Injection molded parts have revolutionized the manufacturing industry, offering unparalleled efficiency, precision, and versatility. This technique, which involves injecting molten plastic into a mold to create a solid object, has become a cornerstone of modern production processes.
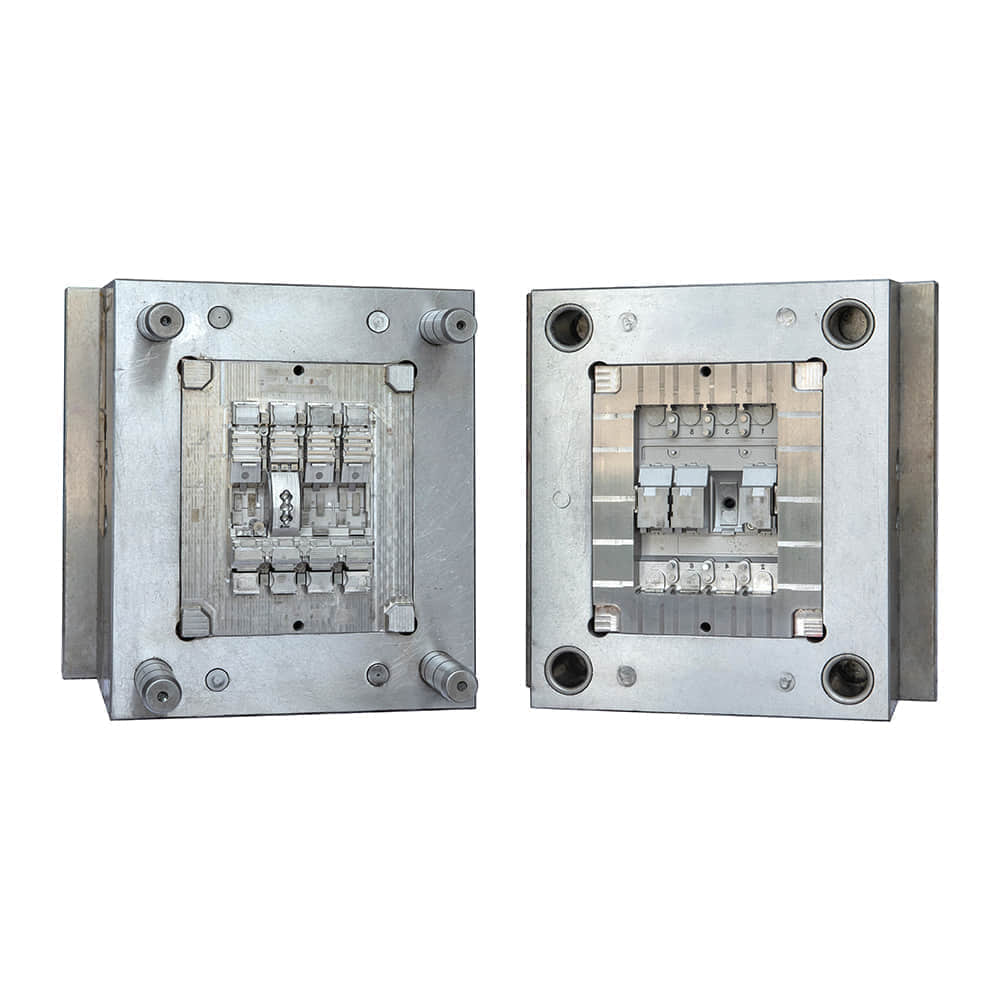
The core principle of injection molding lies in its ability to transform plastic materials into intricate shapes with exceptional accuracy. The process begins with the preparation of the mold, a crucial step that determines the final shape and dimensions of the part. Once the mold is ready, molten plastic is injected into its cavities under high pressure. As the plastic cools and solidifies, it takes the shape of the mold, resulting in a precision-made part.
