Metal stamping is a vital process in the manufacturing industry, allowing for the mass production of intricate metal components with precision and efficiency. At the heart of this process are metal stamping die manufacturers, the unsung heroes behind the scenes who design and create the molds that shape the products we rely on daily.
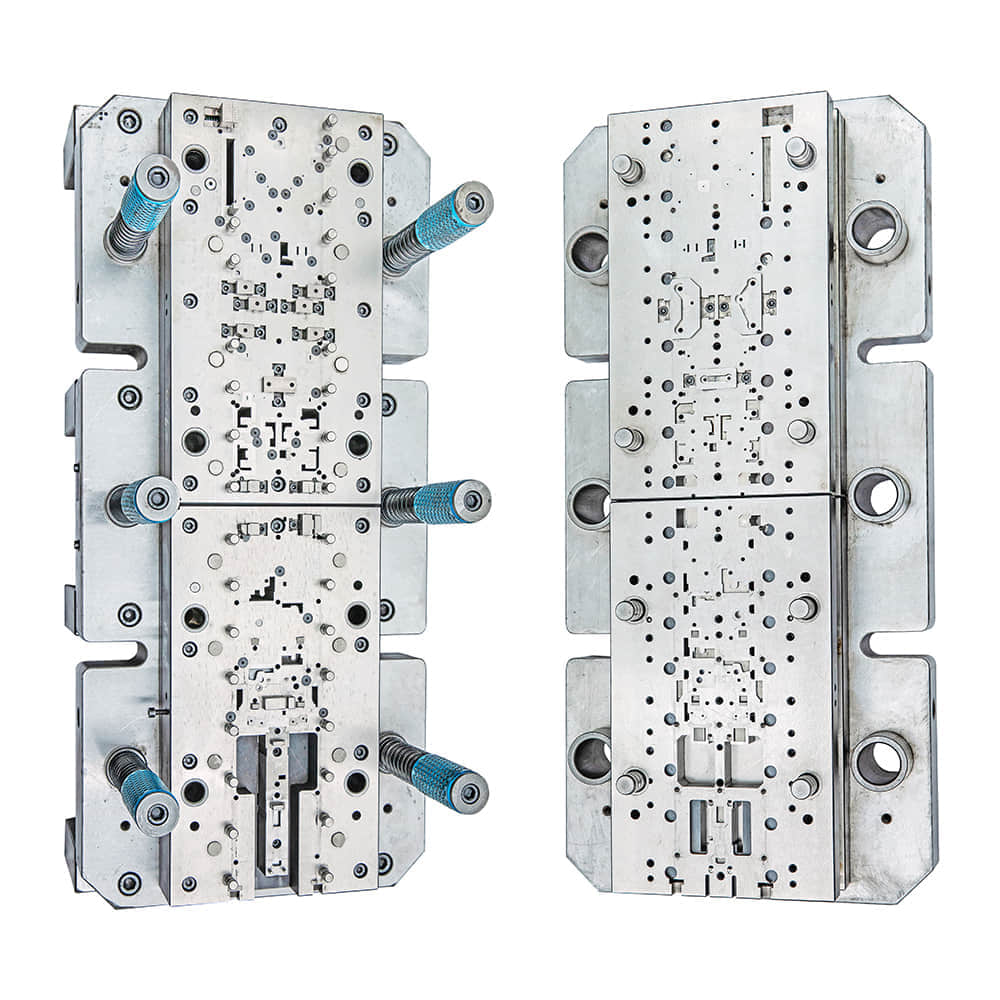
Innovation in Design and Manufacturing
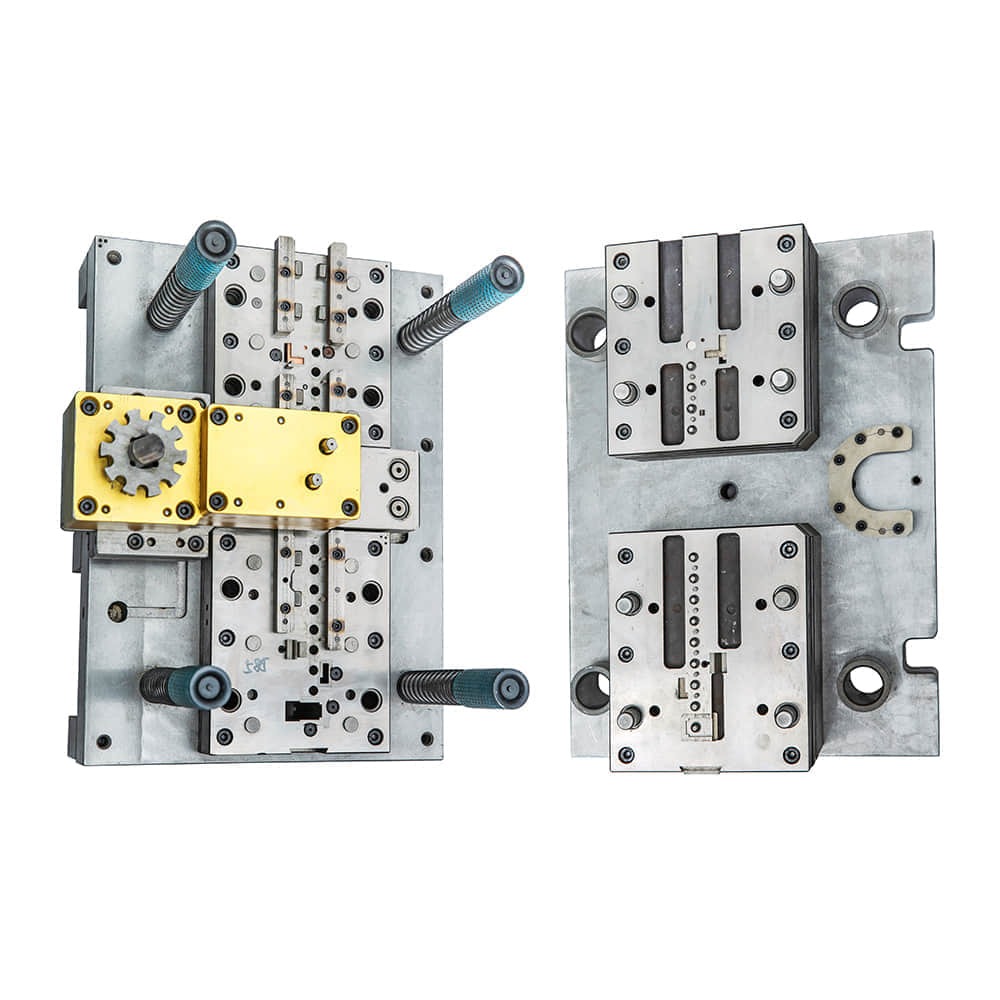
Metal stamping die manufacturers play a pivotal role in modern manufacturing. They are responsible for the creation of dies, which are specialized tools used in stamping presses to cut or form metal sheets into desired shapes. These manufacturers combine traditional craftsmanship with cutting-edge technology to develop dies that meet the exact specifications of their clients. Innovative design is a hallmark of reputable metal stamping die manufacturers. They employ computer-aided design (CAD) software to meticulously craft the intricate patterns and geometries required for each product. This digital approach allows for greater precision, faster prototyping, and easier modifications during the design phase. Precision Engineering: A Cornerstone of Success Precision is non-negotiable in metal stamping, as even the slightest deviation can lead to defects or failures in the final product. Metal stamping die manufacturers ensure that their dies are engineered to exact tolerances, accounting for factors such as material thickness, metal properties, and desired end-product dimensions. The process of creating a metal stamping die involves a combination of advanced machining techniques. Computer numerical control (CNC) machining is often employed to carve out intricate features on hardened steel blocks, resulting in dies that can withstand the high pressures and repeated impacts of the stamping process. This precision engineering not only guarantees the quality of the end product but also prolongs the lifespan of the