Introduction
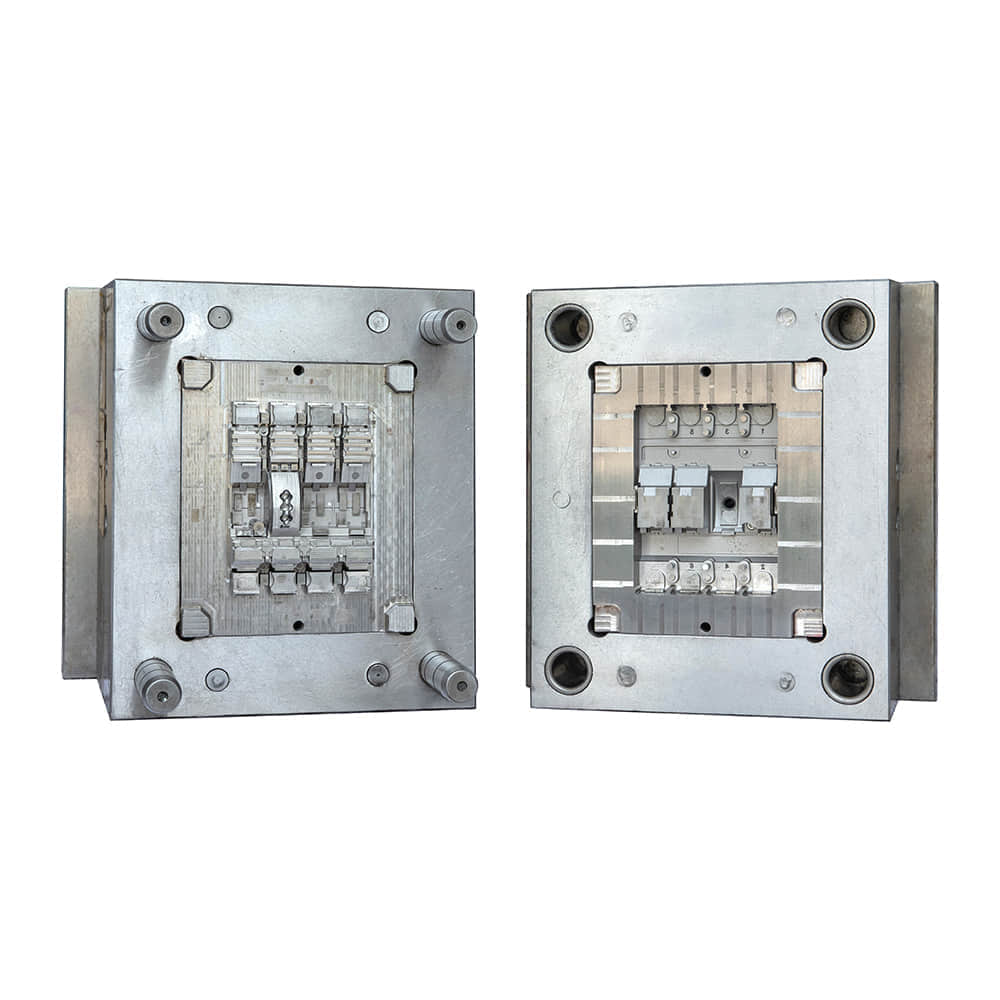
Thermoplastic injection molding is a versatile and widely used manufacturing process that plays a pivotal role in shaping various plastic products. This technique involves injecting melted thermoplastic material into a mold to create complex shapes with precision. The popularity of thermoplastic injection molds is attributed to their numerous advantages, ranging from cost-effectiveness to design flexibility. In this article, we will delve into the key benefits of using thermoplastic injection molds.
