In the realm of automation and control systems, the pneumatic actuator stands as a pivotal component, facilitating precise and efficient movements in various industrial applications. This article aims to delve into the working principles, advantages, and applications of pneumatic actuators, highlighting their significance in modern automation processes.
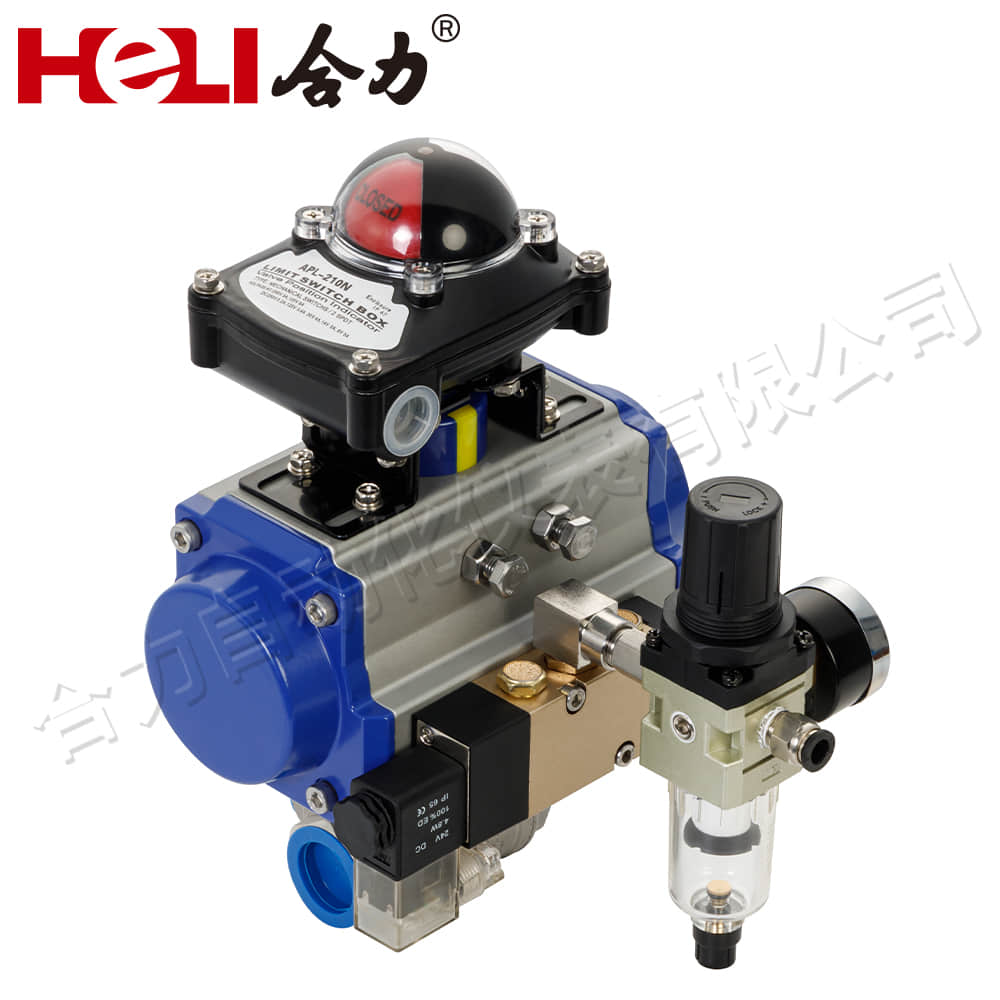
Pneumatic actuators, also known as pneumatic drives or air cylinders, operate on the principle of converting compressed air or gas into mechanical motion. They consist of a cylinder, piston, and connecting rod, which together create linear or rotary motion when actuated by pressurized air. The simplicity and reliability of their design, coupled with the ease of obtaining and controlling compressed air, make pneumatic actuators a popular choice in numerous industrial settings.