die itself, leading to cost savings for manufacturers over time. Efficiency and Sustainability Efficiency is another key aspect of metal stamping die manufacturing. With the global emphasis on sustainable practices, manufacturers are designing dies that minimize material waste and energy consumption. Through careful planning and optimization, manufacturers can create dies that maximize material usage, reducing scrap rates and environmental impact. Furthermore, the integration of sensors and real-time monitoring systems in modern stamping presses allows manufacturers to detect anomalies and make adjustments on the fly. This level of control ensures consistent quality throughout the production process and minimizes downtime due to tooling issues. Meeting Diverse Industry Needs Metal stamping die manufacturers serve a wide array of industries, from automotive and aerospace to electronics and appliances. Each industry comes with its own unique set of requirements, demanding manufacturers to adapt and innovate constantly. Whether it’s producing components with micron-level precision or meeting high-volume production demands, these manufacturers rise to the challenge. The Human Touch While technology has undoubtedly revolutionized the metal stamping die manufacturing process, the human element remains indispensable. Experienced craftsmen bring a wealth of knowledge and expertise to the table, enabling them to identify potential design flaws, foresee manufacturing challenges, and develop creative solutions. The synergy between human skill and technological advancement is what sets exceptional metal stamping die manufacturers apart. In conclusion, metal stamping die manufacturers are the unsung heroes of modern manufacturing, driving innovation, precision, and efficiency in the creation of a wide range of products. Their mastery of design, engineering, and technology ensures that industries continue to thrive, producing high-quality components that power our world.
