In the intricate world of manufacturing, injection molds stand as unsung heroes, quietly shaping the products that surround us. These intricate tools, which are central to the production of a vast array of consumer goods, owe their existence to the meticulous craftsmanship of injection mold manufacturers. In this article, we will delve into the fascinating world of injection mold manufacturing, exploring its significance, the intricate processes involved, and the role it plays in our daily lives.
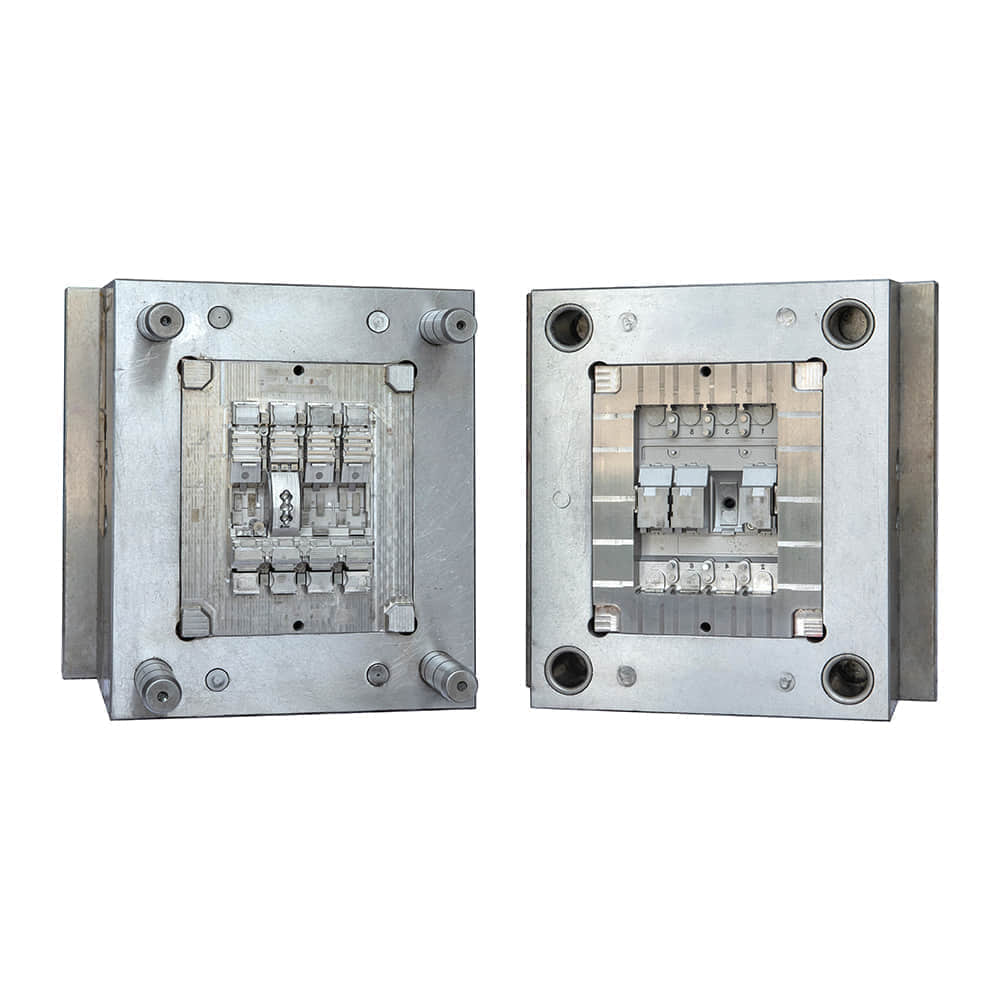
The Significance of Injection Molding
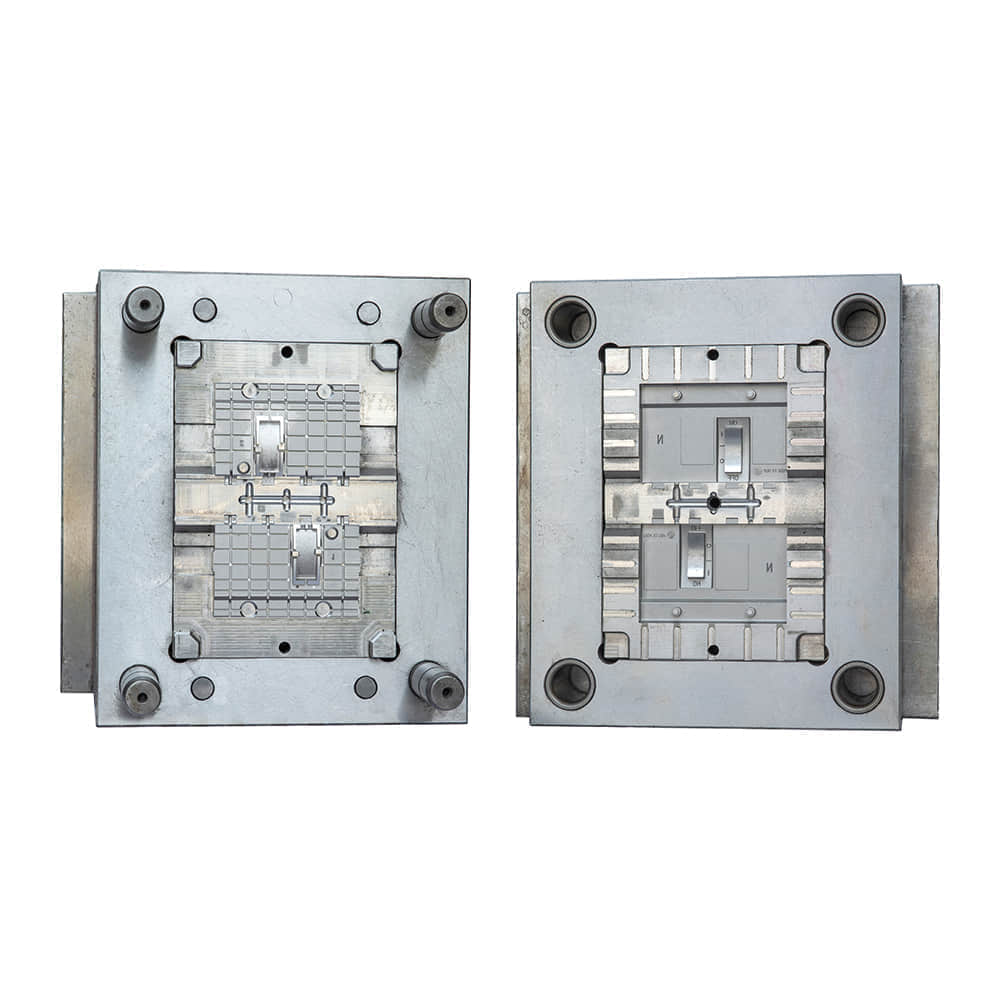
Injection molding is a manufacturing process that plays an indispensable role in our modern world. It is the method of choice for producing a wide range of items, from the tiniest plastic components to large automobile parts. In essence, it involves injecting molten material into a mold cavity, allowing it to cool and solidify, resulting in a precise and repeatable reproduction of the mold’s design. This process is not only efficient but also cost-effective, making it a preferred choice for mass production. The Craft of Injection Mold Manufacturing At the heart of this process lies the injection mold itself, a complex and precise piece of engineering. Injection mold manufacturers are the artisans responsible for crafting these molds with painstaking attention to detail. The process begins with the design phase, where skilled engineers create the blueprint for the mold, considering factors like material type, cooling systems, and part ejection mechanisms. These plans must be precise, as any imperfection can lead to defects in the final product. Once the design is complete, the next step is material selection. Injection molds can be made from various materials, including steel, aluminum, or even ceramics, depending on the specific application. The selected material must have the required strength, durability, and heat resistance to withstand the rigors of the injection molding process. After the material is chosen, the manufacturing process