In the dynamic field of plastic manufacturing, Thermoplastic Injection Molds play a pivotal role. They are the sine qua non of mass production, precision, and durability in the manufacturing of plastic products.
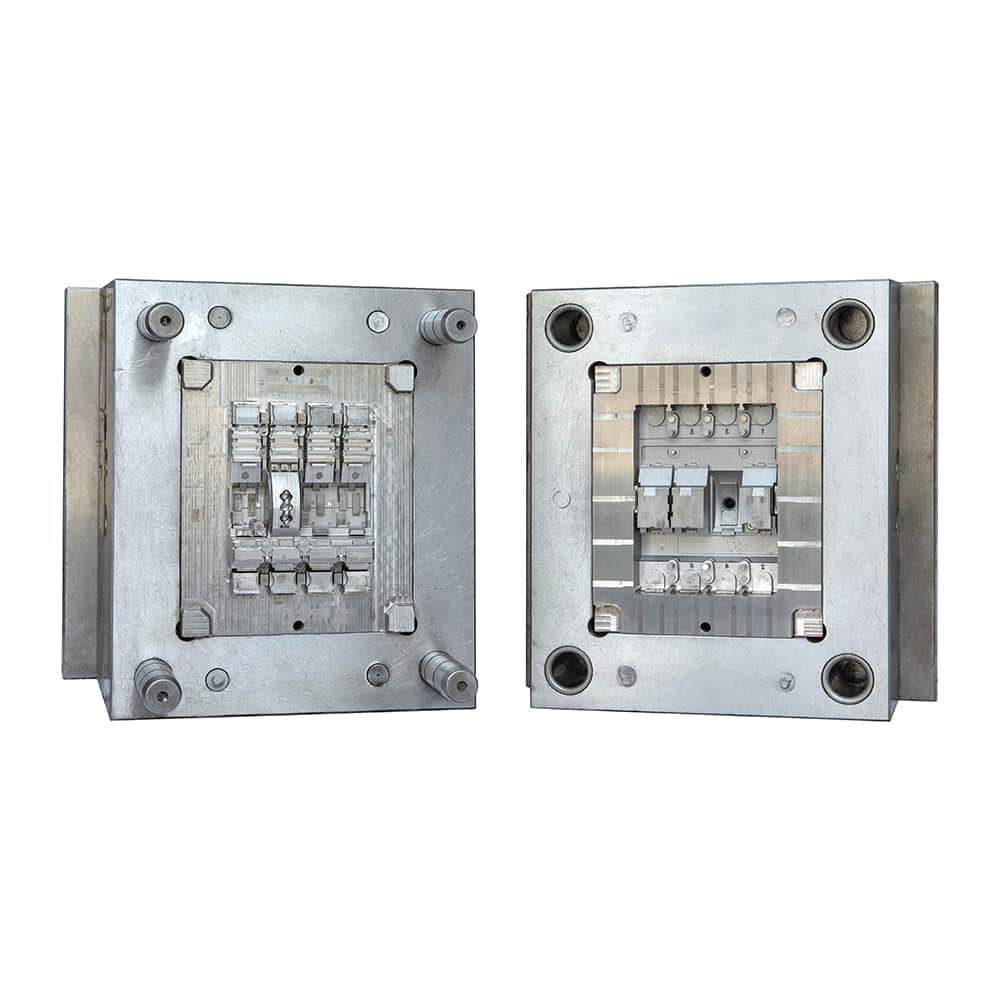
At the heart of the Thermoplastic Injection Molds lies its functionality. It is a tool that transforms molten plastic into desired shapes and sizes, reproducing them with remarkable precision. The process begins with the injection of molten thermoplastic into a cavity, which is formed by two halves of the mold: the fixed and the movable half. The movable half, also known as the ejector half, moves in to create the cavity, while the fixed half, also known as the receiver half, remains stationary. The molten plastic is then injected into this cavity under high pressure, filling it completely. As the plastic cools and solidifies, the movable half retracts, allowing the finished product to be ejected.
