Introduction
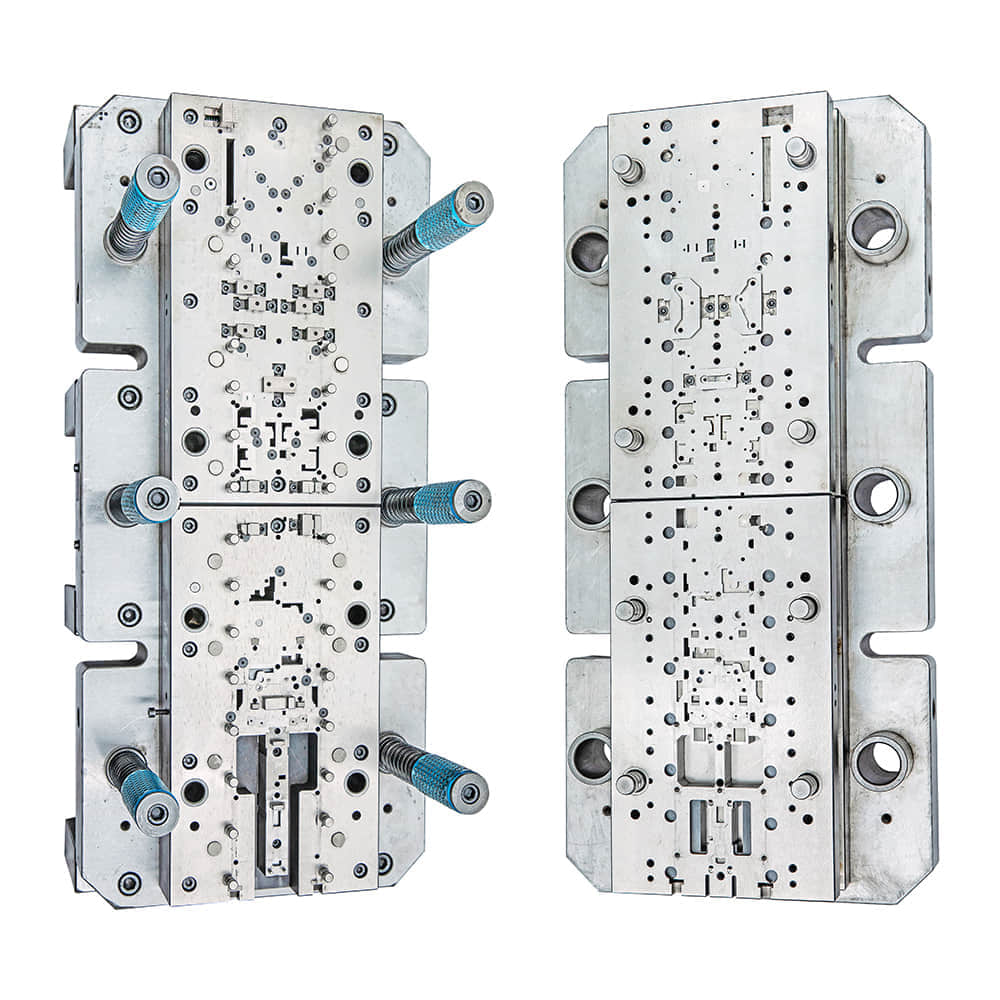
In the realm of manufacturing and industrial processes, the role of precision and efficiency cannot be overstated. One crucial tool that embodies these principles is the blanking die. Blankin die, an essential component in the field of metalworking, plays a significant role in shaping, cutting, and transforming raw materials into intricate components that drive various industries. This article delves into the world of blanking dies, exploring their design, functionality, and impact on modern production processes.
