In the realm of manufacturing, thermosetting molds play a pivotal role in shaping products that range from consumer goods to aerospace components. These molds are essential in producing items that require high precision and durability. In this article, we will delve into the world of thermosetting mold manufacturers, shedding light on their significance, processes, and the ever-evolving industry.
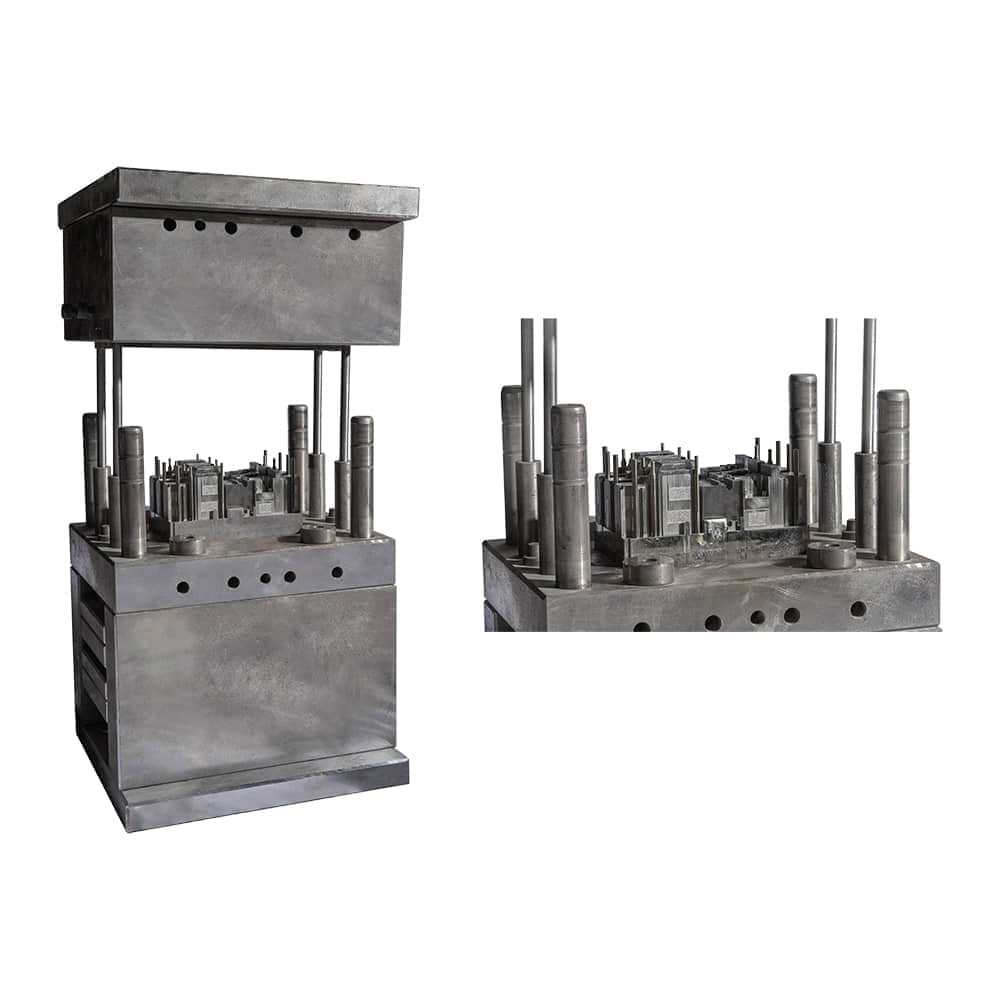
Understanding Thermosetting Molds:
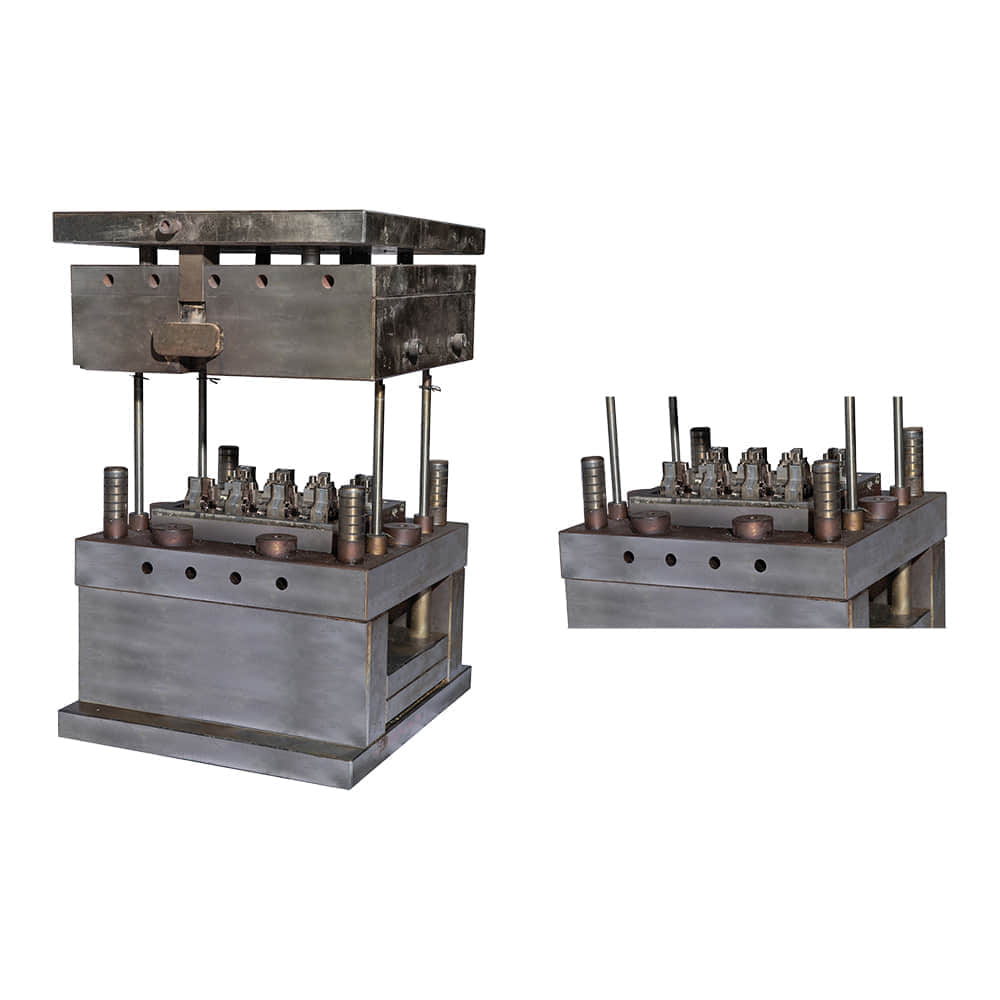
Thermosetting molds are an integral part of the thermosetting plastic manufacturing process. These molds are designed to withstand high temperatures and pressures, making them ideal for shaping materials that undergo irreversible chemical changes when exposed to heat. Unlike thermoplastics, which can be melted and reshaped multiple times, thermosetting plastics, once molded, retain their form permanently. The Significance of Thermosetting Mold Manufacturers: Thermosetting mold manufacturers are instrumental in various industries due to their ability to produce complex and high-performance parts. Let’s explore some key sectors where their products are indispensable: 1. Automotive Industry:In the automotive sector, thermosetting molds are employed to create components such as engine parts, electrical connectors, and interior trims. These molds ensure that the produced parts can withstand extreme temperatures and mechanical stress, enhancing the overall performance and safety of vehicles. 2. Aerospace Industry:In the aerospace industry, precision and reliability are paramount. Thermosetting mold manufacturers contribute by producing critical components like aircraft interiors, composite materials, and engine parts. These molds enable the fabrication of lightweight yet robust materials that are crucial for aircraft efficiency. 