Thermosetting compression moulding, often referred to simply as compression moulding, is a widely used manufacturing process that transforms raw materials into durable and resilient products. This versatile method offers numerous advantages, making it a preferred choice in various industries such as automotive, aerospace, electronics, and more. In this article, we will delve into the world of thermosetting compression moulding, exploring its key principles, applications, and benefits.
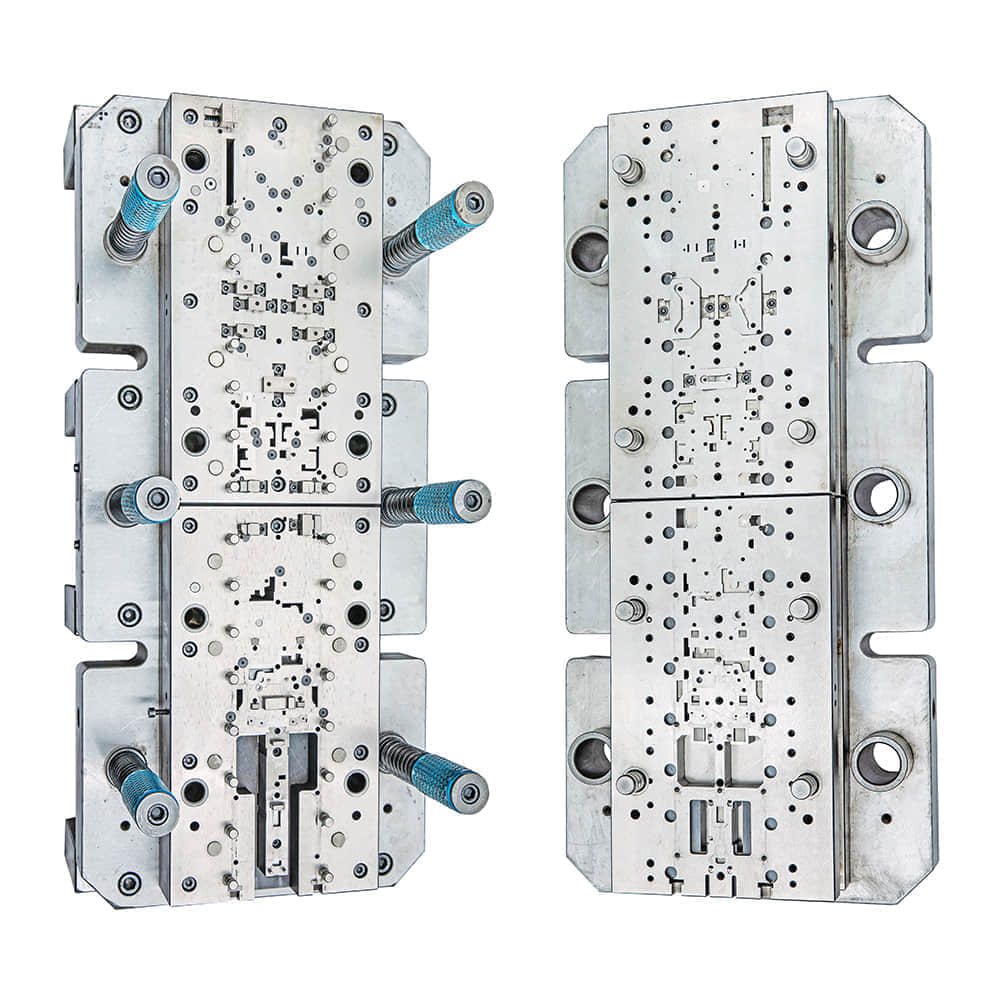
Understanding Thermosetting Compression Moulding
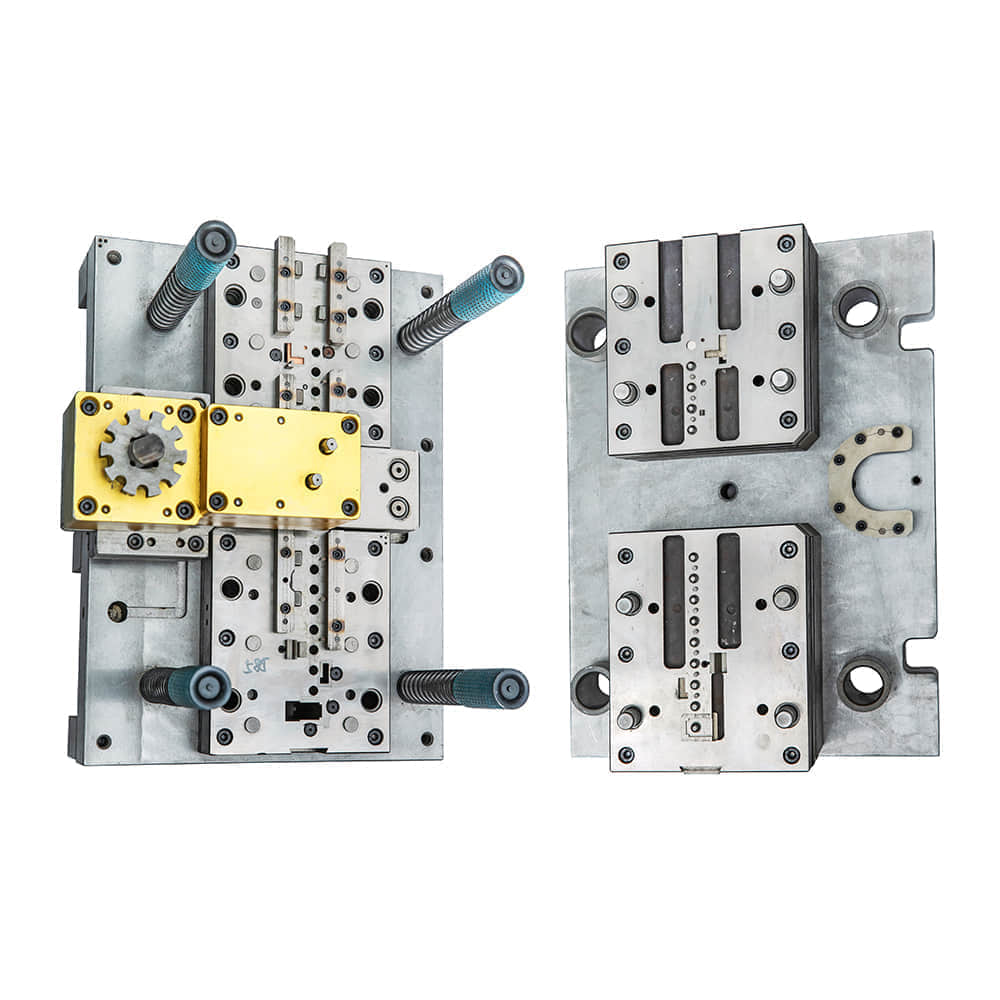
Thermosetting compression moulding is a manufacturing technique used to shape and cure thermosetting materials. Thermosetting materials, unlike thermoplastics, undergo a chemical transformation when heated, becoming rigid and stable. This process involves several key steps: 1. Material Preparation The process begins with the preparation of raw materials, which are typically in the form of granules, pellets, or pre-impregnated sheets. These materials often include phenolic resins, epoxy resins, and other thermosetting polymers, combined with reinforcement materials like fiberglass, carbon fiber, or aramid. 2. Mould Design A carefully designed mould, often made from metal, is used to shape the product. The mould consists of two halves that are brought together during the compression moulding process. 3. Loading the Material The prepared thermosetting material is placed into the open mould cavity. 4. Compression The mould halves are then closed and subjected to high pressure, typically achieved through hydraulic presses. This compression forces the material to conform to the mould’s shape and expels excess resin. 5. Curing The mould, now under pressure, is heated to a specific temperature to initiate the curing process. During curing, the thermosetting resin undergoes a chemical reaction, cross-linking and hardening into a solid form. 6. Cooling and Ejection After curing, the mould is cooled, allowing the part to solidify further. Once sufficiently cooled, the mould opens, and the finished product is ejected. Applications of Thermosetting Compression Moulding Thermosetting compression moulding finds applications in a wide range of industries, owing to its ability to produce high-strength, durable, and dimensionally stable components. Some common applications include: 1. Automotive Parts Compression moulding is used to manufacture various automotive components, including brake pads, clutch plates, and composite body panels, due to its excellent heat resistance and mechanical properties. 2. Electrical and Electronics The process is widely employed in the production of insulating components, circuit boards, and electrical connectors, thanks to its electrical insulation properties and dimensional stability. 3. Aerospace Aerospace applications utilize compression moulding for creating lightweight, high-strength composite parts like aircraft interior panels and structural components. 4. Consumer Goods Thermosetting compression moulding is used for producing consumer goods such as kitchenware, toilet seats, and electrical switchgear components. Advantages of Thermosetting Compression Moulding High Strength: Products manufactured through this process exhibit exceptional strength and rigidity, making them suitable for demanding applications. Dimensional Stability: Compression moulding offers precise control over part dimensions, ensuring consistency and accuracy in production. Chemical Resistance: Thermosetting materials are often resistant to chemicals, making them ideal for applications involving exposure to harsh substances. Heat Resistance: The cured thermosetting products can withstand high temperatures without deforming or degrading. Cost-Effective: The process is cost-effective for large-scale production runs, thanks to rapid cycle times and minimal material waste. Design Flexibility: Moulds can be customized to create complex shapes and intricate designs, offering design freedom. In conclusion, thermosetting compression moulding is a versatile manufacturing process that plays a crucial role in several industries, producing durable and high-performance components. Its ability to create products with outstanding mechanical properties, chemical resistance, and heat resistance make it a reliable choice for various applications. As technology and materials continue to advance, thermosetting compression moulding will likely remain a cornerstone of modern manufacturing. Title: “Leading the Way: China’s Premier Metal Stamping Die Manufacturers” China has established itself as a global manufacturing powerhouse, and its prowess in metal stamping die production is no exception. Chinese metal stamping die manufacturers have consistently demonstrated innovation, quality, and competitiveness on the global stage. In this article, we will explore the world of China’s metal stamping die manufacturers, their rise to prominence, and the key factors driving their success. A Legacy of Excellence China’s journey to becoming a leader in metal stamping die manufacturing is a testament to its unwavering commitment to quality and precision. Over the years, Chinese manufacturers have invested heavily in research, technology, and workforce development, positioning themselves at the forefront of this specialized industry. Cutting-Edge Technology Chinese metal stamping die manufacturers leverage cutting-edge technology to stay ahead of the curve. Computer Numerical Control (CNC) machining, high-speed milling, and advanced CAD/CAM software are just a few of the technologies that enable them to create intricate and precise stamping dies. This technological edge ensures the production of high-quality, dimensionally accurate components. Versatility in Material Expertise One of the key strengths of Chinese metal stamping die manufacturers is their expertise in working with a wide range of materials. Whether it’s steel, aluminum, copper, or exotic alloys, these manufacturers have the capability to craft stamping dies tailored to the specific material properties, ensuring optimal performance and longevity. Global Supply Chain Integration China’s strategic geographical location has made it a hub for global supply chain integration. Metal stamping die manufacturers in China have the advantage of easy access to raw materials, cost-effective transportation, and efficient logistics networks, allowing them to seamlessly serve international clients. Stringent Quality Control Quality control is paramount in the metal stamping die industry, and Chinese manufacturers take it seriously. They adhere to rigorous quality control processes, employing state-of-the-art inspection equipment to ensure that each die meets or exceeds industry standards. This commitment to quality has earned them the trust of customers worldwide. Cost-Effective Solutions Competitive pricing has been a significant driver of China’s success in metal stamping die manufacturing. Chinese manufacturers can offer cost-effective solutions without compromising on quality, making them an attractive choice for businesses looking to optimize their production costs. Skilled Workforce China’s skilled workforce is a valuable asset in the metal stamping die industry. Highly trained engineers, machinists, and technicians contribute their expertise to the design and production of precision dies. Ongoing training and development programs ensure that the workforce remains at the forefront of industry advancements. Global Reach and Impact Chinese metal stamping die manufacturers have expanded their reach far beyond domestic borders. They have successfully established partnerships and collaborations with international clients, becoming an integral part of global supply chains. Their stamping dies are utilized in a myriad of industries, including automotive, electronics, aerospace, and more. Sustainability Initiatives Environmental sustainability is a growing concern, and Chinese metal stamping die manufacturers are actively addressing this issue. Many have adopted eco-friendly practices, such as recycling and waste reduction, to minimize their environmental footprint. This commitment to sustainability aligns with global trends and positions them as responsible industry leaders. In conclusion, China’s metal stamping die manufacturers have risen to prominence through a combination of cutting-edge technology, versatile material expertise, stringent quality control, and a commitment to cost-effective solutions. Their contributions to global supply chains and dedication to innovation ensure that they will continue to play a vital role in the manufacturing landscape for years to come. As the industry evolves, Chinese manufacturers are well-positioned to lead the way in shaping its future. Title: “China’s Excellence in Molded Case Parts Manufacturing” China has emerged as a global powerhouse in the field of molded case parts manufacturing. With a dedication to precision, innovation, and cost-effectiveness, Chinese manufacturers have become leaders in