In the world of plastics manufacturing, Thermosetting Compression Moulding (TCM) stands out as a highly specialized and precise process. It involves the shaping of thermosetting plastics into desired forms through the combined application of heat and pressure. This article aims to delveeper into the working principles, applications, advantages, and challenges of Thermosetting Compression Moulding.
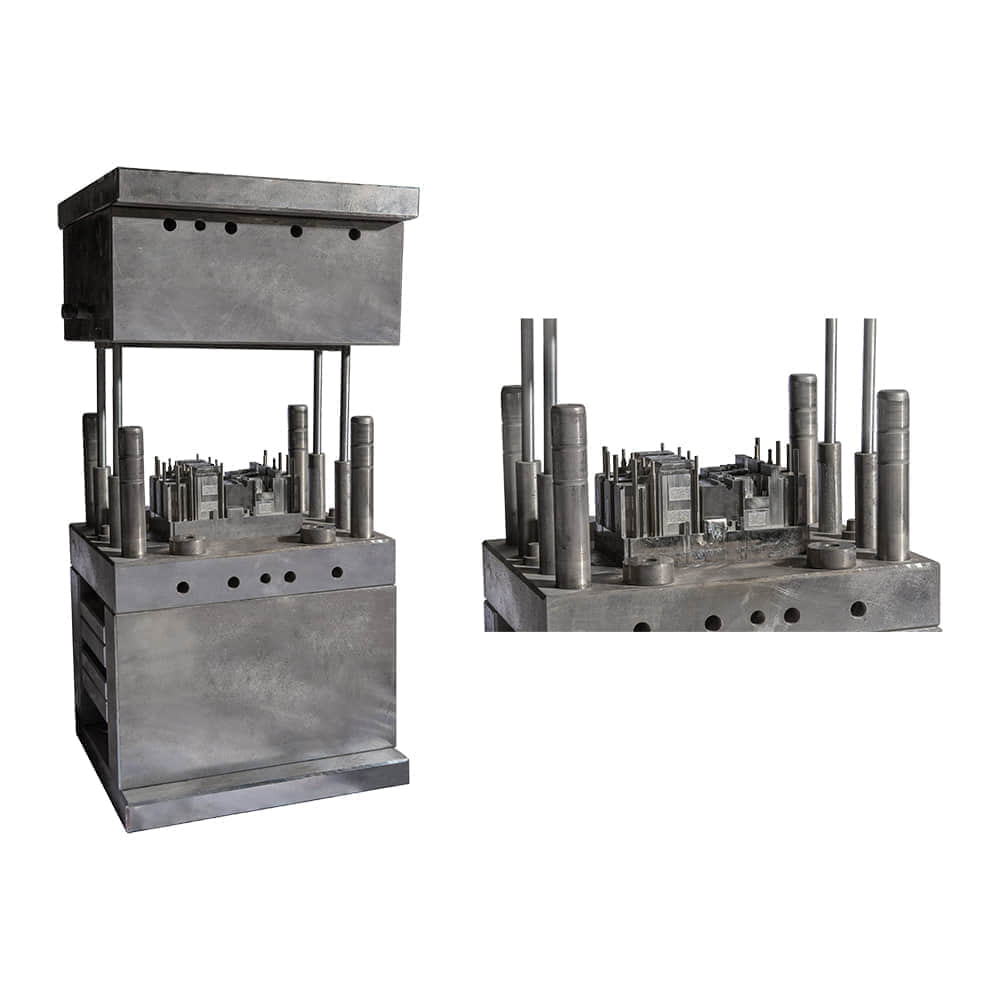
Working Principles of Thermosetting Compression Moulding
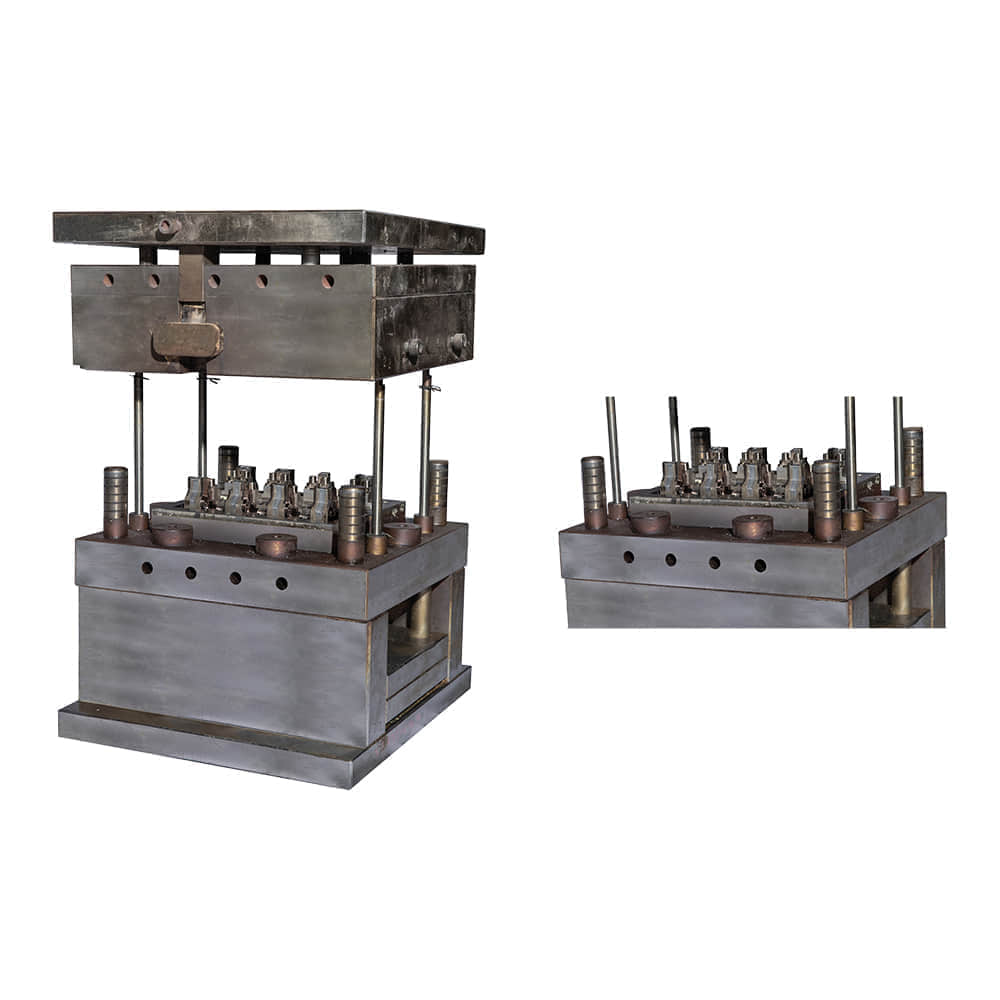
