Thermosetting Compression Moulding, a fundamental yet crucial technique in the plastic manufacturing industry, holds significant importance in shaping a diverse range of products with high precision and durability. This process, which involves the use of heat and pressure to mold thermosetting plastics into desired shapes, offers numerous advantages that make it a preferred choice for various applications.
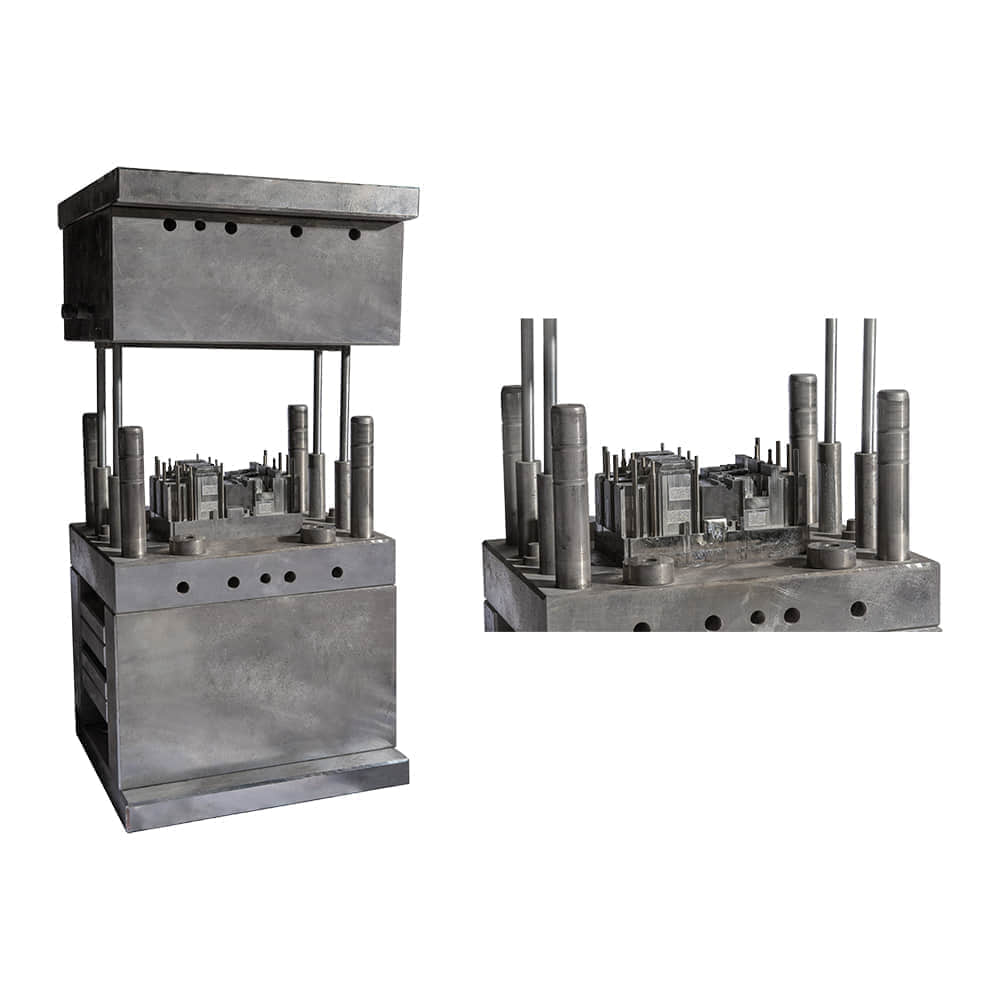
The core principle of Thermosetting Compression Moulding lies in the unique nature of thermosetting plastics. These plastics, unlike thermoplastics, undergo irreversible chemical changes during the molding process, resulting in a permanent, stable product. Once heated and pressed into shape, they retain their form and cannot be reheated and reshaped like thermoplastics. This characteristic, coupled with the high strength and durability of thermosetting plastics, makes them ideal for applications that require long-term stability and reliability.