producing a wide range of molded case parts for various industries. In this article, we will explore the world of China’s molded case parts manufacturers, their rise to prominence, and the factors driving their success. A Legacy of Quality China’s journey to becoming a premier molded case parts manufacturer is characterized by a relentless commitment to quality. Over the years, Chinese manufacturers have invested heavily in research, technology, and workforce development, positioning themselves as leaders in this specialized industry. Cutting-Edge Technology Chinese molded case parts manufacturers leverage cutting-edge technology to maintain their competitive edge. Computer-aided design and manufacturing (CAD/CAM) software, advanced injection molding machines, and robotics automation are just a few of the technologies that enable them to create intricate and precise molded case parts. This technological prowess ensures the production of high-quality components with tight tolerances. Versatility in Materials One of the key strengths of Chinese manufacturers is their expertise in working with a wide range of materials. Whether it’s engineering plastics, thermosetting resins, or specialty compounds, these manufacturers have the capability to craft molded case parts tailored to the specific material properties, ensuring optimal performance and durability. Global Supply Chain Integration China’s strategic geographical location has made it a hub for global supply chain integration. Molded case parts manufacturers in China benefit from easy access to raw materials, cost-effective transportation, and efficient logistics networks, allowing them to efficiently serve international clients. Rigorous Quality Control Quality control is paramount in the molded case parts industry, and Chinese manufacturers uphold stringent standards. They employ advanced quality control processes, including precision measurement and inspection, to ensure that each part meets or exceeds industry specifications. This commitment to quality has earned them the trust of customers worldwide. Competitive Pricing Competitive pricing has been a significant driver of China’s success in molded case parts manufacturing. Chinese manufacturers can offer cost-effective solutions without compromising on quality, making them an attractive choice for businesses looking to optimize their production costs. Skilled Workforce China’s skilled workforce is a valuable asset in the molded case parts industry. Highly trained engineers, mold designers, and technicians contribute their expertise to the design and production of precision parts. Continuous training and development programs ensure that the workforce remains at the forefront of industry advancements. Global Impact Chinese molded case parts manufacturers have expanded their global footprint significantly. They have established partnerships and collaborations with international clients, becoming an integral part of global supply chains. Their molded case parts find applications in diverse industries, including automotive, electronics, healthcare, and consumer goods. Sustainability Initiatives Environmental sustainability is a growing concern, and Chinese molded case parts manufacturers are actively addressing it. Many have adopted eco-friendly practices, such as recycling and waste reduction, to minimize their environmental impact. This commitment to sustainability aligns with global trends and positions them as responsible industry leaders. In conclusion, China’s molded case parts manufacturers have risen to prominence through a combination of cutting-edge technology, versatile material expertise, stringent quality control, and a commitment to cost-effective solutions. Their contributions to global supply chains and dedication to innovation ensure that they will continue to play a vital role in manufacturing for years to come. As the industry evolves, Chinese manufacturers are well-prepared to lead the way in shaping its future. Title: “Empowering Electrical Safety: China’s Leading Universal Circuit Breaker OEM Manufacturers” China has positioned itself as a global hub for manufacturing, and its prowess extends to the production of universal circuit breakers. China’s Universal Circuit Breaker Original Equipment Manufacturers (OEMs) have earned a reputation for their commitment to quality, innovation, and cost-effectiveness. In this article, we will delve into the world of China’s Universal Circuit Breaker OEM manufacturers, their journey to prominence, and the key factors that