3. Electronics Industry:In the electronics industry, where miniaturization is a constant trend, thermosetting molds are used to create intricate circuit boards, insulating materials, and connectors. These molds ensure that electronic components are resilient and capable of withstanding the rigors of everyday use. The Manufacturing Process: The production of thermosetting molds involves a meticulous and multi-step process: 1. Mold Design:Manufacturers start by designing the mold, taking into consideration the specific requirements of the product to be molded. Factors such as material, dimensions, and production volume are carefully considered during this phase. 2. Material Selection:The choice of material for the mold is crucial. Typically, thermosetting materials like epoxy, silicone, and phenolic resins are used due to their high-temperature resistance and durability. 3. Mold Fabrication:Skilled craftsmen or advanced CNC machining techniques are employed to fabricate the mold. Precision is vital in ensuring the final product meets the required specifications. 4. Mold Curing:Once the mold is fabricated, it undergoes a curing process. This involves subjecting the mold to high temperatures, which harden the thermosetting material and make it suitable for molding. 5. Molding:The prepared mold is then used to shape the thermosetting plastic material. This is achieved by injecting the material into the mold cavity and applying heat and pressure until it sets. 6. Quality Control:Rigorous quality control measures are implemented to ensure the molded product meets the desired standards and specifications. Innovations and Challenges: The thermosetting mold manufacturing industry is not without its challenges. Manufacturers continually strive to improve their processes to meet the growing demands for efficiency and sustainability. Innovations such as the use of nanotechnology in mold materials and the incorporation of automation in the production process are shaping the industry’s future. Conclusion: Thermosetting mold manufacturers play a crucial role in numerous industries by enabling the production of durable and high-performance components. Their expertise in mold design, material selection, and fabrication processes ensures that products meet the stringent requirements of modern applications. As technology continues to advance, these manufacturers will remain at the forefront of innovation, driving progress across various sectors.