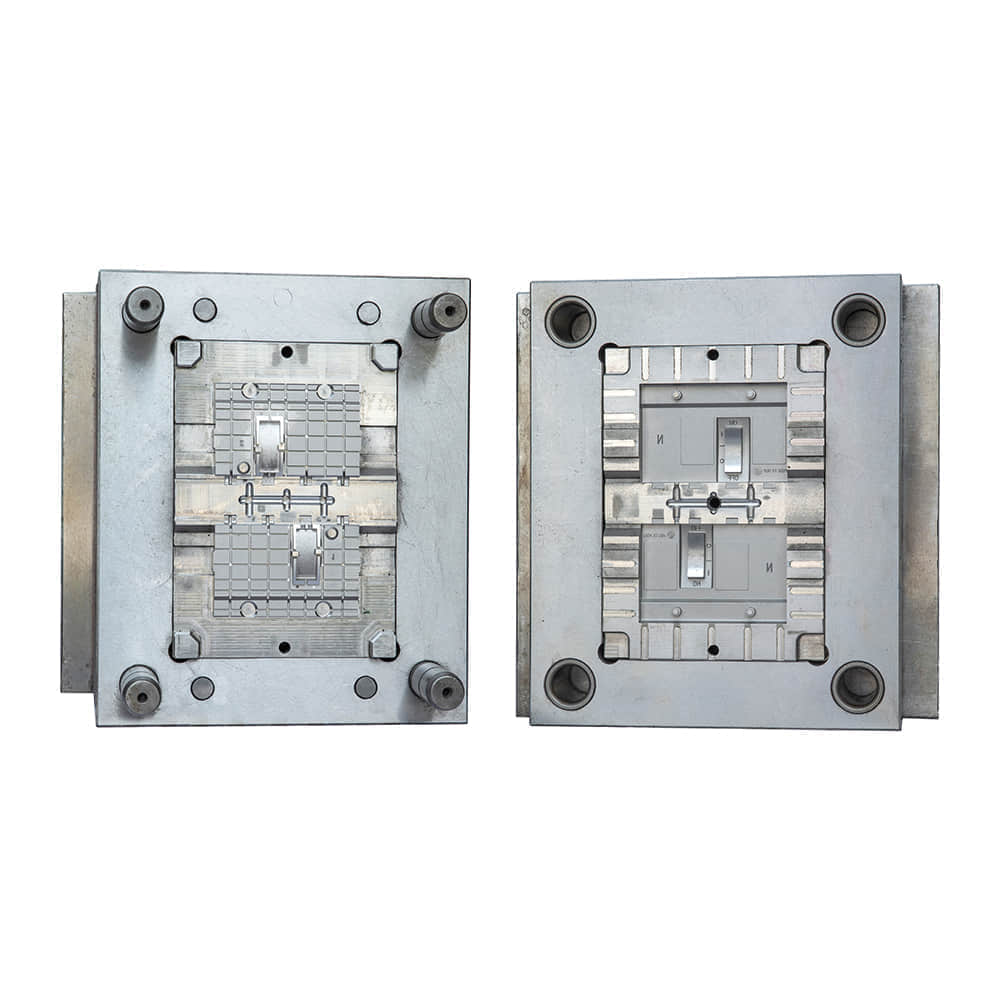
The beauty of injection molding lies in its adaptability. This process can be used to create parts ranging from the smallest components to large, complex assemblies. The versatility of injection molding allows manufacturers to produce a wide range of products, from automotive parts to household appliances and even medical devices. Moreover, injection molding offers significant advantages in terms of efficiency and cost-effectiveness. The process can be highly automated, reducing labor costs and increasing production speeds. Additionally, the use of molds allows for mass production of identical parts, ensuring consistency and reducing the need for post-processing.
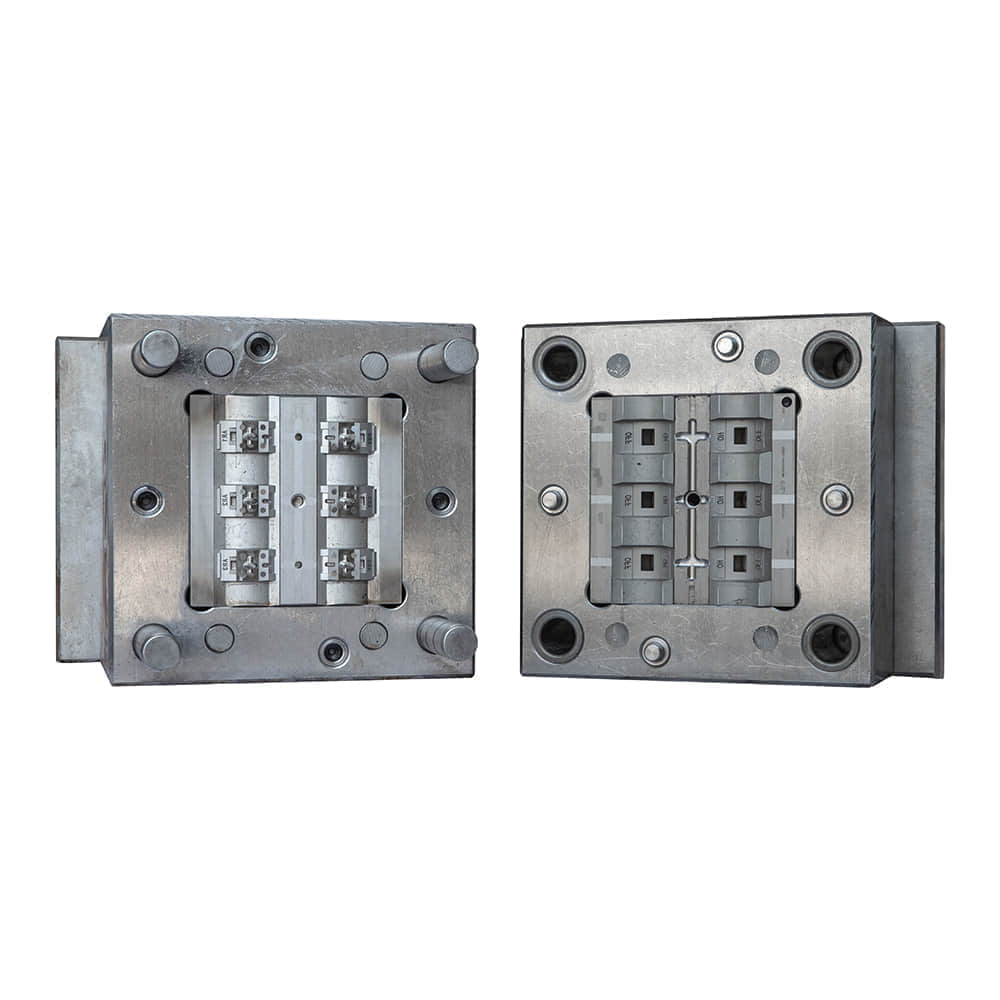