Innovation and Precision: The World of Injection Molded Parts Manufacturing
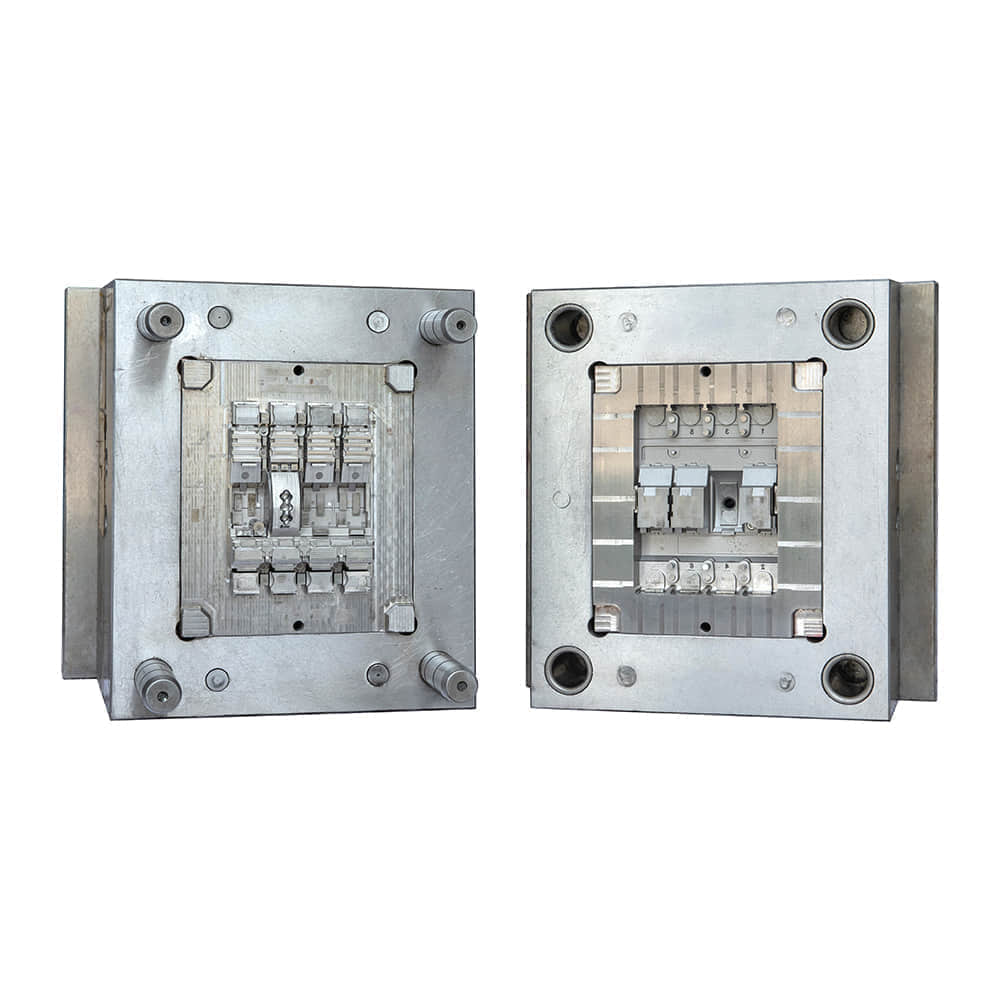
In today’s rapidly evolving industrial landscape, injection molded parts have become indispensable components across various industries, from automotive and electronics to medical devices and consumer goods. These versatile and cost-effective components owe their success to injection molded parts manufacturers who combine innovation with precision to meet the ever-growing demands of modern manufacturing. In this article, we’ll delve into the world of injection molded parts manufacturing, exploring the processes, materials, and innovations that drive this dynamic industry.
