Blanking dies play a pivotal role in the world of manufacturing and fabrication. These precision tools are instrumental in creating a wide range of products, from intricate electronic components to everyday items like beverage cans. In this article, we will delve into the world of blanking dies, exploring their functions, types, design considerations, and their significance in various industries.
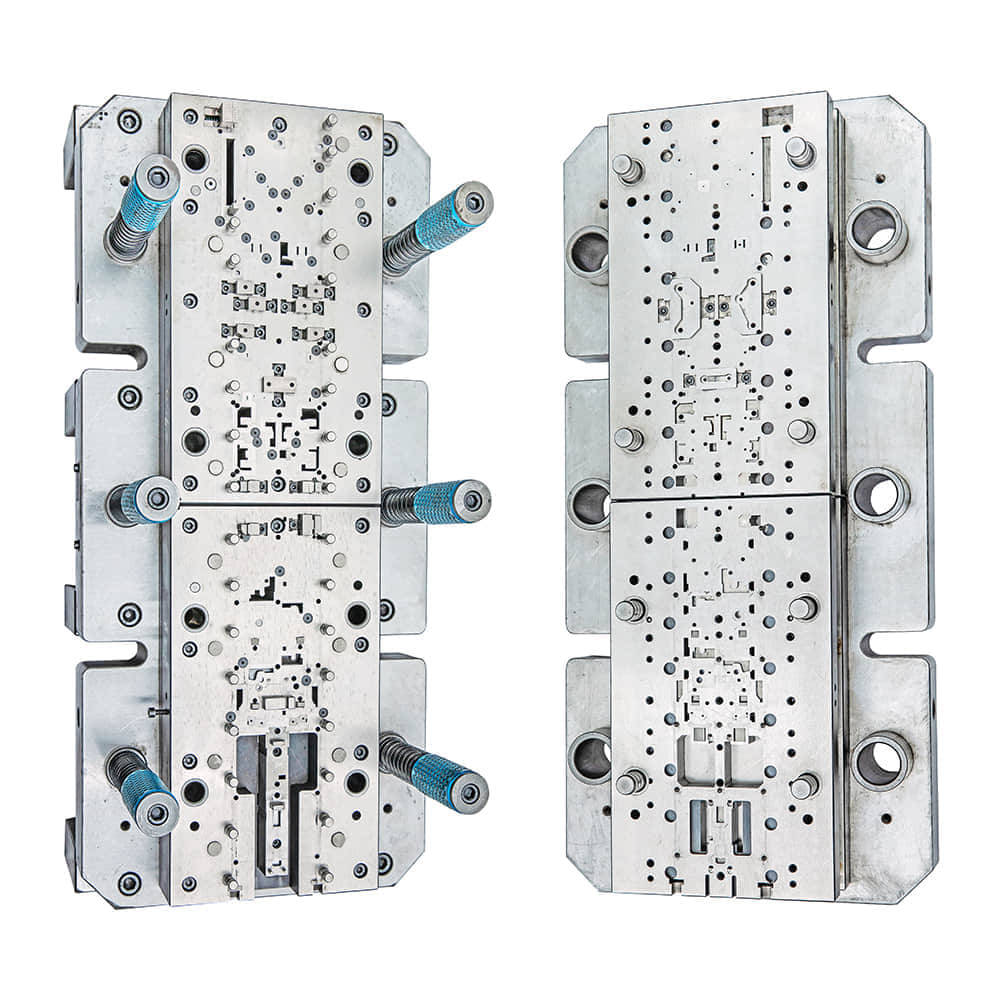
What Is a Blanking Die?
