SMC Molding: A Revolution in Composite Materials
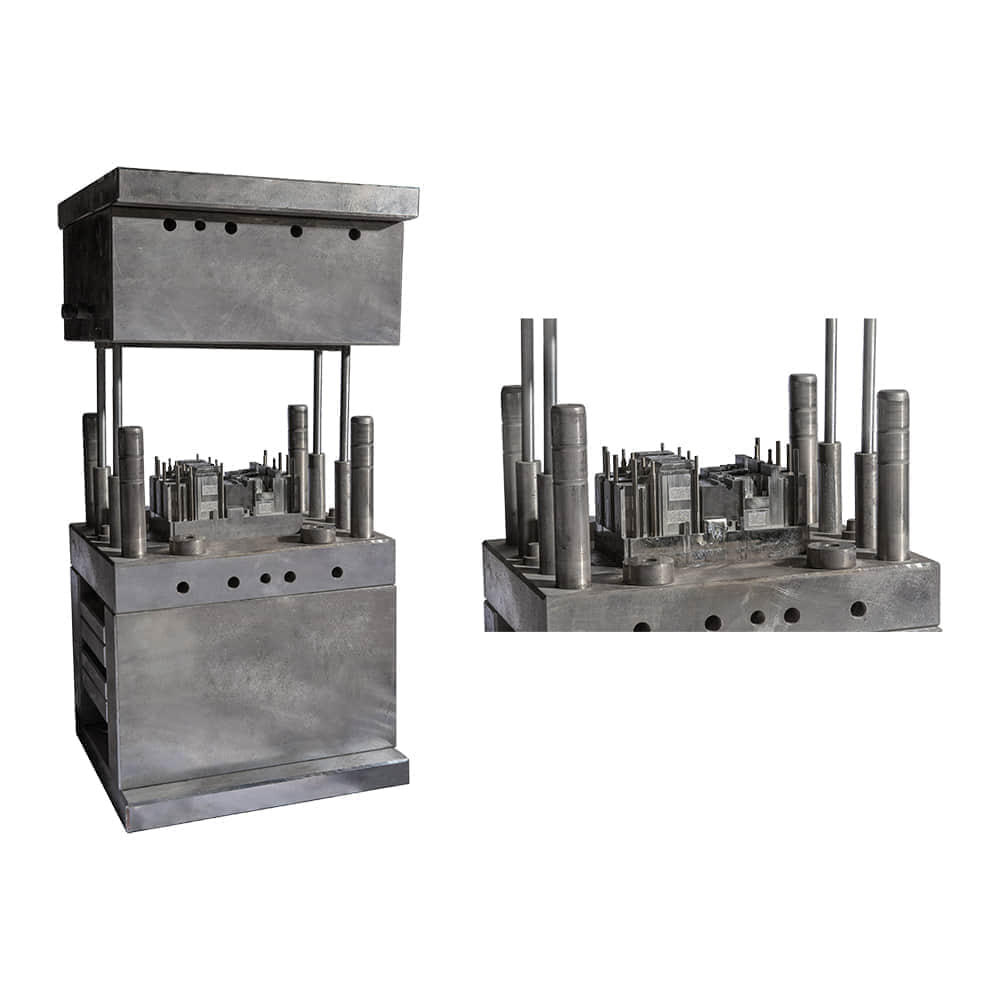
In the realm of composite materials, Sheet Molding Compound (SMC) has emerged as a game-changer. SMC molding offers a myriad of advantages that make it a popular choice for various industries. In this article, we delve into the world of SMC molding, exploring its key features, applications, and the advantages it brings to the table.