drive their success. A Legacy of Excellence China’s ascent to becoming a premier Universal Circuit Breaker OEM manufacturer reflects a steadfast commitment to quality and precision. Over the years, Chinese OEMs have invested significantly in research, technology, and workforce development, positioning themselves at the forefront of this specialized industry. Cutting-Edge Technology Chinese Universal Circuit Breaker OEM manufacturers employ state-of-the-art technology to maintain their competitive edge. Advanced electrical testing equipment, computer-aided design (CAD) software, and robotic automation are just some of the technologies they utilize to produce efficient and reliable circuit breakers. This technological prowess ensures that the circuit breakers meet rigorous safety and performance standards. Versatility in Product Range One of the key strengths of Chinese manufacturers is their ability to offer a wide range of circuit breakers tailored to diverse requirements. Whether it’s miniature circuit breakers (MCBs), molded case circuit breakers (MCCBs), or residual current circuit breakers (RCCBs), these manufacturers can produce circuit breakers designed to handle various electrical systems and voltages. Global Supply Chain Integration China’s strategic geographical location has made it a focal point for global supply chain integration. Universal Circuit Breaker OEM manufacturers in China benefit from easy access to raw materials, cost-effective transportation, and efficient logistics networks, enabling them to efficiently serve international clients. Stringent Quality Control Quality control is paramount in the circuit breaker industry, and Chinese OEMs adhere to rigorous quality standards. They employ advanced quality control processes, including comprehensive electrical testing and inspection, to ensure that each circuit breaker meets or exceeds industry specifications. This unwavering commitment to quality has earned them the trust of customers worldwide. Competitive Pricing Competitive pricing has been a significant driver of China’s success in the Universal Circuit Breaker OEM manufacturing sector. Chinese manufacturers can provide cost-effective solutions without compromising on quality, making them an attractive choice for businesses looking to optimize their electrical systems while managing costs. Skilled Workforce China’s skilled workforce is a valuable asset in the circuit breaker industry. Highly trained engineers, electrical experts, and technicians contribute their expertise to the design and production of reliable circuit breakers. Continuous training and development programs ensure that the workforce stays up-to-date with industry advancements. Global Impact Chinese Universal Circuit Breaker OEM manufacturers have expanded their reach far beyond China’s borders. They have forged partnerships and collaborations with international clients, becoming an integral part of global electrical systems. Their circuit breakers are utilized in a wide range of industries, including residential, commercial, industrial, and renewable energy applications. Sustainability Initiatives Environmental sustainability is a growing concern, and Chinese Universal Circuit Breaker OEM manufacturers are actively addressing it. Many have adopted eco-friendly practices, such as designing energy-efficient circuit breakers and promoting recycling and waste reduction, to minimize their environmental footprint. This commitment to sustainability aligns with global trends and positions them as responsible industry leaders. In conclusion, China’s Universal Circuit Breaker OEM manufacturers have risen to prominence through a combination of cutting-edge technology, product versatility, stringent quality control, and cost-effective solutions. Their contributions to global electrical safety and dedication to innovation ensure that they will continue to be pivotal players in the industry for years to come. As the world embraces advancements in electrical systems, Chinese manufacturers are well-equipped to lead the way in shaping a safer and more efficient future. Title: “Powering Safety: China’s Leading DC Molded Case Circuit Breaker OEM Manufacturers” In the realm of electrical safety and power distribution, China has established itself as a global hub for innovation and manufacturing. Specifically, China’s DC Molded Case Circuit Breaker Original Equipment Manufacturers (OEMs) have earned a reputation for their unwavering commitment to quality, technological prowess, and cost-effective solutions. In