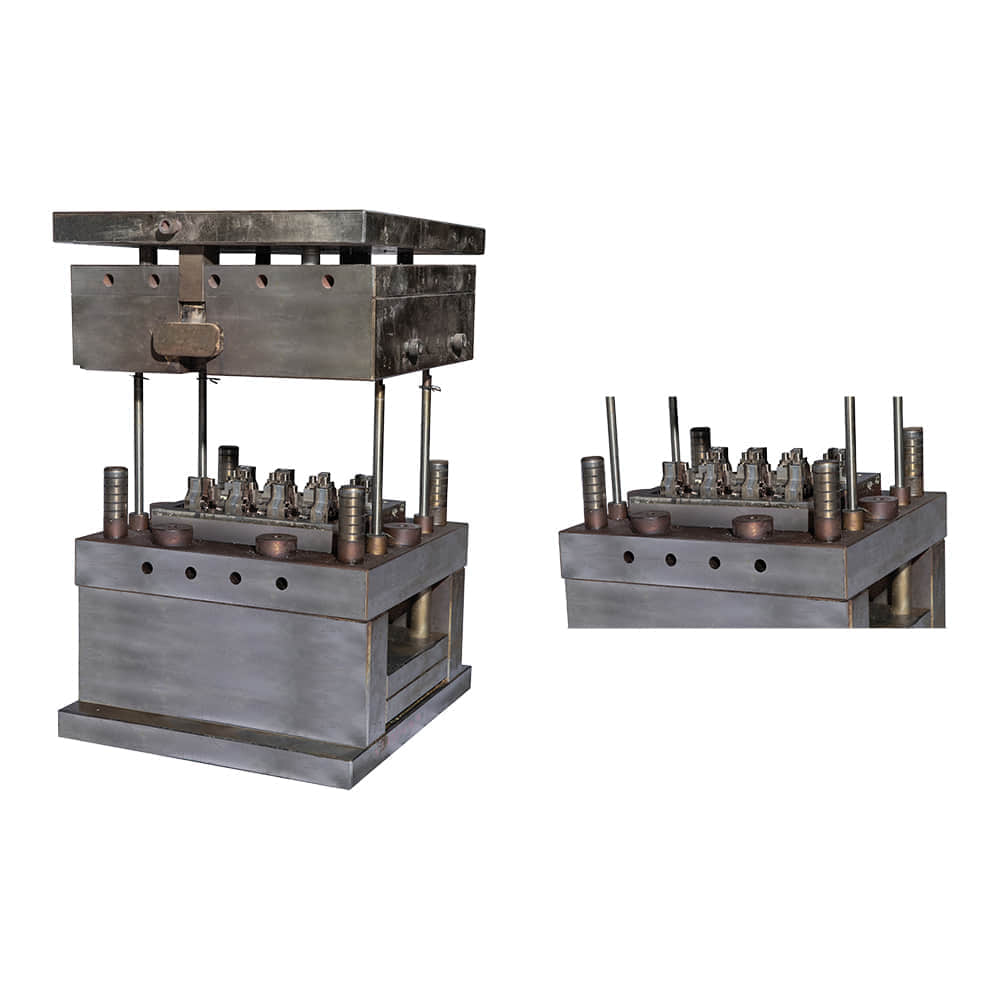
Introduction: MCCB (Molded Case Circuit Breaker) SMC (Sheet Molding Compound) parts play a crucial role in the electrical industry. These components ensure the safe and efficient operation of electrical systems. In this article, we will explore the technical aspects of MCCB SMC parts manufacturing and their significance in electrical applications.
MCCB SMC Parts Manufacturing Process: The production of MCCB SMC parts involves several intricate steps. Firstly, high-quality raw materials such as glass fibers, resin, and fillers are carefully selected. The materials are then mixed and compounded to form the SMC, a dough-like compound. This SMC is then molded into specific shapes using compression molding techniques.
During the compression molding process, the SMC is placed in a mold cavity and subjected to high pressure and temperature. This ensures the proper flow and distribution of the material, resulting in components with excellent strength and dimensional accuracy. The molded parts are then cured and cooled before further processing.
Key Factors in MCCB SMC Parts Manufacturing:
- Material Selection: The choice of materials greatly affects the performance and durability of MCCB SMC parts. The SMC should have good electrical insulation properties, mechanical strength, and resistance to heat and chemicals.