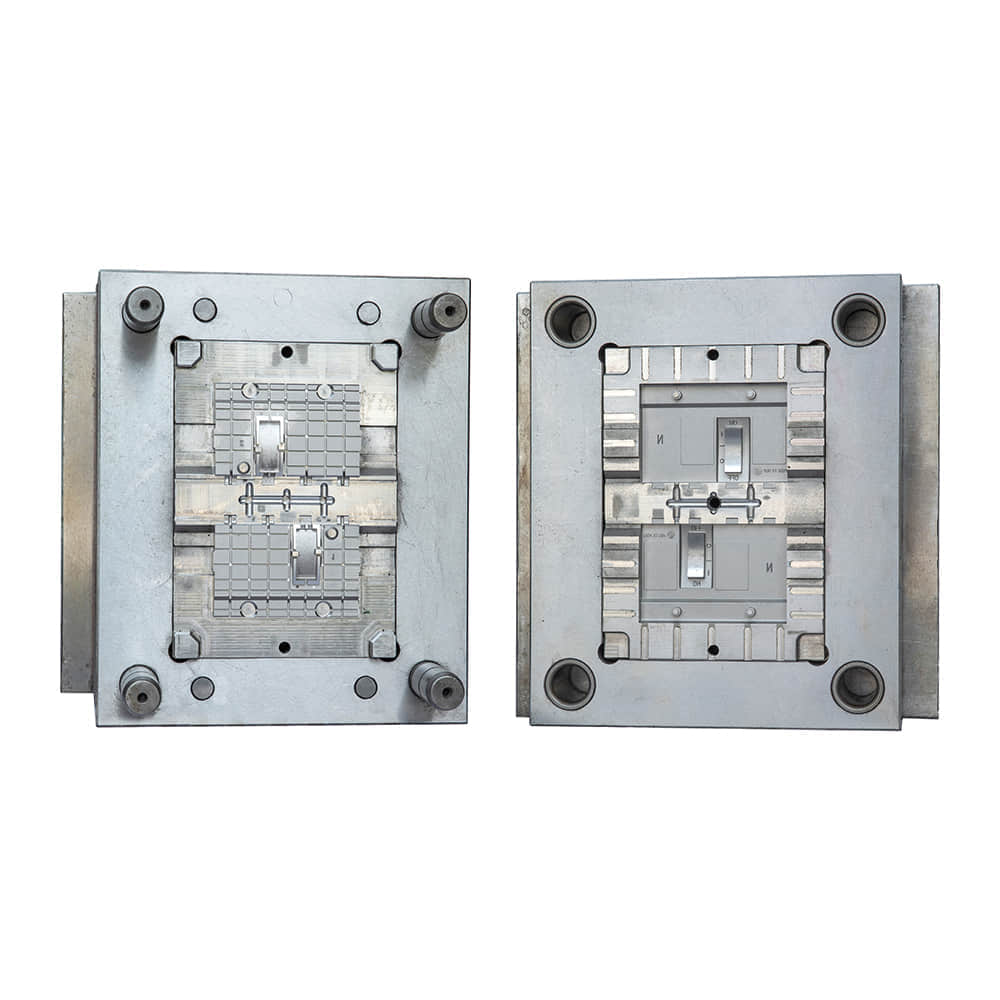
Precision and Complex Geometry Thermoplastic injection molds enable the creation of intricate and complex shapes with a high level of precision. The mold cavity is carefully crafted to replicate even the smallest details, resulting in finished products that meet tight tolerances. This level of accuracy is crucial in industries such as medical devices and electronics, where small variations can have significant consequences. Cost-Effectiveness One of the primary advantages of thermoplastic injection molding is its cost-effectiveness, particularly for large-scale production. Once the initial mold is created, the subsequent production process becomes highly efficient. The fast cycle times and minimal waste contribute to reduced production costs, making it an ideal choice for industries that require mass production of plastic components. Wide Range of Thermoplastics Thermoplastic injection molds are compatible with a vast array of thermoplastic materials, each possessing unique properties and characteristics. Engineers can choose the most suitable material for the desired application, whether it’s a rigid material for structural components or a flexible one for consumer products. This versatility ensures that the end product meets specific performance requirements. Short Lead Times The design and manufacturing of thermoplastic injection molds are relatively quick compared to other mold-making processes. Computer-aided design (CAD) and computer-aided manufacturing (CAM) technologies expedite mold creation, resulting in shorter lead times. This is especially advantageous when rapid product development or quick adaptation to market demands is required. Reduced Material Waste Thermoplastic injection molding produces minimal material waste due to its precision-driven process. The ability to control the injection volume and fill patterns helps minimize excess material. Furthermore, any excess material generated during the production process can be recycled, contributing to environmental sustainability. Consistent Quality The automated nature of thermoplastic injection molding ensures consistent quality across each manufactured part. This is particularly important for industries where product reliability and uniformity are critical. The process minimizes variations, reducing the likelihood of defects and ensuring that each product meets the desired specifications. Design Flexibility Designers have a high degree of flexibility when it comes to designing parts for thermoplastic injection molding. The process allows for the integration of various features, such as undercuts, threads, and hinges, directly into the mold. This eliminates the need for secondary operations and assembly, further streamlining the production process. Conclusion Thermoplastic injection molds have revolutionized the way plastic products are manufactured, offering a multitude of advantages that cater to diverse industries. From intricate designs to cost-effective production, the benefits of thermoplastic injection molding are hard to overlook. As technology continues to advance, we can anticipate even greater precision, efficiency, and sustainability in this essential manufacturing process.
