In the realm of manufacturing, injection molding plays a pivotal role in the production of countless everyday items, from intricate electronic components to household appliances and automotive parts. Behind the scenes of this essential process stands the injection mold manufacturer, a key player in the world of manufacturing. In this article, we will delve into the world of injection mold manufacturers, exploring their critical role, the innovation they bring to the table, and the unwavering commitment to quality that defines their work.
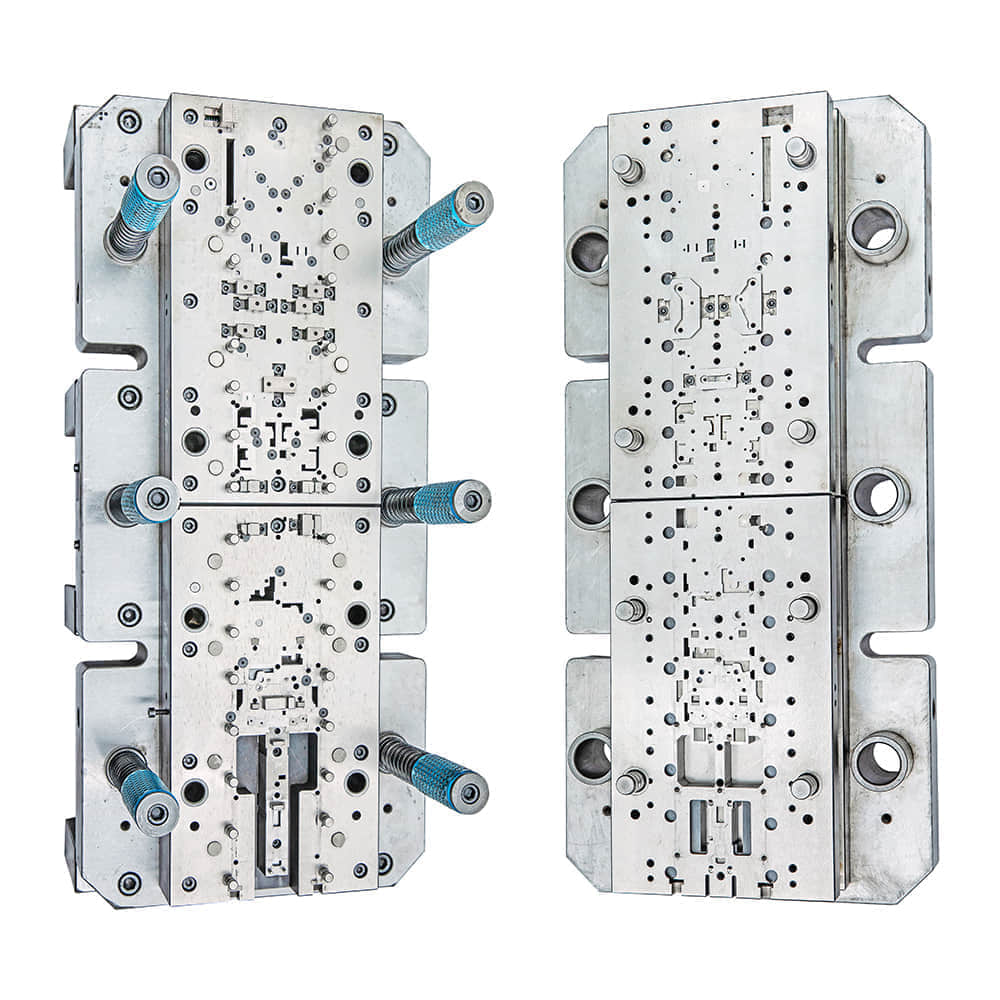
The Crucial Role of Injection Mold Manufacturers
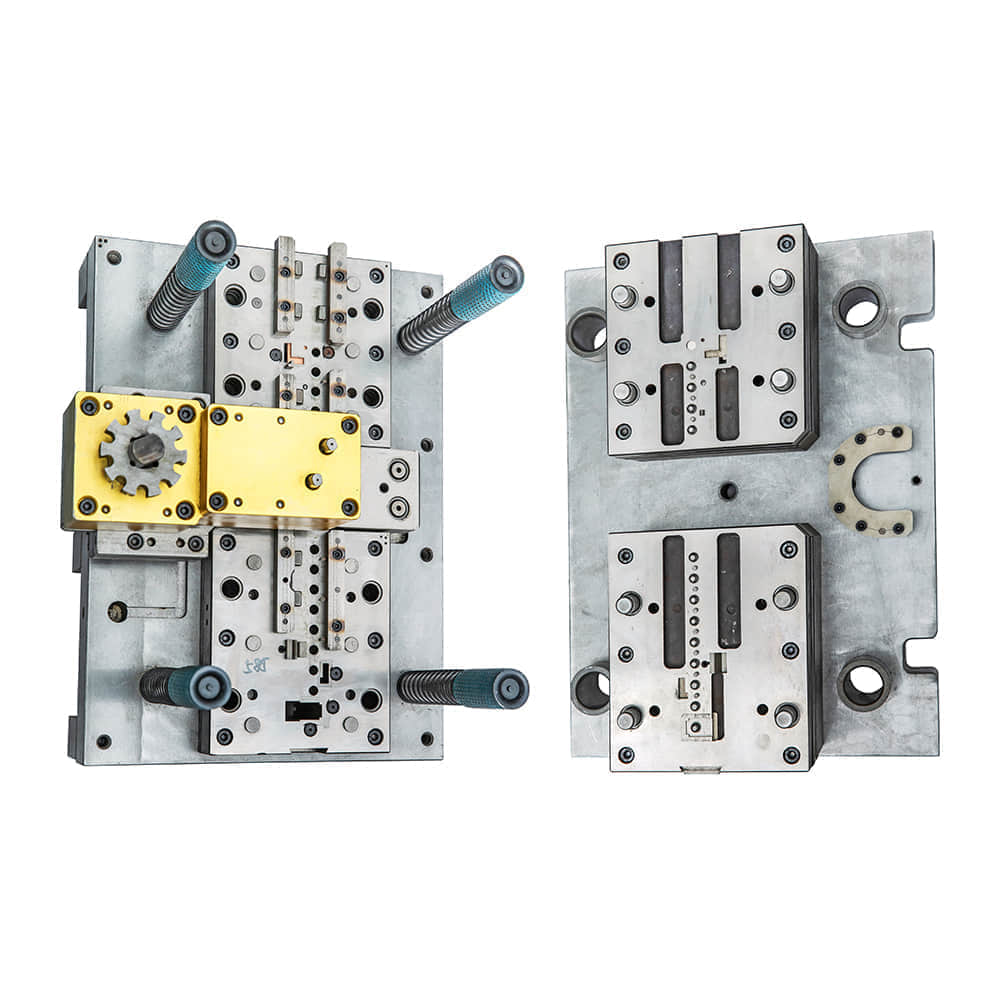
Injection mold manufacturers are the masterminds behind the molds that shape plastics and other materials into various products. These molds are the heart of the injection molding process, determining the quality, precision, and efficiency of production. The significance of injection mold manufacturers cannot be overstated, as they serve as the foundation upon which entire industries rely. Precision Engineering at Its Best One of the hallmarks of injection mold manufacturers is their dedication to precision engineering. The molds they create must meet exacting standards to produce parts that fit seamlessly together in final products. Achieving such precision requires cutting-edge technology, vast expertise, and an acute attention to detail. In modern manufacturing, computer-aided design (CAD) and computer-aided manufacturing (CAM) software play pivotal roles in mold design and production. These tools enable injection mold manufacturers to create intricate designs with micron-level accuracy. From tiny medical device components to large automotive parts, these manufacturers can customize molds to meet the unique requirements of their clients. Innovation in Material and Design Injection mold manufacturers are at the forefront of innovation in materials and design. They constantly explore new materials that offer enhanced performance, durability, and sustainability. Biodegradable plastics, high-strength composites, and specialized polymers are just a few examples of materials that have revolutionized the manufacturing industry. These innovations wouldn’t be possible without the expertise of injection mold manufacturers. Moreover, injection mold manufacturers are adept at developing molds for complex and innovative product designs. They collaborate closely with product designers and engineers to ensure that molds are optimized for the intended application. Whether it’s creating intricate patterns on consumer electronics or ensuring a watertight seal in plumbing components, injection mold manufacturers are indispensable partners in bringing creative ideas to life. Quality Assurance and Certifications Quality is the cornerstone of any successful manufacturing process, and injection mold manufacturers take this responsibility seriously. They adhere to rigorous quality assurance standards and certifications to ensure that every mold they produce meets or exceeds industry requirements. ISO 9001 certification, for instance, is a common benchmark for quality management systems in the