Injection molding is a manufacturing process that has revolutionized the production of plastic and other materials. It allows for the creation of intricate and precise parts with remarkable consistency. In this article, we will delve into the world of injection molded parts, exploring the process, its advantages, and its diverse applications.
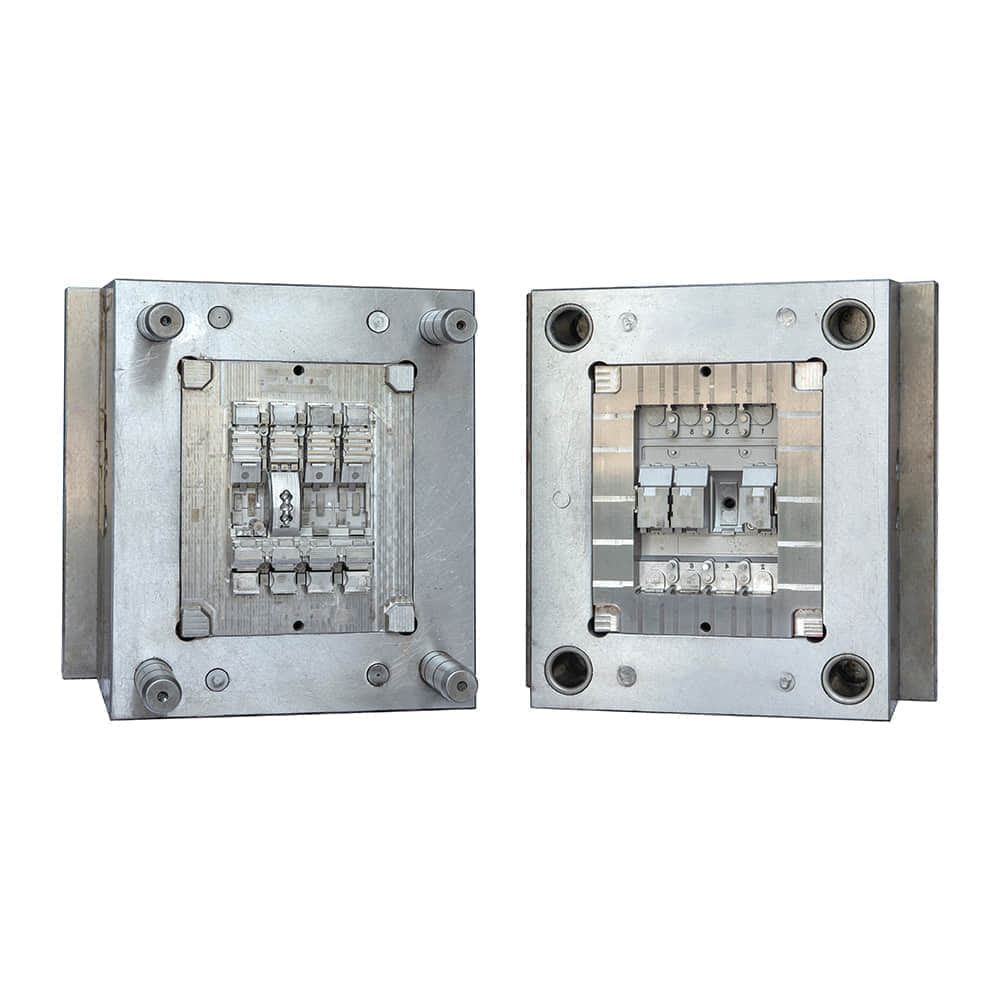
The Injection Molding Process
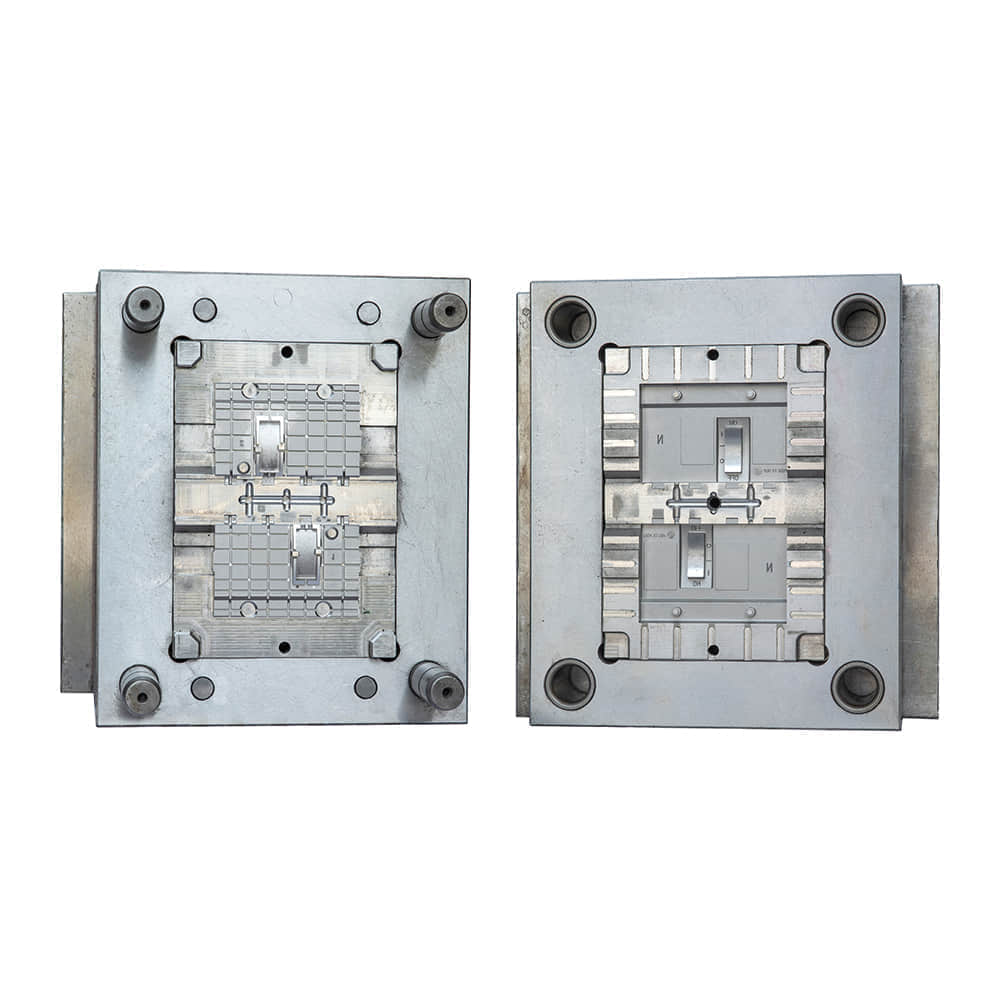
Injection molding is a manufacturing technique that involves melting a material and injecting it into a mold cavity. Once the material cools and solidifies, it takes the shape of the mold, resulting in the production of a specific part or product. This process is highly versatile and can be used with a wide range of materials, including plastics, metals, ceramics, and even some composite materials. Precision and Consistency One of the primary advantages of injection molding is the precision it offers. The molds used in this process are typically made with computer-aided design (CAD) technology, ensuring that each part is replicated with exceptional accuracy. This level of precision is crucial in industries where tight tolerances and exact specifications are required. Furthermore, injection molding is known for its consistency. Each part produced is virtually identical to the next, regardless of batch size. This level of consistency is particularly valuable in industries like automotive manufacturing, where safety and performance standards are stringent. Advantages of Injection Molded Parts Cost-Effective Production Injection molding is a cost-effective manufacturing method, especially for high-volume production runs. The initial tooling costs can be significant, but once the molds are created, the cost per part decreases substantially. This makes injection molding an excellent choice for producing large quantities of parts or products. Complex Geometries Injection molding can create parts with complex geometries that would be difficult or impossible to achieve with other manufacturing methods. This capability allows for innovative designs and the production of intricate components for various applications. Wide Material Selection The versatility of injection molding extends to the materials that can be used. From commodity plastics to high-performance engineering resins, there