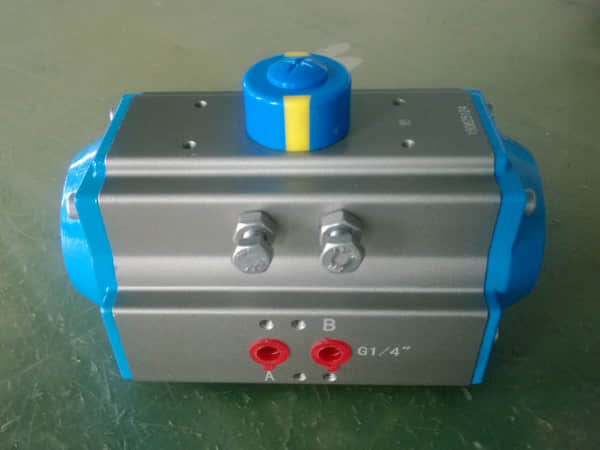
The working principle of a pneumatic actuator is straightforward. Compressed air is supplied to one end of the cylinder, pushing the piston and connecting rod in the opposite direction. By controlling the flow of compressed air, the actuator can be precisely positioned or moved to perform various tasks. The speed and force of the actuator can be adjusted by varying the pressure and flow rate of the compressed air, offering a high level of controllability. One of the primary advantages of pneumatic actuators is their safety and reliability. Since they operate using compressed air, there is no risk of electric sparks or fires, making them suitable for use in hazardous environments. Additionally, pneumatic actuators require minimal maintenance and have a long service life, reducing downtime and maintenance costs.
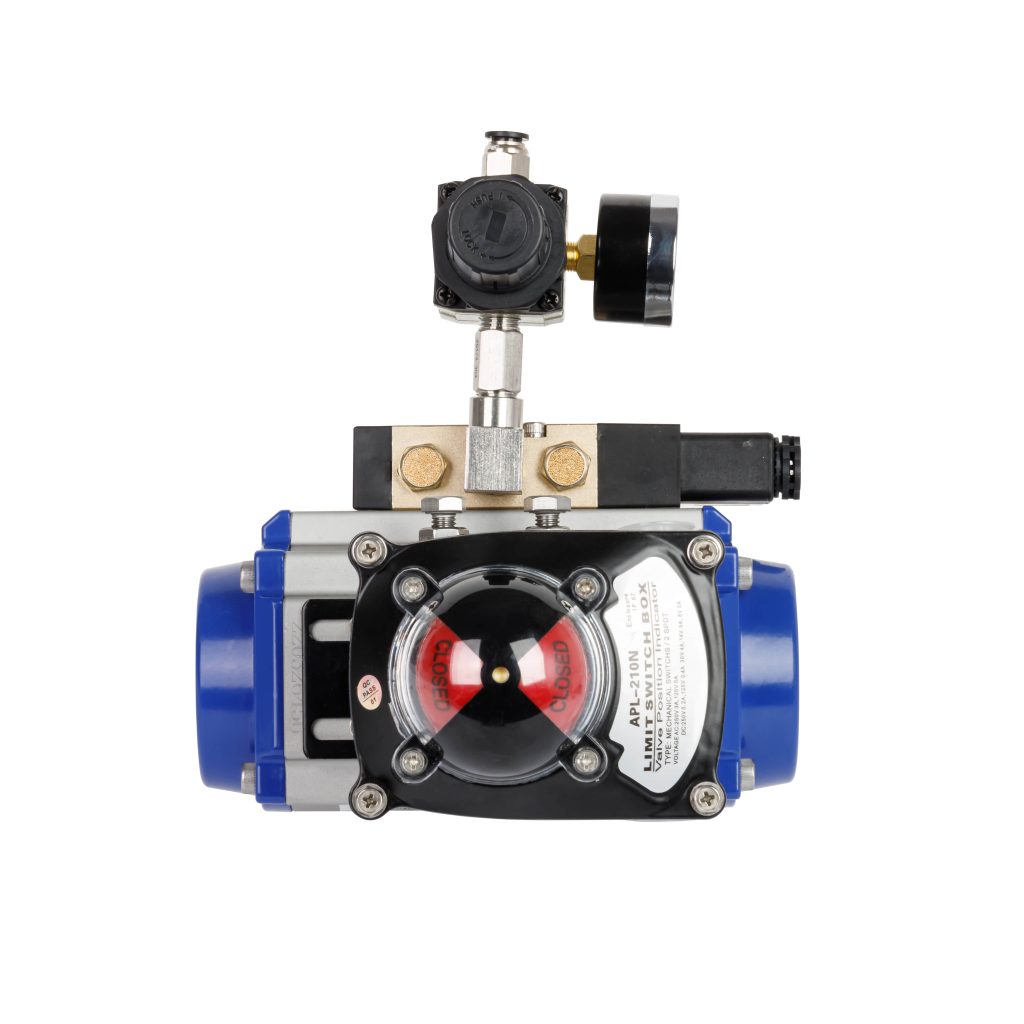