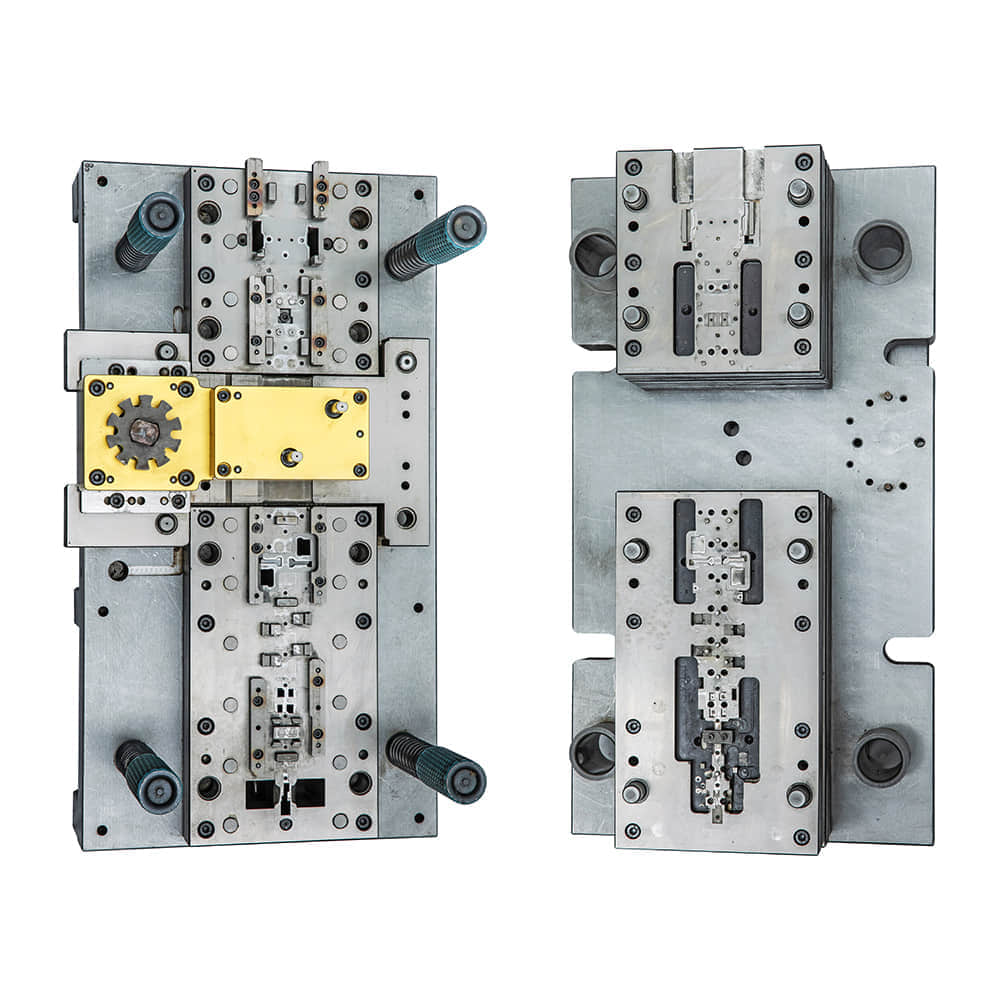