Thermosetting Compression Moulding, a crucial process in the manufacturing of thermosetting plastics, involves the use of heat and pressure to shape and solidify plastic materials. This technique, renowned for its precision and efficiency, finds widespread application in various industries, ranging from electrical to automotive and beyond.
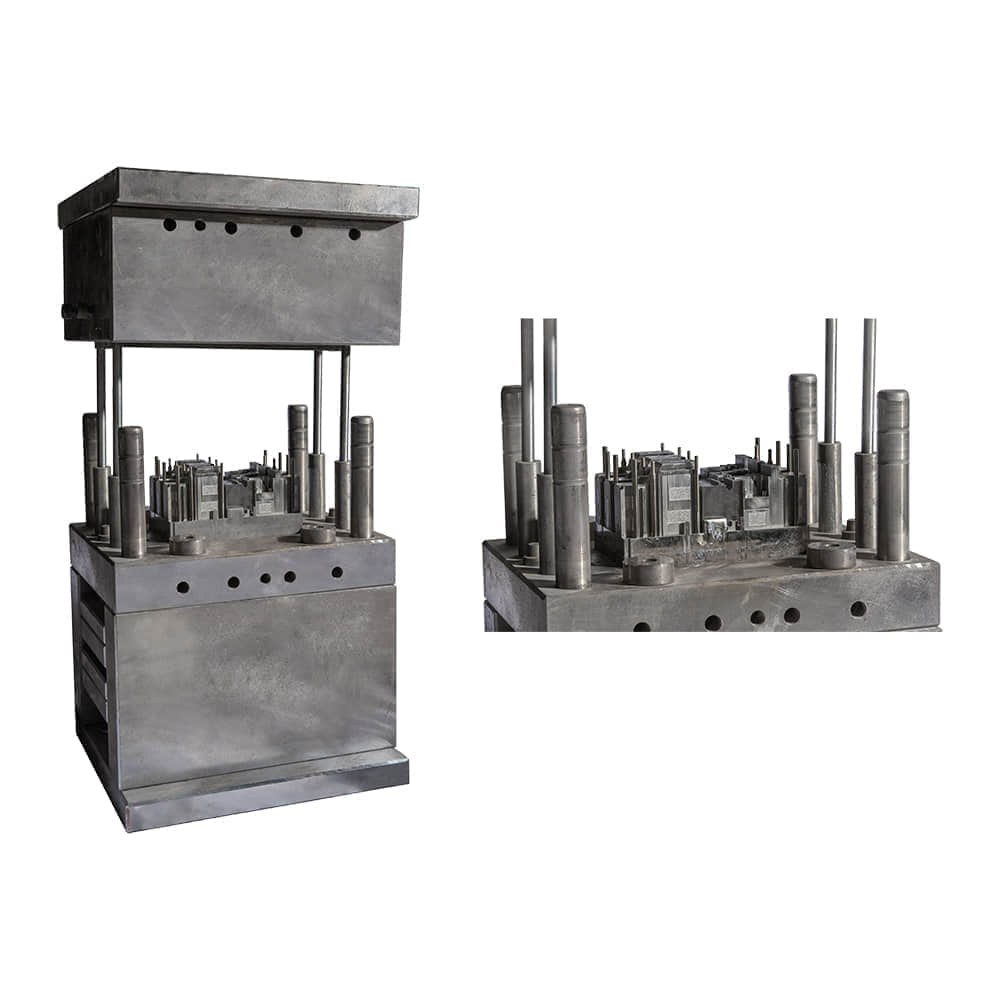
The process begins with the placement of the thermosetting plastic, such as phenolic plastic, amino plastic, or unsaturated polyester, within a pre-designed mold cavity. Once the mold is closed, it is subjected to heat, causing the plastic to soften and flow into the cavity’s intricate shapes. The application of pressure ensures that the plastic fills the mold cavity uniformly, eliminating any voids or imperfections.
