In the realm of plastic manufacturing, Thermoplastic Injection Molds occupy a pivotal position. These molds, as the core of the injection molding process, transform thermoplastic materials into a vast array of products, ranging from tiny components to large-scale parts. Understanding the intricacies of thermoplastic injection molds is crucial for anyone seeking to delve deeper into the plastics industry.
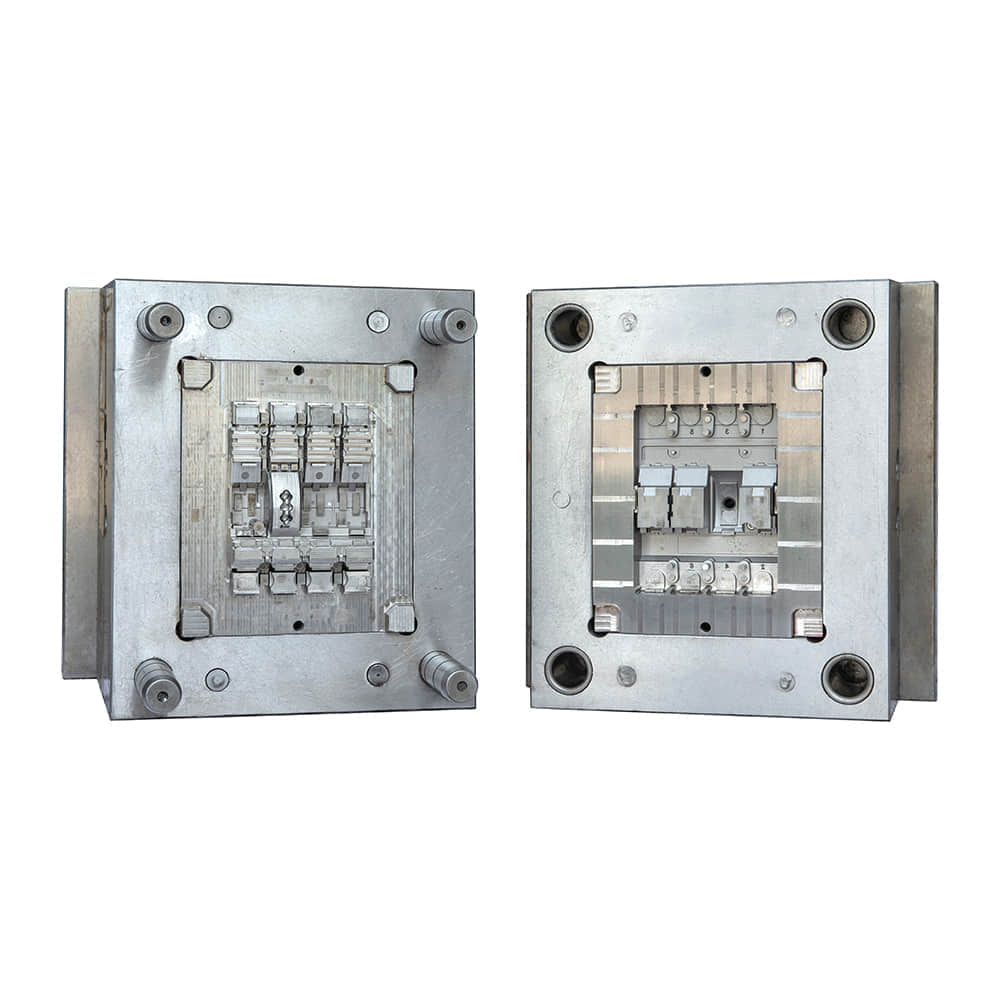
Thermoplastic Injection Molds are designed with precision and care, tailored to the specific needs of the product being manufactured. The mold’s design takes into account factors such as the plastic’s melting point, flow properties, and the desired shape and dimensions of the final product. The intricate channels and cavities within the mold ensure that the molten plastic flows evenly and fills the mold cavity completely, resulting in a smooth and uniform finish.