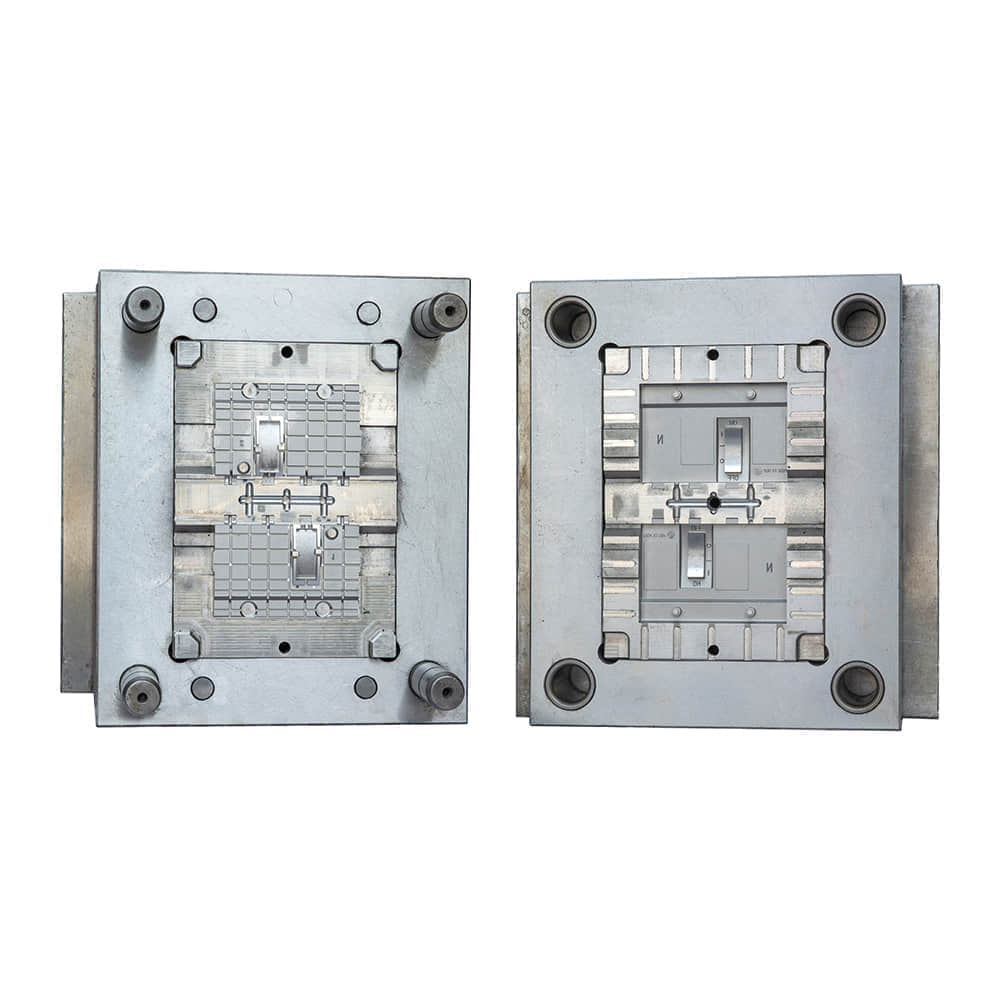
The Art of Injection Molding Injection molding is a manufacturing process that involves injecting molten material, typically thermoplastics, into a mold cavity to create a precise, three-dimensional replica of the desired part. This process is known for its ability to produce high-quality, complex parts in large quantities with remarkable consistency. It’s no wonder that injection molded parts have found their way into countless industries. Materials Matter One of the critical factors in injection molding success is the selection of materials. Manufacturers must carefully choose the right thermoplastic material for a specific application, considering factors such as strength, flexibility, heat resistance, and cost-effectiveness. Common materials include ABS, polypropylene, polycarbonate, and nylon, among others. Innovations in material science continue to expand the possibilities for injection molding, allowing for the creation of parts with enhanced properties and performance. Precision and Consistency Precision is the hallmark of injection molded parts manufacturing. Modern injection molding machines are equipped with advanced controls and automation systems that ensure consistent part quality. These machines can precisely control factors like temperature, pressure, and injection speed, resulting in parts that meet tight tolerances and specifications. Moreover, the use of computer-aided design (CAD) and computer-aided manufacturing (CAM) software enables manufacturers to optimize the mold design for maximum efficiency and accuracy. Sustainability Initiatives As environmental concerns grow, injection molded parts manufacturers are increasingly focusing on sustainability. Many are adopting eco-friendly materials and processes to reduce waste and energy consumption. Bioplastics, recycled plastics, and energy-efficient machines are some of the innovations in this direction. Sustainability not only benefits the environment but also aligns with the preferences of consumers and regulatory requirements in many regions. Customization and Prototyping The versatility of injection molding allows for the creation of custom parts tailored to specific applications. Manufacturers often work closely with their clients to design and prototype parts that meet precise requirements. Rapid prototyping technologies, such as 3D printing and CNC machining, have become invaluable tools for developing and testing molds before mass production begins, saving time and resources. Quality Control and Testing Quality control is a paramount concern in injection molded parts manufacturing. Rigorous testing procedures, including dimensional inspections, material analysis, and stress testing, ensure that each part meets the highest standards. Innovations in non-destructive testing techniques and quality assurance methodologies continue to enhance the reliability and safety of injection molded parts. The Future of Injection Molded Parts Manufacturing Looking ahead, the injection molded parts manufacturing industry is poised for further innovation and growth. Advances in automation and Industry 4.0 technologies are streamlining production processes and increasing efficiency. The integration of artificial intelligence (AI) and machine learning into quality control and predictive maintenance will further enhance the industry’s capabilities. In conclusion, injection molded parts manufacturers play a vital role in shaping our modern world. Their commitment to innovation and precision enables the production of high-quality, customized components that drive progress across a wide range of industries. As technology continues to advance, we can expect even more exciting developments in injection molding, making it an industry to watch in the years to come.