this article, we will delve into the world of China’s DC Molded Case Circuit Breaker OEM manufacturers, their journey to prominence, and the key factors fueling their success. A Legacy of Excellence China’s ascent to becoming a premier DC Molded Case Circuit Breaker OEM manufacturer is marked by its dedication to precision and safety. Over the years, Chinese OEMs have invested significantly in research, technology, and workforce development, positioning themselves as leaders in this specialized industry. Cutting-Edge Technology Chinese DC Molded Case Circuit Breaker OEM manufacturers leverage state-of-the-art technology to maintain their competitive edge. Advanced electrical testing equipment, computer-aided design (CAD) software, and robotic automation are just some of the technologies they employ to produce efficient and reliable DC molded case circuit breakers. This technological prowess ensures that their circuit breakers meet the most rigorous safety and performance standards. Versatility in Product Range One of the key strengths of Chinese manufacturers is their ability to offer a diverse range of DC molded case circuit breakers tailored to meet a wide array of requirements. Whether it’s low-voltage, medium-voltage, or high-voltage DC circuit breakers, these manufacturers can produce circuit breakers designed to handle various electrical systems and voltages, catering to an array of applications. Global Supply Chain Integration China’s strategic geographical location has made it a focal point for global supply chain integration. DC Molded Case Circuit Breaker OEM manufacturers in China benefit from easy access to raw materials, cost-effective transportation, and efficient logistics networks, enabling them to efficiently serve international clients. Stringent Quality Control Quality control is paramount in the circuit breaker industry, and Chinese OEMs adhere to rigorous quality standards. They employ advanced quality control processes, including comprehensive electrical testing and inspection, to ensure that each DC molded case circuit breaker meets or exceeds industry specifications. This unwavering commitment to quality has earned them the trust of customers worldwide. Competitive Pricing Competitive pricing has been a significant driver of China’s success in the DC Molded Case Circuit Breaker OEM manufacturing sector. Chinese manufacturers can provide cost-effective solutions without compromising on quality, making them an attractive choice for businesses looking to enhance electrical safety while managing costs. Skilled Workforce China’s skilled workforce is a valuable asset in the circuit breaker industry. Highly trained engineers, electrical experts, and technicians contribute their expertise to the design and production of reliable DC molded case circuit breakers. Continuous training and development programs ensure that the workforce remains at the forefront of industry advancements. Global Impact Chinese DC Molded Case Circuit Breaker OEM manufacturers have expanded their reach far beyond China’s borders. They have forged partnerships and collaborations with international clients, becoming an integral part of global electrical systems. Their circuit breakers are utilized in diverse industries, including renewable energy, telecommunications, data centers, and industrial automation. Sustainability Initiatives Environmental sustainability is a growing concern, and Chinese DC Molded Case Circuit Breaker OEM manufacturers are actively addressing it. Many have adopted eco-friendly practices, such as designing energy-efficient circuit breakers and promoting recycling and waste reduction, to minimize their environmental footprint. This commitment to sustainability aligns with global trends and positions them as responsible industry leaders. In conclusion, China’s DC Molded Case Circuit Breaker OEM manufacturers have risen to prominence through a combination of cutting-edge technology, product versatility, stringent quality control, and cost-effective solutions. Their contributions to global electrical safety and dedication to innovation ensure that they will continue to be pivotal players in the industry for years to come. As the world embraces advancements in electrical systems, Chinese manufacturers are well-equipped to lead the way in powering a safer and more efficient future. Title: “Empowering Electrical Control: China’s Leading Frame Circuit Breaker Fixed Switch Manufacturers” China’s reputation as a global manufacturing powerhouse extends to the production of frame