In various industrial settings, safety remains a paramount concern, especially when dealing with environments containing potentially explosive gases, vapors, or dust. The use of hazardous area thermostats has emerged as a crucial solution to maintain safety standards in such environments. These specialized thermostats are designed to regulate temperature while mitigating the risk of ignition, ensuring the wellbeing of both personnel and equipment.
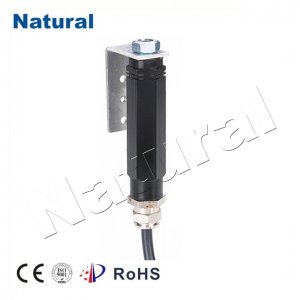
Hazardous area thermostats are engineered to function in locations where the potential for ignition is high. Industries such as oil and gas, chemical processing, mining, and manufacturing often require equipment that can operate in these hazardous conditions. These thermostats play a pivotal role in preventing ignition sources, thereby reducing the probability of accidents and catastrophic events. One key feature of hazardous area thermostats is their compliance with stringent safety certifications. These certifications ensure that the thermostats meet industry standards and regulations. One well-known certification is the ATEX (Atmosphères Explosibles) certification in Europe, while other regions might have similar standards. These certifications are a testament to the extensive testing and evaluation that these thermostats undergo to prove their suitability for hazardous environments. The design of hazardous area thermostats prioritizes durability and reliability. They are often constructed with robust materials that can withstand harsh conditions, such as extreme temperatures, corrosive substances, and mechanical stress. This ensures the thermostats can function consistently in spite of the challenging environment, reducing the risk of system failure or malfunction. To prevent the potential for ignition, hazardous area thermostats are equipped with intrinsically safe components. These components are engineered to limit the energy they can release, preventing the generation of sparks or excessive heat that could trigger an explosion. Moreover, the wiring and connections in these thermostats are designed to eliminate any chances of electrical arcing or short circuits, which could prove disastrous in hazardous locations. Maintaining an optimal operating temperature is vital for both operational efficiency and safety in industrial processes. Hazardous area thermostats help achieve this balance by monitoring and adjusting the temperature within specific ranges. This not only ensures the equipment operates efficiently but also prevents overheating, which could potentially lead to ignition. Incorporating advanced technology, some hazardous area thermostats are equipped with remote monitoring and control capabilities. This feature allows operators to keep track of temperature variations from a safe distance, minimizing the need for personnel to enter the hazardous area frequently. Remote control not only reduces risks but also enhances operational efficiency by enabling swift adjustments when needed. In conclusion, hazardous area thermostats have revolutionized safety measures in industries where the potential for explosion is high. Through rigorous testing, compliance with safety certifications, and the use of intrinsically safe components, these thermostats provide a reliable solution for maintaining temperature control while minimizing the risk of ignition. Their durability, remote monitoring capabilities, and role in preventing catastrophic events make them indispensable assets in hazardous environments. As industries continue to prioritize safety, the continued development of hazardous area thermostats will play a pivotal role in safeguarding both personnel and assets.