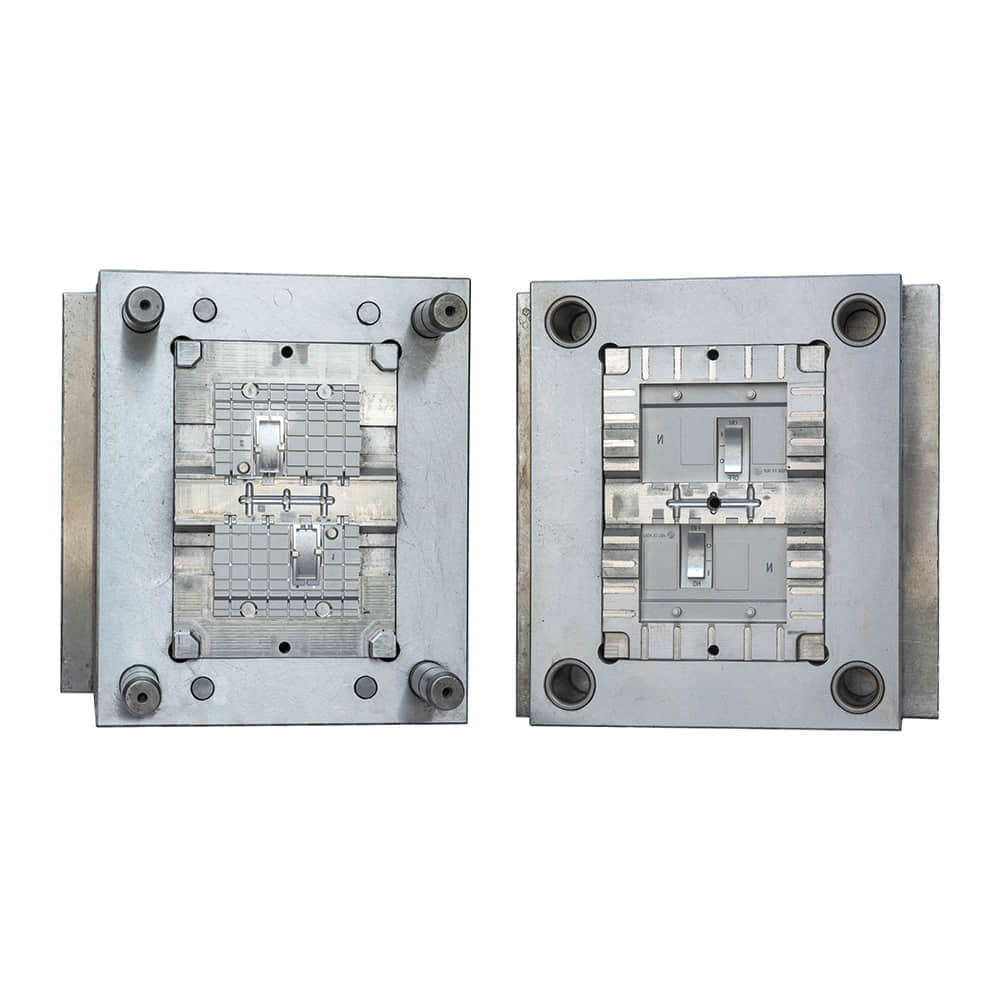
The injection molding process begins with the thermoplastic material being fed into the injection molding machine. The material is then heated to a molten state and forcibly injected into the mold cavity under high pressure. Once the plastic has cooled and solidified, the mold is opened, and the finished product is ejected. This entire process is highly automated, ensuring efficiency and consistency in production. The choice of thermoplastic material for injection molding is crucial. Different materials have varying properties such as strength, durability, flexibility, and heat resistance. The selection of the appropriate material depends on the specific application and requirements of the final product.
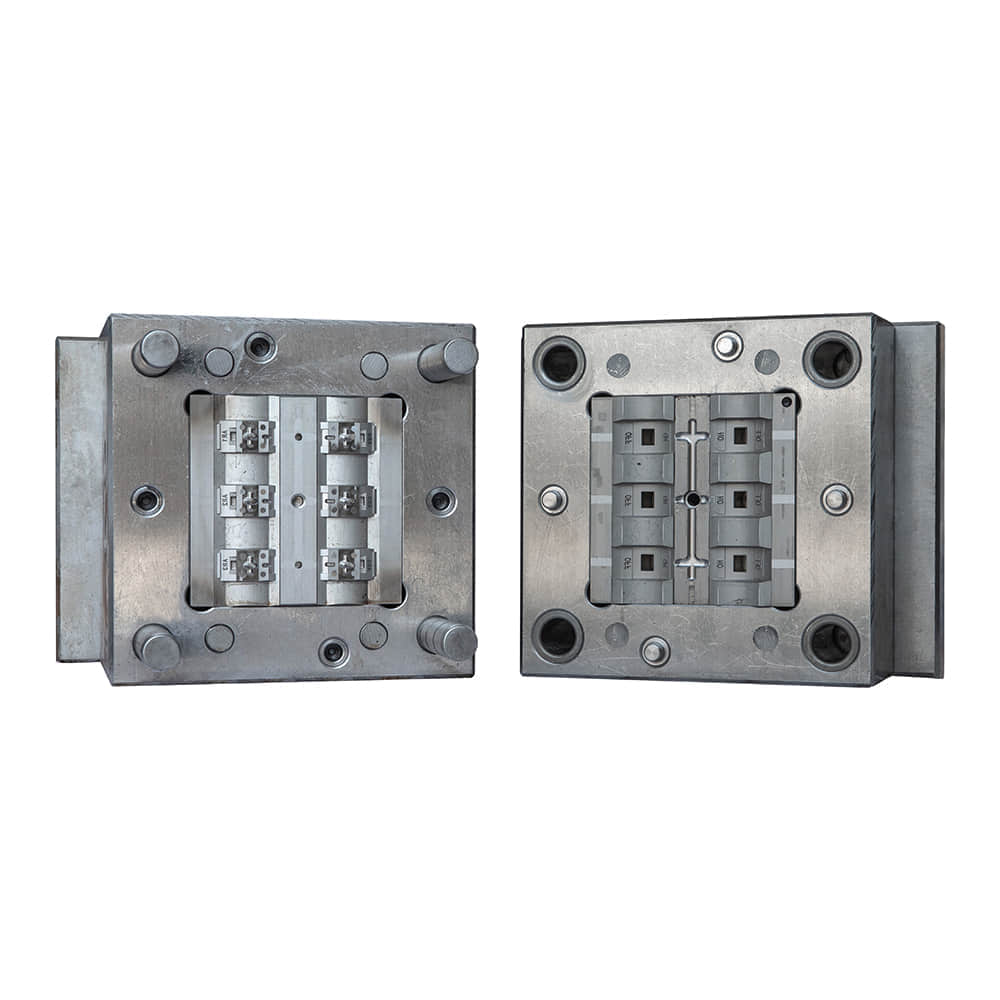