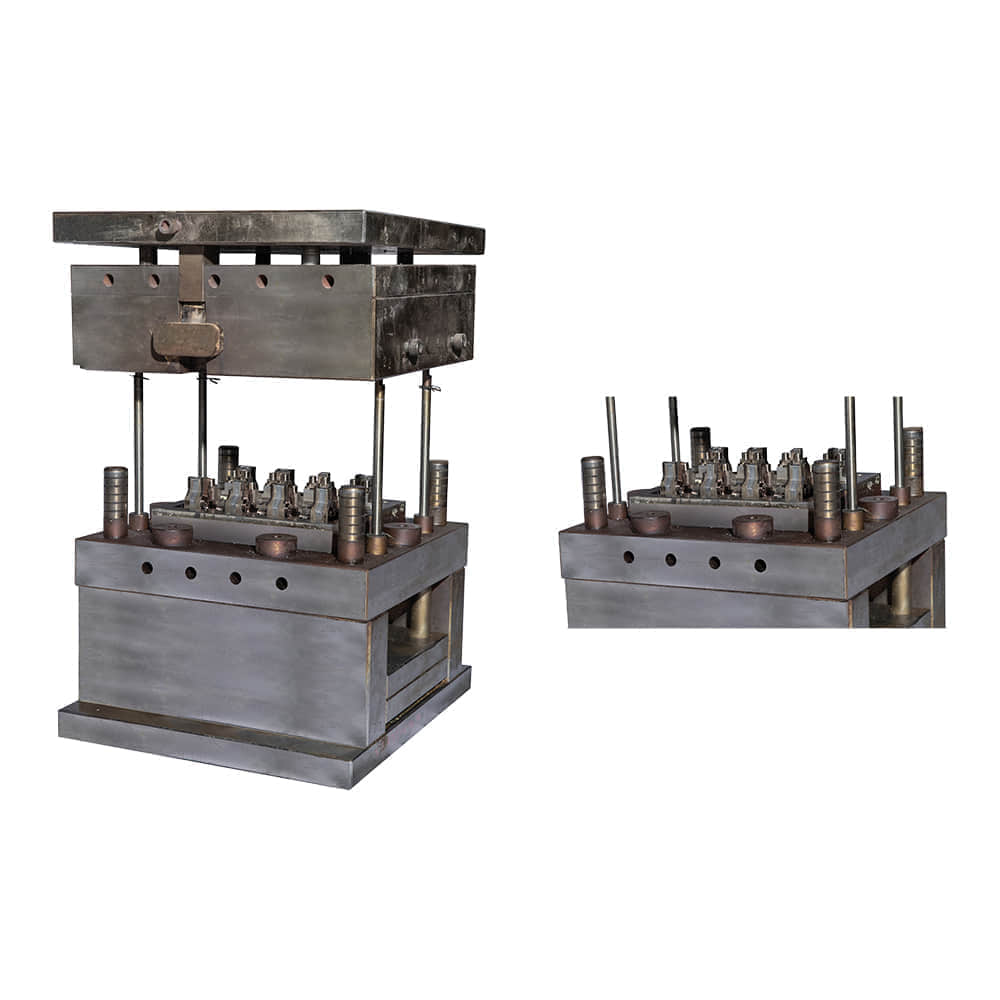
What is SMC Molding? SMC, or Sheet Molding Compound, is a type of composite material that consists of a combination of resins, fibers, and additives. This blend is typically prepped in a sheet form and is ready for molding into various shapes and sizes. The process of SMC molding involves the compression of these sheets at elevated temperatures, allowing for the creation of high-strength, durable, and complex parts and components. The Components of SMC Resins:SMC typically uses polyester resins, although other types can be employed depending on specific requirements. These resins play a crucial role in providing the material with its structural integrity. Fibers:Reinforcing fibers, such as glass or carbon fibers, are incorporated into the SMC to enhance its strength and rigidity. The choice of fibers can be tailored to meet specific performance needs. Additives:Various additives, including fillers, flame retardants, and pigments, can be added to the SMC mixture to achieve desired properties and aesthetics. Advantages of SMC Molding SMC molding offers a plethora of advantages, making it a preferred choice for manufacturers in various industries: High Strength:SMC components exhibit exceptional strength-to-weight ratios, making them ideal for applications requiring structural integrity and durability. Complex Shapes:SMC can be molded into intricate and complex shapes with ease, allowing for design flexibility and innovation. Corrosion Resistance:SMC is highly resistant to corrosion, making it suitable for outdoor and harsh environment applications. Low Maintenance:Components made from SMC require minimal maintenance, reducing long-term operational costs. Excellent Dielectric Properties:SMC is an excellent insulator, making it perfect for electrical and electronic applications. Weight Reduction:SMC’s lightweight nature contributes to fuel efficiency in automotive and aerospace industries. Design Freedom:Manufacturers have the freedom to incorporate design features directly into the SMC sheet, reducing the need for secondary operations. Applications of SMC Molding SMC molding finds applications in a wide range of industries: Automotive:SMC is used to manufacture various automotive parts, including body panels, bumpers, and interior components, due to its lightweight and high strength properties. Aerospace:SMC is utilized in aircraft interiors and structural components, contributing to weight reduction and fuel efficiency. Construction:SMC is used for producing durable and corrosion-resistant architectural elements like cladding and facades. Electrical and Electronics:SMC’s excellent dielectric properties make it suitable for electrical enclosures, switchgear, and insulators. Renewable Energy:SMC is employed in wind turbine components and solar panel structures, taking advantage of its strength and weather resistance. Marine:SMC is used for boat hulls, decks, and other marine components due to its resistance to water and corrosion. The Future of SMC Molding As industries continue to prioritize lightweight, durable, and environmentally friendly materials, SMC molding is expected to play an increasingly vital role. Advances in materials science and manufacturing processes are likely to further enhance the capabilities and applications of SMC, paving the way for innovative solutions in various sectors. In conclusion, SMC molding is a versatile and transformative technology in the realm of composite materials. Its unique blend of strength, versatility, and cost-effectiveness makes it an attractive choice for industries seeking to push the boundaries of what is possible in design and performance. With ongoing developments and innovations, SMC molding is poised to shape the future of composite materials across multiple industries.