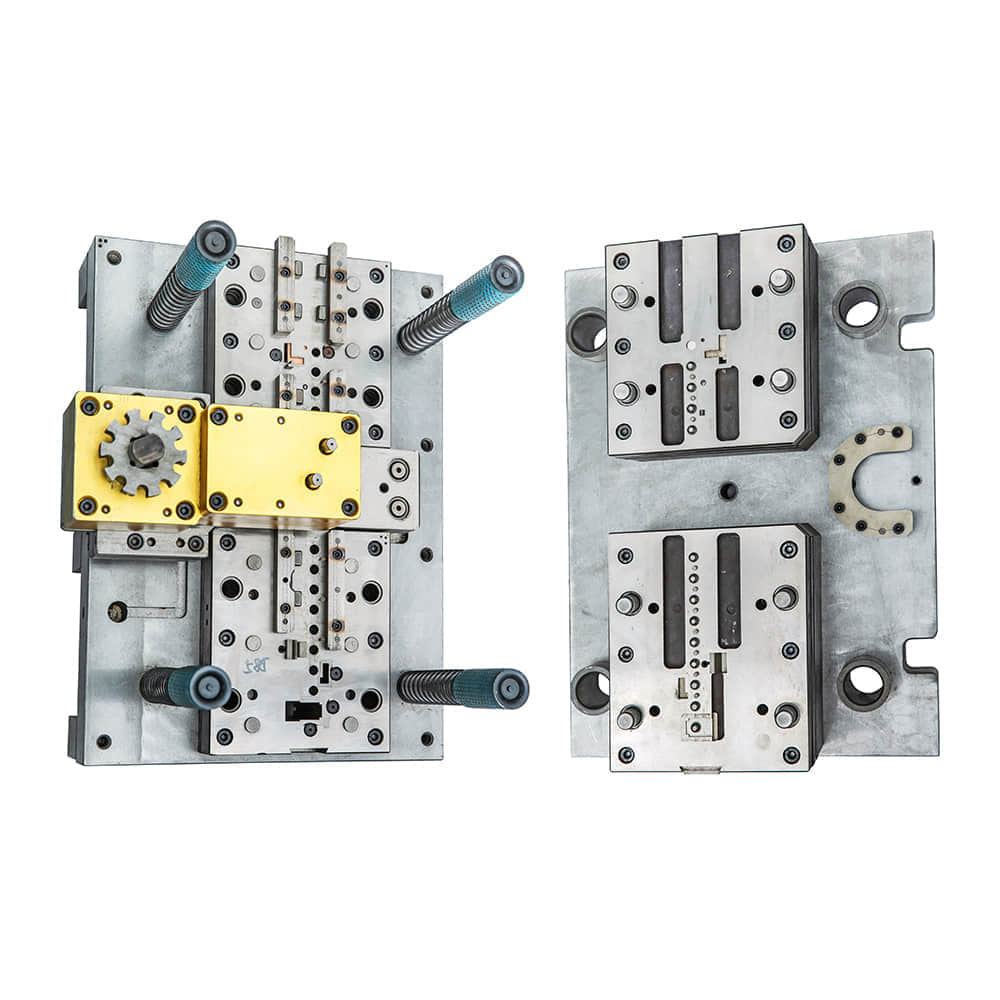
Understanding Blanking Dies Blanking dies are specialized tools used to cut intricate shapes from sheet metal with precision and consistency. The process involves placing a sheet of metal between the upper and lower portions of the die, followed by a powerful force that pierces through the metal and creates the desired shape. This technology is widely employed in the automotive, aerospace, electronics, and consumer goods industries, where precision and quality are paramount. Design and Components The design of a blanking die is a meticulous process that requires careful consideration of several factors. The die is typically made from high-strength tool steel, capable of withstanding the immense pressures involved in the cutting process. The components of a blanking die include: Punch:The punch is the upper part of the die and is responsible for creating the desired shape by exerting pressure on the sheet metal. It is often customized to the specific shape required by the product. Die Block:The die block, also known as the matrix, is the lower part of the die. It provides a base for the sheet metal to rest on during the cutting process and helps define the final shape. Strippers:These components help remove the cut piece from the punch after the operation, ensuring that the finished product doesn’t stick to the punch. Pilots and Guiding Mechanisms:To ensure accurate alignment between the punch and die block, guiding mechanisms such as pilots are used. These maintain proper positioning and prevent errors during the cutting process. Functionality and Applications The primary function of blanking dies is to transform raw materials into precise components required for various industries. Their applications are diverse: Automotive Industry:Blanking dies are extensively used in the production of automobile parts such as gears, brackets, and panels. The ability to create intricate shapes with minimal waste makes them indispensable in this sector. Electronics:In the electronics industry, where miniaturization and precision are crucial, blanking dies are employed to create components like connectors, contacts, and small metal parts used in electronic devices. Aerospace:Aerospace components demand high precision and structural integrity. Blanking dies are utilized to produce parts like brackets, fasteners, and structural elements for aircraft and spacecraft. Consumer Goods:From utensils to jewelry, blanking dies enable the production of aesthetically pleasing and functional items. The ability to mass-produce intricate designs efficiently contributes to the affordability and availability of consumer goods. Advantages and Challenges Blanking dies offer several advantages, such as high precision, repeatability, and efficient material usage. They facilitate mass production while maintaining consistency in the produced parts. However, there are challenges as well. The design and fabrication of blanking dies can be complex and costly, particularly for intricate shapes. Additionally, wear and tear due to high-pressure operations can lead to maintenance issues and affect the quality of the cut. Conclusion In the world of modern manufacturing, blanking dies stand as a testament to precision engineering and technological innovation. Their ability to transform raw materials into intricate components with speed and accuracy has revolutionized industries ranging from automotive to electronics. As technology continues to evolve, blanking dies will likely see further enhancements, contributing to the advancement of various sectors and shaping the products we use daily.