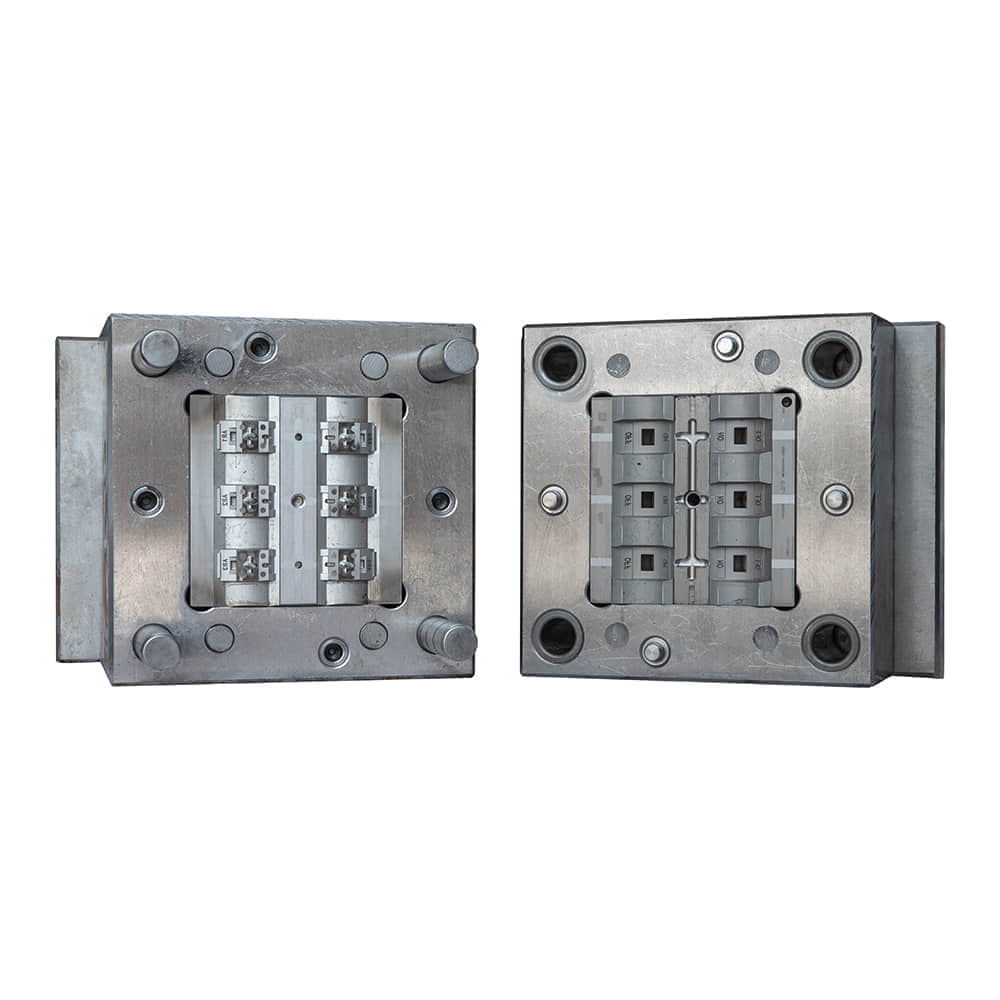