manufacturing sector. Injection mold manufacturers with this certification demonstrate their commitment to consistently delivering products that meet customer expectations. Environmental Responsibility In recent years, environmental concerns have taken center stage in manufacturing. Injection mold manufacturers are actively involved in sustainable practices, aiming to minimize waste and reduce their carbon footprint. They explore eco-friendly materials, implement energy-efficient processes, and embrace recycling and waste reduction strategies. In conclusion, injection mold manufacturers are unsung heroes of the manufacturing world, playing a vital role in shaping the products that we use daily. Their dedication to precision, innovation, quality, and sustainability ensures that our world continues to progress technologically while minimizing its impact on the environment. As technology advances and new materials emerge, injection mold manufacturers will remain at the forefront of innovation, driving progress and shaping the future of manufacturing. 标题:Manufacturer of Molded Case Circuit Breaker: Power Distribution and Safety Assurance Introduction In the realm of electrical engineering and power distribution, molded case circuit breakers (MCCBs) stand as essential guardians of safety and efficiency. These devices play a crucial role in protecting electrical circuits from overloads and short circuits, ensuring the reliable operation of electrical systems. Behind the production of these vital components stands the manufacturer of molded case circuit breakers, a cornerstone of the electrical industry. In this article, we will delve into the world of MCCB manufacturers, exploring their pivotal role in power distribution, the technology they employ, and their unwavering commitment to safety and reliability. The Crucial Role of MCCB Manufacturers MCCBs are indispensable components in electrical systems. They serve as the first line of defense, interrupting the flow of electricity when abnormalities occur, such as excessive current or short circuits. This interruption prevents damage to equipment, electrical fires, and potential hazards to both people and property. MCCB manufacturers are the architects behind these protective devices. They design, engineer, and produce MCCBs that meet stringent quality and safety standards. These manufacturers are pivotal in ensuring the safety and reliability of electrical systems across industries, from residential buildings to industrial complexes. Advanced Technology and Engineering MCCB manufacturers are at the forefront of technological advancements in electrical engineering. They employ cutting-edge technology and advanced materials to create MCCBs that are not only highly efficient but also reliable under various conditions. One of the key advancements in MCCB technology is the use of electronic trip units. These units provide precise, adjustable protection settings and can communicate with control systems for real-time monitoring. This level of control allows for more tailored protection and enhances the overall efficiency of electrical systems. Additionally, MCCB manufacturers continuously explore materials that