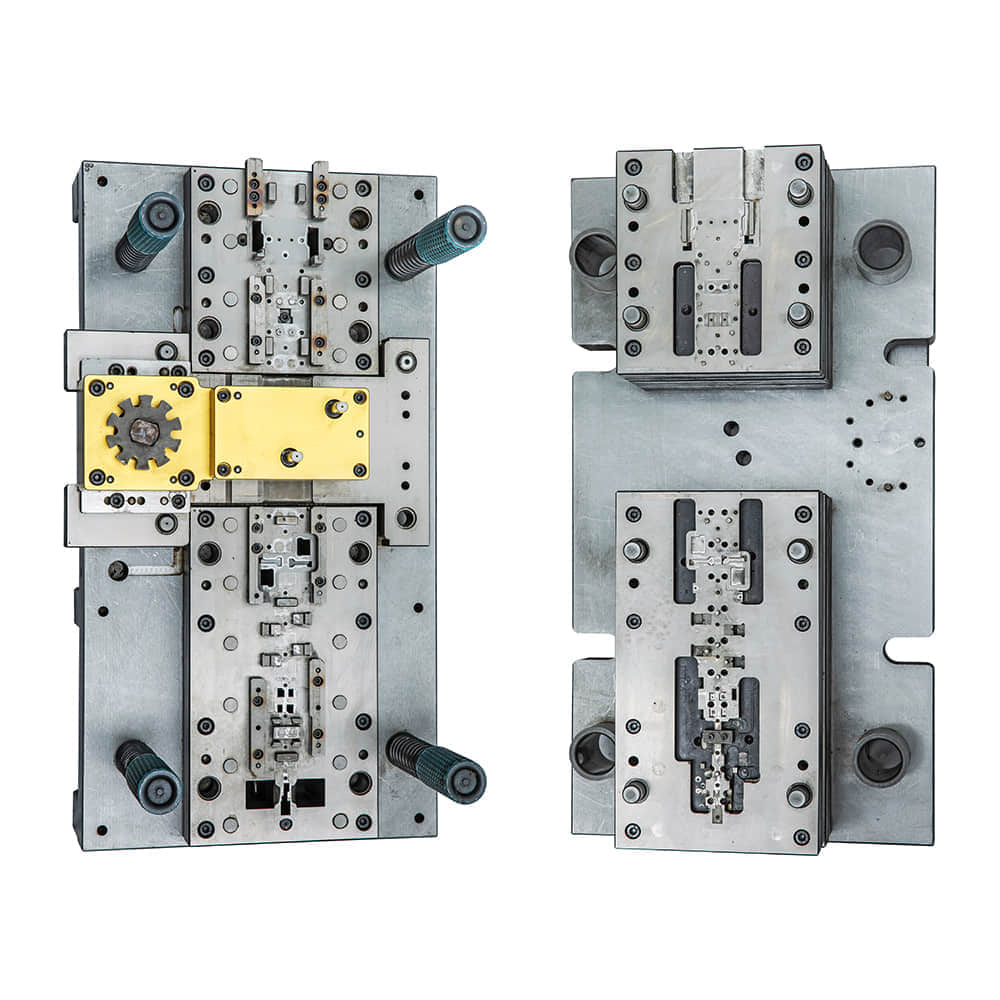