- Mold Design: The design of the mold plays a critical role in achieving the desired part geometry and surface finish. The mold should be precisely designed to accommodate shrinkage and ensure uniform filling of the SMC material.
- Compression Molding Parameters: Proper control of temperature, pressure, and time during the compression molding process is crucial. Optimal parameters ensure thorough curing of the SMC and prevent defects such as voids, warpage, or delamination.
Quality Control and Testing: To ensure the reliability and performance of MCCB SMC parts, rigorous quality control measures are implemented. Various tests are conducted, including dimensional inspection, electrical conductivity testing, thermal resistance analysis, and mechanical strength assessments. These tests verify compliance with industry standards and customer requirements.
Significance in Electrical Applications: MCCB SMC parts find wide application in electrical distribution systems, industrial machinery, and power generation equipment. They provide reliable protection against overcurrent and short circuits, preventing electrical accidents and damage to valuable equipment. The high mechanical strength and thermal stability of MCCB SMC parts ensure their longevity and sustained performance in demanding environments.
Conclusion: MCCB SMC parts manufacturing involves a meticulous process that encompasses material selection, mold design, and precise control of compression molding parameters. These components play a vital role in ensuring electrical safety and the efficient operation of electrical systems. With their excellent electrical insulation properties and mechanical strength, MCCB SMC parts are indispensable in various industries. Manufacturers must uphold strict quality control measures to deliver reliable components that meet the stringent demands of the electrical industry.
Efficiency and Innovation in MCCB SMC Parts Manufacturing
Introduction: As the demand for reliable and high-performance electrical components continues to rise, MCCB (Molded Case Circuit Breaker) SMC (Sheet Molding Compound) parts manufacturers are constantly striving to enhance their production processes. In this article, we will delve into the efficient and innovative techniques employed by MCCB SMC parts manufacturers to meet the evolving needs of the electrical industry.
Efficient Material Management: Efficient material management is crucial in MCCB SMC parts manufacturing. Manufacturers employ advanced inventory control systems to optimize material usage, reduce waste, and ensure a streamlined production flow. Just-in-time (JIT) inventory strategies and real-time tracking systems help minimize inventory holding costs while ensuring the availability of materials when needed. Additionally, recycling and reusing waste materials contribute to sustainability and cost reduction.
Automation and Robotics: MCCB SMC parts manufacturers are increasingly integrating automation and robotics into their production processes. Automated systems offer numerous advantages, including increased production speed, improved precision, and enhanced safety. Robots are utilized for tasks such as material handling, mold loading, and part inspection. This integration of automation helps reduce manual labor, minimize errors, and enhance overall manufacturing efficiency.
Advanced Mold Design and Simulation: Innovative mold design and simulation technologies are revolutionizing MCCB SMC parts manufacturing. Computer-aided design (CAD) software allows designers to create complex and customized molds with precise specifications. Furthermore, simulation software enables manufacturers to analyze mold filling patterns, optimize gating systems, and predict part defects before the actual production process begins. This iterative approach minimizes trial and error, accelerates time-to-market, and ensures high-quality MCCB SMC parts.
Process Optimization and Continuous Improvement: MCCB SMC parts manufacturers employ lean manufacturing principles to optimize their production processes. Value stream mapping, Kaizen events, and Six Sigma methodologies are utilized to identify and eliminate inefficiencies, reduce lead times, and enhance overall productivity. By continuously evaluating and improving their operations, manufacturers can achieve higher levels of quality, cost-effectiveness, and customer satisfaction.
Advanced Testing and Quality Assurance: To meet stringent industry standards, MCCB SMC parts manufacturers implement advanced testing and quality assurance techniques. Non-destructive testing methods such as X-ray inspection, ultrasonic testing, and thermal imaging are employed to detect internal defects and ensure the integrity of the parts. Statistical process control (SPC) techniques and automated inspection systems monitor key quality parameters throughout the manufacturing process. These rigorous quality control measures guarantee that MCCB SMC parts meet the highest standards of performance and reliability.
Conclusion: Efficiency and innovation are vital for MCCB SMC parts manufacturers to thrive in the competitive electrical industry. By implementing efficient material management, integrating automation and robotics, utilizing advanced mold design and simulation technologies, optimizing processes, and ensuring rigorous testing and quality assurance, these manufacturers can deliver high-quality MCCB SMC parts that meet the evolving demands of the market. Through continuous improvement and a commitment to excellence, they contribute to the advancement and reliability of electrical systems worldwide.
Regenerate response