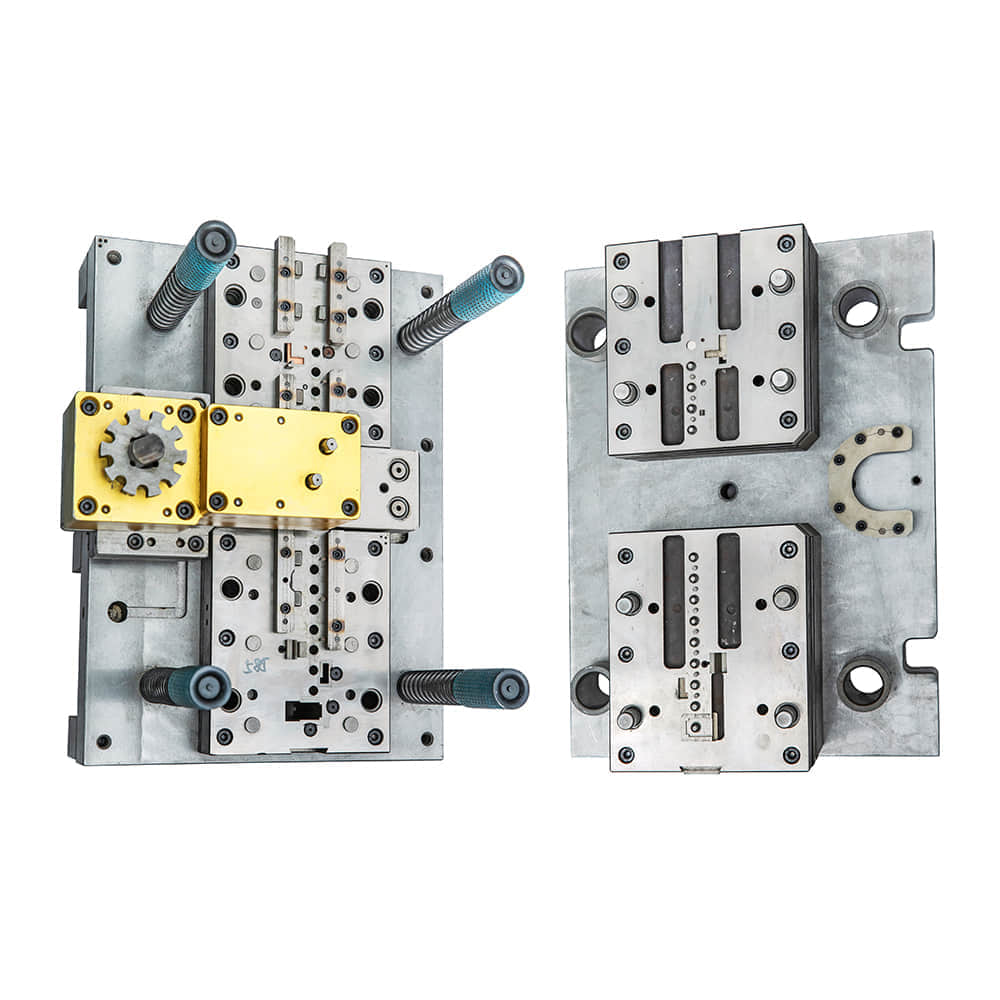
At its core, a blanking die is a specialized cutting tool used to shear or punch sheet metal, resulting in a blank or flat piece of material with specific dimensions and contours. This process is a fundamental step in the manufacturing of countless products. Functions of Blanking Dies Blanking dies serve several critical functions in manufacturing: Material Shearing: The primary function of a blanking die is to cut or shear sheet material into desired shapes and sizes. This is often the initial step in creating parts for more complex assemblies. Precision Tolerances: Blanking dies can achieve incredibly tight tolerances, ensuring that each blanked piece meets precise dimensional requirements. High Productivity: They enable high-speed, automated production, making them indispensable in industries with mass production needs. Material Utilization: Efficient blanking die design minimizes material waste, reducing production costs and environmental impact. Types of Blanking Dies There are several types of blanking dies, each designed for specific applications: Simple Blanking Dies: These are used for basic, straightforward cutting operations. Compound Blanking Dies: Employed when more complex shapes or tighter tolerances are required, compound blanking dies consist of multiple cutting operations within a single die set. Progressive Blanking Dies: Designed for high-volume production, progressive dies perform a sequence of operations in one pass, increasing efficiency. Transfer Blanking Dies: These dies move the material from one station to another, allowing for intricate shapes and patterns. Design Considerations The design of a blanking die is a complex process that requires meticulous attention to detail. Here are some key considerations: Material Selection: The die material must be hard enough to withstand repeated use and resist wear and tear. Die Clearance: Proper clearance between the punch and die is critical to achieving clean cuts and preventing material damage. Die Shape: The shape of the die cavity determines the final shape of the blanked piece. Precision is paramount. Strip Layout: In progressive and transfer dies, the layout of the strip carrying the material is crucial to the success of the operation. Significance Across Industries Blanking dies are used in various industries, including: Automotive: They produce components like body panels and chassis parts with high precision. Electronics: Blankings dies are essential for creating intricate components found in electronic devices. Packaging: The production of cans, lids, and other packaging materials heavily relies on blanking dies. Aerospace: They help manufacture critical aircraft parts with tight tolerances. Medical: Blanking dies play a role in crafting medical device components and instruments. In conclusion, blanking dies are the unsung heroes of modern manufacturing, enabling the creation of precise components and products that we use every day. Their diverse types and intricate designs make them an essential tool across various industries, contributing to efficiency, accuracy, and material utilization. Understanding the importance of blanking dies sheds light on the complexity and innovation that underpins the manufacturing processes we often take for granted.
