In the world of manufacturing, precision and innovation are two essential pillars upon which the industry stands. Metal stamping die manufacturers play a pivotal role in this landscape, contributing significantly to the production of a wide range of products we use daily. In this article, we will delve into the fascinating world of metal stamping die manufacturers, exploring their significance, processes, and the vital role they play in shaping industries worldwide.
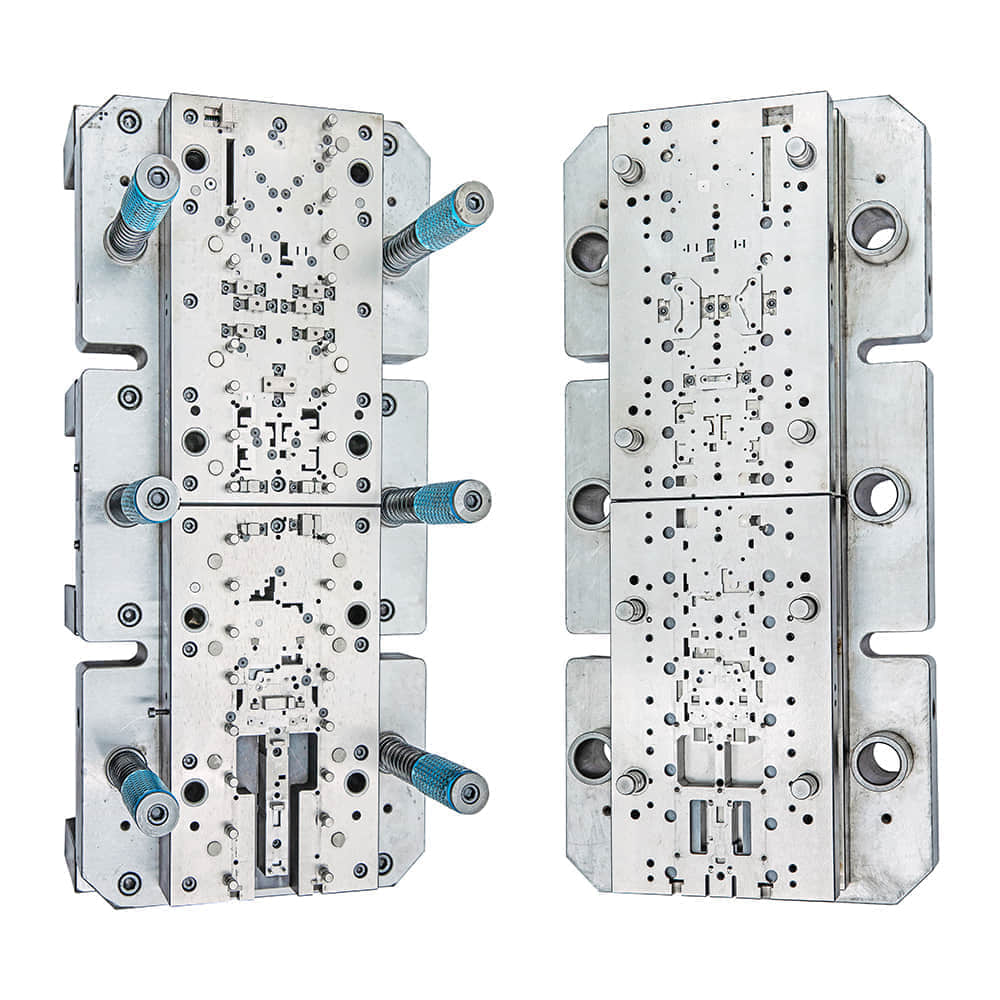
Understanding Metal Stamping Dies

Before delving into the role of metal stamping die manufacturers, it is crucial to comprehend what metal stamping dies are. Metal stamping dies, often referred to as tooling, are specialized tools used in the manufacturing process to shape, cut, or deform metal sheets into specific forms or designs. These dies are precision-engineered to ensure consistency and accuracy in the stamped parts they produce. The Significance of Metal Stamping Die Manufacturers Metal stamping die manufacturers are the unsung heroes of the manufacturing world. They cater to a wide range of industries, including automotive, aerospace, electronics, and more. Here are some reasons why they are essential: Precision Production: Metal stamping die manufacturers are responsible for creating dies with impeccable precision. This precision is vital, as it directly influences the quality and accuracy of the stamped metal components. Cost-Effective Manufacturing: Stamping dies allow for cost-effective mass production of metal parts. They significantly reduce labor costs and increase production efficiency, making them an integral part of manufacturing processes. Innovation Catalysts: These manufacturers constantly innovate and improve their die designs, materials, and processes. This innovation drives advancements in industries that rely on metal stamping, helping them stay competitive and relevant in the ever-evolving market. The Manufacturing Process Creating metal stamping dies is a meticulous and intricate