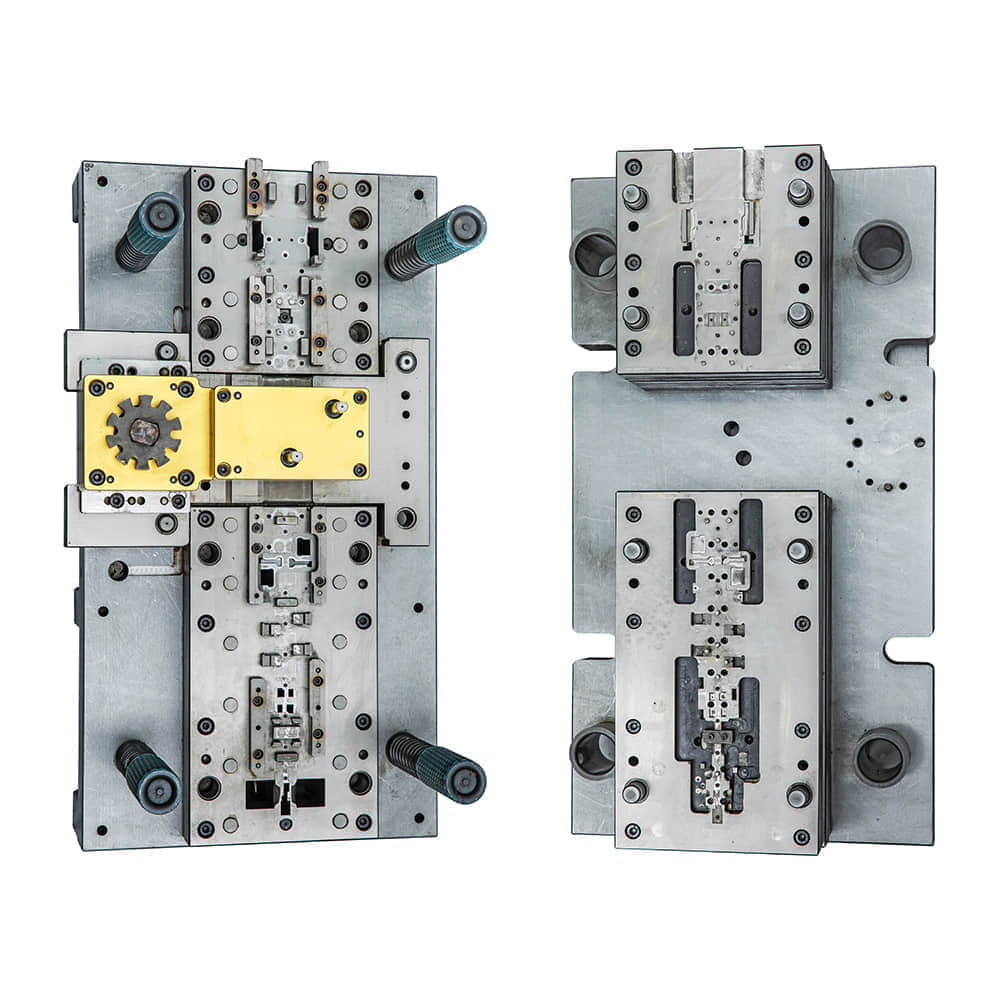