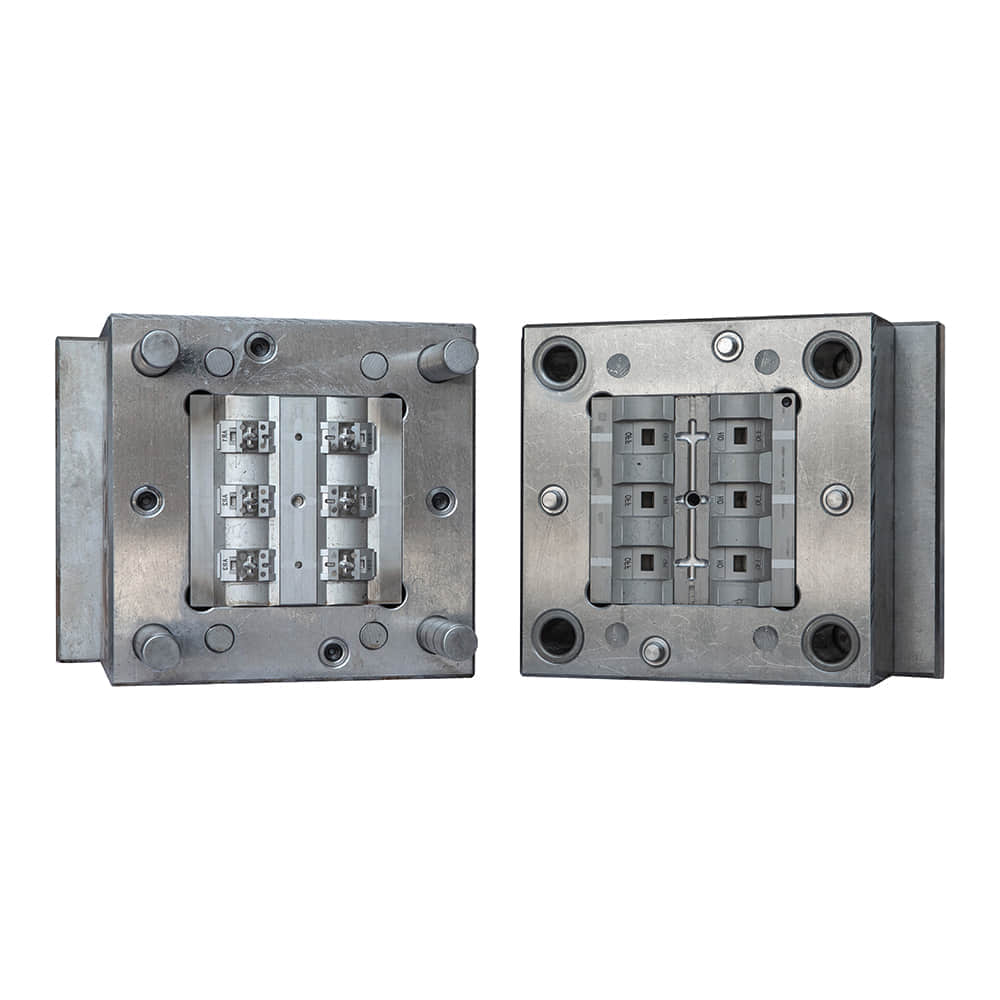