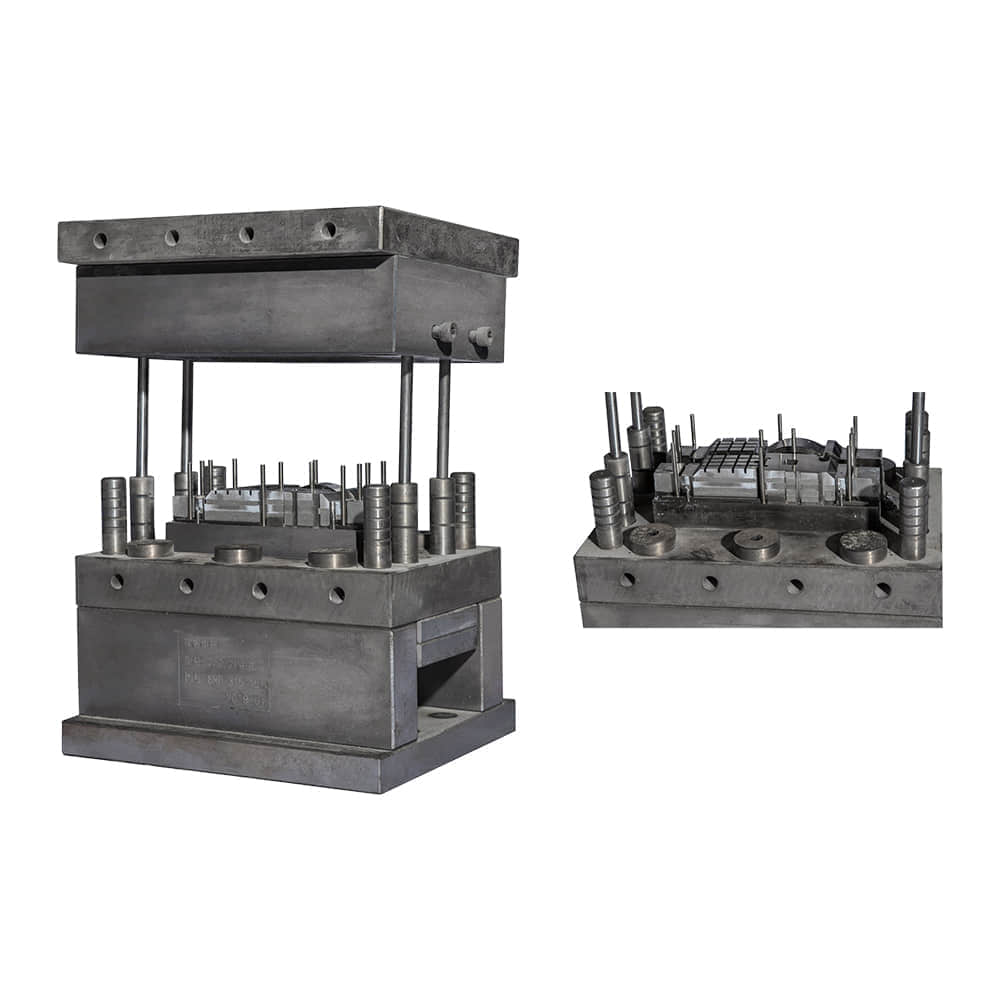