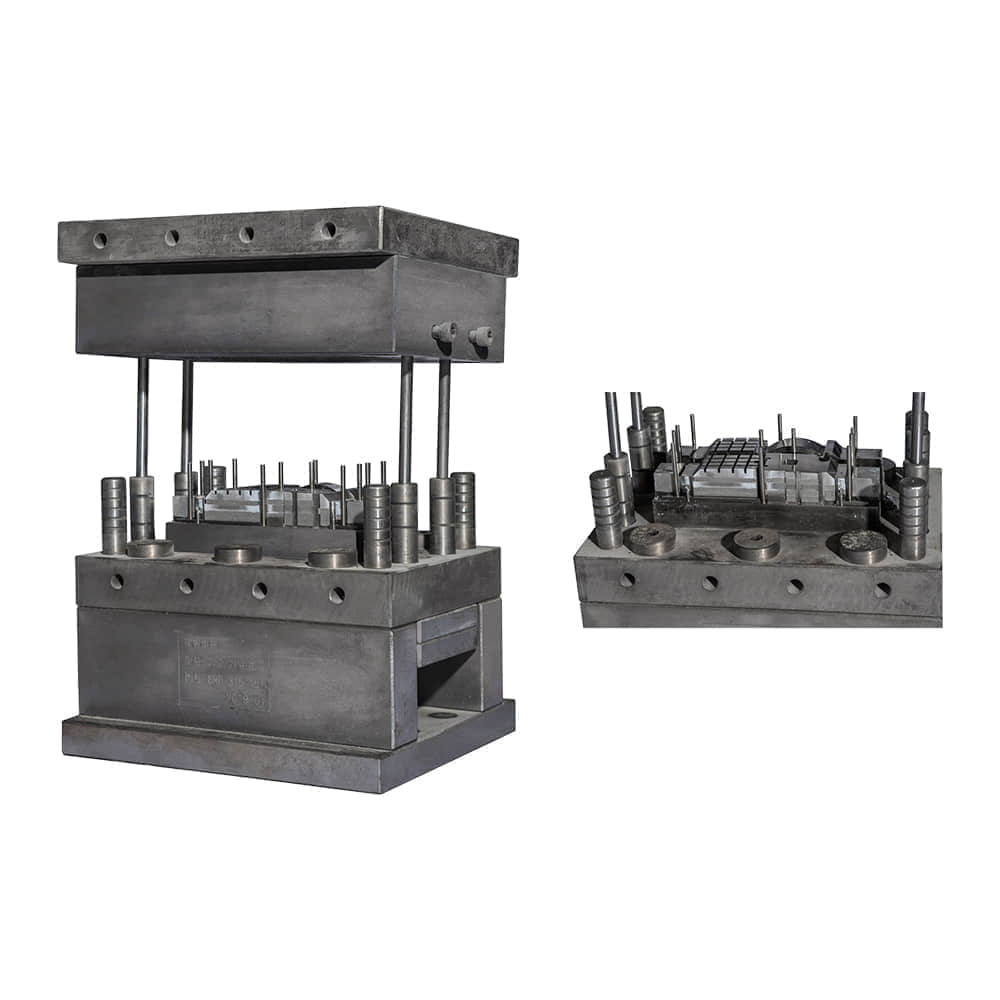