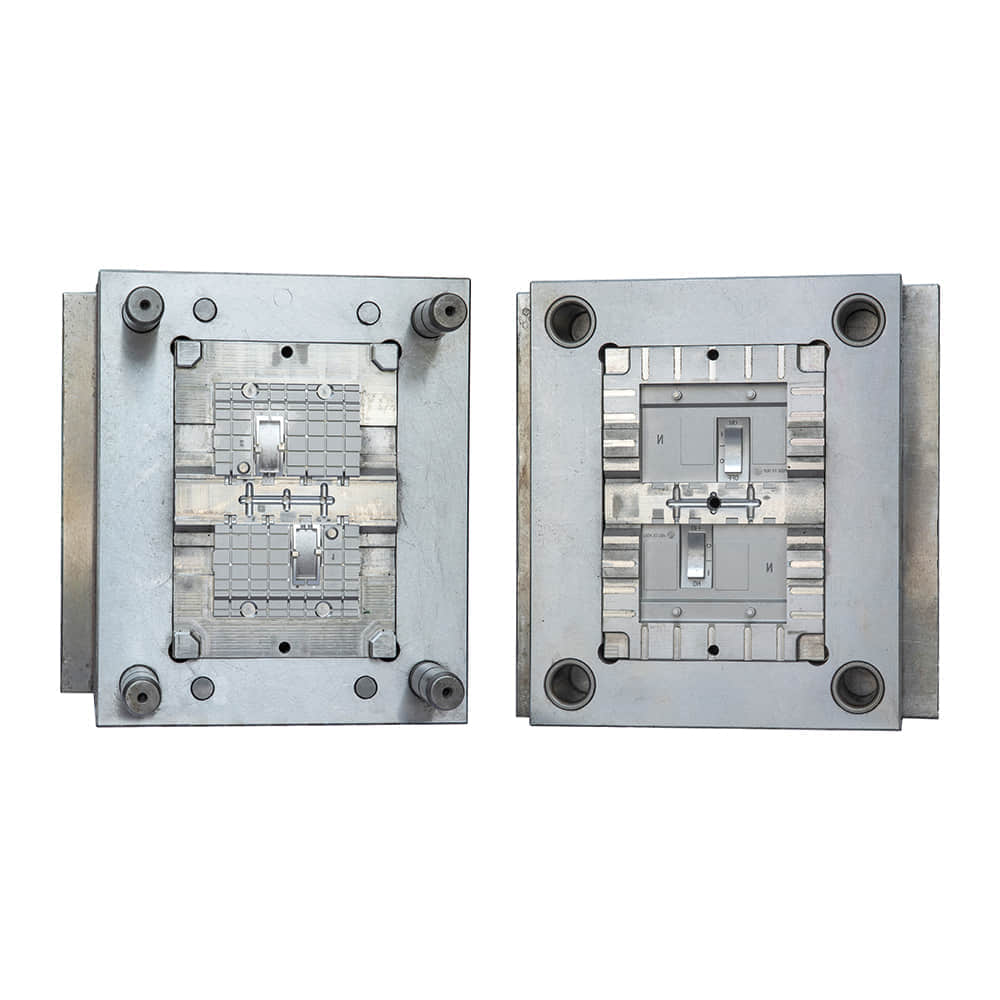
The design of these molds is complex and requires meticulous attention to detail. It must account for factors like the type of thermoplastic used, the desired shape and size of the product, as well as the specific manufacturing process. The mold must be strong enough to withstand the high injection pressures and temperatures, yet designed in a way that allows for efficient heat transfer for faster cooling and solidification. The materials used in the construction of Thermoplastic Injection Molds are also critical. They must be able to withstand high temperatures and pressures, yet remain dimensionally stable. Materials like steel, aluminum, and PEEK (Polyetheretherketone) are commonly used due to their high strength and resistance to wear and tear.
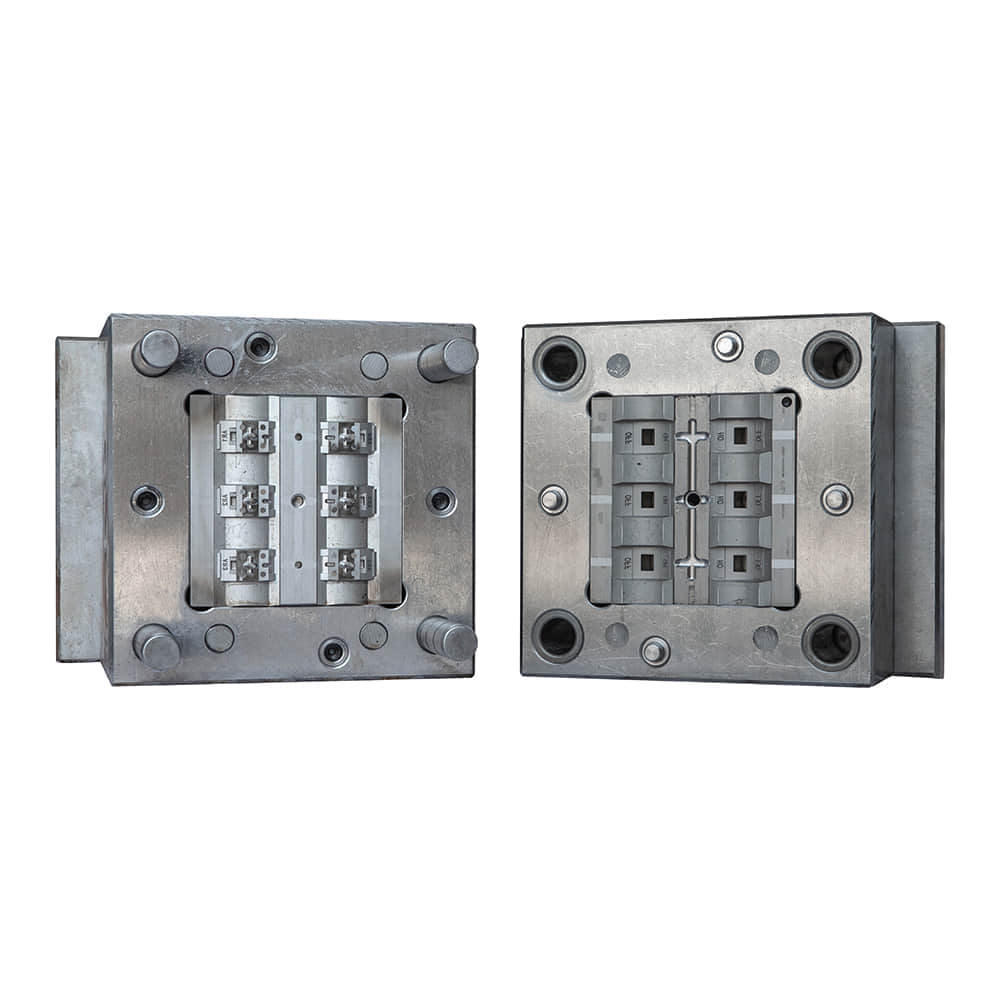