circuit breaker fixed switches. Chinese manufacturers in this field have earned recognition for their unwavering commitment to quality, innovative solutions, and cost-effective offerings. In this article, we will explore the world of China’s frame circuit breaker fixed switch manufacturers, their journey to prominence, and the key factors contributing to their success. A Legacy of Excellence China’s rise to becoming a premier frame circuit breaker fixed switch manufacturer is characterized by an unwavering dedication to precision and safety. Over the years, Chinese manufacturers have invested substantially in research, technology, and workforce development, positioning themselves at the forefront of this specialized industry. Cutting-Edge Technology Chinese frame circuit breaker fixed switch manufacturers leverage state-of-the-art technology to maintain their competitive edge. Advanced equipment for metal forming, precision machining, and assembly automation are just a few examples of the technologies they utilize to produce efficient and reliable fixed switches. This technological prowess ensures that their products meet rigorous safety and performance standards. Versatility in Product Range One of the key strengths of Chinese manufacturers is their ability to offer a diverse range of fixed switches tailored to meet a wide array of electrical control system requirements. Whether it’s low-voltage or high-voltage applications, these manufacturers can produce fixed switches designed to handle various electrical systems and voltages, catering to a wide range of applications. Global Supply Chain Integration China’s strategic geographical location has made it a hub for global supply chain integration. Frame circuit breaker fixed switch manufacturers in China benefit from easy access to raw materials, cost-effective transportation, and efficient logistics networks, enabling them to efficiently serve international clients. Stringent Quality Control Quality control is paramount in the electrical control industry, and Chinese manufacturers adhere to rigorous quality standards. They employ advanced quality control processes, including comprehensive testing and inspection, to ensure that each fixed switch meets or exceeds industry specifications. This unwavering commitment to quality has earned them the trust of customers worldwide. Competitive Pricing Competitive pricing has been a significant driver of China’s success in the frame circuit breaker fixed switch manufacturing sector. Chinese manufacturers can provide cost-effective solutions without compromising on quality, making them an attractive choice for businesses looking to enhance electrical control systems while managing costs. Skilled Workforce China’s skilled workforce is a valuable asset in the electrical control industry. Highly trained engineers, electrical experts, and technicians contribute their expertise to the design and production of reliable fixed switches. Continuous training and development programs ensure that the workforce remains at the forefront of industry advancements. Global Impact Chinese frame circuit breaker fixed switch manufacturers have expanded their reach far beyond China’s borders. They have established partnerships and collaborations with international clients, becoming integral components of global electrical control systems. Their fixed switches are used in diverse industries, including power distribution, industrial automation, and building infrastructure. Sustainability Initiatives Environmental sustainability is a growing concern, and Chinese frame circuit breaker fixed switch manufacturers are actively addressing it. Many have adopted eco-friendly practices, such as designing energy-efficient switches and promoting recycling and waste reduction, to minimize their environmental footprint. This commitment to sustainability aligns with global trends and positions them as responsible industry leaders. In conclusion, China’s frame circuit breaker fixed switch manufacturers have risen to prominence through a combination of cutting-edge technology, product versatility, stringent quality control, and cost-effective solutions. Their contributions to global electrical control systems and dedication to innovation ensure that they will continue to be pivotal players in the industry for years to come. As the world embraces advancements in electrical control, Chinese manufacturers are well-equipped to lead the way in powering a safer, more efficient, and sustainable future. Title: “Pioneering Electrical