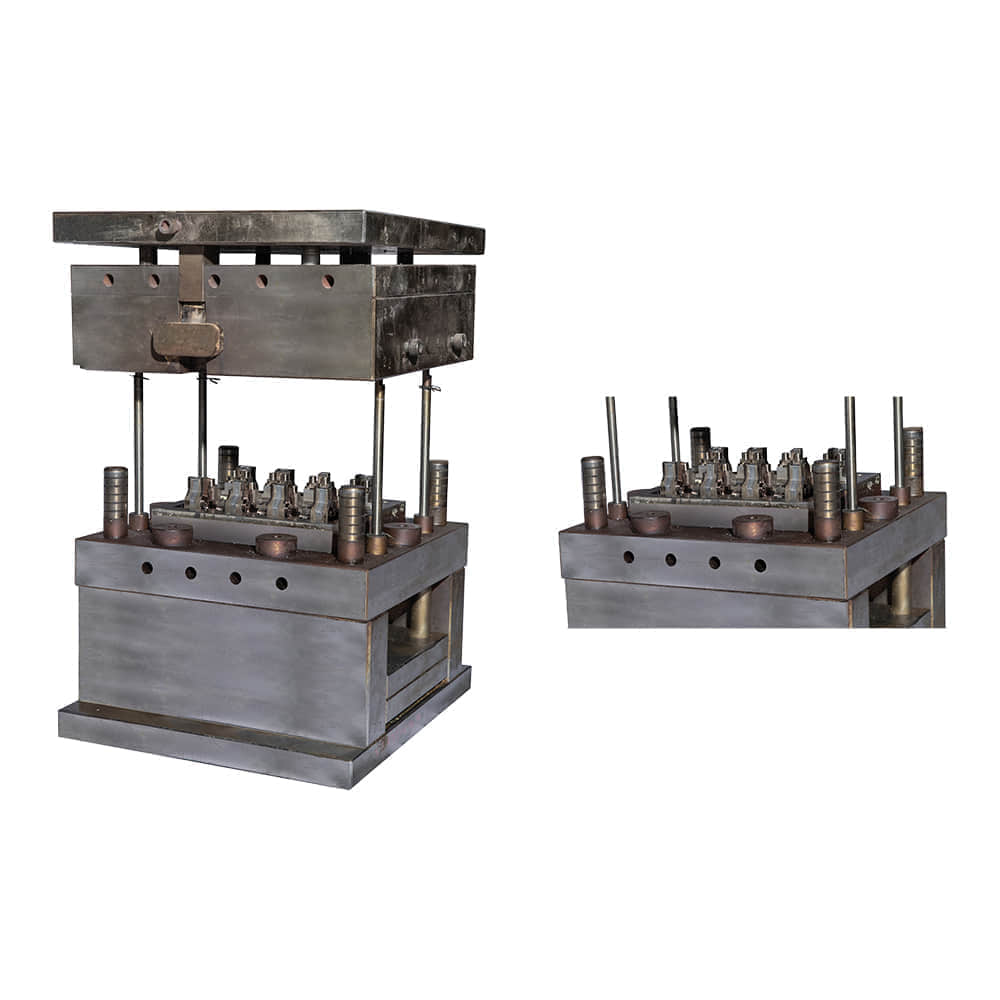
The process of Thermosetting Compression Moulding begins with the preparation of the mold, which is designed to produce the desired shape of the plastic product. The mold, typically made of metal, consists of two halves: the upper and lower molds. The plastic material, in the form of pellets or sheets, is then placed into the mold cavity. Once the mold is closed, the heating process begins. The mold is heated to a temperature that activates the plastic’s thermoplasticity, allowing it to flow and fill the mold cavity. Simultaneously, pressure is applied to ensure that the plastic material evenly distributes within the mold and takes the shape of the cavity.
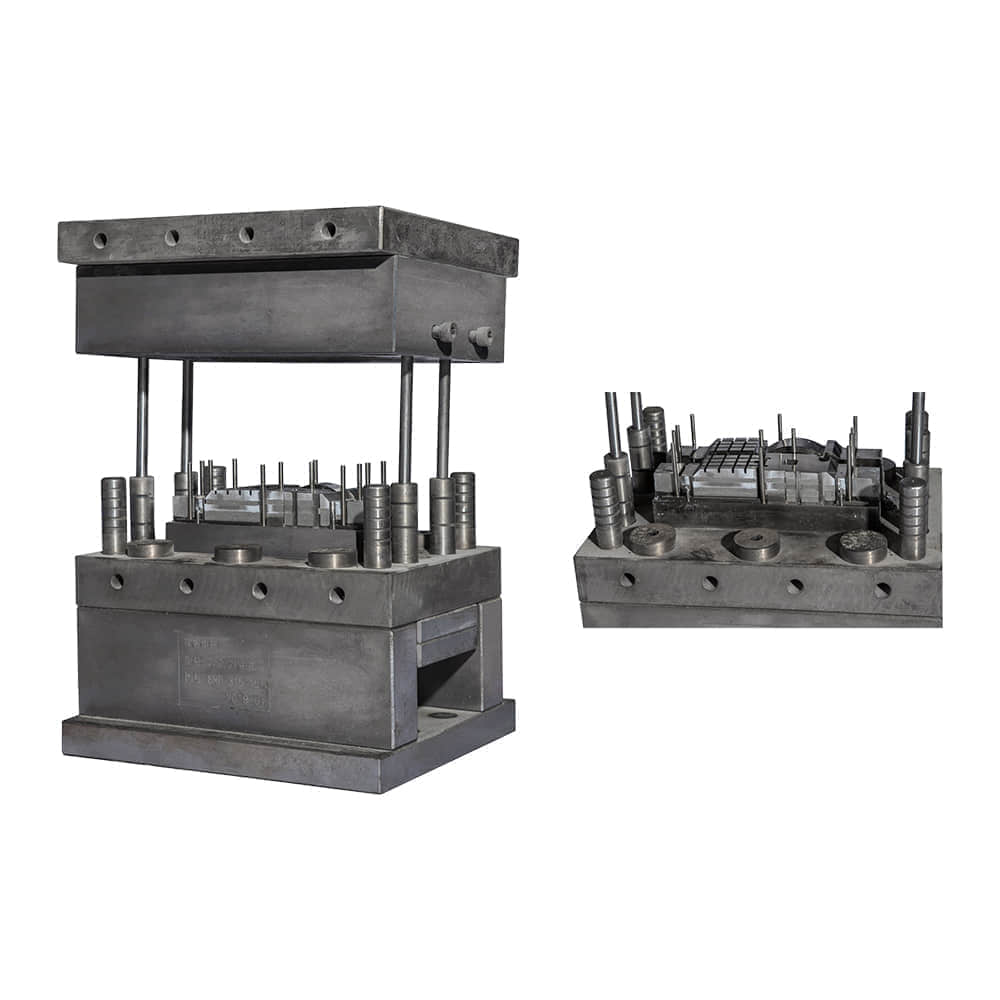