is a vast selection of materials available for injection molding. This allows manufacturers to choose the material that best suits their specific requirements, whether it’s for strength, durability, heat resistance, or other properties. Reduced Post-Processing Many parts produced through injection molding require minimal post-processing. This reduces the overall production time and cost. In some cases, parts can be used immediately after they are ejected from the mold, saving both time and resources. Applications of Injection Molded Parts The applications of injection molded parts are diverse and can be found in various industries, including: 1. Automotive Industry Injection molded parts are used extensively in the automotive industry for components like bumpers, interior panels, and engine components. The precision and durability of injection molded parts are critical in ensuring the safety and reliability of vehicles. 2. Medical Devices The medical industry relies on injection molded parts for items such as syringes, medical device housings, and surgical instruments. The high level of precision and cleanliness achievable through injection molding is vital for these applications. 3. Consumer Electronics Injection molded parts play a significant role in the production of consumer electronics, including phone cases, computer components, and electrical connectors. The ability to create intricate designs with tight tolerances is essential in this sector. 4. Packaging Plastic packaging, such as bottles, containers, and caps, is often manufactured through injection molding. The process allows for efficient production of standardized and custom packaging solutions. 5. Aerospace Aerospace applications demand lightweight, high-strength components, making injection molded parts a suitable choice for items like interior cabin components and air ducts. Conclusion Injection molded parts have become an integral part of modern manufacturing across various industries due to their precision, consistency, and cost-effectiveness. The ability to produce complex geometries with a wide range of materials makes injection molding a versatile and valuable manufacturing process. As technology continues to advance, it is likely that injection molding will continue to evolve, enabling even more innovative and efficient production methods in the future.