Safety: Leading the Way in DC Molded Case Circuit Breaker Manufacturing” In the realm of electrical safety and power distribution, the manufacture of DC molded case circuit breakers holds immense significance. Manufacturers in this specialized field, particularly in China, have gained recognition for their unwavering commitment to quality, innovative solutions, and cost-effective offerings. This article delves into the world of DC molded case circuit breaker manufacturers, focusing on their journey to prominence and the key factors contributing to their success. A Legacy of Excellence The journey of becoming a premier manufacturer of DC molded case circuit breakers is marked by an unwavering dedication to precision and safety. Over the years, Chinese manufacturers, in particular, have invested significantly in research, technology, and workforce development, positioning themselves as leaders in this specialized industry. Cutting-Edge Technology Manufacturers of DC molded case circuit breakers harness state-of-the-art technology to maintain their competitive edge. They employ advanced equipment for precise metal forming, precision machining, and automated assembly. These technologies ensure the production of efficient and reliable circuit breakers that adhere to stringent safety and performance standards. Versatility in Product Range One of the key strengths of these manufacturers is their ability to offer a diverse range of DC molded case circuit breakers tailored to meet various electrical system requirements. Whether it’s low-voltage, medium-voltage, or high-voltage applications, these manufacturers can produce circuit breakers designed to handle a wide range of electrical systems and voltages, serving a multitude of applications. Global Supply Chain Integration China’s strategic geographical location has made it a central hub for global supply chain integration. Manufacturers of DC molded case circuit breakers in China benefit from easy access to raw materials, cost-effective transportation, and efficient logistics networks, enabling them to efficiently serve international clients. Stringent Quality Control Quality control is paramount in the electrical safety industry, and manufacturers adhere to rigorous quality standards. They employ advanced quality control processes, including comprehensive testing and inspection, to ensure that each circuit breaker not only meets but often exceeds industry specifications. This unwavering commitment to quality has earned them the trust of customers worldwide. Competitive Pricing Competitive pricing has been a significant driver of success for manufacturers of DC molded case circuit breakers. They offer cost-effective solutions without compromising on quality, making them an attractive choice for businesses seeking to enhance electrical safety while managing costs effectively. Skilled Workforce China’s skilled workforce is a valuable asset in the electrical safety industry. Highly trained engineers, electrical experts, and technicians contribute their expertise to the design and production of reliable circuit breakers. Continuous training and development programs ensure that the workforce remains at the forefront of industry advancements. Global Impact Manufacturers of DC molded case circuit breakers have expanded their reach far beyond China’s borders. They have established partnerships and collaborations with international clients, becoming integral components of global electrical safety systems. Their circuit breakers are used in diverse industries, including power distribution, renewable energy, industrial automation, and building infrastructure. Sustainability Initiatives Environmental sustainability is a growing concern, and manufacturers of DC molded case circuit breakers are actively addressing it. Many have adopted eco-friendly practices, such as designing energy-efficient circuit breakers and promoting recycling and waste reduction, to minimize their environmental footprint. This commitment to sustainability aligns with global trends and positions them as responsible industry leaders. In conclusion, manufacturers of DC molded case circuit breakers have risen to prominence through a combination of cutting-edge technology, product versatility, stringent quality control, and cost-effective solutions. Their contributions to global electrical safety and dedication to innovation ensure that they will continue to be pivotal players in the industry for years to come. As the world embraces advancements in electrical safety, these manufacturers