process that requires a deep understanding of materials, engineering principles, and precision machining. Here are the key steps involved: Design and Engineering: The process begins with detailed design and engineering, where experts create 3D models and simulations of the desired metal part and its corresponding die. This phase ensures that the final product meets all specifications and quality standards. Material Selection: The choice of materials is critical. High-quality tool steel or carbide is commonly used to ensure durability and longevity. Machining and Fabrication: CNC machining and other advanced techniques are employed to fabricate the die. Every detail must be meticulously machined to achieve the desired precision. Heat Treatment: To enhance the hardness and wear resistance of the die, it undergoes a heat treatment process. Testing and Quality Assurance: Rigorous testing and quality control measures are employed to ensure the die meets the required tolerances and specifications. Maintenance and Repairs: Metal stamping dies require periodic maintenance and, occasionally, repairs to ensure they continue to produce high-quality stamped components over their lifespan. Pushing the Boundaries of Innovation Metal stamping die manufacturers are constantly pushing the boundaries of innovation. They adopt cutting-edge technologies like additive manufacturing (3D printing) and artificial intelligence to enhance their design and production processes. These advancements result in more efficient and cost-effective manufacturing methods, benefitting industries across the board. Conclusion Metal stamping die manufacturers are the driving force behind the scenes of modern manufacturing. Their commitment to precision, innovation, and quality plays a pivotal role in shaping industries worldwide. As technology continues to advance, we can expect these manufacturers to lead the way in revolutionizing the metal stamping industry, making it even more integral to our daily lives.
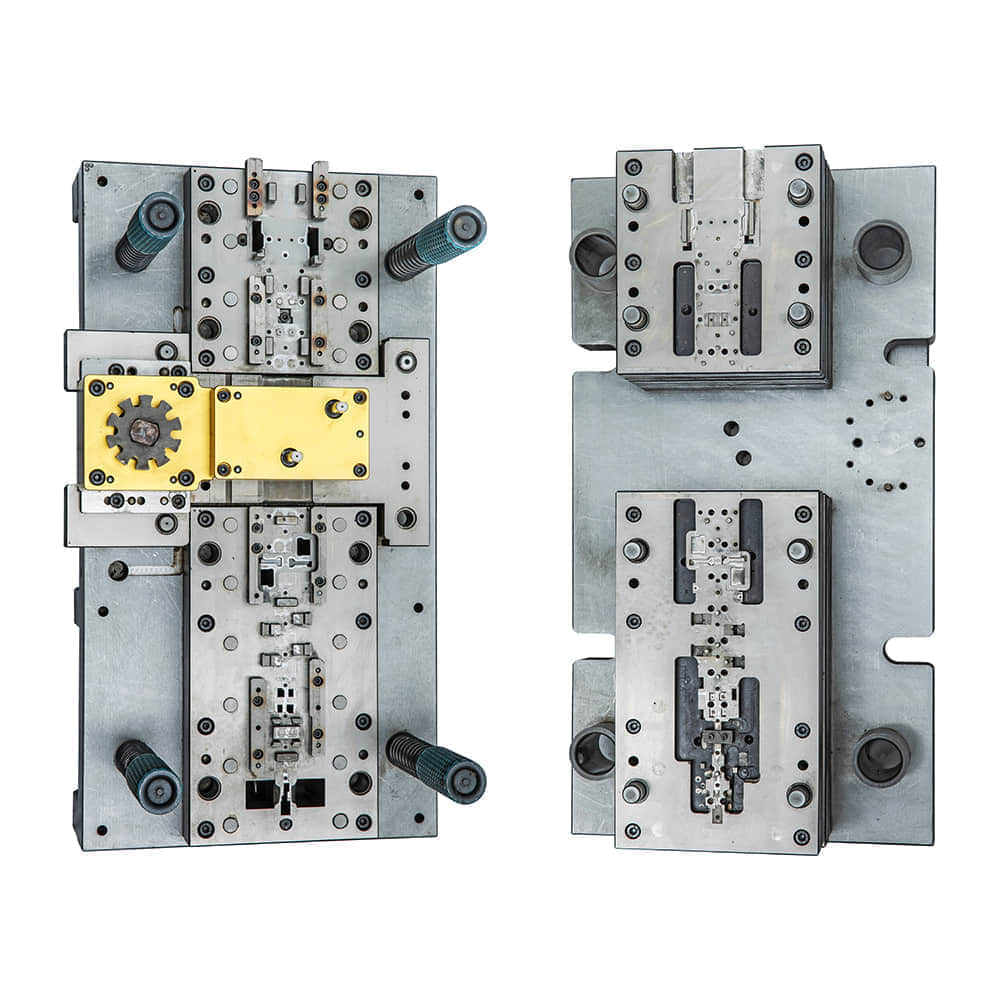