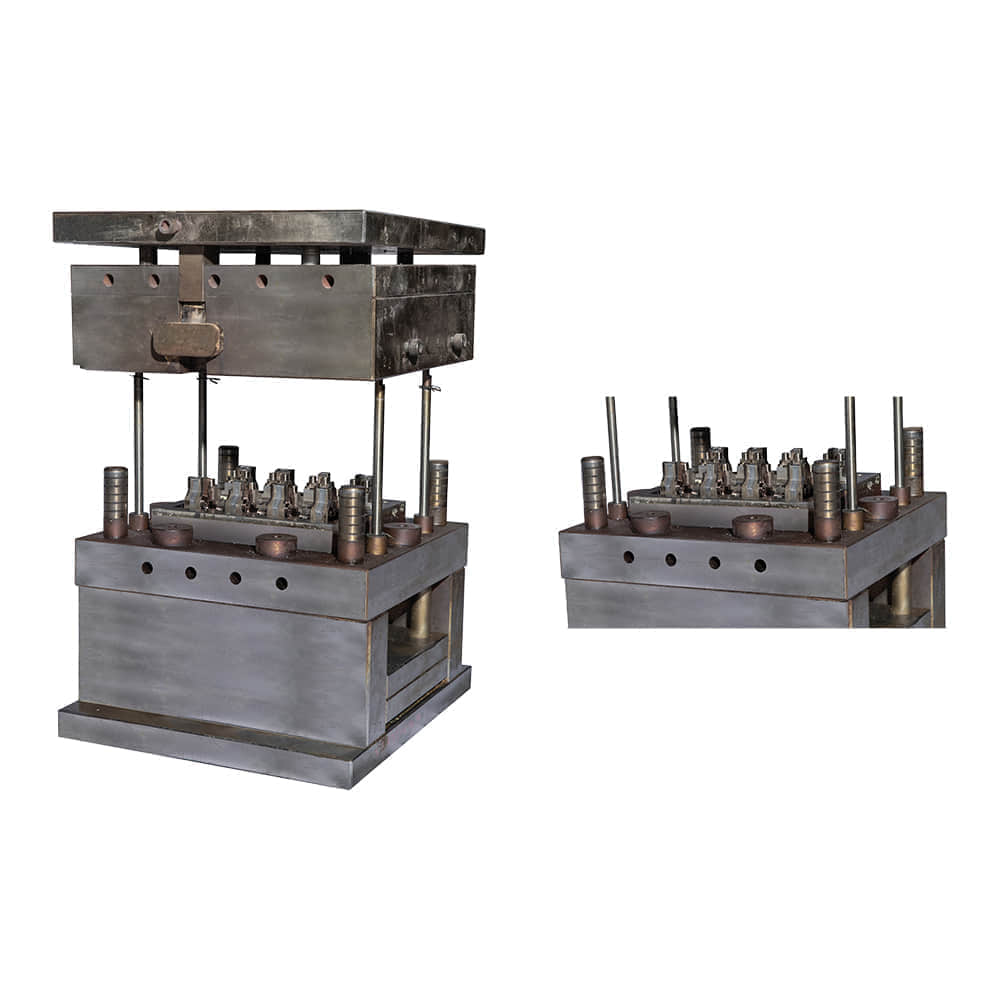
The critical stage of the process is the curing reaction, where the plastic undergoes a chemical transformation from a linear structure to a cross-linked, three-dimensional network. This transformation is irreversible, conferring the final product with its desired physical and mechanical properties, such as high heat resistance and dimensional stability. The advantages of Thermosetting Compression Moulding are numerous. Firstly, it offers a high degree of precision, enabling the production of complex shapes with tight tolerances. Secondly, the process is relatively fast, allowing for high production rates and cost-effective manufacturing. Furthermore, the curing reaction results in a strong and durable product that can withstand harsh environmental conditions.
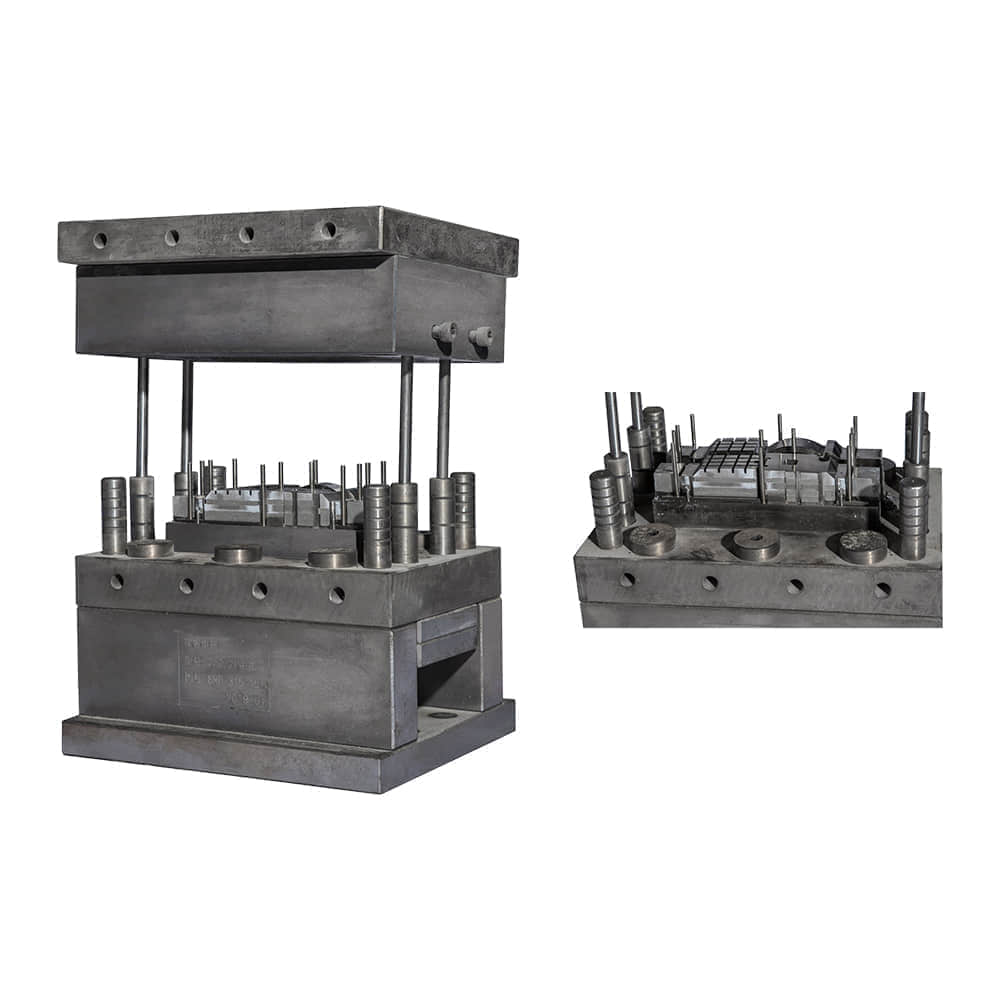