are well-prepared to lead the way in pioneering a safer, more efficient, and sustainable future. Title: “Crafting Precision: Exploring the World of Metal Stamping Die Manufacturers” Metal stamping die manufacturing is a pivotal industry with a profound impact on various sectors, including automotive, aerospace, electronics, and more. Within this realm, metal stamping die manufacturers play a crucial role in transforming raw materials into precision-engineered components. In this article, we will delve into the world of metal stamping die manufacturers, exploring their processes, significance, and the key factors driving their success. The Art of Metal Stamping Die Manufacturing Metal stamping die manufacturing is a process that involves the creation of tools, called dies, which are used to cut, shape, and form metal sheets into specific components. These components are crucial components of many products we use daily, from automobile parts to household appliances. The process begins with the design and engineering of the stamping die, taking into consideration the final product’s specifications. Once the die design is complete, skilled tool and die makers use computer-aided design (CAD) software and precision machinery to create the physical die. Precision and Accuracy The hallmark of metal stamping die manufacturing is precision and accuracy. These dies are crafted with meticulous attention to detail, ensuring that each component produced is consistent and meets stringent quality standards. The precise nature of this process makes it ideal for industries where tight tolerances and exact specifications are critical. Versatility in Material Expertise Metal stamping die manufacturers are known for their expertise in working with a wide range of materials. Whether it’s steel, aluminum, copper, or exotic alloys, these manufacturers have the capability to create stamping dies tailored to the specific material properties, ensuring optimal performance and longevity. Diverse Applications Metal stamping die manufacturers serve a wide range of industries, each with its unique requirements. Some common applications include automotive parts like fenders and engine components, aerospace components such as brackets and panels, and electronic connectors used in devices and appliances. Technological Advancements Advancements in technology have significantly impacted the metal stamping die manufacturing process. Computer Numerical Control (CNC) machining, high-speed milling, and sophisticated simulation software have enhanced precision, efficiency, and speed in die production. These technological advancements allow manufacturers to produce complex and intricate designs with ease. Quality Assurance Quality control is paramount in metal stamping die manufacturing. Manufacturers employ rigorous quality control processes, including meticulous inspection and testing, to ensure that every die meets or exceeds industry standards. This commitment to quality not only guarantees the reliability of the components produced but also ensures the safety of end-users. Cost-Effective Production Metal stamping die manufacturing is known for its cost-effectiveness, particularly for large production runs. The process offers rapid cycle times and minimal material waste, making it an attractive choice for businesses looking to optimize their production costs while maintaining quality. Customization and Design Freedom One of the advantages of metal stamping die manufacturing is the ability to customize dies to create complex shapes and intricate designs. This flexibility allows manufacturers to meet the specific requirements of diverse industries and products. Environmental Responsibility In an era of increased environmental consciousness, many metal stamping die manufacturers have adopted eco-friendly practices, such as recycling and waste reduction, to minimize their environmental footprint. This commitment to sustainability aligns with global trends and positions them as responsible industry leaders. In conclusion, metal stamping die manufacturers are the unsung heroes behind the precision and quality of countless products we rely on daily. Their dedication to precision, versatility in material expertise, and commitment to innovation ensure that they continue to play a vital role in modern manufacturing. As technology advances and materials evolve, metal stamping die manufacturers will remain at the forefront, shaping the future of various industries through their craft.
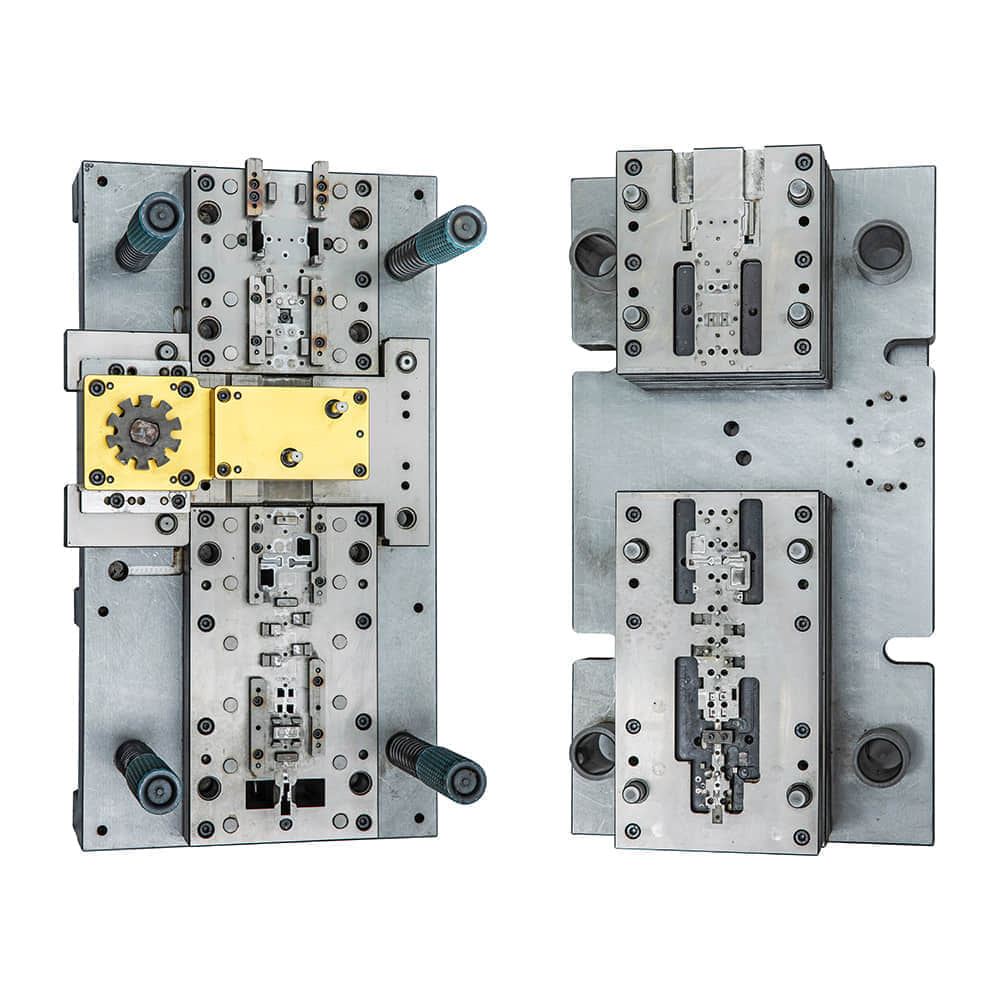