enhance the performance and durability of their products. Advanced arc extinguishing materials, high-quality conductive components, and robust insulating materials all contribute to the reliability and safety of MCCBs. Customization for Diverse Applications MCCB manufacturers understand that one size does not fit all in the world of electrical systems. They offer a wide range of MCCBs with varying specifications to accommodate different applications. From small residential panels to large industrial switchboards, MCCBs come in various sizes, current ratings, and trip characteristics to meet the specific needs of each installation. Furthermore, MCCB manufacturers work closely with electrical engineers and contractors to customize MCCBs for specialized applications. This collaborative approach ensures that MCCBs are precisely tailored to the demands of diverse industries, such as oil and gas, manufacturing, and renewable energy. Safety Compliance and Certification Safety is paramount when it comes to electrical components. MCCB manufacturers adhere to rigorous safety standards and certifications to guarantee the reliability of their products. Certifications like UL (Underwriters Laboratories) and IEC (International Electrotechnical Commission) provide assurance that MCCBs have undergone extensive testing and meet the highest safety and performance criteria. By consistently adhering to these standards, MCCB manufacturers ensure that their products can be trusted in critical applications where safety is paramount. Environmental Responsibility In today’s world, environmental responsibility is a growing concern. MCCB manufacturers are taking steps to reduce their environmental footprint by implementing sustainable practices in their production processes. This includes reducing waste, conserving energy, and exploring eco-friendly materials. In conclusion, the manufacturer of molded case circuit breakers plays an indispensable role in ensuring the safety, reliability, and efficiency of electrical systems worldwide. Their commitment to advanced technology, customization, safety compliance, and environmental responsibility makes them key players in the ever-evolving field of electrical engineering. As technology continues to advance and energy systems become more complex, MCCB manufacturers will remain at the forefront, safeguarding the future of power distribution. 标题:Metal Stamping Die Manufacturers: Shaping the Future of Precision Engineering Introduction In the world of precision engineering and manufacturing, metal stamping dies are unsung heroes that give shape to countless products we encounter daily. These intricate tools are the result of the expertise and craftsmanship of metal stamping die manufacturers. In this article, we will explore the pivotal role these manufacturers play in shaping the world of manufacturing, their dedication to precision, and their commitment to innovation and quality. The Essence of Metal Stamping Die Manufacturers Metal stamping dies are specialized tools used to shape metal sheets into precise forms and patterns. These dies are used in a wide range of industries, from automotive and aerospace to consumer electronics