commences. Skilled machinists and toolmakers use state-of-the-art machinery to meticulously shape and assemble the mold components. Precision is paramount, as even the tiniest deviation from the design can lead to costly defects and production delays. Quality Control and Precision Injection mold manufacturing is a field where precision reigns supreme. The molds produced must meet strict quality standards to ensure the final products are flawless. Quality control measures, such as rigorous inspections and testing, are integral to the process. Manufacturers employ cutting-edge technology, including 3D scanning and metrology equipment, to verify the mold’s dimensions and functionality. This dedication to quality is essential to delivering molds that produce consistent, defect-free parts. Injection Mold Manufacturers in Our Lives The influence of injection mold manufacturers extends into virtually every aspect of our daily lives. Think of the plastic components in your smartphone, the buttons on your television remote, or the dashboard of your car. All of these rely on injection molded parts, and thus, on the expertise of injection mold manufacturers. These professionals are the unsung heroes behind the products we often take for granted. The Future of Injection Mold Manufacturing As technology advances, so too does the field of injection mold manufacturing. Innovations like 3D printing and computer-aided design (CAD) have revolutionized the industry, enabling faster prototyping and more complex mold designs. Additionally, sustainability is becoming an increasingly important consideration, leading manufacturers to explore eco-friendly materials and processes. In conclusion, injection mold manufacturing is a fascinating blend of art and science that shapes the modern world around us. The precision, craftsmanship, and innovation of injection mold manufacturers are central to the production of countless everyday items. As technology evolves and consumer demands change, so too will the world of injection mold manufacturing, ensuring its continued relevance in our lives.