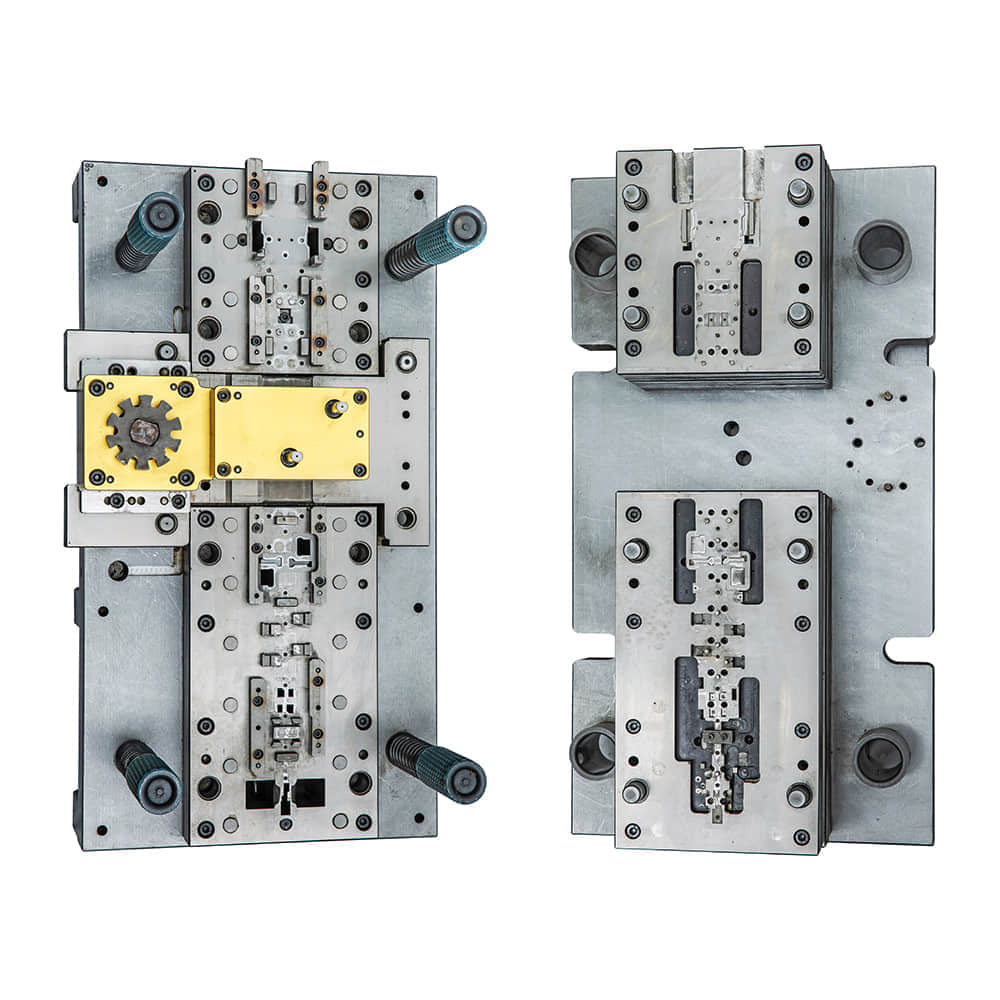