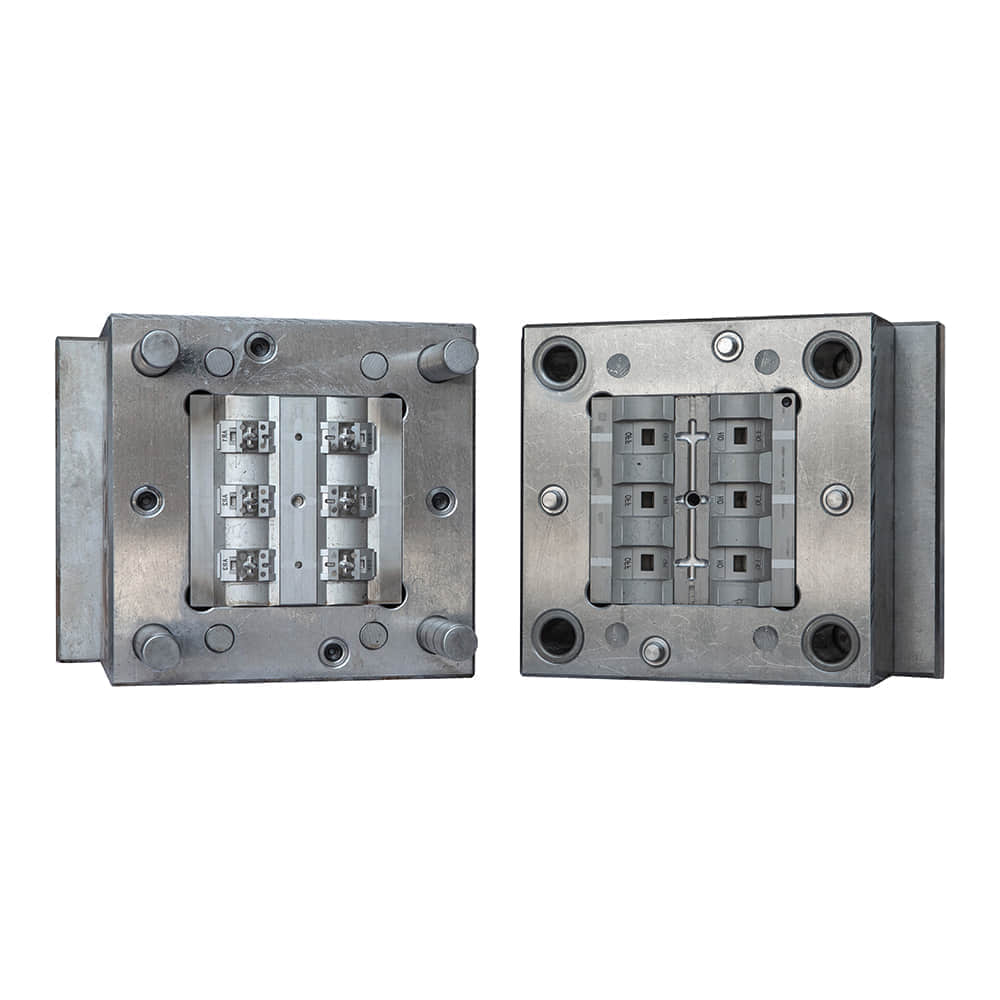