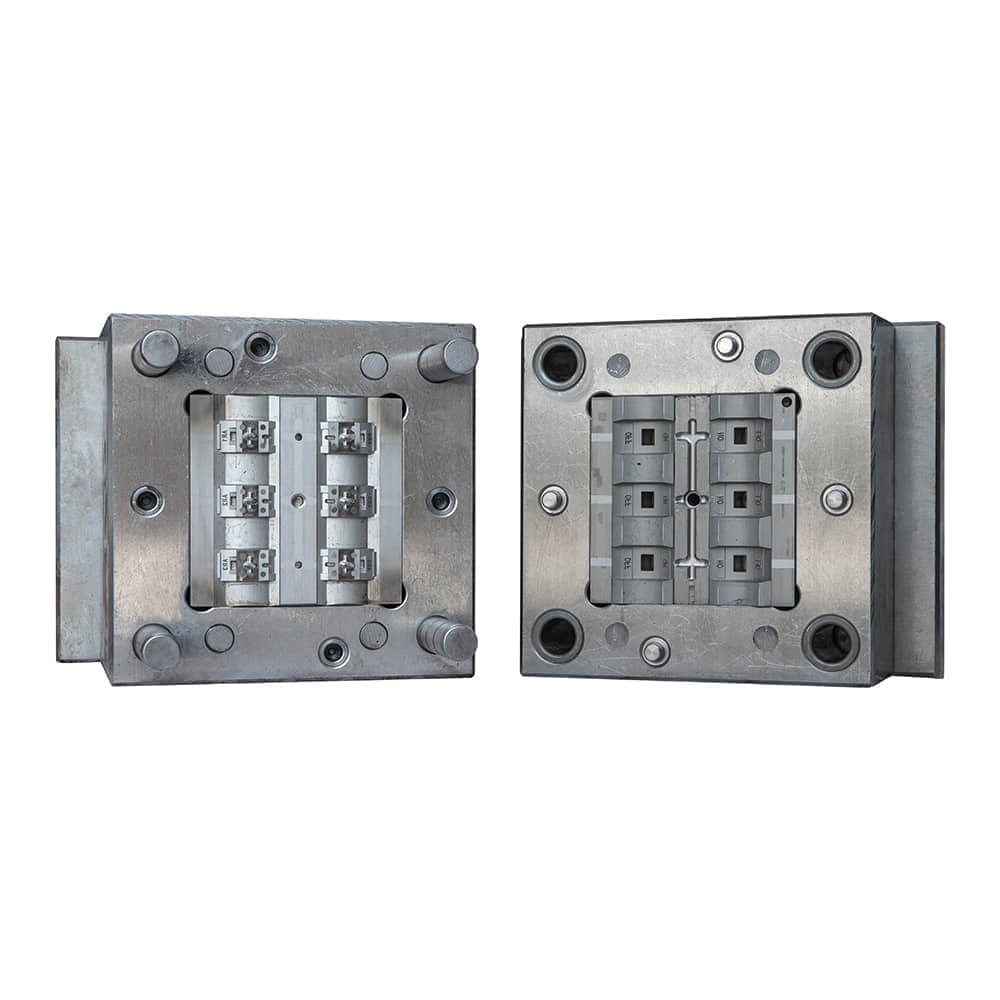