and appliances. Metal stamping die manufacturers are the architects behind these vital tools, combining engineering prowess with craftsmanship to create dies that enable mass production of complex metal parts. Precision Engineering at its Core Precision is the bedrock of metal stamping die manufacturing. These manufacturers must adhere to the tightest tolerances and exacting specifications to ensure that every stamped part is consistent and accurate. Achieving such precision requires cutting-edge technology, extensive experience, and meticulous attention to detail. Computer-aided design (CAD) and computer-aided manufacturing (CAM) software are fundamental tools used by metal stamping die manufacturers. These software programs enable them to create intricate die designs with micron-level accuracy. Whether it’s forming intricate automotive components or crafting delicate electronic parts, these manufacturers must achieve perfection in every detail. Innovation in Design and Materials Metal stamping die manufacturers are at the forefront of innovation in design and materials. They work hand-in-hand with product designers and engineers to optimize die designs for specific applications. This collaboration ensures that each die is tailored to meet the unique requirements of the products they will produce. Moreover, these manufacturers continuously explore new materials and technologies to enhance the performance of their dies. Advanced tool steels, coatings, and heat treatment processes are just a few examples of innovations that have improved the durability and longevity of metal stamping dies. Quality Assurance and Certifications Quality assurance is paramount in metal stamping die manufacturing. These manufacturers adhere to stringent quality control processes and often seek certifications to demonstrate their commitment to excellence. ISO 9001 certification, for instance, is a widely recognized benchmark for quality management systems in manufacturing. Manufacturers with this certification showcase their dedication to consistently delivering products that meet or exceed industry standards. Environmental Responsibility In recent years, environmental sustainability has become a central concern in manufacturing. Metal stamping die manufacturers are actively working to reduce their environmental impact by implementing sustainable practices. This includes recycling and waste reduction, energy-efficient manufacturing processes, and exploring eco-friendly materials. Conclusion Metal stamping die manufacturers are the cornerstone of precision engineering and manufacturing. Their dedication to precision, innovation, quality, and sustainability ensures that industries can rely on their expertise to produce the parts and products that drive progress and innovation across various sectors. As technology advances and new materials emerge, metal stamping die manufacturers will continue to play a pivotal role in shaping the future of precision engineering and manufacturing. Their commitment to excellence ensures that our world continues to benefit from the reliable and consistent production of complex metal parts.
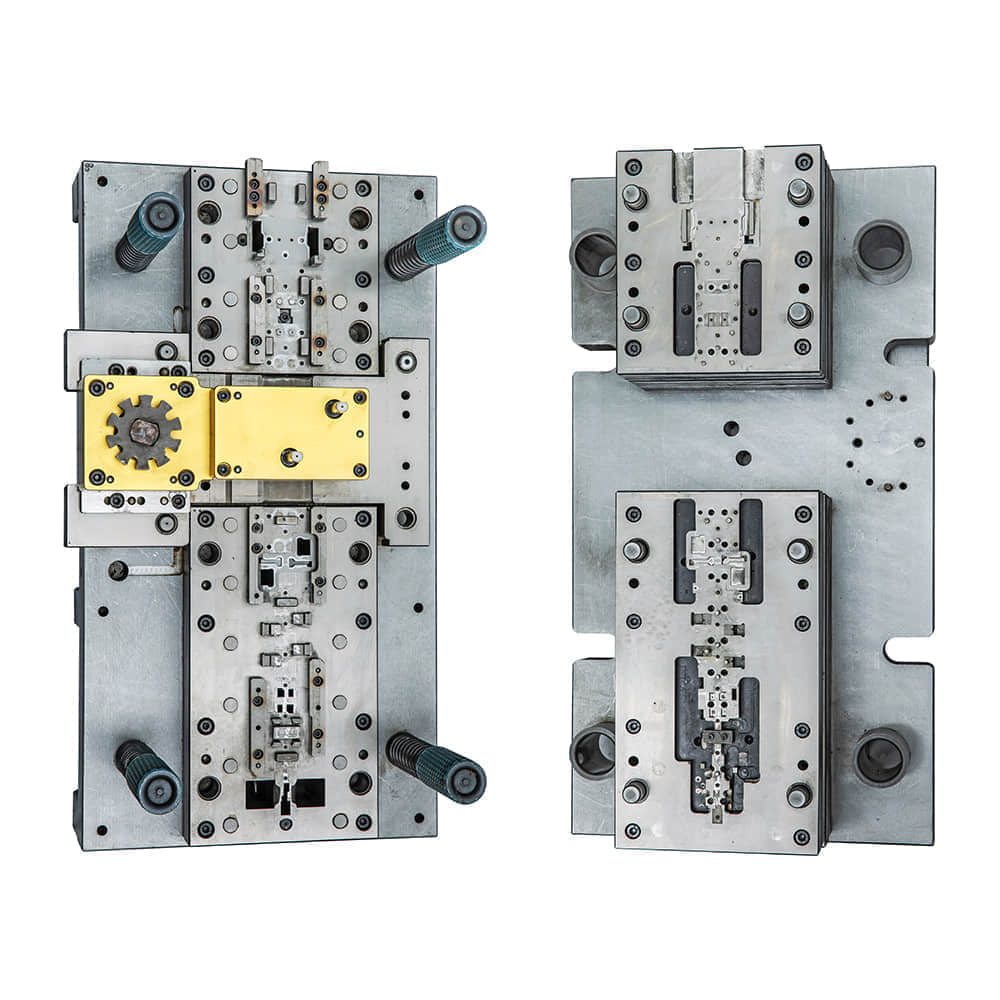