The process begins with the selection of a suitable mould, which is made from materials like steel or aluminum. The mould is designed to withstand the high temperatures and pressures required for the moulding process. The mould cavity is then coated with a release agent to ensure easy removal of the finished part once it has cooled. The next step involves loading the powdered or preformed thermosetting plastic material into the mould cavity. The mould is then closed, and heat is applied to initiate the curing process. This heat activation triggers a chemical reaction within the plastic, converting it from a soft, malleable state to a rigid, insoluble one.
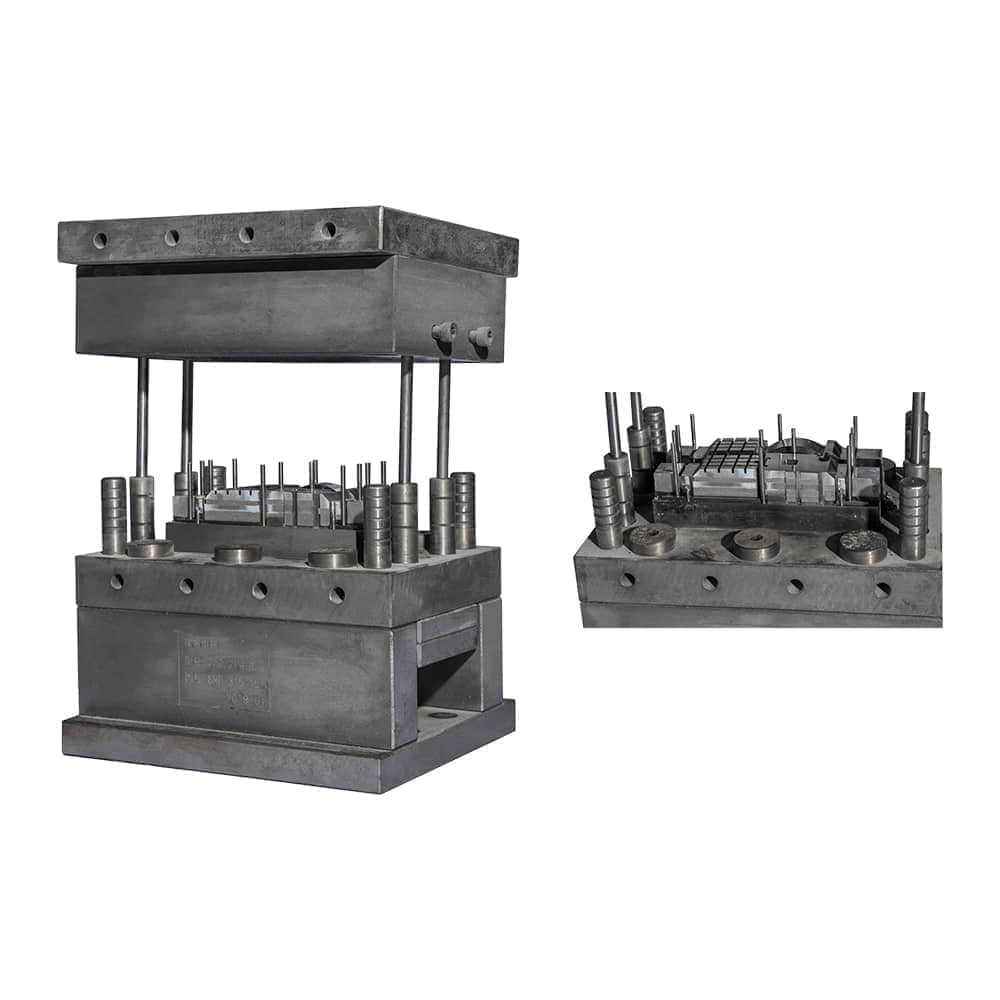